Cavity Substrate Vender. Open a cavity or Open multi-Cavity or Open multi-step cavity on the Substrates. professional Cavity Substrate production team. we have made this Cavity Substrates with high quality and fast shipping time.
The Cavity Substrate PCB stands out as an innovative printed circuit board distinguished by its unique cavity structure on either the surface or within its layers. This distinctive design offers significant advantages in electronic component layout and plays a pivotal role in enhancing heat dissipation performance.
Diverging from traditional circuit boards, the Cavity Substrate PCB has garnered widespread attention. The incorporation of a cavity on the board’s surface or internally provides a more adaptable space for electronic component placement. In contrast to conventional planar circuit boards, the Cavity Substrate PCB effectively accommodates a diverse range of components, leading to heightened integration.
One of its standout features is the notable improvement in thermal performance. The cavity structure contributes to increased surface area, facilitating a more efficient heat dissipation rate. This becomes increasingly crucial in addressing the escalating heat generation in modern electronic devices. Through optimized heat dissipation, the Cavity Substrate PCB ensures the stable operation of electronic components within a confined space, effectively meeting the challenges posed by high-temperature environments.
Moreover, the Cavity Substrate PCB design streamlines the interconnection between electronic components. The cavity structure not only offers additional connection channels but also reduces the resistance and inductance of these interconnections, thereby enhancing circuit performance. This heightened interconnectivity positions Cavity Substrate PCBs as particularly adept in applications requiring high frequency and high speed.
Overall, Cavity Substrate PCB is not just a printed circuit board but an innovative technology leading the field of electronic engineering. Its unique design provides flexible solutions for the layout and heat dissipation of electronic components, allowing modern electronic devices to achieve greater performance in smaller spaces.
What types of Cavity Substrate PCB are there?
In the field of electronic engineering, Cavity Substrate PCB has attracted widespread attention for its diverse design and application flexibility. This type of printed circuit board mainly includes ball grid array (BGA), chip size package (CSP), etc. Each type shows unique advantages in specific application scenarios.
Ball Grid Array (BGA)
A ball grid array is a Cavity Substrate PCB that features a bottom layer covered with tiny solder balls. This design performs well in high-density integrated circuits, providing a more compact layout for electronic components.
BGA (Ball Grid Array) offers high density and performance by accommodating a large number of solder balls, enabling an efficient layout of components that enhances circuit board performance. Its design facilitates effective heat dissipation, leading to lower operating temperatures for electronic components. This, in turn, improves equipment stability and lifespan. The even distribution of solder balls enhances connection reliability, minimizing thermal stress on the circuit board resulting from temperature fluctuations.
Chip Scale Package (CSP)
Chip size packaging is another type of Cavity Substrate PCB whose design pays more attention to compact size and lightweight. CSP is widely used in thin and light electronic devices. Its advantages are as follows:
Compact Design: The CSP’s design is more streamlined, enabling the creation of smaller and lighter electronic devices. This makes it ideal for the development of portable products.
Reduced Weight: Thanks to its compact size, CSP significantly decreases the overall weight of electronic devices, enhancing their portability and mobility.
Short distance connection: The connection distance between components in CSP design is shorter, which helps to improve signal transmission speed and stability.
Different types of Cavity Substrate PCB have their own advantages and applicability in application scenarios. BGA is commonly used in high-performance computers, servers and communication equipment, while CSP is more suitable for smartphones, tablets and other thin and light portable devices. Choosing the appropriate type depends on specific design needs and equipment usage.
In electronic engineering, understanding and making full use of the different types of Cavity Substrate PCB can help designers better meet project needs and promote the innovation and development of electronic products.
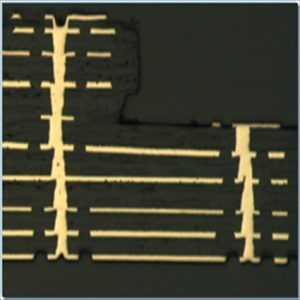
Cavity Substrate Vender
What are the advantages of Cavity Substrate PCB?
Cavity Substrate PCB, an innovative type of circuit board, presents a range of compelling advantages over traditional printed circuit boards (PCBs). This article will delve into the specific benefits of Cavity Substrate PCB and explore how these features render it an ideal choice for the design of contemporary electronic devices.
Smaller size
One of the first advantages of Cavity Substrate PCB is its smaller size. Cavity Substrate PCB effectively reduces the overall volume by forming a cavity structure on its surface or inner layer. This is crucial for modern electronic devices, especially in scenarios such as mobile devices and embedded systems, which are extremely sensitive to space.
Higher cooling performance
The cavity structure helps optimize thermal channels and efficiently conduct heat to the external environment. This makes Cavity Substrate PCB perform even better in the design of high-performance, high-power consumption equipment.
Better electromagnetic compatibility
PCBs with a cavity substrate offer a notable advantage in improving electromagnetic compatibility, making them a favored option in modern electronic device design. The built-in cavity structure efficiently reduces the adverse impacts of electromagnetic interference (EMI) and radio frequency interference (RFI), consequently enhancing signal integrity and fortifying device stability. These characteristics are essential for guaranteeing the reliability and resilience to interference of electronic equipment.
The compact dimensions of Cavity Substrate PCBs align seamlessly with the prevailing trend toward smaller form factors in electronic devices. This size advantage empowers designers with increased flexibility in layout and assembly, facilitating more streamlined and compact product designs. Simultaneously, in the realm of high-performance equipment, the PCB’s superior heat dissipation capabilities contribute significantly to stable device operation, mitigating the risk of electronic component damage stemming from overheating.
Moreover, the improved electromagnetic compatibility of Cavity Substrate PCBs results in heightened reliability and enhanced anti-interference capabilities for electronic devices. Given the increasing prevalence of wireless communications, mitigating the effects of electromagnetic interference on signals becomes crucial. This minimized interference guarantees superior communication quality, delivering users a more stable and dependable overall experience.
In summary, Cavity Substrate PCB, with its distinctive design structure and exceptional performance characteristics, emerges as an ideal solution to meet the design requirements of modern electronic equipment. When selecting circuit board types, designers can consider the size advantages, heat dissipation performance, and electromagnetic compatibility offered by Cavity Substrate PCB, ultimately leading to enhanced product performance and user experience.
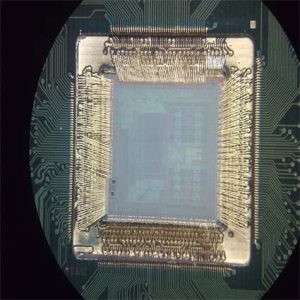
Cavity Substrate Vender
Why choose Cavity Substrate PCB?
In today’s electronic engineering field, why are designers increasingly inclined to choose Cavity Substrate PCB among the many circuit board options? This involves not only its unique performance, but also its superior performance in specific application scenarios.
First of all, the uniqueness of Cavity Substrate PCB is mainly reflected in its design structure and performance advantages. Compared with traditional printed circuit boards, Cavity Substrate PCB forms a cavity structure on its surface or inner layer. This structure provides greater flexibility for the layout of electronic components.
Mobile devices often have extremely high requirements on the size and weight of onboard electronic components, and Cavity Substrate PCB meets these requirements. Its compact design makes mobile devices thinner, lighter and more portable without sacrificing performance.
In fields such as drones, Cavity Substrate PCBs exhibit outstanding performance. Given the frequent necessity for drones to integrate diverse electronic components within confined spaces, the design structure of Cavity Substrate PCBs facilitates a more condensed layout of components, thereby enhancing the overall system’s performance. Furthermore, the exceptional heat dissipation capabilities contribute to ensuring the drone’s stable operation in high-intensity working environments, ultimately extending the equipment’s service life.
Designers opt for Cavity Substrate PCBs primarily due to their superior electromagnetic compatibility. In contemporary electronic devices, the electromagnetic interaction among various components has become an unavoidable challenge. The design of Cavity Substrate PCBs effectively isolates electromagnetic interference, thereby improving the stability and reliability of the entire system.
Especially in areas such as mobile devices and drones that place stringent requirements on the performance and size of electronic products, Cavity Substrate PCB has shown unparalleled advantages, providing designers with more possibilities and promoting the field of electronic engineering. of continuous innovation.
What is the manufacturing process of Cavity Substrate PCB?
The production of Cavity Substrate PCB (cavity substrate printed circuit board) is a intricate and precise undertaking, encompassing various manufacturing stages for both the main board and base plate. Employing advanced processes and technologies, manufacturers guarantee the accurate creation of cavity structures, meeting stringent customer demands for performance and reliability.
Motherboard and backplane manufacturing
The process of manufacturing a Cavity Substrate PCB begins with the fabrication of the motherboard and backplane. The design of these two requires careful consideration to ensure that they fit perfectly to create the desired cavity structure. The motherboard carries the electronic components and connecting wiring, while the backplane is usually the supporting structure of the entire circuit board.
Application of precision technology
The key to manufacturing Cavity Substrate PCBs is the use of precision processes. Advanced manufacturing equipment and technology ensure a precise cavity is formed between the motherboard and base plate, which requires operations at the micron level. Precision cutting, drilling and stacking processes are key steps in achieving this goal.
The precise formation of the cavity structure is achieved through the utilization of advanced tools and equipment in the manufacturing process. High-tech tools like laser cutting and CNC machines are employed to meticulously implement the designed cavity structure onto the circuit board. This ensures an exact fit with the layout and proper connection of electronic components.
To meet the stringent performance and reliability requirements set by customers, manufacturers maintain a rigorous focus throughout the manufacturing process. Stringent quality control measures and testing are implemented at every stage to guarantee the structural stability of the circuit board. The goal is to ensure reliable electrical performance and the ability to operate effectively in diverse environmental conditions.
Through these advanced manufacturing technologies and processes, Cavity Substrate PCB is able to achieve complex cavity structures, providing higher performance and reliability for electronic devices. This deep precision in manufacturing processes is one of the key innovations in modern electronic engineering, providing more flexible and efficient solutions for a variety of application areas.
In what application areas is Cavity Substrate PCB widely used?
Cavity Substrate PCB, an innovative solution in electronic engineering, has gained widespread application in modern electronic devices. Its design advantages position it as the preferred circuit board type for smartphones, computers, communication equipment, and various other fields.
In terms of smartphone applications, the small size and high degree of integration of Cavity Substrate PCB provide more design freedom for the device. With the trend of smart phones pursuing thinner and lighter weight, the compact design of Cavity Substrate PCB makes the internal components of the phone more compact and neat, providing more space for larger-capacity batteries and advanced functional modules. This further drives smartphone performance and design innovation.
In the realm of computing, particularly in high-performance equipment like lightweight laptops and supercomputers, the efficient heat dissipation features of Cavity Substrate PCBs have emerged as a decisive factor. The cavity structure not only facilitates an effective heat dissipation pathway but also diminishes overall temperatures, thereby aiding in sustaining device stability and performance. Moreover, the compact design of Cavity Substrate PCBs contributes to an enhanced overall energy efficiency ratio for computers, enabling the accommodation of more computing resources within a given volume.
In the field of communication equipment, the widespread adoption of Cavity Substrate PCBs has further propelled the advancement of communication technology. Their attributes of miniaturization and high integration empower communication equipment to reduce size and weight while upholding optimal performance. This proves especially crucial for devices with spatial constraints, such as wireless communication equipment and base stations, enabling them to better adapt to diverse environments.
The Cavity Substrate PCB has experienced significant success in the realm of electronic devices, owing to its design advantages. Its extensive application has not only spurred innovation in electronic products but has also played a pivotal role in advancing technology and enhancing equipment performance across various industries. Looking ahead, as technology continues to evolve, it is anticipated that the Cavity Substrate PCB will further leverage its distinctive advantages across diverse fields, opening up new possibilities in the realm of electronic engineering.
How to find Cavity Substrate PCB?
In the realm of modern electronic engineering, the selection of an appropriate manufacturer or supplier for Cavity Substrate PCBs is pivotal for project success. Designers must meticulously assess several key factors to ensure that the chosen Cavity Substrate PCB aligns with the project requirements.
Designers must thoroughly investigate potential manufacturers or suppliers, examining their track record, customer feedback, and compliance with international quality standards. Manufacturers with excellent reputations are more likely to deliver reliable products.
Assessing a manufacturer’s technical capabilities and equipment proficiency is crucial for ensuring high product quality, especially for intricate Cavity Substrate PCBs.
Customization is often vital in project designs, so designers should inquire about a manufacturer’s ability to provide custom solutions and adapt to specific design requirements.
The effectiveness of a manufacturer’s quality control and testing processes directly impacts product reliability. It’s essential to confirm adherence to advanced quality control standards and thorough testing to minimize defects.
Considering project timelines is critical. Designers should request production lead time estimates and explore the possibility of expedited delivery. Understanding the manufacturer’s after-sales service support system is also essential for timely and adequate support throughout the project.
Considering the aforementioned factors is paramount in the selection of a Cavity Substrate PCB manufacturer or supplier. Collaboration with an experienced and reputable manufacturer enables designers to secure a high-quality, dependable Cavity Substrate PCB tailored to their project’s specific needs. Through comprehensive investigation and collaboration, designers can establish enduring, stable relationships, laying a robust foundation for future projects.
It is crucial to consider the above factors when choosing a Cavity Substrate PCB manufacturer or supplier. By working with an experienced, reputable manufacturer, designers can ensure they receive a high-quality, reliable Cavity Substrate PCB that meets the specific needs of their project. Through in-depth investigation and collaboration, designers can establish long-term, stable relationships and lay a solid foundation for future projects.
What is the quote for Cavity Substrate PCB?
When selecting a Cavity Substrate PCB, designers must take into account various factors, and obtaining an accurate quote stands out as a crucial step for ensuring the project’s seamless progression. This article will explore the intricacies involved in securing a quote for Cavity Substrate PCB, encompassing considerations such as the manufacturing process, material costs, and more. Additionally, it will underscore the significance of effective communication with the manufacturer throughout the process.
Advanced manufacturing processes usually include precise cavity structure formation, highly integrated component layout, etc., which will affect production costs. The level of workmanship used by different manufacturers may differ, so designers need to understand the level of workmanship and technical strength of the manufacturer when obtaining a quote.
Material cost is another important factor that affects the Cavity Substrate PCB quote. High-performance substrate materials, advanced packaging materials, etc. will increase manufacturing costs. Designers need to fully communicate with manufacturers to ensure that the materials selected meet the project requirements and understand their impact on the overall cost.
The degree of customization of Cavity Substrate PCB will directly affect the quotation. If the project has special requirements for cavity structure and component layout, the manufacturer will need to perform additional customization processes. Designers should clearly communicate project requirements and understand the specific impact of custom craftsmanship on the quote so that informed decisions can be made.
Production quantity is another key factor that affects Cavity Substrate PCB quotes. Typically, mass production reduces the manufacturing cost of a single product. Designers need to discuss expected production quantities with manufacturers early in the project to obtain a more precise quote and find the balance between quantity and cost.
Full communication with the manufacturer is integral to ensuring an accurate quote. The designer needs to introduce the project requirements in detail, including technical specifications, customization requirements, production quantities, etc., to ensure that the manufacturer can provide an accurate quotation that meets the project needs. Timely communication can also help resolve potential issues and ensure projects are completed on time and with quality.
When choosing Cavity Substrate PCB, a full understanding of the quote formation process is fundamental to ensuring a successful project. Designers need to comprehensively consider factors such as manufacturing processes, material costs, customization needs, and production quantities, and work closely with manufacturers to obtain quotes that best suit project needs. Through informed decision-making and effective communication, designers can ensure that projects proceed smoothly and economically, efficiently.
What are the frequently asked questions about Cavity Substrate PCB?
Cavity Substrate PCBs, with their innovative design and versatile applications, often raise questions among designers and engineers. Let’s delve into some common queries surrounding Cavity Substrate PCBs:
What distinguishes Cavity Substrate PCBs from traditional PCBs?
Cavity Substrate PCBs feature cavities on their surface or inner layers, impacting electronic component layout and heat dissipation. Understanding this distinction is crucial for designers exploring advanced circuit board options.
In what scenarios is choosing Cavity Substrate PCBs particularly beneficial?
Designers must discern the specific scenarios where the performance characteristics of Cavity Substrate PCBs shine. Identifying these scenarios ensures optimal utilization in applications like mobile devices and unmanned aerial vehicles.
What is the manufacturing process involved in creating Cavity Substrate PCBs?
Delving into the manufacturing process, which encompasses the fabrication of both main and bottom boards, sheds light on the precision techniques and technologies employed. This knowledge ensures an understanding of how manufacturers achieve precise cavity structures.
What factors influence the quoting process for Cavity Substrate PCBs?
Obtaining quotes for Cavity Substrate PCBs entails consideration of factors such as manufacturing processes and material costs. Communicating with manufacturers and understanding these cost-related aspects is vital for project planning.
What are the typical challenges or concerns associated with Cavity Substrate PCBs?
Exploring common issues or challenges encountered with Cavity Substrate PCBs provides designers with insights into potential pitfalls and solutions. Addressing these concerns enhances the overall reliability and success of projects utilizing this advanced circuit board technology.
In conclusion, gaining a comprehensive understanding of Cavity Substrate PCBs involves addressing these fundamental questions. This knowledge empowers designers to make informed decisions, ensuring the effective integration of Cavity Substrate PCBs in cutting-edge electronic designs.