Chip Package Substrates Manufacturer.A Chip Package Substrates Manufacturer specializes in crafting intricate substrates crucial for semiconductor packaging. Their expertise lies in producing substrates that serve as the foundation for integrated circuits, enabling efficient electrical connections within electronic devices. Meticulous attention is paid to material selection, design precision, and manufacturing processes to ensure optimal performance and reliability. These manufacturers play a pivotal role in the semiconductor industry, providing the backbone for a wide array of electronic products, from smartphones to sophisticated computer systems, facilitating the seamless integration of microchips into various applications.
As a key component of electronic products, microchip package substrates (Chip Package Substrates) play a vital role in the field of modern technology. These substrates not only provide a platform to support and connect microchips, but also play a key role in circuit design and performance. They provide the necessary support and protection for the normal operation of microchips by providing electrical connections, signal transmission and heat dissipation support, thereby promoting the continuous innovation and development of electronic products.
What are Chip Package Substrates?
Chip Package Substrates are vital components in electronic products, playing a key role in packaging microchips and providing support, connectivity and functionality. The structures of these substrates are complex and sophisticated, often composed of multiple layers of materials, including conductive materials (such as copper), insulating materials, and other specialty materials.
In Chip Package Substrates, conductive materials are mainly used to form circuit connections and signal transmission paths. Copper is one of the most commonly used conductive materials, and its excellent conductive properties make it ideal for manufacturing circuit paths. These circuit paths are staggered on different levels of the substrate to implement complex electronic functions.
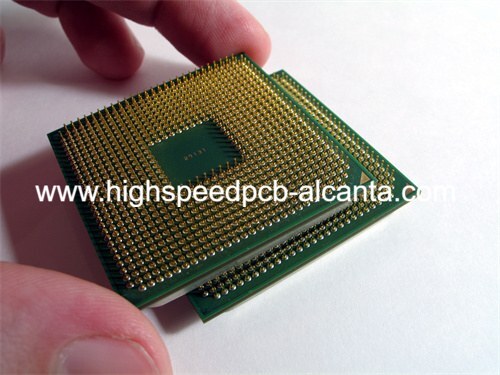
Chip Package Substrates Manufacturer
At the same time, the insulating materials in Chip Package Substrates play the role of isolating and protecting circuits to prevent short circuits or other damage between circuits. These insulation materials usually have good high temperature resistance and chemical stability to ensure that the substrate can operate stably and reliably in various working environments.
In addition to conductive materials and insulating materials, Chip Package Substrates may also contain other special materials, such as heat dissipation materials. As the performance of electronic products continues to improve, the requirements for heat dissipation effect are also getting higher and higher. Therefore, in some high-performance applications, a heat sink or other heat dissipation device may be integrated on the substrate to ensure that the microchip maintains the appropriate temperature while operating.
Overall, Chip Package Substrates play a vital role in electronic products. Not only do they provide a platform to support and connect microchips, they also play a key role in circuit design and performance. Through reasonable selection of materials and precision manufacturing processes, Chip Package Substrates can ensure that electronic products have excellent performance, reliability and stability, thereby meeting the needs of modern technology fields for high-performance, high-reliability products.
Chip Package Substrates design Reference Guide.
Chip Package Substrates (microchip package substrates) are an indispensable part of modern electronic products, and their design directly affects the performance and reliability of the product. The following is a reference guide on Chip Package Substrates design, designed to help engineers better understand and apply this key technology.
Material selection
Material selection for Chip Package Substrates is crucial. Conductive materials (such as copper) are used for circuit connections, insulating materials are used to isolate and protect circuits, and other special materials are used to achieve specific functions, such as heat dissipation, corrosion protection, etc. When selecting materials, factors such as thermal conductivity, mechanical strength, and corrosion resistance need to be considered, and a reasonable combination should be made based on specific application requirements.
Lamination process
Chip Package Substrates are usually multi-layer structures, and the lamination process is one of the key steps in their manufacturing process. During the lamination process, each layer of material is heated and compacted to form a complete packaging substrate. Engineers need to pay attention to the control of lamination parameters to ensure bonding quality and thickness uniformity between layers to ensure the quality and performance of the packaging substrate.
Patterned design
Pattern design is an important part of Chip Package Substrates design. Through patterning, engineers can form various circuit connections and component layouts on the substrate to realize circuit functions. During the patterning process, parameters such as line width, spacing, and interlayer connections need to be considered to meet the requirements of circuit design and ensure the feasibility and stability of the manufacturing process.
Thermal design
Good thermal design is crucial for microchip packaging substrates. Engineers need to consider the layout and material selection of the heat dissipation structure during the design process to improve the heat dissipation efficiency of the packaging substrate and ensure the stability and reliability of the microchip during long-term operation. Common heat dissipation designs include heat sinks, heat dissipation holes, etc.
Reliability verification
After the Chip Package Substrates design is completed, engineers need to conduct reliability verification to ensure that the performance and reliability of the package substrate meet the design requirements. Reliability verification includes simulation, process verification, environmental testing, etc. to verify the stability and reliability of the packaging substrate under various working conditions.
Through the above design reference guide, engineers can better understand and apply Chip Package Substrates technology, improve the quality and efficiency of product design, and promote the development and innovation of the electronic product industry.
What material is used in Chip Package Substrates?
The material selection of Chip Package Substrates directly affects the performance and characteristics of the packaging substrate. When designing and manufacturing Chip Package Substrates, engineers need to carefully consider the properties of different materials to meet specific application needs. Here are some common Chip Package Substrates materials and their characteristics:
High thermal conductivity metals (such as copper)
Copper is a commonly used conductive metal with excellent thermal conductivity. In Chip Package Substrates, copper is often used to make wires and connectors to ensure good electrical connections and signal transmission. Its excellent thermal conductivity also helps dissipate heat, thereby improving the performance and stability of the microchip.
High temperature resistant ceramic material
Ceramic materials have excellent high temperature resistance and chemical stability, and can still maintain stable physical and chemical properties in high temperature environments. In some high-temperature application scenarios, such as automotive electronics and aerospace, ceramic substrates are often selected as Chip Package Substrates to ensure the reliability and stability of microchips under extreme conditions.
High strength polymer material
Polymer materials have the characteristics of lightweight, high strength, corrosion resistance, etc., and are widely used in some applications requiring lightweight and high strength. In electronics, polymer materials are often used to make insulating layers and structural supports for packaging substrates to provide the necessary structural strength and electrical isolation.
Different application scenarios and requirements may require different material combinations. For example, in the field of high-performance computing, it may be necessary to combine high thermal conductivity metal and ceramic materials to achieve excellent heat dissipation and electrical performance; while in portable electronics, more emphasis is placed on lightweight and structural strength, and polymers may be chosen. material as the main substrate material.
In general, the material selection of Chip Package Substrates should comprehensively consider factors such as electrical performance, thermal conductivity, mechanical properties, chemical stability, etc., to meet the needs of specific application scenarios and ensure the performance and reliability of the microchip.
What size are Chip Package Substrates?
The size of Chip Package Substrates is one of the crucial considerations in design and application. Their size is typically based on specific application requirements and product design, and therefore can vary widely.
In many applications, Chip Package Substrates often need to be small enough to fit into compact electronic product designs. For example, smartphones, tablets, and portable electronic devices often require smaller packaging substrates to ensure thinness, lightness, and portability. In these cases, the size of Chip Package Substrates is often limited to a few centimeters to coordinate the layout with other components and parts.
On the other hand, some high-performance and industrial-grade applications may require larger size Chip Package Substrates. For example, high-performance servers, data center equipment and industrial automation systems often require larger packaging substrates to accommodate more chips, connectors and other components. In these cases, the size of Chip Package Substrates may reach tens of centimeters or even larger to meet the requirements of complex circuits and functions.
In addition, there are some special applications that require very small or very large Chip Package Substrates. For example, in the fields of microelectronics, medical devices, and aerospace, tiny packaging substrates may be required to achieve a high degree of integration and miniaturization, while in some industrial equipment and power systems, larger packaging substrates may be required to carry more power. and current.
In short, the size of Chip Package Substrates depends on its specific application scenarios and product design needs. Therefore, when designing and selecting Chip Package Substrates, the impact of size on overall product performance and functionality needs to be carefully considered to ensure optimal design and performance.
The Manufacturer Process of Chip Package Substrates.
The manufacturing process of Chip Package Substrates is a complex and precise process involving multiple key steps. Each step requires a high degree of technical and equipment support to ensure that the quality and performance of the packaging substrate meet the design requirements.
The first is the design phase, which is the basis of the entire manufacturing process. During the design phase, engineers determine the layout, hierarchy, and circuit connections of the package substrate based on the product’s needs and specifications. They use professional design software to draw the schematics and wiring diagrams of the packaging substrate to ensure that the circuit connections are accurate.
Next comes the material selection stage. When manufacturing Chip Package Substrates, it is necessary to select suitable substrate materials, conductive layer materials, insulating materials and other special materials. The selection of these materials will directly affect the performance and characteristics of the packaging substrate and therefore requires careful consideration and testing.
Then comes the lamination stage. In the lamination process, designed layers of materials are stacked together and high temperatures and pressures are used to hold them together. This ensures that the packaging substrate is structurally sound and will not deform or crack due to temperature changes or mechanical stress.
Drilling is the next critical step. At this stage, precision drilling equipment is used to drill holes into the package substrate for circuit connections and component installation. These holes must be accurately positioned, consistent in size, and have a smooth surface to ensure smooth subsequent processes.
Next is the metallization stage. During the metallization process, a conductive layer is formed on the surface of the packaging substrate through chemical methods or physical plating. These conductive layers will be used for circuit connections and signal transmission, so they must have good conductivity and corrosion resistance.
The last is the patterning stage. During the patterning process, photolithography is used to transfer the designed circuit pattern to the surface of the packaging substrate. Chemical etching or etching is then used to remove the excess metal layer, leaving the required circuit connections and component soldering areas.
To sum up, the manufacturing process of Chip Package Substrates involves multiple key steps such as design, material selection, lamination, drilling, metallization, and patterning. These steps require highly sophisticated equipment and technical support to ensure that the quality and performance of the packaging substrate meet design requirements, thereby ensuring the reliability and stability of electronic products.
The Application area of Chip Package Substrates.
Chip Package Substrates (CPS) are widely used in modern electronic products, and their performance and stability are directly related to the overall performance and reliability of the product. Smartphones are one of the most typical applications. In the design of smartphones, CPS plays a key role in connecting various chips and circuits. Not only do they need to be small in size to fit into the compact design of mobile phones, they also need to have high-speed signal transmission and good heat dissipation to ensure the performance and stability of mobile phones. In the computer field, CPS is also one of the indispensable components. From motherboards to memory, processors and graphics processors, various computer components require CPS for connectivity and packaging. The performance of CPS directly affects the running speed, stability and power consumption efficiency of the computer. In the field of automotive electronics, CPS also plays an important role. Modern cars are equipped with a large number of electronic devices, including engine control units, safety systems, entertainment systems, etc. These devices all require high-performance CPS for connection and packaging. The reliability of CPS is directly related to the safety and stability of the car. Communication equipment is also one of the important application areas of CPS. From base stations to network equipment, wireless communication systems require a large amount of CPS to implement signal processing and data transmission. The performance of CPS directly affects the signal transmission speed and stability of communication equipment. In general, Chip Package Substrates are widely used in various electronic products, and their performance and stability directly affect the overall performance and reliability of these products. In the ever-evolving electronics industry, CPS will continue to play an important role in promoting technological progress and product innovation.
What are the advantages of Chip Package Substrates?
Chip Package Substrates have significant advantages in electronic product design, and these advantages make it the first choice among many packaging technologies. Compared with other packaging technologies, Chip Package Substrates can achieve a higher level of integration. Through miniaturized design and multi-layer structure, Chip Package Substrates can accommodate more functional modules and components in a limited space, thereby realizing functional integration of electronic products and improving product performance and functionality.
In addition, Chip Package Substrates also have better heat dissipation effect. Since microchips operate at high temperatures, good heat dissipation capabilities are crucial to maintaining stable operation of microchips. Chip Package Substrates adopt excellent thermal conductive materials and designs, which can effectively conduct heat from the chip to the external environment, maintain the normal operating temperature of the chip, and avoid performance degradation and failure caused by overheating.
In addition, Chip Package Substrates have lower power consumption. Optimized design and material selection can reduce circuit power consumption, extend battery life, and improve the energy efficiency ratio of electronic products, thus complying with the development trend of energy conservation and environmental protection.
Most importantly, Chip Package Substrates offer greater reliability and stability. Its precise manufacturing process and high-quality materials ensure the quality and stability of the packaging substrate. It can run stably for a long time under various environmental conditions and is not susceptible to external interference and damage, ensuring the long-term reliability of electronic products.
To sum up, Chip Package Substrates have many advantages in electronic product design, including high integration, excellent heat dissipation, low power consumption, and high reliability and stability. They are suitable for various complex electronic product designs and will Provide important support for the performance improvement and reliable operation of electronic products.
FAQ
What types of electronic products are Chip Package Substrates suitable for?
Chip Package Substrates are suitable for a wide range of electronic products, whether consumer electronics or industrial equipment. In terms of consumer electronics, such as smartphones, tablets, laptops, digital cameras, etc., Chip Package Substrates play a key role. They provide stable circuit support and connections to ensure the performance and stability of the device. In addition, Chip Package Substrates are also widely used in the automotive electronics field for control systems, infotainment systems, etc. Communication equipment, industrial control equipment and medical electronic equipment are also one of the important application areas of Chip Package Substrates.
Is the manufacturing process of Chip Package Substrates complicated?
The manufacturing process of Chip Package Substrates requires a high degree of precision and technical requirements, so it can be said to be complex. The manufacturing process usually includes design, material selection, lamination, drilling, metallization, patterning, etc. Each link requires sophisticated equipment and technology to ensure the quality and performance of the packaging substrate. For example, the lamination process requires strict control of temperature and pressure to ensure a strong and even bond between different layers of materials. The patterning process requires high-precision photolithography to create circuit patterns to ensure the circuit’s connection and conductive properties. Although the manufacturing process is complex, with the continuous advancement of modern manufacturing technology, production efficiency has been significantly improved, thereby reducing manufacturing costs and improving product quality.
What are the advantages of Chip Package Substrates compared to other packaging technologies?
Compared with other packaging technologies, Chip Package Substrates have many advantages. First, Chip Package Substrates can achieve a higher level of integration, integrating multiple electronic components onto a single package substrate, thereby reducing the size and volume of the circuit board and improving the compactness of the device. Secondly, Chip Package Substrates have good heat dissipation performance. Through appropriate design and material selection, they can effectively dissipate the heat generated by electronic components and improve the stability and reliability of the equipment. In addition, Chip Package Substrates have good signal transmission performance and conductive properties, which can meet the requirements of high-speed data transmission and complex circuit design. Most importantly, Chip Package Substrates have relatively low manufacturing costs and are suitable for mass production, thereby reducing the manufacturing costs of electronic products and improving the competitiveness of products.