Ceramics Substrate Manufacturer.A leading ceramics substrate manufacturer, renowned for precision and innovation in material engineering, specializes in crafting high-performance substrates for diverse industries. With state-of-the-art facilities and a dedicated team of experts, they meticulously design and produce substrates tailored to exact specifications, ensuring superior thermal conductivity, mechanical strength, and electrical insulation. Their commitment to quality extends from rigorous quality control measures to continuous research, driving advancements in ceramic technology. Trusted by global clients, they provide reliable solutions for critical applications, establishing themselves as pioneers in the field of ceramic substrate manufacturing.
In today’s digital age, the rapid development of electronic technology has made our lives increasingly intelligent and convenient. As one of the core components of many electronic devices, ceramic substrates play a vital role in various fields. This article will delve into the critical role of ceramic substrates in the modern electronics industry and explore their wide range of applications and importance.
What is Ceramics Substrate?
Ceramic substrate, also known as Ceramics Substrate, is a substrate material used to support and connect electronic components, which plays an important role in circuit boards. Compared with traditional substrate materials, ceramic substrates have excellent thermal conductivity and insulation properties, so they perform well in harsh environments such as high temperature and high frequency.
Material composition
Ceramic substrates are usually made of ceramic materials such as aluminum oxide (Alumina) or aluminum nitride (AlN). Aluminum oxide is one of the most commonly used ceramic substrate materials and has good mechanical strength and chemical stability, making it suitable for most general applications. Aluminum nitride has higher thermal conductivity and insulation properties and is suitable for applications with higher heat dissipation requirements.
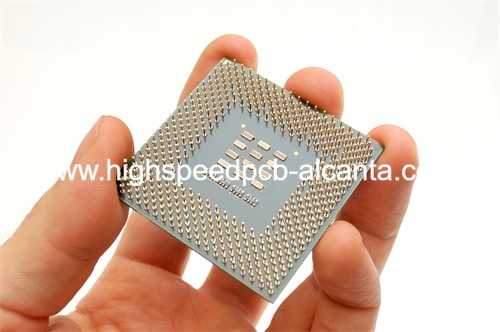
Ceramics Substrate Manufacturer
Excellent performance
The excellent performance of ceramic substrates stems from their material properties. First of all, ceramic materials have excellent thermal conductivity and can effectively dissipate heat and maintain a stable operating temperature of electronic components. Secondly, ceramic materials have good insulation properties, which can prevent short circuits and leakage between electronic components and ensure the reliability and safety of the circuit. In addition, ceramic substrates also have good corrosion resistance and mechanical strength, and can adapt to working conditions in various harsh environments.
Application areas
Ceramic substrates are widely used in many fields, especially in electronic equipment in high-frequency, high-power and high-temperature environments. For example, power modules, radio frequency devices, LED lighting, sensors and other fields often use ceramic substrates as key components. Its stable performance and reliable operating characteristics make it the first choice for many critical applications.
As an important electronic substrate material, ceramic substrate has excellent thermal conductivity, insulation and corrosion resistance, and plays an irreplaceable role in the modern electronic field. With the continuous development and advancement of science and technology, ceramic substrates will continue to play an important role in promoting the development and innovation of the electronics industry.
Ceramics Substrate design Reference Guide.
Designing ceramic substrates is a complex and critical task that directly affects the performance and reliability of electronic devices. When designing ceramic substrates, many factors need to be considered, including circuit layout, thermal management, material selection, etc. Here are some key steps and best practices to help ensure substrate performance and reliability:
Circuit layout
When designing ceramic substrates, proper circuit layout is crucial. A good layout can minimize signal interference and electromagnetic interference and improve the stability and reliability of the circuit. The length of signal lines should be minimized and crossover and loopback wiring should be avoided to reduce loss and delay during signal transmission.
Thermal management
Ceramic substrates have good thermal conductivity, but thermal management still requires attention in high-power applications. During the design process, radiators, heat dissipation holes, and heat dissipation pads should be reasonably arranged to ensure that heat can be effectively conducted and dissipated to avoid damage to electronic components due to overheating.
Material selection
When selecting materials, a reasonable selection should be made based on specific application requirements and environmental conditions. Commonly used ceramic materials include alumina, aluminum nitride, etc. They have good high temperature resistance, corrosion resistance and insulation properties, and are suitable for various harsh working environments.
Design Codes and Standards
When designing ceramic substrates, relevant design specifications and standards should be followed to ensure that the design meets industry requirements and can successfully pass testing and certification. Being familiar with and following relevant standards can reduce design risks and improve design reliability and stability.
Simulation and testing
After the design is completed, simulation and testing should be performed to verify the performance and reliability of the design. Through electromagnetic compatibility analysis, thermal simulation, etc. through simulation software, potential problems can be discovered early and adjusted and optimized, thereby improving the success rate and efficiency of the design.
Designing ceramic substrates is a complex and precise task that requires comprehensive consideration of various factors and appropriate measures for optimization. By following the above design reference guide, you can ensure that the substrate design meets the requirements and has excellent performance and reliability, providing reliable guarantee for the smooth operation of electronic equipment.
What material is used in Ceramics Substrate?
As an important part of the electronic field, ceramic substrate material selection is crucial. Typically, ceramic substrates are made of high-performance ceramic materials such as aluminum oxide and aluminum nitride. These materials have a range of excellent properties that make them ideal for many electronic applications.
First of all, alumina, as one of the commonly used materials for ceramic substrates, has excellent thermal conductivity and insulation properties. It can effectively conduct heat to the substrate surface and disperse heat to the surrounding environment, thereby ensuring the stable operation of electronic devices in high-temperature environments. In addition, alumina has good corrosion resistance and can resist the erosion of chemicals and humidity, ensuring long-term reliable operation of the substrate.
On the other hand, aluminum nitride is also one of the common choices for ceramic substrates, especially in high-power and high-frequency applications. Aluminum nitride has higher thermal conductivity and better mechanical strength, allowing it to withstand higher temperatures and greater pressures. This makes aluminum nitride substrates widely used in applications requiring higher performance, such as radio frequency devices, power modules, etc.
Overall, ceramic materials such as aluminum oxide and aluminum nitride play a vital role in the manufacturing of ceramic substrates. They not only have excellent thermal conductivity, corrosion resistance and insulation properties, but also can meet the requirements of various harsh working environments. Therefore, whether in consumer electronics or industrial fields, ceramic substrates are a reliable and efficient choice, providing a solid foundation for the stable operation of electronic equipment.
What size are Ceramics Substrate?
Ceramic substrates are very flexible in size and can be customized to meet specific application requirements. This diversity allows ceramic substrates to play a role in a variety of electronic devices, from microelectronics to large industrial equipment, which may use ceramic substrates in different sizes and shapes.
In microelectronic devices, ceramic substrates are often very small and delicate in size. For example, in portable electronic products such as smartphones, tablets, and wearable devices, micro ceramic substrates are often used to save space and achieve higher integration. These substrates often have complex designs that can accommodate multiple electronic components and provide good electrical performance and heat dissipation.
On the other hand, in large industrial equipment, the size of ceramic substrates may be larger and more complex. For example, in the field of power electronics, ceramic substrates used for high-voltage power modules are usually larger to accommodate more power devices and circuits. These large substrates may need to have higher mechanical strength and thermal stability to cope with harsh operating environments and high power densities.
In addition, the shape of the ceramic substrate can also be varied according to specific application requirements. In addition to common rectangular and square substrates, they can also be customized into various special shapes, such as circular, oval or even irregular shapes, to suit the design requirements of specific equipment.
Overall, the diversification of ceramic substrate sizes provides greater flexibility and choice for the design and manufacturing of electronic devices. Whether it is a micro or large device, ceramic substrates can meet a variety of application needs with their excellent performance and reliability.
The Manufacturer Process of Ceramics Substrate.
The manufacturing process of ceramic substrates is a complex and precise process that involves multiple links to ensure the quality and performance stability of the substrates. Here’s a closer look at the process:
Material preparation
The first step in making ceramic substrates is to prepare the materials. Typically, high-performance ceramics such as aluminum oxide or aluminum nitride are used as substrate materials. These materials need to undergo rigorous screening and processing to ensure that their chemical composition and physical properties meet the requirements.
Forming
After the material is prepared, the ceramic powder is mixed with relevant additives and made into a substrate of the required size and shape through a molding process. The molding process can use injection molding, press molding and other methods to ensure that the substrate has the required geometry and structure.
Sintering
After forming, the ceramic substrate needs to be sintered to increase its density and mechanical strength. Sintering is to place the formed substrate in a high-temperature environment so that its particles combine and form a dense structure. This process is usually performed in a high-temperature furnace and requires strict control of temperature and atmosphere to ensure the quality and performance of the substrate.
Processing
The sintered ceramic substrate needs to be processed to achieve the final size and surface accuracy requirements. The processing process includes cutting, drilling, surface grinding and other processes to ensure that the flatness and geometric accuracy of the substrate meet the design requirements. This step requires high-precision processing equipment and the exquisite skills of technicians.
Test
Finally, manufactured ceramic substrates undergo rigorous testing to ensure their quality and performance. Testing includes visual inspection, dimensional inspection, electrical performance testing and other aspects. Only substrates that pass various tests and meet standard requirements can be considered qualified and can enter the next stage of production or application.
In short, the manufacturing process of ceramic substrates involves multiple complex links, requires sophisticated equipment and technology, and has strict quality control requirements for each link. The exquisite application of these processes ensures the stability and reliability of the substrate, making it an indispensable and important component in various electronic devices.
The Application area of Ceramics Substrate.
Ceramic substrates are widely used in the electronics industry, and their excellent properties make them the first choice for many critical applications. In terms of power modules, ceramic substrates can effectively manage power distribution and provide good heat dissipation performance, so they are widely used in various power converters, inverters and power modules. The manufacturing of RF devices is also inseparable from ceramic substrates, because they can provide stable dielectric constant and low loss, thereby ensuring signal transmission quality and stability. The LED lighting industry is also one of the important application fields of ceramic substrates. Its excellent thermal conductivity can effectively reduce the operating temperature of the LED chip, extend its service life, and ensure the stability and brightness of the light source. In addition, ceramic substrates are also widely used in sensor manufacturing, such as pressure sensors, temperature sensors, and gas sensors. The ceramic substrate can provide a stable support structure and good electrical insulation properties to ensure the accuracy and reliability of the sensor. In general, the wide application of ceramic substrates in the electronics industry fully reflects its advantages in thermal management, electrical performance and reliability, and plays an important role in the performance improvement and innovation of modern electronic equipment.
What are the advantages of Ceramics Substrate?
As an important part of the modern electronic field, ceramic substrates have unique advantages among many substrate materials. Ceramic substrates offer many advantages over traditional substrate materials, making them the first choice for many critical applications.
First, ceramic substrates have higher thermal conductivity. Its excellent thermal conductivity enables heat to be efficiently conducted from electronic components to the surface of the substrate and then dissipated to the surrounding environment. This helps maintain a stable operating temperature for electronic devices and avoid performance degradation or damage caused by overheating.
Secondly, ceramic substrates have better high temperature resistance. In high-temperature working environments, traditional substrate materials may lose their stability due to excessive temperatures, causing the performance of electronic devices to be damaged or even fail to work properly. The ceramic substrate can withstand higher operating temperatures, maintain its stability and reliability, and ensure long-term stable operation of the equipment.
In addition, ceramic substrates also have superior mechanical strength. Its high strength and wear resistance allow the ceramic substrate to maintain its integrity in various harsh environments and is not susceptible to external impact or vibration. This makes ceramic substrates outstanding in demanding industrial applications and capable of long-term stable operation.
To sum up, ceramic substrates provide stable and reliable basic support for electronic devices with their high thermal conductivity, excellent high temperature resistance and excellent mechanical strength. Whether in industrial applications in extreme environments or in consumer electronics in daily life, ceramic substrates can play an important role in ensuring efficient operation and long-term stability of equipment.
FAQ
What are the advantages of ceramic substrates compared to other substrates?
Ceramic substrates have excellent thermal conductivity and high temperature resistance, and can maintain stable performance in extreme working environments. Compared with traditional substrate materials, such as FR-4, ceramic substrates have better mechanical strength and chemical corrosion resistance, and are suitable for various harsh application scenarios.
What is the cost of ceramic substrates?
Due to the particularity of ceramic substrate materials and manufacturing processes, its cost is usually higher. However, given their excellent performance and long-term stability, ceramic substrates remain a value-for-money choice in many high-end applications.
What are the design considerations for ceramic substrates?
When designing ceramic substrates, special attention needs to be paid to thermal management, interlayer connections, surface treatment, etc. Reasonable wiring design and heat dissipation design can improve the performance and reliability of the substrate.
Are ceramic substrates susceptible to mechanical damage?
Ceramic substrates usually have high mechanical strength and can resist a certain degree of mechanical shock and vibration. However, under extreme circumstances, such as severe physical impact or bending, it is still possible to cause the substrate to crack or be damaged.
How environmentally friendly are ceramic substrates?
Most ceramic substrate materials are inorganic materials and have good environmental adaptability and eco-friendliness. In addition, the long life and reliability of ceramic substrates can reduce the amount of electronic waste generated and benefit environmental protection.