BGA Cavity Substrate Manufacturer, High speed and high frequency Cavity packaging substrate production. Open cavity(slot) on the PCB or BGA substrates. To do the Depth control slot on the base materials.
BGA Cavity Substrate is an innovative Package Substrate. Its unique feature is that a groove (Cavity) is formed in the base plate for embedding chips or other key components. The purpose behind this design is to achieve higher integration, smaller size, and superior heat dissipation and signal transmission performance in electronic devices. BGA Cavity Substrate plays a vital role in modern electronic manufacturing. Let’s explore its specific role and importance.
First, the groove design of BGA Cavity Substrate allows chips or other components to be directly embedded into the base plate, thus achieving a higher level of integration. By leaving space inside the base plate, not only can the chip be more closely integrated on the circuit board, but it can also accommodate more functional modules and achieve more complex circuit designs. This highly integrated design helps reduce the size and weight of electronic devices and improves product performance and functionality.
Secondly, the groove structure of BGA Cavity Substrate provides convenient conditions for optimizing heat dissipation performance. After the chip is directly embedded in the base plate, heat can be effectively conducted through the close contact between the base plate and the chip, improving heat dissipation efficiency.
The design of BGA Cavity Substrate enhances electrical signal transmission performance by utilizing a groove structure, which shortens signal paths, reduces attenuation and interference, and boosts stability and reliability. This is particularly vital for high-frequency, high-rate data transmission and signal processing, ensuring electronic devices operate smoothly in challenging environments, thus enhancing user experience and product reliability.
Overall, BGA Cavity Substrate serves as a pivotal packaging technology in modern electronic devices. Its groove design not only enables higher integration and smaller form factors but also enhances heat dissipation and signal transmission, thereby supporting performance enhancement and functionality expansion of electronic devices. With ongoing advancements in the electronics industry, BGA Cavity Substrate is poised to become a prominent trend in future electronic product design and manufacturing.
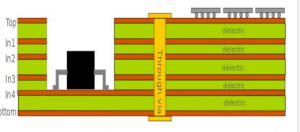
BGA Cavity Substrate
What types of BGA Cavity Substrate are there?
BGA Cavity Substrate, as a key Package Substrate, plays an important role in modern electronic devices. However, to fully realize their advantages, the appropriate type needs to be selected based on specific application needs and manufacturing processes. Below we’ll explore the main types of BGA Cavity Substrate and how to choose the best option for your specific needs.
BGA Cavity Substrate can be made of different materials, common ones include:
FR4 is a commonly utilized composite material composed of glass fiber reinforced epoxy resin, renowned for its excellent mechanical properties and thermal stability. It can be paired with various substrate materials such as high-frequency media like PTFE or ceramics, depending on the specific requirements of the application.
The groove shapes of BGA Cavity Substrate may also vary, common ones include:
Rectangular groove: suitable for conventional chip packaging, easy to manufacture and install.
Irregular grooves: Designed according to the shape and size of a specific chip to minimize space usage.
Package specifications are another important factor to consider when selecting BGA Cavity Substrate. Common package specifications include:
Number of pins: Select the appropriate package specifications based on the number and arrangement of pins of the chip or device.
Package size: Considering the size and layout of the overall circuit board, select an appropriately sized package specification.
To choose the type of BGA Cavity Substrate suitable for specific needs, you need to consider the following aspects:
Application requirements: Determine the required performance parameters, such as high-frequency characteristics, thermal management capabilities, etc., based on specific application scenarios and functional requirements.
Selecting the appropriate BGA Cavity Substrate entails a thorough assessment of factors like chip size, pin arrangement, and manufacturing complexity versus cost. This decision involves weighing various considerations such as material choice, groove shape, and packaging specifications against the specific application requirements and manufacturing constraints. By meticulously evaluating these factors, one can harness the benefits of BGA Cavity Substrate effectively, ensuring optimal performance and reliability of electronic devices.
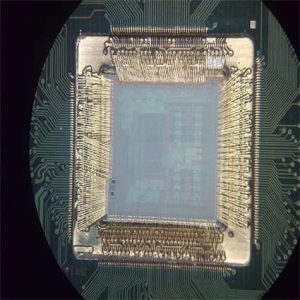
BGA Cavity Substrate
What are the advantages of BGA Cavity Substrate?
BGA Cavity Substrate offers several distinct advantages over traditional packaging technology, making it a prevalent choice in modern electronic devices. Firstly, it enables higher integration by incorporating a groove (Cavity) in the base plate, allowing for closer embedding of chips or components. This not only optimizes space utilization but also reduces overall packaging volume, resulting in thinner, lighter, and more portable devices.
Secondly, BGA Cavity Substrate excels in size efficiency. With its groove design, the base plate size can be adjusted more flexibly, while reducing the distance between the chip and the base plate further shrinks the package size. This compact design enhances electronic device performance and meets consumer demand for sleeker, lighter products.
Moreover, BGA Cavity Substrate demonstrates superior heat dissipation capabilities. Direct contact between the chip and the base plate enables efficient heat transfer, dissipating heat through specialized structures. This enhanced heat dissipation design lowers chip operating temperatures, enhancing device stability and reliability.
Additionally, BGA Cavity Substrate delivers excellent electrical signal transmission performance. The groove design shortens signal transmission paths, reducing impedance and transmission delays, thus improving signal transmission rates and stability. This optimization boosts device data processing capabilities, meeting the requirements for high-speed communication and big data processing.
In summary, BGA Cavity Substrate surpasses traditional packaging technology in integration, size efficiency, heat dissipation, and electrical signal transmission performance. Its widespread adoption in smartphones, communication equipment, automotive electronics, and other fields underscores its indispensable role in modern electronic engineering.
What is the manufacturing process of BGA Cavity Substrate?
Manufacturing BGA Cavity Substrate is a complex and precise process involving multiple key steps, from material preparation to packaging completion, each step is critical.
The manufacturing process of BGA Cavity Substrate starts with material preparation, which involves selecting appropriate substrate materials and copper pours that meet stringent requirements to ensure optimal quality and performance. Typically, non-conductive materials like FR-4 or FR-5 are chosen for the substrate, while copper serves as the conductive layer facilitating connections between the chip and other components.
Next is designing and machining the grooves. Depending on the specific chip size and requirements, the designer will design the shape and size of the grooves on the base plate. The key to this step is to ensure the precision and accuracy of the grooves for subsequent packaging work.
Then comes the process of contacting the copper covering. Inside the recess, copper will be applied to allow connection to the chip or other components. This step requires a high degree of precision and technique to ensure uniformity and integrity of the copper pour for good electrical connection and signal transmission.
Next comes the encapsulation step. Once the copper inside the recess is ready, the chip or other component is embedded in it and packaged. This step includes both precision mounting work and the application of packaging materials to ensure the safety and stability of chips and components.
Manufacturing BGA Cavity Substrates involves a series of crucial steps demanding precision and advanced technology to ensure the final product meets performance and reliability standards. These steps include material preparation, substrate fabrication, component assembly, and packaging. Quality control and testing, including visual inspection, electrical testing, and temperature cycling, are integral to ensuring compliance with specifications. Each step is essential in supporting the advancement and innovation of modern electronic devices.
In what fields is BGA Cavity Substrate used?
BGA Cavity Substrate, an innovative circuit board technology, finds extensive applications across diverse electronic devices. In smartphones and tablets, it facilitates seamless integration of processors, memory, and essential chips, enabling sleeker designs and enhanced performance. In the realm of computers and servers, it optimizes connectivity between crucial components, enhancing system performance and reducing board space. In communication equipment, it ensures robust signal transmission and faster speeds, bolstering device stability and efficiency. Automotive electronics benefit from its resilience to harsh environments, ensuring reliable operation in vehicles’ critical systems. Moreover, in medical equipment, it guarantees precise signal transmission and reliability, meeting stringent industry standards. Overall, BGA Cavity Substrate’s versatile design and superior performance foster innovation across various sectors, driving electronic technology’s continual advancement.
How to find BGA Cavity Substrate manufacturer?
When looking for a BGA Cavity Substrate manufacturer, we should pay special attention to several key aspects to ensure we choose a reliable partner to ensure product quality and project success. Here are some suggestions:
To select a BGA Cavity Substrate manufacturer, thorough evaluation of potential suppliers is essential. This entails assessing their reputation, experience, production capacity, and equipment proficiency. Quality control measures and certifications like ISO 9001 are vital indicators of reliability. Technical support and after-sales service capabilities are also crucial. Ultimately, cost-effectiveness should be weighed against quality and service standards to ensure optimal value. By meticulously scrutinizing these factors, we can identify a suitable partner to facilitate project success.
What is the quote for BGA Cavity Substrate?
When obtaining a quote for BGA Cavity Substrate, it’s crucial to consider several factors to select the appropriate supplier and comprehend the quote’s significance. These factors encompass the diverse materials employed in manufacturing, such as substrate materials, metal layers, insulating materials, among others, all of which directly influence the final product’s pricing.
Different production processes will affect manufacturing costs. For example, using more complex processes may increase manufacturing costs but may improve product quality and performance.
In manufacturing, expenses can rise when high-density interconnect (HDI) or multi-layer designs are necessary. Typically, the per-unit cost decreases for large bulk orders compared to smaller batch orders. Rush orders might incur extra fees.
Additional service and support provided by the manufacturer may affect the price quoted. For example:
To accurately obtain a quote for BGA Cavity Substrate, it’s essential to consider several key factors. Firstly, inquire about the technical support offered by manufacturers to assist with design optimization and production issues. Additionally, check if they provide sample making services at low or no cost for testing purposes. Another crucial aspect is assessing the after-sales service, including quality assurance and repair/replacement policies, as these can impact the overall cost. Consulting multiple manufacturers and evaluating various factors will help in selecting the supplier that aligns best with your requirements and budget.
What are the common problems with BGA Cavity Substrate?
Are there any limitations or drawbacks associated with BGA Cavity Substrate?
While BGA Cavity Substrate offers numerous advantages, it may present challenges in terms of cost, complexity, and compatibility with certain components or manufacturing processes. Designers should carefully evaluate these factors when deciding whether to use BGA Cavity Substrate in their designs.
Can BGA Cavity Substrate be used for high-frequency applications?
Yes, BGA Cavity Substrate can be designed and manufactured to support high-frequency applications. However, it requires careful consideration of factors such as substrate material, layout design, and signal integrity to optimize performance in such applications.
Are there any limitations to the size or complexity of BGA Cavity Substrate designs?
While BGA Cavity Substrate offers flexibility in design, there may be practical limitations regarding size, complexity, and manufacturability. Design constraints should be carefully evaluated during the product development phase to ensure feasibility and optimal performance.
How are BGA Cavity Substrates manufactured?
BGA Cavity Substrates are manufactured using advanced PCB fabrication techniques. This process involves creating cavities on the substrate surface and precisely mounting components within these cavities. The manufacturing process also includes multiple layers of insulation and conductive traces to ensure optimal performance.
Are BGA Cavity Substrates cost-effective compared to other substrate technologies?
The cost-effectiveness of BGA Cavity Substrates depends on factors such as volume production, design complexity, and material selection. While initial setup costs may be higher due to specialized manufacturing processes, the enhanced performance and functionality offered by BGA Cavity Substrates can justify the investment in many applications.
What are the main advantages of using BGA Cavity Substrate?
BGA Cavity Substrate offers several advantages over traditional PCBs. Its key benefits include higher integration density, improved thermal management, and smaller footprint. Additionally, it enables more efficient routing of signals and power, leading to enhanced performance in compact electronic devices.
BGA Cavity Substrate offers advanced capabilities and versatile applications in the field of electronic packaging. By addressing common questions and concerns, stakeholders can better understand its benefits and effectively leverage its potential in various electronic devices and systems.