Cavity PCB| High Speed Cavity PCB Manufacturer.Cavity PCBs, crafted with precision, epitomize cutting-edge technology in electronics. As a leading Cavity PCB| High Speed Cavity PCB Manufacturer, we specialize in designing and fabricating PCBs tailored for high-frequency applications. Our adept team ensures meticulous attention to detail, guaranteeing superior performance and reliability. With advanced manufacturing processes and state-of-the-art equipment, we deliver PCBs optimized for speed and efficiency. Whether for telecommunications, aerospace, or medical devices, our Cavity PCBs meet the demands of modern technology, facilitating seamless data transmission and signal integrity. Trust us for innovative solutions driving the forefront of electronic advancement.
In today’s digital era, the role of Cavity PCB manufacturers is crucial. They not only provide high-performance, high-reliability PCB solutions, but also play a key role in promoting innovation and development of electronic equipment. Through professional technology and precise manufacturing processes, Cavity PCB manufacturers are able to meet customer needs and maintain a competitive advantage in the ever-changing market. Their existence provides a solid foundation for the development of the electronics industry.
What is a Cavity PCB?
When talking about Cavity PCB, we inevitably involve a unique printed circuit board design that plays a key role in the field of electronic manufacturing. So, what is Cavity PCB?
Cavity PCB, literally translated as “groove PCB”, is indeed a printed circuit board with grooves or cavities. These grooves or cavities can be formed by cutting or machining the inside of the circuit board, providing an ideal space for housing electronic components or other components within them. This design allows electronic components to be embedded inside the PCB, enabling a more compact and highly integrated circuit design.
The design flexibility of Cavity PCBs makes them useful in a variety of applications. For example, in wireless communication equipment, Cavity PCB can accommodate antennas or radio frequency modules to achieve better signal transmission and reception performance. In medical devices, Cavity PCBs can house sensors or micro-components for more precise data collection and processing. In the aerospace field, Cavity PCB can accommodate inertial navigation devices or communication modules to maximize space utilization.
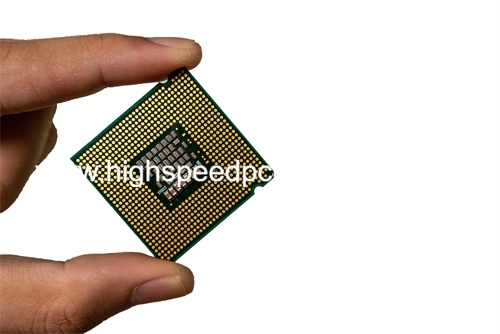
Cavity PCB| High Speed Cavity PCB Manufacturer
In addition to its applications in electronic devices, Cavity PCB also plays an important role in fields such as microelectronics and MEMS (microelectromechanical systems). By creating tiny cavities or channels inside the PCB, Cavity PCB enables more complex circuit layouts and higher levels of integration, thereby promoting the development of microelectronics technology.
Overall, the design of Cavity PCB expands the functionality of printed circuit boards to a new dimension, providing electronic engineers with more design options and room for innovation. By cleverly utilizing internal space, Cavity PCB not only achieves a high degree of circuit integration, but also improves the performance and reliability of electronic equipment, promoting the development of the entire electronics manufacturing industry.
How to Design a Cavity PCB?
Designing Cavity PCB is a complex and critical task that requires experienced engineers and advanced software tools to achieve optimal results. The design process not only involves the determination of cavity location, but also requires a comprehensive consideration of multiple factors such as circuit requirements, material selection, and manufacturing feasibility to ensure that the final circuit board has excellent performance and reliability.
First, it is crucial to determine the location of the cavity in the Cavity PCB. This requires consideration of the layout of individual components in the circuit and the impact of cavities on circuit performance. For example, placing sensitive components inside the cavity can effectively isolate them, reduce external interference, and improve the stability of the circuit.
Second, the design process needs to optimize circuit layout to ensure that cavities do not adversely affect circuit routing. Engineers need to use advanced layout tools to adjust component locations and connection lines to minimize signal interference and electromagnetic coupling effects. In addition, the shape and size of the cavity need to be considered to ensure the smoothness and stability of the circuit routing.
During the design process, engineers also need to consider material selection and manufacturing feasibility. Selecting the appropriate substrate material is critical to Cavity PCB performance. For example, materials with lower dielectric constants and losses can improve the signal transmission speed and stability of circuits. In addition, engineers need to consider the machining and manufacturing process of the cavity to ensure the quality and reliability of the final product.
In short, designing Cavity PCB requires engineers to have rich experience and deep professional knowledge, as well as advanced software tools to assist design and optimization. Comprehensive consideration of factors such as cavity location, circuit layout, material selection and manufacturing feasibility can ensure that the final circuit board meets customer needs and has excellent performance and reliability.
What is the Cavity PCB Fabrication Process?
Cavity PCB manufacturing process is a complex and precise process that requires an experienced technical team and advanced manufacturing equipment. The key steps and precautions for Cavity PCB manufacturing will be introduced in detail below:
First, manufacturers must choose high-quality raw materials suitable for Cavity PCB. Typically, these raw materials include high-performance substrate materials, such as FR4 or Rogers materials, as well as conductive materials and cover layers. The correct selection of raw materials is an important factor in ensuring the performance and reliability of the final product.
Once the appropriate raw material has been selected, the next step is to cavity process the PCB board. This involves using advanced processing equipment to cut grooves or cavities in the PCB board according to the design requirements. The shape and size of the cavity must be accurate to the micron level to ensure the smooth progress of the subsequent assembly process.
After the cavity processing is completed, the PCB board usually enters the lamination and molding stage. This step involves stacking different layers of materials, such as conductive layers, insulating layers and covering layers, and holding them together through a process of high temperature and pressure. This ensures the stability and durability of the PCB board.
Quality control is crucial throughout the entire manufacturing process. Manufacturers must ensure that strict quality standards are met at every step and carry out the necessary inspections and tests to ensure the performance and reliability of the final product. High-precision processing equipment and advanced detection technology are widely used in these processes to ensure product quality.
Cavity PCB manufacturing is a comprehensive process involving multiple critical steps and precision operations. Only an experienced manufacturing team and advanced equipment can ensure that the quality and performance of the final product reaches the expected level. Through the correct selection of raw materials, precision processing and strict quality control, manufacturers can provide high-quality Cavity PCB products that meet customer needs and expectations.
How to Manufacturer a Cavity PCB?
Manufacturing a cavity PCB requires the following steps:
Design: First, the cavity PCB needs to be designed. This includes determining PCB dimensions, hierarchy, cavity shape and size, etc. Design software such as Altium Designer, Cadence Allegro, etc. can be used to create PCB designs.
Material preparation: Select materials suitable for cavity PCB manufacturing. Typically, fiberglass reinforced epoxy is the commonly used substrate material. In addition, copper foil is also needed to make the conductive layer of the PCB.
Making internal cavities: Using mechanical processing or chemical processing to form a cavity structure inside the PCB. This may involve drilling, milling or using a special lamination process to create the cavity.
PCB manufacturing: Transfer the designed PCB pattern to the substrate, and use photolithography, etching and other processes to form a conductive layer on the surface of the substrate. This process may also include the stacking and lamination of multi-layer PCBs.
Surface treatment: Surface treatment of the manufactured PCB, including removal of residual chemicals, cleaning and surface coating, etc., to ensure the quality and stability of the PCB.
Inspection and testing: Inspection and testing of the manufactured cavity PCB to ensure that it meets the design requirements and performance indicators.
Packaging and delivery: Finally, the manufactured cavity PCB is packaged and delivered to the customer as per their requirements.
The above are the general steps for manufacturing cavity PCB. The specific manufacturing process may vary due to different design requirements, material selection and manufacturing process.
How Much Does a Cavity PCB Cost?
PCB prices will vary based on a variety of factors. How expensive it is depends on the following aspects:
Board type: PCB can use different types of substrate materials, such as FR-4 (commonly used fiberglass composite materials), metal substrates (such as aluminum substrates or copper substrates), etc. The cost of different materials varies greatly.
Number of layers: The number of layers of a PCB determines its complexity. Different types of PCBs such as single-sided boards, double-sided boards, and multi-layer boards will have different costs.
Process requirements: If the PCB requires special processes, such as high-precision printing, special surface treatment (such as spray plating, chemical gold plating, etc.), the cost will increase accordingly.
Number and size of holes: The number and size of holes on the PCB will affect the difficulty and cost of processing. More holes and smaller sizes usually mean higher costs.
Order quantity: Larger quantity orders tend to get better price deals, while smaller quantity orders may cost more.
Overall, for a common Cavity PCB, the price usually ranges from a few dollars to dozens of dollars, depending on the above factors and the supplier’s pricing strategy.
What materials are Cavity PCB made of?
The material of Cavity PCB is a key factor in determining its performance and suitability. Typically, Cavity PCB uses high-performance substrate materials, such as FR4 or Rogers materials. These materials have excellent thermal conductivity and mechanical properties, making them excellent in a variety of application scenarios.
First, let’s understand the FR4 material. FR4 is a fiberglass-reinforced epoxy resin that is widely used in PCB manufacturing. It has excellent electrical properties and mechanical strength and can withstand working conditions in high temperature and high humidity environments. The FR4 material has good thermal conductivity and helps dissipate heat, thereby improving the stability and reliability of the PCB. Due to its relatively low cost, FR4 materials are well suited for most applications, especially consumer electronics and industrial control equipment.
Another commonly used Cavity PCB material is Rogers material. Rogers material is a high-performance polymer composite with excellent dielectric and thermal conductivity properties. Compared with FR4, Rogers material has a lower dielectric constant and more stable signal transmission, making it suitable for high-frequency applications such as communication equipment and radar systems. In addition, Rogers materials also have good high temperature resistance and chemical stability, and can meet the requirements of harsh working environments.
Whether using FR4 or Rogers materials, Cavity PCB can play an important role in various application scenarios. Their superior performance and reliability make Cavity PCBs the solution of choice for many electronic devices. At the same time, with the continuous advancement of technology, people’s requirements for Cavity PCB materials are also constantly increasing. In the future, we can look forward to the application of more new materials, bringing new opportunities and challenges to the development of Cavity PCB.
Who manufactures Cavity PCB?
In today’s high-tech electronics industry, Cavity PCB manufacturers play a vital role. So, who makes Cavity PCB? The answer is: the manufacturer is right here, in our company.
As a professional Cavity PCB manufacturer, we are committed to providing customers with high-quality, high-performance printed circuit board solutions. We have advanced production equipment and technology, and are equipped with an experienced engineering team to meet various customer needs.
In our manufacturing facility, we strictly implement the ISO quality management system to ensure that every Cavity PCB meets the highest quality standards. We use advanced processes and materials to ensure products have excellent performance and reliability.
Our client base includes businesses and organizations from all walks of life, from small startups to multinational giants. Whether it is a simple electronic device or a complex high-end product, we are able to provide customers with customized solutions and provide comprehensive support at every stage of product design, manufacturing and delivery.
We not only focus on product quality, but also on customer experience. We have won the trust and praise of our customers with our professional, timely and personalized services. No matter what problem our customers have, we will do our best to help them and ensure the highest level of customer satisfaction.
Therefore, if you are looking for a reliable Cavity PCB manufacturer, you may wish to consider our company. We will wholeheartedly provide you with high-quality products and services to achieve success and development together.
What are 5 qualities of a good customer service?
Quality Cavity PCB manufacturers’ focus on customer service is not only reflected in the quality of their products, but also in the quality of service they provide. Here are five key attributes that ensure customers have the best experience throughout their relationship:
Professionalism: Professionalism is the cornerstone of a quality Cavity PCB manufacturer. They have an experienced team of engineers and technical experts who are able to understand customers’ needs and provide professional advice. From initial consultation to final product delivery, they always support their clients with professionalism and knowledge.
Prompt response: Prompt response is an important factor in building good customer relationships. Quality manufacturers focus on timely communication and promptly respond to customers’ emails, phone calls, or online inquiries. They respect their clients’ time and work hard to ensure that clients receive prompt help and support at any stage.
Personalized care: Establish a close cooperative relationship with customers, gain an in-depth understanding of their projects and goals, and provide customized solutions based on their specific requirements.
Problem-solving skills: Problems are inevitable during the PCB manufacturing process. However, quality manufacturers have excellent problem-solving skills and are able to quickly identify and resolve problems as they arise. Whether it is technical difficulties or supply chain issues, they can effectively deal with them to ensure the smooth progress of the project.
Continuous Improvement: Quality manufacturers are always improving their products and services. They actively collect customer feedback and use it to improve their manufacturing processes and service quality. Through continuous improvement, they are able to continuously improve customer satisfaction and establish long-term and stable cooperative relationships with customers.
The above attributes together form the cornerstone of customer service from quality Cavity PCB manufacturers. Through professional and timely response, personalized care, problem-solving capabilities and continuous improvement, they are able to ensure that customers receive the best experience throughout the entire cooperation process, thereby achieving a win-win situation for both parties.
FAQS
How is the cost of Cavity PCB manufacturing determined?
The cost of Cavity PCB is affected by many factors, the most important of which include material selection, design complexity and production scale. The use of high-performance materials and complex designs increases costs, while mass production may lower unit costs. Therefore, customers should consider these factors comprehensively when considering Cavity PCB manufacturing costs and have in-depth discussions with the manufacturer to obtain an accurate quotation.
How to choose the right Cavity PCB manufacturer?
There are several factors to consider when choosing the right Cavity PCB manufacturer. First, customers should evaluate the manufacturer’s experience and technical capabilities, including its expertise and track record in Cavity PCB manufacturing. Secondly, customers should also consider the manufacturer’s production capabilities and quality control levels to ensure that project needs can be met and reliable products can be provided. In addition, the level of customer service is also an important consideration in selecting a manufacturer, including responsiveness, communication skills and problem-solving abilities.
How is Cavity PCB different from regular PCB?
The main difference between Cavity PCB and regular PCB is its design with grooves or cavities. These grooves or cavities can be used to house electronic components or other components, thereby improving the performance and stability of the circuit. In contrast, conventional PCBs are typically flat designs with no grooves or cavities.
What application fields is Cavity PCB suitable for?
Cavity PCB is suitable for many application fields, especially scenarios with high circuit performance and space requirements. For example, fields such as communication equipment, medical equipment, aerospace devices, and high-end consumer electronics often use Cavity PCB to achieve higher integration and performance optimization.
How long is the design and manufacturing cycle of Cavity PCB?
The design and manufacturing cycle of Cavity PCB depends on the complexity of the project and the manufacturer’s production capabilities. Generally speaking, it can take weeks or even months from design to delivery of the finished product. Customers should negotiate with the manufacturer and establish a clear project timeline to ensure the project is completed on time.