BGA Substrate Manufacturing. From 2 layer to 20 layer IC/BGA substrates will be made with High speed and high frequency materials. Professional substrate production.
Ball Grid Array (BGA) Substrate is an innovative packaging technology in electronic device design that strategically organizes spherical solder joints on the base plate to create a grid-like structure. This distinctive design enhances the performance and reliability of contemporary electronic devices.
The core feature of BGA Substrate is its layout of spherical solder joints, which are distributed in a grid pattern on the base plate. This design not only greatly increases component density, but also improves connection reliability. The uniform distribution of spherical solder joints not only improves the efficiency of signal transmission, but more importantly, BGA Substrate shows superior stability compared to traditional packaging methods in the face of temperature changes and mechanical stress.
The definition of BGA Substrate is not just a physical structure, but also a technical concept that promotes the advancement of electronic engineering. Its design concept aims to solve the problems of space occupation and insufficient heat dissipation encountered in traditional circuit packaging. By soldering components to ball solder joints on the backplane, BGA Substrate successfully achieves a more compact design, providing an ideal solution for the simplicity and high performance of modern electronic devices.
The significance and prevalence of BGA (Ball Grid Array) Substrates in the electronics industry continue to escalate, demonstrating remarkable efficacy not only in sophisticated applications like computer motherboards and communication equipment but also in everyday consumer electronics such as smartphones and tablets. This packaging technique offers unparalleled flexibility to device designers, enabling the integration of more powerful functionalities within confined spaces.
In essence, the term BGA Substrate transcends mere technical jargon; it embodies an innovation with revolutionary implications in electronic engineering. Leveraging its distinctive structure and superior performance, BGA Substrates have become an indispensable element in the design of modern electronic devices, propelling ongoing technological advancements.
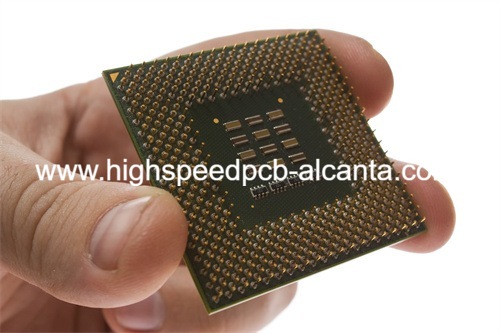
BGA Substrate Manufacturin
What are the types of BGA Substrate?
At the forefront of electronic device design, the Ball Grid Array (BGA) Substrate stands out for its diverse range of types, each demonstrating distinctive characteristics suited for various application scenarios. This article will provide a comprehensive exploration of different BGA Substrate variants, including micro BGA and ball-column BGA, elucidating their pivotal roles in specific devices.
Micro BGA: extremely miniaturized package
Micro BGA Substrate is a compactly designed packaging technology known for its extremely small size and high-density solder joint layout. This type of BGA Substrate is particularly suitable for devices with extremely high space requirements, such as portable smart devices and embedded systems. Its miniaturized design makes the circuit board more compact, providing an ideal solution for the design of modern lightweight electronic products.
Ball-column BGA: superior connectivity and heat dissipation performance
The ball-column BGA substrate incorporates a distinctive ball-column-shaped solder joint arrangement to enhance both connectivity and heat dissipation performance. This innovative design not only increases the contact area of the solder joints, improving connection reliability, but also enhances heat dissipation efficiency. This makes it particularly well-suited for applications in high-performance computing devices, graphics processing units (GPUs), and other equipment where stability and effective temperature management are crucial.
On the other hand, the micro BGA substrate finds widespread use in compact electronic devices such as smartphones, wearables, and headphones, owing to its miniature design. The key advantage lies in its contribution to achieving lighter and more portable product designs. In contrast to the ball-column BGA substrate, the micro BGA substrate is often preferred for scenarios that prioritize miniaturization without compromising performance, making it a popular choice for smaller consumer electronics.
Overall, the diverse types of BGA Substrate provide engineers with the opportunity to choose the most suitable packaging technology in different application scenarios. Through an in-depth understanding of types such as micro BGA and ball-column BGA, we can better understand their advantages in different devices and provide more flexible solutions for the design of electronic products. In the future of electronic engineering, the precise selection of BGA Substrate type will be a critical step in achieving a balance between product performance and reliability.
What are the advantages of BGA Substrate?
In the realm of modern electronic equipment design, the Ball Grid Array (BGA) Substrate emerges as a prominent solution, offering distinct advantages over conventional circuit boards. This examination will delve into the superior performance of BGA Substrate, particularly in the areas of miniaturization, high-density layout, and effective heat dissipation capabilities.
To commence, BGA Substrate excels in miniaturization. In contrast to traditional circuit boards, BGA Substrate utilizes a grid structure of spherical solder joints, enabling the integration of a greater number of components within a confined space. This miniaturization design is crucial in alignment with the modern trend of electronic equipment, contributing to the development of lighter and more portable devices while enhancing overall system integration.
Secondly, BGA Substrate exhibits significant advantages in achieving high-density layouts. The closely arranged spherical solder joints result in shorter connection distances between components, effectively minimizing signal transmission delays. This high-density layout not only enhances system response speed but also mitigates resistance and inductance, thereby optimizing signal transmission stability.
A prominent characteristic of BGA substrates is their exceptional heat dissipation performance. The design of spherical solder joints establishes an efficient heat dissipation pathway for electronic components, facilitating temperature reduction, extending the lifespan of devices, and improving performance stability. This attribute holds particular significance in applications demanding rigorous heat dissipation, such as high-performance computing and communication equipment.
In summary, BGA Substrate successfully addresses the ongoing pursuit of lightweight, high performance, and reliability in modern electronic equipment. Its advantages in miniaturization, high-density layout, and exceptional heat dissipation performance make it a standout solution in various application scenarios, establishing it as an indispensable component in contemporary electronic engineering.
Why choose BGA Substrate over other boards?
In the realm of contemporary electronic device design, engineers favor the utilization of Ball Grid Array Substrates (BGA Substrates) owing to their outstanding performance and distinctive attributes. In comparison to conventional circuit boards, BGA Substrates exhibit superior qualities across three pivotal dimensions: electrical performance, size efficiency, and connectivity. Consequently, BGA Substrates have emerged as a crucial element in the design landscape of modern electronic equipment.
Excellent electrical performance
The BGA substrate demonstrates superior electrical performance attributed to its grid-like arrangement of spherical solder joints. This configuration not only enhances the number of contact points but also minimizes resistance and inductance. The resulting design effectively mitigates signal attenuation during transmission, thereby ensuring a consistently stable signal transmission quality. In contrast to conventional circuit boards, BGA substrate offers heightened reliability and stability in electrical performance, positioning it as an optimal selection for contemporary electronic devices demanding superior signal transmission quality.
Size advantage
BGA Substrate stands out for its smaller size. Due to the layout of ball solder joints, BGA Substrate can be designed more compactly compared to other circuit boards. This feature makes the overall size of electronic devices smaller, making it possible for the modern trend of thinness, lightness, and portability. In mobile devices such as smartphones and portable computers, BGA Substrate’s small size design lays a solid foundation for achieving lighter devices.
Reliable connectivity
The BGA substrate exhibits robust connectivity performance due to its unique design. The spherical solder joints it employs offer a multitude of connection points, significantly enhancing the contact area between electronic components and the base plate. This design improvement contributes to heightened reliability in connections, particularly in challenging conditions such as high vibration and elevated temperatures. Consequently, the BGA substrate ensures a steadfast foundation for the stable operation of electronic equipment.
To sum up, BGA Substrate has become the first choice for modern electronic device design due to its excellent electrical performance, smaller size and reliable connectivity. When engineers choose circuit boards, they often prefer to use BGA Substrate to meet the equipment’s requirements for high performance, miniaturization and reliability. Its superior performance not only improves the overall performance of electronic equipment, but also provides broad space for innovative design and development. In today’s pursuit of excellent performance and compact design, the new concept of BGA Substrate has profoundly affected the development direction of modern electronic engineering.
What is the manufacturing process of BGA Substrate?
In modern electronic engineering, the manufacturing process of Ball Grid Array (BGA) Substrate is a precise process involving multiple key steps of the motherboard and base plate. An in-depth understanding of this process helps reveal the secrets of its high quality and reliability.
First, the process of manufacturing BGA Substrate begins with the preparation of the motherboard. Motherboards are typically constructed from high-quality substrate materials to ensure their physical strength and electrical performance meet stringent requirements. When selecting materials, factors such as thermal expansion coefficient and thermal conductivity need to be considered to improve the stability of BGA Substrate.
Next, the design layout on the motherboard plays a key role. BGA Substrate’s spherical solder joints must be precisely arranged into a grid-like structure, which involves highly advanced design software and automation tools. Designers need to consider the arrangement, spacing, and connection of components to ensure the stability of signal transmission and the overall performance of the circuit.
After the design of the motherboard is completed, the manufacturing of the baseboard follows. The copper foil layer on the base plate acts as a conductor and connection. Through processes such as chemical etching, it is ensured that the circuit on the base plate matches the design on the motherboard perfectly. The precision of this step determines the success of subsequent processes.
The subsequent crucial phase in BGA Substrate manufacturing is the ball soldering process, which demands intricate technical expertise. This step involves utilizing soldering equipment to precisely affix ball solder joints to the backplane, ensuring secure attachment of electronic components to the base plate and establishing a stable electrical connection.
Precision and high-quality standards peak during ball soldering, necessitating the incorporation of advanced detection technology to verify the connection quality of each ball solder joint. This proactive approach mitigates potential failures and performance issues, ensuring the reliability of the BGA Substrate. The implementation of highly automated testing equipment not only enhances production efficiency but also guarantees consistency in the manufacturing process.
Quality control assumes a pivotal role in the entire manufacturing sequence. Stringent inspection and testing procedures are employed to identify and rectify any potential defects before the product leaves the production line. This meticulous approach ensures the BGA Substrate’s high quality and reliability, positioning it as the preferred choice in the design of contemporary electronic devices.
In summary, the BGA Substrate manufacturing process is a sophisticated series of procedures involving critical steps, ranging from motherboard and base plate preparation to the technical intricacies of ball soldering, and concluding with rigorous quality control inspections. Each step is indispensable in ensuring the ultimate product’s high quality and reliability. This professional manufacturing process solidifies the BGA Substrate’s irreplaceable role in modern electronic engineering.
In what application fields is BGA Substrate widely used?
The Ball Grid Array (BGA) Substrate, an advanced packaging technology, plays a pivotal role in enhancing the performance and reliability of contemporary electronic devices, including smartphones, computers, and communication equipment. Its extensive applications are instrumental in advancing product capabilities and ensuring robust functionality within these domains.
BGA Substrate is especially vital in smartphone design. The continual evolution of smartphones drives the demand for smaller size, lighter weight, and enhanced performance. With its compact design and high-density layout, BGA Substrate efficiently accommodates the integration of various components, including processors, memory, and sensors. This streamlined integration not only reduces device weight but also enhances overall performance and responsiveness.
Furthermore, BGA Substrate assumes a crucial role in the realm of computers. Contemporary computer systems continually seek higher processing power and faster data transfer speeds. BGA Substrate addresses this need by minimizing signal transmission delays through shorter signal paths, lower resistance, and inductance, thereby optimizing the overall performance of computer systems. Its exceptional heat dissipation capabilities also present an effective solution for managing the thermal challenges of high-performance computers.
In the field of communication equipment, BGA Substrate also plays a vital role. Communication devices need to handle large amounts of data and maintain highly reliable connectivity. BGA Substrate provides communication devices with greater processing power and supports more complex communication protocols through its miniaturization and high-density layout. Its reliable connectivity ensures the stable operation of communication equipment under various environmental conditions, thus meeting the growing needs of modern communication.
Taken together, the wide application of BGA Substrate in modern electronic products such as smartphones, computers and communication equipment has significantly promoted the development of these fields. Its excellent performance and reliability make it an indispensable key technology in today’s electronic engineering. Through continuous innovation and continuous applicability expansion, BGA Substrate will continue to lead the electronics industry toward a more advanced and efficient future.
How to find BGA Substrate?
When looking for high-quality BGA Substrate, choosing the right supplier is crucial. Here are some suggestions to ensure you have easy access to the key components you need, with supplier recommendations including our own.
Company advantages: First of all, consider choosing our company as the supplier of BGA Substrate. With ten years of PCB engineering experience, we are committed to providing high-quality electronic components. By choosing our company, you will benefit from our extensive experience and expertise.
Supplier reputation: Checking the supplier’s reputation and reputation is the key to choosing a BGA Substrate supplier. Understand customer feedback and reviews of potential vendors through web searches, industry forums, and peer recommendations.
Quality certification: Ensure that suppliers have relevant quality certifications, such as ISO 9001, etc. Such certifications usually indicate that a supplier’s products meet international standards and are more reliable.
Work with the manufacturer: Sometimes, it can be a good option to work directly with the manufacturer of BGA Substrate. Manufacturers are often able to provide in-depth information about their products and ensure that the products meet their design specifications.
Technical support: Choose a manufacturer that can provide good technical support to ensure that you can receive timely help during the use of BGA Substrate. This is critical to troubleshooting potential issues and optimizing performance.
How to ensure easy access to key components
Regular delivery: When working with suppliers, make sure they deliver on time and provide a stable supply. This is crucial for your production planning.
Inventory management: Consider working with your supplier on inventory management to ensure adequate BGA Substrate is in stock when needed. This helps alleviate potential supply chain pressures.
Contracts and Guarantees: Sign clear contracts with suppliers specifying delivery times, prices and quality standards. Ensure relevant safeguards are in place to address potential product quality issues.
By carefully selecting suppliers and manufacturers, and establishing good relationships, you can ensure easy access to high-quality BGA Substrate, resulting in better results in your electronic engineering projects.
How to get a quote for BGA Substrate?
In the field of electronic engineering, obtaining a high-quality BGA Substrate quote is a key part of ensuring project success. This involves a deep understanding of market price trends and pricing factors so readers can make more informed decisions in project budgeting.
First, to get an accurate BGA Substrate quote, it’s crucial to pay close attention to market price trends. Understanding current market conditions can help readers better plan their budgets and avoid unnecessary expenses caused by market fluctuations. Regularly tracking the price dynamics of BGA Substrate is crucial to grasp market supply and demand and predict future price changes.
Secondly, pricing factors are one of the key factors affecting BGA Substrate’s quotation. Understanding these factors, such as material cost, manufacturing process complexity, supply chain stability, etc., can help readers more comprehensively evaluate the reasonableness of the quotation. At the same time, considering the competition and technological differences among different suppliers, selectively selecting suitable suppliers is also an effective means to control costs.
When making a decision, readers need to weigh price and performance against the specific needs of their project. The cheaper option isn’t necessarily the most affordable, and a higher price doesn’t always mean better quality. Therefore, an in-depth understanding of BGA Substrate’s technical specifications, quality standards, as well as the supplier’s reputation and after-sales service will help readers make more comprehensive and informed decisions.
For the management of project budget, in addition to considering the unit price, it is also necessary to comprehensively evaluate the overall cost. This includes various potential expense factors such as shipping, customization requirements, bulk purchase discounts, and more. Careful analysis of these aspects can provide readers with a more accurate project budget and ensure that unexpected expenses will not affect the smooth progress of the project in the later stages.
During the quotation stage, timely communication and negotiation are also key to ensuring that the final quotation meets expectations. Establishing a good cooperative relationship with suppliers not only helps to obtain more competitive prices, but also provides more support during project implementation.
Overall, getting a BGA Substrate quote and making an informed decision requires deep market understanding, a keen grasp of pricing factors, and a comprehensive consideration of the overall project budget. Through sound planning and accurate decision-making, readers will be able to ensure the financial sustainability and successful implementation of their projects.
What common questions need answers to about BGA Substrate?
What types of BGA Substrates are available, and which applications do they cater to?
Exploring the various types of BGA Substrates, such as Micro BGA and Ball Column BGA, is essential to grasp their specific features and understand which applications benefit most from each type.
Where can one find reputable sources for BGA Substrate, and what factors should be considered when selecting a supplier?
Guidance on finding high-quality BGA Substrate sources, including suggestions on reliable suppliers and manufacturers, ensures that readers can confidently access the crucial components required for their projects.
How can one obtain accurate and competitive quotes for BGA Substrate?
Providing practical advice on acquiring quotes for BGA Substrate, including insights into market trends and pricing factors, enables readers to make well-informed decisions within their project budgets.
What are some frequently encountered issues with BGA Substrate, and how can they be addressed?
Addressing common concerns and offering solutions related to BGA Substrate ensures that readers are equipped to troubleshoot potential problems effectively, enhancing the reliability of their electronic designs.
What advantages does BGA Substrate offer over conventional circuit boards?
Dive into the advantages, including miniaturization, high-density layout, and superior heat dissipation, which make BGA Substrate a preferred choice in modern electronics.
How is the manufacturing process of BGA Substrate executed?
Gain insights into the intricacies of the manufacturing process, involving precise steps for both the main and bottom boards, ensuring the end product’s high quality and reliability.
How can individuals ensure the seamless integration of BGA Substrate into their electronic projects?
Conclude by offering practical tips and best practices for integrating BGA Substrate into electronic projects, ensuring a smooth and successful implementation.