Ceramic package substrate Manufacturer, Ceramic substrate(PCB), 96AL2O3 Ceramic substrate(PCB), ALN Ceramic substrate(PCB) manufacture. we produce the Ceramic series materials PCB and package substrate from 1 layer to 16 layers.
Ceramic packaging substrate is a specialized substrate made of ceramic materials designed to provide reliable support and electrical connections to semiconductor devices. It plays an integral role in modern electronic design, providing superior performance and reliability for a variety of applications.
Key to Thermal Management: Ceramic packaging substrates are known for their excellent thermal management capabilities. This substrate can effectively conduct and dissipate the heat generated by the device, ensuring that the device maintains a stable operating temperature under high loads. They maintain equipment reliability and performance whether in high-power applications or under harsh environmental conditions.
Excellent electrical insulation properties: Another important feature of ceramic packaging substrates is their excellent electrical insulation properties. This characteristic makes the substrate play an important role in electronic systems, ensuring that problems such as short circuits or leakage of circuits do not occur. This reliable electrical insulation performance makes ceramic packaging substrates the preferred choice for many critical applications.
Guarantee of mechanical stability: Ceramic packaging substrates have excellent mechanical stability and can withstand vibration, impact and other external stresses. This stability ensures the reliability of the device in various working environments, thereby extending the service life of the equipment and reducing maintenance costs.
Overall, ceramic packaging substrates not only provide strong support and electrical connections, but also offer superior thermal management, electrical insulation, and mechanical stability. In electronic design, selecting the appropriate ceramic packaging substrate is one of the keys to ensuring device performance and reliability.
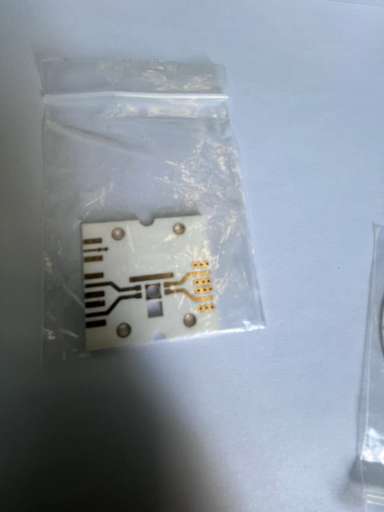
Ceramic PCB
What types of ceramic packaging substrates are there?
In PCB engineering, ceramic packaging substrates are widely used to meet various application requirements. These substrates are made from different types of ceramic materials, each with its own unique characteristics and applicable scenarios. The following are several common ceramic packaging substrate types:
Alumina ceramic substrates use aluminum oxide as the main component and have excellent thermal conductivity and mechanical strength. They are typically used in applications that require high thermal stability and durability, such as high-power electronics and electronic systems in high-temperature environments.
Aluminum nitride ceramic substrate uses aluminum nitride as the substrate material, which has excellent thermal conductivity and electrical insulation properties. This makes them excellent in high frequency and microwave applications such as RF power amplifiers and communications systems.
Silicon carbide ceramic substrate is made of silicon carbide material, which has high thermal conductivity and excellent high temperature resistance. They are commonly used in applications that require high thermal management capabilities and resistance to high temperature environments, such as automotive electronic systems and industrial control equipment.
Each type of ceramic packaging substrate is designed for specific application scenarios and needs, providing reliable performance and a stable working environment. Therefore, when selecting a ceramic packaging substrate, the most suitable type should be determined based on the project requirements and specific application scenarios.
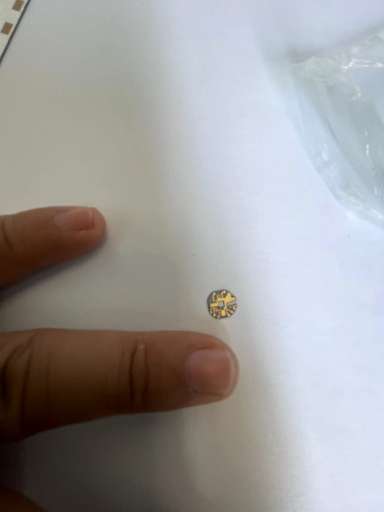
Ceramic PCB
Why choose ceramic package substrate instead of other boards?
In today’s world of electronic design, choosing the right substrate material is critical. Compared with traditional PCB (Printed Circuit Board, printed circuit board), ceramic packaging substrates show unparalleled advantages in performance and reliability, especially in extremely harsh environments. These advantages are mainly reflected in the following aspects:
Ceramic materials have excellent thermal conductivity and can effectively transfer heat away from the device, allowing for efficient thermal management. In high-power applications, such as power electronic equipment and high-performance computing systems, ceramic packaging substrates can effectively reduce temperatures and improve system stability and reliability.
Ceramic materials have excellent dielectric properties and low losses, providing good electrical insulation properties and high-frequency response. This makes ceramic packaging substrates widely used in high-frequency electronic equipment and RF/microwave applications, such as communication equipment and radar systems.
Compared with traditional organic substrates, ceramic packaging substrates have higher mechanical strength and stability, and can resist stress caused by vibration, impact and temperature changes. This makes them a first choice for aerospace systems, automotive electronics and other high-reliability applications.
Due to their excellent thermal management, electrical performance and mechanical stability, ceramic packaging substrates are able to maintain stable operation in extreme operating environments. Whether under harsh conditions such as high temperature, high humidity, high altitude or strong magnetic field, ceramic packaging substrates can ensure the reliability and long-term stability of electronic systems.
To sum up, ceramic packaging substrates have become the first choice for high-power applications, aerospace systems, automotive electronics and other fields due to their excellent performance advantages. When selecting substrate materials, fully considering the unique advantages of ceramic packaging substrates will help ensure the stability, reliability, and long-term performance of electronic systems.
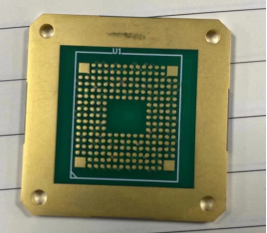
Ceramic Package Substrate
What is the manufacturing process of ceramic packaging substrates?
The manufacturing process of ceramic packaging substrates is a precise and complex process involving multiple critical steps to ensure that the quality and performance of the final product reaches the expected level. The following is a detailed description of the manufacturing process of ceramic packaging substrates:
First, the manufacturing process begins with the preparation of ceramic materials. This involves the process of grinding and mixing the raw ceramic materials to ensure uniformity and consistency of the material. This step is critical to the quality of the final product, as the quality of the material will directly affect the performance and stability of the substrate.
Next, the prepared ceramic material is used to create the substrate. This step can be accomplished by pressing or casting, depending on the manufacturing process chosen. Through these methods, ceramic materials are shaped into substrates of the desired size and shape.
Subsequently, the formed substrate is sent to a high-temperature sintering furnace for sintering treatment. At high temperatures, ceramic materials undergo physical and chemical changes that bring them to the desired density and strength. The key to this step is to control the sintering temperature and time to ensure the substrate has the desired physical properties.
After sintering is complete, the substrate is metallized and patterned. This means coating a substrate surface with a metal layer and using photolithography to print the desired circuit pattern onto the metal layer. These circuit patterns will become the final circuit paths, connecting the various electronic components.
Finally, the substrate is surface treated and inspected to ensure its quality and consistency. This includes cleaning and applying a protective coating to the substrate surface to prevent contamination and damage. At the same time, the size, shape and electrical properties of the substrate are rigorously inspected and tested to ensure compliance with specifications.
To sum up, the manufacturing process of ceramic packaging substrates is a precise and complex process that requires exquisite technology and strict quality control. Through this process, ceramic packaging substrates with excellent performance and stability can be produced, providing reliable support and connections for various electronic applications.
What are the applications of ceramic packaging substrates?
As a key electronic component, ceramic packaging substrate is widely used in various industries. The following are the specific applications of ceramic packaging substrates in different industries:
In the energy field, ceramic packaging substrates are widely used in power electronic equipment such as inverters, converters and motor drives. These devices require efficient thermal management and electrical performance, and ceramic substrates provide excellent thermal conductivity and electrical insulation properties to ensure stable operation of the device.
In the fields of communications and radar, ceramic packaging substrates are used in RF and microwave systems. These systems require high-frequency signal transmission and reception, and the low loss and excellent electrical properties of ceramic substrates make them an ideal choice, ensuring stable and reliable signal transmission.
In the aerospace and defense fields, ceramic packaging substrates are widely used in avionics, missile and satellite components. These components need to withstand extreme environmental conditions and challenges, and the high temperature resistance, corrosion resistance and mechanical strength of ceramic substrates enable them to maintain stable performance under harsh conditions.
In the medical field, ceramic packaging substrates are used in diagnostic equipment and implantable devices. These devices have extremely high requirements for precise signal processing and stable electrical performance, and the excellent characteristics of ceramic substrates ensure the reliability and accuracy of the devices.
In the automotive field, ceramic packaging substrates are used in automotive electronic equipment such as engine control units, sensors and safety systems. These devices need to withstand harsh conditions such as high temperatures, high pressures and vibrations, and the durability and stability of ceramic substrates make them the material of choice in automotive electronics.
In summary, ceramic packaging substrates play an important role in various industries, providing key support for the performance and reliability of electronic equipment, and promoting the continuous development and progress of modern technology.
Where can I find ceramic packaging substrates?
When looking for ceramic packaging substrates, you can look to reputable ceramic packaging substrate manufacturers. These manufacturers specialize in providing a variety of standard and customized solutions to meet specific project requirements. By working with these suppliers, you gain the following benefits:
First, these manufacturers have the experience and expertise to provide customized ceramic packaging substrate solutions based on your needs. Whether it is for a specific application scenario or in response to special requirements, they are able to provide personalized design and manufacturing services.
Second, reputable ceramic packaging substrate manufacturers focus on quality and consistency. They use advanced production processes and strict quality control measures to ensure that the substrates they produce meet high quality requirements. This focus on quality ensures product reliability and stability, providing a reliable foundation for your electronic design.
Additionally, these vendors focus on timely delivery to meet customer timelines. They usually have efficient production and logistics systems that can deliver products to customers in a timely manner, ensuring that projects can proceed as planned and avoid unnecessary delays and losses.
To sum up, working with a reputable ceramic packaging substrate manufacturer can provide you with comprehensive support and guarantee for your electronic design. They offer standard and custom solutions to meet a variety of project needs, and their commitment to quality, consistency and timely delivery gives you the confidence to choose them as your partner for successful project implementation.
What is the quotation of ceramic packaging substrate?
Pricing for ceramic packaging substrates varies based on many factors including material type, size, quantity, and specific customization requirements. As we know, different types of ceramic materials have different properties and costs. For example, aluminum oxide and aluminum nitride ceramic substrates are generally more affordable than other types of ceramic substrates, while silicon carbide ceramic substrates can be more expensive but offer excellent performance in high-temperature environments.
In addition to material type, size is also an important factor affecting cost. Larger substrate sizes typically increase material and processing costs. In addition, the quantity ordered will also affect the price. Generally speaking, the price of bulk order will be more competitive. Generally speaking, ordering in larger quantities may result in a better price.
In addition, specific customization needs will also have an impact on the quotation. For example, if special surface treatment or metallization processes are required, this may result in additional costs.
Therefore, to get an accurate quote, it’s best to request quotes from multiple manufacturers. This allows you to compare prices, quality and delivery times from different suppliers and make informed decisions taking into account budget constraints. Choosing the right manufacturer not only ensures a reasonable price, but also ensures high-quality ceramic packaging substrates, thus providing reliable support for your project.
Frequently Asked Questions (FAQs)
Can Ceramic Package Substrates withstand high temperatures?
Yes, Ceramic Package Substrates are known for their excellent thermal stability and can withstand high temperatures encountered in various applications, making them suitable for use in harsh environments and demanding conditions.
What are the differences between Alumina and Aluminum Nitride Ceramic Substrates?
Alumina Ceramic Substrates typically offer high thermal conductivity and electrical insulation, making them suitable for applications requiring efficient heat dissipation and electrical isolation. On the other hand, Aluminum Nitride Ceramic Substrates provide superior thermal conductivity combined with excellent dielectric properties, making them ideal for high-power and high-frequency applications.
Are Ceramic Package Substrates suitable for high-frequency applications?
Yes, Ceramic Package Substrates, especially those made from materials like Aluminum Nitride and Silicon Carbide, exhibit low dielectric losses and high-frequency capabilities, making them well-suited for RF, microwave, and other high-frequency applications in telecommunications, radar systems, and more.
How do Ceramic Package Substrates compare to traditional PCBs in terms of reliability?
Ceramic Package Substrates offer higher reliability compared to traditional PCBs due to their superior thermal management, mechanical strength, and resistance to environmental factors such as moisture, humidity, and corrosion. This enhanced reliability makes Ceramic Package Substrates preferable for critical applications where failure is not an option.
Can Ceramic Package Substrates be customized for specific project requirements?
Yes, Ceramic Package Substrates can be customized to meet specific project requirements in terms of dimensions, material composition, surface finish, and electrical characteristics. Many manufacturers offer customization services to tailor Ceramic Package Substrates according to the unique needs of each project.
Are there any environmental considerations when using Ceramic Package Substrates?
Ceramic Package Substrates are generally considered environmentally friendly due to their inert nature and recyclability. However, certain manufacturing processes and materials used in Ceramic Package Substrate production may have environmental impacts. It’s essential to choose reputable manufacturers who prioritize sustainable practices and materials.