Ceramic Packages For MEMS Sensors Manufacturing.Ceramic packages play a pivotal role in the manufacturing process of MEMS sensors, encapsulating delicate micro-electromechanical systems with precision and durability. These meticulously crafted casings provide a shield against external influences, ensuring the sensors’ functionality remains intact in diverse environments. Employing advanced techniques, manufacturers intricately design and fabricate ceramic packages to meet stringent quality standards. Their high thermal conductivity and mechanical stability safeguard the sensitive components within, enabling optimal sensor performance. Through meticulous attention to detail, ceramic packages exemplify the fusion of engineering excellence and material innovation in the realm of MEMS sensor manufacturing.
In the field of microelectromechanical system (MEMS) sensor manufacturing, ceramic packaging is a crucial key technology. It not only provides reliable mechanical support, but also effectively protects the sensor from the external environment. Through ceramic packaging, MEMS sensors can operate stably and maintain high performance under various harsh conditions.
What is a ceramic package?
As a key technology, ceramic packaging plays an important role in the manufacturing of microelectromechanical systems (MEMS) sensors. Its design and manufacturing process aims to provide solid mechanical support and reliable environmental protection for MEMS sensors to ensure normal operation and long-term stability of the sensors under various external environmental conditions.
First, ceramic packaging provides superior mechanical support for MEMS sensors. MEMS sensors are usually composed of tiny mechanical structures, such as micro vibrators, pressure sensors, etc. These structures are very tiny and fragile and need to be well supported to avoid mechanical damage. The high strength and hardness of ceramic materials make them excellent packaging material choices, which can effectively protect the internal structure of the sensor and prevent it from being damaged by external shock and vibration during use.
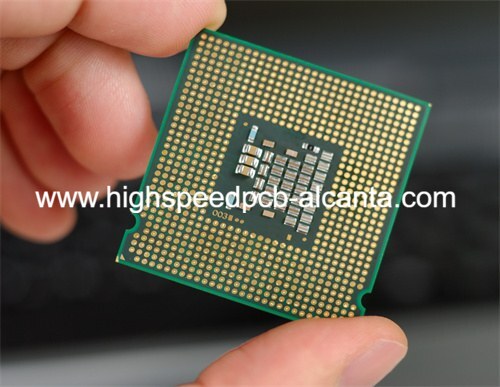
Ceramic Packages For MEMS Sensors Manufacturing
Secondly, ceramic packaging can also provide reliable environmental protection. MEMS sensors often need to work in harsh environmental conditions, such as high temperature, high humidity or corrosive gas environments. Ceramic materials have excellent chemical stability and high temperature resistance, which can effectively resist erosion and damage from the external environment and ensure the stable operation of the internal components of the sensor. In addition, the ceramic package also has good sealing performance, which can effectively isolate the inside of the sensor from the external environment and prevent the intrusion of external substances such as dust and water vapor, further improving the reliability and service life of the sensor.
In general, the ceramic package not only provides a solid mechanical support for the MEMS sensor, but also provides reliable environmental protection to protect the sensor from the external environment. Its application in sensor manufacturing provides an important guarantee for the performance and stability of the sensor, and promotes the widespread application and development of MEMS technology in various fields.
How to design a ceramic package?
Designing a ceramic package is a complex and critical process that involves multiple steps, from material selection to final structural design. Each step requires careful consideration to ensure that the final package can meet the performance requirements of the MEMS sensor.
First, material selection is one of the first considerations when designing ceramic packages. When selecting materials, engineers need to consider the thermal stability, chemical stability, and mechanical strength of ceramics. Commonly used ceramic materials include aluminum oxide, silicon nitride, etc., which have good high-temperature stability and chemical inertness, and are very suitable for packaging MEMS sensors with strict requirements.
Secondly, determining dimensions is another critical step in the design process. The size of the package needs to match the size of the MEMS sensor and take into account the allocation of space inside the package to accommodate the sensor components and connection lines. In addition, the external dimensions of the package also need to take into account the requirements of the final application scenario, such as the space constraints of assembly in the device.
Next comes the structural design phase, where engineers need to consider the layout, layering and connections of the package. This includes determining the number of layers for the package, laying out the location of the sensor elements, and designing the routing scheme for the wires and pins. Through modeling and simulation with CAD software, engineers can simulate packaging of different structures and optimize layout and connection methods to achieve the best performance and reliability.
Finally, optimization of ceramic process parameters is a key step to ensure packaging quality. This includes the control of process parameters such as sintering temperature, pressure, and time, as well as the optimization of subsequent processes such as surface treatment and coating of protective layers. Through precise process control and equipment operation, it is possible to ensure that the ceramic package has high quality and stability and meets the strict requirements of MEMS sensors.
To sum up, designing ceramic packages is a complex process that comprehensively considers many aspects such as materials, size, structure and process parameters. Through modeling and simulation with CAD software, engineers can accurately design a packaging structure that meets the performance requirements of MEMS sensors, providing an important guarantee for the reliable operation of the sensor.
What is the manufacturing process of ceramic packaging?
The manufacturing process of ceramic packages is a complex and precise process, which usually includes multiple key steps such as raw material preparation, molding, sintering and surface treatment. First, manufacturing ceramic packages requires the selection of high-quality ceramic raw materials suitable for high temperature and chemical stability, such as aluminum oxide or silicon nitride. These raw materials are precisely processed and screened to ensure that their quality and performance meet packaging requirements.
Secondly, molding is one of the important steps in manufacturing ceramic packages. During the molding process, carefully designed molds press the ceramic raw material into the desired shape and size. This process requires a high degree of precision and stability to ensure the consistency and accuracy of the final package.
Next comes the sintering stage, which is one of the key steps in manufacturing ceramic packages. In a high-temperature furnace, the formed ceramic parts are exposed to high temperatures for sintering, so that they become dense materials with good mechanical strength and chemical stability. The sintering process requires strict control of temperature and time to ensure that the quality and performance of ceramic parts meet expected requirements.
Finally, surface treatment is performed to further improve the performance and reliability of the ceramic package. Surface treatment can include cleaning, protective layer coating, drilling and other processes to ensure that the surface of the package is smooth, clean, and has good connectivity and solderability.
Through precise process control and equipment operation, ceramic packaging manufacturers are able to achieve high quality and stable products. These precision manufacturing processes ensure the durability and reliability of ceramic packages, making them the packaging solution of choice for a variety of demanding applications.
How much does a ceramic package cost?
The cost of ceramic packaging is one of the important factors to consider when developing manufacturing plans. These costs are affected by a variety of factors, including size, complexity, material selection, and manufacturing processes.
First, the size of the package has a direct impact on cost. Larger size ceramic packages require more materials and processes, so the cost is relatively high. In addition, although smaller packages consume less material, the manufacturing process may be more difficult, which will also have an impact on costs.
Secondly, the complexity of packaging is one of the important factors that determine the cost. Complex packaging structures may require more production processes and equipment, as well as higher levels of technical requirements, thereby increasing manufacturing costs. In comparison, the cost of simple packaging structures is relatively low.
Material selection also directly affects the cost of ceramic packaging. Different ceramic materials have different properties and costs. Generally speaking, high-quality ceramic materials have a higher price, but also provide better performance and reliability.
Finally, the manufacturing process is one of the important factors affecting the cost of ceramic packaging. High-precision manufacturing processes and equipment usually require higher investment costs, but they can also ensure the quality and stability of packaging. The low-cost manufacturing process may reduce the quality and reliability of the package, thereby increasing the cost of subsequent maintenance and repair.
Overall, the cost of high-quality ceramic packages is usually relatively high, but these costs are acceptable compared with the performance and reliability they bring. Therefore, when developing a manufacturing plan, factors such as size, complexity, material selection, and manufacturing processes need to be considered to find the ceramic packaging solution that best suits the project needs.
What materials are used in ceramic packages?
Ceramic packaging plays a vital role in MEMS sensor manufacturing, and its material selection directly affects the performance and reliability of the package. Common ceramic packaging materials mainly include high-temperature stability materials such as aluminum oxide and silicon nitride.
First, alumina (Al2O3) is a commonly used ceramic packaging material with good mechanical strength and chemical stability. Aluminum oxide performs well in high-temperature environments and resists thermal stress and chemical corrosion, making it suitable for use in demanding MEMS sensor packaging. Its excellent insulating properties also make aluminum oxide an ideal choice for electrical insulation, helping to protect sensor elements from external interference.
Secondly, silicon nitride (Si3N4) is also a common ceramic packaging material. Silicon nitride has excellent high temperature stability and mechanical properties and can withstand extreme conditions in high temperature environments. At the same time, silicon nitride has good wear resistance and chemical inertness, and can effectively protect MEMS sensors from mechanical damage and corrosion. Due to its excellent performance, silicon nitride is widely used in the packaging of high-performance MEMS sensors to ensure stable operation of sensors in harsh environments.
To sum up, aluminum oxide and silicon nitride are two commonly used ceramic packaging materials. They have excellent properties such as high temperature stability, mechanical strength and chemical stability, and are very suitable for packaging MEMS sensors with strict requirements. By rationally selecting and optimizing packaging materials, the performance and reliability of MEMS sensors can be effectively improved to meet the needs of different application scenarios.
Who makes ceramic packages?
In terms of manufacturing ceramic packages, major suppliers include professional packaging manufacturers and MEMS sensor manufacturers. Among them, as a professional electronic component manufacturing company, our company is also one of the main suppliers of ceramic packaging.
The company has advanced production equipment and technical teams and is committed to providing customers with high-quality, customized ceramic packaging solutions. We adopt a strict quality management system to ensure that every production link meets high standards of quality requirements. From material procurement to molding, sintering, and surface treatment, we strictly control every detail to ensure the stability and reliability of ceramic packaging.
As a packaging supplier with many years of experience, the company also focuses on close cooperation with customers. We have an in-depth understanding of our customers’ needs and application scenarios, and provide professional technical support and customized solutions to meet our customers’ individual needs.
In addition to the manufacturing of ceramic packages, the company also provides a series of value-added services, including package design optimization, cost control advice, production process optimization, etc., to help customers improve production efficiency and reduce costs.
In general, as a professional electronic component manufacturing company, our company has rich experience and professional technical strength in the field of ceramic packaging, and is able to provide customers with high-quality, customized packaging products and services.
What are the five qualities of great customer service?
Excellent customer service is one of the key factors in the success of any business. In the modern competitive market environment, providing excellent customer service not only enhances customer loyalty, but also establishes a good reputation for the company. Here are five key attributes of great customer service:
Responding promptly when customers need help or have questions is crucial. By quickly responding to customer inquiries and concerns, the company demonstrates its importance and concern for customers, enhancing customers’ trust in the company. Whether it’s by phone, email, or online chat, you should ensure that you communicate with your customers in a timely and effective manner.
When dealing with customer issues, it’s crucial to treat your customers’ needs with empathy. Understanding customers’ pain points and needs, and providing full understanding and care can enhance customer satisfaction and establish good customer relationships. By actively listening to customer feedback and suggestions and providing customers with personalized solutions, you can enhance customer trust and loyalty.
Reliability means that a company consistently delivers on its promises, ensuring customer trust. Whether it is product delivery time, service quality or after-sales support, it should maintain a stable and reliable level. By establishing a sound service process and quality management system, we ensure that customers can receive stable and consistent high-quality services, thereby enhancing customer confidence and trust in the company.
Clear and transparent communication is the basis for building good customer relationships. During the service process, conveying important information to customers in a timely manner and maintaining smooth and transparent communication can reduce misunderstandings and dissatisfaction and improve customer satisfaction. At the same time, proactively communicate with customers to understand their needs and feedback, which will help to adjust and improve services in a timely manner and enhance customer experience.
Actively solving customer problems and striving to achieve customer satisfaction are important manifestations of high-quality customer service. When customers encounter problems or difficulties, companies should act quickly, provide effective solutions, and ensure that the problem is completely resolved. By resolving issues promptly, you not only maintain customer satisfaction but also build your business’s reputation for customer service.
To sum up, excellent customer service not only requires key attributes such as responsiveness, empathy, reliability, communication skills and problem-solving skills, but also requires the joint efforts and continuous improvement of all employees of the enterprise to ensure that customers receive the best service experience, thereby achieving the company’s long-term development goals.
Frequently Asked Questions
What are the primary applications of ceramic packaging for MEMS sensors?
Ceramic packaging for MEMS sensors finds application across various industries, including automotive electronics, industrial automation, aerospace, and medical devices. Its high temperature stability, corrosion resistance, and mechanical strength make it ideal for demanding environments where reliable sensor performance is critical.
Can ceramic packaging be customized to specific design requirements?
Yes, ceramic packaging can be customized to meet specific design requirements, including dimensional specifications, thermal management needs, and integration with other components. Manufacturers often offer design consultation services to help optimize the packaging solution for the intended application.
What are the main challenges associated with ceramic packaging manufacturing?
Some of the main challenges in ceramic packaging manufacturing include achieving precise dimensional tolerances, ensuring uniform material properties, minimizing defects such as cracks or voids, and maintaining consistency in production processes. Addressing these challenges requires advanced manufacturing techniques and rigorous quality control measures.
Is ceramic packaging cost-effective compared to other packaging materials?
Ceramic packaging tends to have higher upfront costs compared to plastic or metal alternatives. However, its long-term durability, reliability, and performance benefits often justify the initial investment, especially for applications requiring high temperature resistance and robustness.