Cavity PCB | High Frequency PCB Manufacturing.”Cavity PCBs are meticulously crafted, embodying precision and efficiency in high-frequency PCB manufacturing. These specialized boards feature cavities, meticulously engineered to house sensitive components, ensuring optimal signal integrity and reduced electromagnetic interference. High-frequency PCB manufacturing employs advanced techniques, meticulously controlling impedance and minimizing signal loss, crucial for applications demanding exceptional performance. Engineers meticulously design these boards to meet stringent specifications, guaranteeing reliability in aerospace, telecommunications, and medical equipment. With meticulous attention to detail, cavity PCBs epitomize cutting-edge technology, driving innovation in diverse industries.”
Cavity PCB, or cavity printed circuit board, is a specially designed PCB with a cavity structure on its surface or inside. This design allows the circuit board to accommodate more components or provide a more complex layout while maintaining its original functionality. Cavity PCB plays an important role in electronic equipment, providing higher integration, better signal transmission and more stable electrical performance. By installing components in the cavity, Cavity PCB can effectively reduce the size of the circuit board and improve the performance density of the device. Therefore, it is widely used in fields with high performance requirements such as communication equipment, wireless networks, and radar systems.
How to design Cavity PCB?
When designing a Cavity PCB, there are a number of key principles and steps to consider to ensure its performance and reliability. Here are a few key aspects to note when designing Cavity PCB:
When designing a Cavity PCB, you must first determine the location and size of the cavity. This needs to take into account the layout and connection requirements of the electronic components, as well as the impact of the cavity on the overall structure and performance of the PCB. Ensure that the cavity is properly located and sized to meet the requirements of the circuit design and mechanical structure.
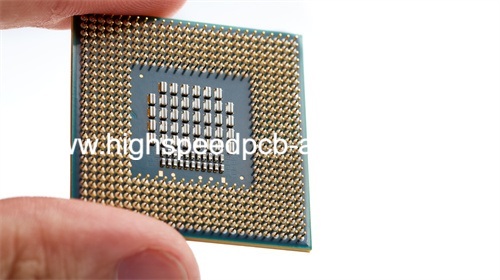
Cavity PCB | High Frequency PCB Manufacturing
Choosing the right material is crucial for designing Cavity PCB. Different application scenarios may require different types of substrate materials, such as FR-4, high-frequency materials or special substrate materials. The selection of materials should take into account factors such as their dielectric constant, thermal stability, mechanical strength, etc. to ensure the performance and stability of the PCB.
When designing Cavity PCB, electromagnetic compatibility (EMC) issues need to be considered to prevent electromagnetic interference from affecting the circuit. This includes reasonable circuit layout, grounding planning, signal line shielding and isolation and other measures to reduce the impact of interference and noise on the circuit.
The boundary treatment of the cavity is crucial to the design of Cavity PCB. Reasonable boundary processing can reduce boundary effects and signal leakage, and improve PCB performance and reliability. This includes using appropriate shielding and isolation measures, as well as optimizing cavity structure and closure.
When designing Cavity PCB, its mechanical strength and stability need to be considered to ensure that the PCB can function properly under various environmental conditions. This includes considering the reinforcement and support of the cavity structure, as well as selecting appropriate connection methods and fixtures to prevent damage or deformation of the PCB during transportation and use.
Finally, after designing the Cavity PCB, necessary testing and verification work needs to be performed to ensure that the performance and reliability of the PCB meet the design requirements. This includes electrical performance testing, mechanical strength testing and environmental adaptability testing to identify potential problems and make timely corrections.
In short, designing Cavity PCB requires comprehensive consideration of factors such as circuit design, material selection, electromagnetic compatibility, boundary treatment, mechanical strength, and test verification to ensure that the performance and reliability of the PCB meet expected requirements.
What is the manufacturing process of Cavity PCB?
The manufacturing process of Cavity PCB (cavity PCB) is a complex and precise process, involving multiple key steps and the use of professional processes. Below we will introduce in detail the main processes and related processes of Cavity PCB manufacturing.
First, the manufacturing process of Cavity PCB usually includes the following key steps:
Design and Planning: Detailed design and planning is required before manufacturing Cavity PCB. This includes determining the location, size, and shape of the cavity, as well as determining how other key components will be laid out and connected.
Material preparation: Selecting suitable substrate materials and cavity filling materials is the first step in manufacturing Cavity PCB. Commonly used substrate materials include FR-4 fiberglass composites, while cavity fill materials are selected based on specific application needs, such as air, resin or other insulating materials.
Processing and preparation: Next, the substrate will be processed and prepared according to the design requirements. This may involve steps such as cutting the substrate, drilling holes, surface preparation, and creating and filling cavities. The manufacturing of cavities is usually done through high-precision processes such as CNC machines or laser machining.
Printing the circuit layers: Once the substrate is ready, you can start printing the circuit layers. This involves using photolithography to print circuit patterns onto the substrate surface and chemical etching to remove unwanted copper foil.
Electroplating: After etching is completed, the substrate needs to be electroplated to enhance its electrical conductivity and corrosion resistance. This often includes treatments such as gold plating or tin plating to ensure the robustness and reliability of circuit connections.
Soldering and Assembly: Finally, the electronic components will be soldered to the substrate and undergo final assembly and testing. This may involve hand soldering or surface mount (SMT) soldering using automated equipment.
In the Cavity PCB manufacturing process, many specific processes are also involved, such as chemical etching, metallization, welding technology, etc. The precise application and strict control of these processes are key factors in ensuring the quality and performance of Cavity PCBs. Through careful design and precision processing, Cavity PCB can achieve higher performance, reliability and functionality, and is widely used in wireless communications, medical equipment, aerospace and other fields.
What is the manufacturing process of Cavity PCB?
When manufacturing Cavity PCB, it needs to go through a series of precise steps and special processing techniques to ensure the quality and performance of the final product. The following are the key steps and considerations for the Cavity PCB manufacturing process:
The manufacturing of Cavity PCB requires special materials and precise machining processes. First of all, it is very critical to choose the appropriate substrate material, usually materials with good insulation properties and mechanical strength, such as FR-4 or high-frequency materials. The substrate is then cut and processed according to the design requirements to ensure accuracy in size and shape.
Next, inner layer stacking takes place, where the copper foil and substrate layers are stacked together and bonded together using pressure and heat. During the inner layer stacking process, it is necessary to ensure that the position and thickness of each layer meet the design requirements.
After the inner layer stacking is completed, the outer layer is processed. This includes steps such as applying photosensitive adhesive, exposure, etching and surface treatment to form the circuit pattern of the PCB. In Cavity PCB manufacturing, special processing techniques such as deep hole drilling and precision film coating are usually required to meet the requirements of cavity design.
Designing and manufacturing the cavities in Cavity PCB is one of the key steps in the Cavity PCB manufacturing process. The design of the cavity needs to consider the overall structural and functional requirements of the circuit board, as well as the connection and isolation between the cavity and other components.
During the design phase, the location, shape, and size of the cavity need to be determined and how it will integrate with the rest of the board. CAD software is usually used for cavity design, and simulation and analysis are performed to ensure that the cavity design meets the requirements.
During the manufacturing stage, cavities are usually created by mechanical machining or chemical etching. During machining, a CNC machine or laser processing equipment is used to precisely cut the shape and size of the cavity. During chemical etching, a special etching solution is used to remove portions of the substrate material to create the shape of the cavity.
During the Cavity PCB manufacturing process, special processing techniques require special attention. For example, during the cavity manufacturing process, machining accuracy and surface quality need to be ensured to avoid affecting the functionality and reliability of the cavity.
In addition, attention needs to be paid to the connection and isolation of the cavity from other parts of the circuit board to ensure the stability and electrical performance of the cavity. During processing, appropriate processes and equipment need to be used to ensure that the size and shape of the cavity meet the design requirements.
In general, the manufacturing process of Cavity PCB requires highly precise processing technology and strict quality control to ensure that the quality and performance of the final product meet the expected goals.
Through appropriate material preparation and processing steps, as well as professional cavity design and special processing technology, Cavity PCBs can be manufactured with high quality and reliability to meet the needs of various applications.
How much does Cavity PCB cost?
The cost of Cavity PCB is determined by a variety of factors. Understanding these factors is important to evaluate and optimize the cost of Cavity PCB. The following will introduce several factors that mainly affect the cost of Cavity PCB:
Material cost: The material of Cavity PCB directly affects its cost. Special materials, high-frequency materials or materials with special properties often result in higher costs. In addition, as material costs fluctuate and supply and demand relationships change, the cost of Cavity PCB will also change accordingly.
Design complexity: The design complexity of Cavity PCB has a great impact on the cost. Complex designs require more engineer time and resources to complete, thus increasing manufacturing costs. In addition, whether special requirements or custom features are included in the design will also affect the cost.
Manufacturing process: The process and technology used in the manufacturing process of Cavity PCB will also affect the cost. For example, some special processing processes may require higher equipment costs or more complex operating procedures, thereby increasing manufacturing costs.
Volume and batch size: The quantity and batch size at which Cavity PCBs are produced also affects its cost. Typically, high-volume production reduces unit costs because it allows for greater efficiency and more effective resource utilization. In contrast, low-volume production typically results in higher unit costs.
Technical support and services: Some suppliers may provide additional technical support and services, such as design consulting, sample testing, etc. These additional services may increase the overall cost, but also improve the quality and reliability of the product.
To sum up, the cost of Cavity PCB is affected by many factors, including material cost, design complexity, manufacturing process, volume and batch size, as well as technical support and services. When evaluating and optimizing the cost of Cavity PCB, these factors need to be considered comprehensively and the most suitable option is selected to meet project needs and budget requirements.
What material is Cavity PCB made of?
The performance and reliability of Cavity PCB (cavity PCB) largely depends on the materials selected. When selecting Cavity PCB materials, many factors need to be considered, including electrical performance, mechanical strength, heat resistance, and cost. The following will introduce some commonly used Cavity PCB materials and factors to consider when selecting materials.
FR-4: FR-4 is one of the most commonly used substrates, consisting of fiberglass cloth and epoxy resin. It has good mechanical properties and high temperature resistance and is suitable for most general Cavity PCB applications.
PTFE (polytetrafluoroethylene): PTFE is an excellent high-frequency material with low dielectric loss and excellent insulation properties. It is often used in Cavity PCB applications that require higher frequencies and lower signal loss.
Aluminum substrate: The aluminum substrate is composed of an aluminum substrate and an insulating layer. It has excellent heat dissipation performance and mechanical strength and is suitable for Cavity PCB design of high-power electronic devices.
Ceramic substrate: Ceramic substrate has good high-temperature stability and insulation properties, and is suitable for Cavity PCB design in high-temperature environments and special applications.
Metal substrate: Commonly used materials for metal substrate include copper, aluminum and steel. They have good thermal conductivity and mechanical strength and are suitable for Cavity PCB design with some special requirements.
To sum up, choosing the right materials is crucial to the performance and reliability of Cavity PCB. During the design and manufacturing process, various factors need to be considered comprehensively and the most suitable materials selected to ensure that Cavity PCB can meet the expected performance and reliability requirements in various application scenarios.
Who makes Cavity PCB?
The manufacturing process of Cavity PCB requires highly professional technical and equipment support, so choosing the right manufacturer is crucial. In this field, there are many professional PCB manufacturers providing Cavity PCB manufacturing services, including our company.
Our company is a professional PCB manufacturer with many years of experience and is committed to providing high-quality Cavity PCB manufacturing services. We have advanced production equipment and technical teams to meet customers’ needs for various complex PCBs.
Our company has advanced production lines and precision processing equipment to achieve efficient manufacturing of Cavity PCBs. We have a highly skilled team with extensive experience and expertise capable of providing customers with customized solutions.
As a professional PCB manufacturer, our company strictly follows the ISO quality management system and has passed multiple international certifications, including ISO 9001 and ISO 14001. We adopt strict quality control measures to ensure that every batch of products meets customer requirements and standards.
The company focuses on communication and cooperation with customers and provides customers with a full range of technical support and services. Our professional team will provide personalized solutions according to customer needs and respond to customer needs and feedback in a timely manner.
The company continuously invests in R&D and innovation and is committed to improving product quality and production efficiency. We work with customers to jointly promote the development of Cavity PCB manufacturing technology and contribute to the development and application of electronic equipment.
As a professional manufacturer of Cavity PCB manufacturing, our company will continue to adhere to the purpose of “quality first, customer first”, provide customers with high-quality products and services, and jointly promote the development and progress of the electronics industry.
Five Characteristics of Great Customer Service
Cavity PCB manufacturing services companies need to have the following key characteristics when providing customer service to ensure customers receive a high-quality service experience:
When customers raise questions or needs, the company should be able to respond promptly and provide positive feedback and solutions. Timely communication can establish a good cooperative relationship and enhance customers’ trust in the company.
Cavity PCB manufacturing involves complex processes and technologies. The customer service team should have professional knowledge and experience and be able to provide customers with professional technical support and solutions to help customers solve various problems.
Different customers may have different needs and requirements. High-quality customer service should be able to provide personalized customized solutions to meet the specific needs of customers and improve customer satisfaction.
Good communication is key to keeping customer relationships strong. The customer service team should be able to communicate clearly and accurately with customers, listen to customer opinions and feedback, resolve issues promptly, and provide timely updates and progress to customers.
Excellent customer service doesn’t just stop after the transaction is completed, it should also provide ongoing after-sales support. The company should be able to provide customers with technical support, maintenance services and after-sales guarantees to ensure that problems encountered by customers during use can be solved in a timely manner.
Through the above methods, customers can ensure a high-quality customer service experience and improve the smoothness and satisfaction of cooperation.
FAQS
What are the cost implications of manufacturing Cavity PCBs?
The cost of manufacturing Cavity PCBs depends on various factors, including design complexity, material selection, production volume, and manufacturing processes. Optimizing design for manufacturability and selecting cost-effective materials can help mitigate manufacturing costs while ensuring desired performance and reliability.
What are the key considerations in designing a Cavity PCB?
Designing a Cavity PCB involves several crucial considerations. Engineers must carefully plan the layout to accommodate the cavity while ensuring signal integrity and thermal management. Additionally, they need to select suitable materials that offer the required mechanical strength and electrical properties.
How does the manufacturing process differ for Cavity PCBs compared to traditional PCBs?
The manufacturing process for Cavity PCBs involves additional steps to create the cavities. These steps include precision milling or routing to carve out the voids within the PCB substrate. Furthermore, specialized techniques such as controlled-depth drilling may be required for certain cavity designs
What are the typical applications of Cavity PCBs?
Cavity PCBs find applications in industries where space-saving, electromagnetic shielding, and thermal management are critical. Common applications include aerospace and defense systems, telecommunications equipment, medical devices, and high-performance computing.