Aviation PCB Manufacturer.An Aviation PCB Manufacturer specializes in crafting printed circuit boards (PCBs) tailored for aviation applications. With precision engineering and stringent quality control measures, they produce PCBs designed to withstand the demanding conditions of airborne systems. These boards are engineered to meet the rigorous standards of the aviation industry, ensuring reliability, durability, and performance in critical flight operations. From cockpit instrumentation to communication systems, their expertise lies in delivering cutting-edge electronic solutions that uphold safety and efficiency in the skies.
With the rapid advancement of aviation technology, the requirements for avionics systems are becoming increasingly stringent, and the demand for reliability and performance is also increasing. In this wave of development, aviation circuit board (Aviation PCB) plays an indispensable role as a core component that connects and supports various electronic components. This article will deeply explore the definition, design principles, manufacturing process, application scope and many advantages of aviation circuit boards, aiming to reveal the importance and value of this key technology in the aviation field.
What is Aviation PCB?
Aviation circuit board is one of the indispensable basic components in avionics system. They are designed to carry and connect various electronic components inside the aircraft, such as microprocessors, sensors, communication equipment, etc., to support the normal operation and communication functions of the aircraft. Compared with traditional circuit boards, aviation circuit boards must meet higher performance and reliability requirements to cope with the harsh environment and complex working conditions in the aviation field.
The manufacturing process of aviation circuit boards usually uses printed circuit technology, which is characterized by printing electrical wires and connection points on a special material substrate to achieve connections between various electronic components. These materials are usually specialty resins with high temperature and high pressure properties, such as polytetrafluoroethylene (PTFE) or polyimide (PI), to ensure the stability and reliability of circuit boards under extreme temperature and pressure conditions.
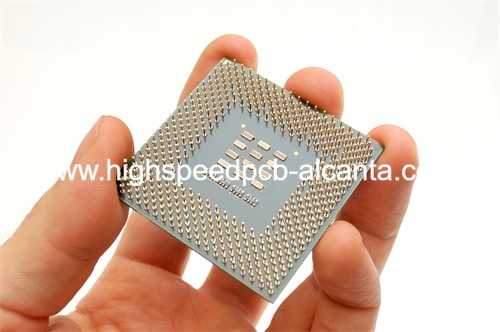
Aviation PCB Manufacturer
The design and manufacturing of aviation circuit boards must comply with strict standards and specifications to ensure their safety and reliability in the aviation field. This includes rigorous electrical performance testing, reliability analysis and environmental suitability testing to verify the board’s performance and stability under various flight conditions.
In short, aviation circuit boards play a vital role in avionics systems. They not only connect and support various electronic components, but are also a key component in ensuring the safety, performance and reliability of aircraft. By using high-quality materials and precision manufacturing processes, aviation circuit boards can meet the stringent requirements for system stability and performance in the aviation field, providing solid support for the development of aviation technology.
Aviation PCB design Reference Guide.
In the design process of aviation circuit boards (Aviation PCB), special consideration needs to be given to stability and performance in extreme environments. Avionics systems often face harsh conditions such as high temperature, high pressure, and high humidity, so a well-designed circuit board is crucial to the reliable operation of the system. Here are a few key points to note when designing aerospace circuit boards:
Choose high temperature and high pressure materials
In an aerospace environment, circuit boards can be exposed to extreme temperatures and pressures, so it is critical to select materials with high temperature and pressure characteristics. Commonly used high-temperature and high-voltage materials include polyimide (PI) and polytetrafluoroethylene (PTFE), which have excellent thermal stability and insulation properties and can maintain the stability of circuit boards under extreme conditions.
Optimize layout and routing
Good layout and wiring design can reduce signal interference and electromagnetic interference, and improve system performance and stability. During the design process, the crossover and interference between signal lines should be minimized, the wiring paths of power and ground wires should be reasonably planned, and shielding measures should be taken to ensure the stability and accuracy of signal transmission.
Consider weight and space constraints
Avionics systems often have strict weight and space constraints, so circuit board layouts need to be compact and efficient when designing them. Through careful design, limited space can be maximized while ensuring board performance and stability. Highly integrated and compact circuit board layouts can be achieved using technologies such as surface-mount assembly (SMT) and multi-layer stacking designs.
To sum up, designing aviation circuit boards requires comprehensive consideration of factors such as material properties, layout design, and space constraints to ensure the stability and performance of the system in extreme environments. Through careful design and strict control, high-quality aviation circuit boards can be achieved, providing a solid guarantee for the reliable operation of avionics systems.
What material is used in Aviation PCB?
As the core component of the avionics system, aviation circuit board (Aviation PCB) material selection is crucial, directly affecting the performance, reliability and adaptability of the system. In the design and manufacturing process of aviation circuit boards, the following main materials are usually used:
FR-4 high performance fiberglass composite material
FR-4 is a common substrate material with excellent insulation properties and mechanical strength. In aviation applications, FR-4 materials are usually specially treated to improve their high temperature resistance, pressure resistance, and fire resistance and adapt to the complex working environment of aircraft.
High temperature and high pressure materials
Avionics systems often need to work under extreme temperature and pressure conditions, so the materials used in aviation circuit boards must have good high temperature resistance and mechanical strength. High-temperature and high-pressure materials can maintain stability over a wide temperature range and have high pressure resistance, making them suitable for aviation applications in various extreme environments.
Special copper foil
The conductive layer of aviation circuit boards usually uses special copper foil, which has high conductivity and corrosion resistance. These copper foils are precisely processed to meet the high requirements of avionics systems for conductive layers and ensure the stability and reliability of signal transmission.
Special coating materials
The surface of aviation circuit boards usually needs to be covered with a special coating material to protect the circuit board from the impact of the external environment, such as moisture, corrosion, etc. These special coating materials have excellent waterproof and anti-corrosion properties and can effectively extend the service life of aviation circuit boards.
High frequency materials
For some avionics systems that need to process high-frequency signals, the materials used in aviation circuit boards also need to have good high-frequency performance to ensure the stability and accuracy of signal transmission. High-frequency materials usually have low dielectric constant and dielectric loss, which can effectively reduce signal attenuation and distortion.
In general, the materials used in aviation circuit boards need to have excellent high temperature and high pressure performance, electrical conductivity, anti-corrosion performance and high frequency performance to meet the stability and reliability requirements of avionics systems in complex environments. By rationally selecting and combining these materials, high-performance aviation circuit boards suitable for various aviation applications can be designed, providing strong support for the development of aviation technology.
What size are Aviation PCB?
Aviation circuit boards show amazing adaptability and diversity in size. Their size depends on the specific scenario and functional requirements of the application. In the aerospace sector, aerospace circuit boards can range in size from as tiny as a few millimeters to as massive as several meters, depending on their purpose and installation space constraints.
Miniaturization Trend and Development of Avionics Equipment
As avionics equipment continues to develop and aircraft design continues to evolve, the requirements for aviation circuit board size are also constantly changing. Especially with the strict requirements on weight and volume of aircraft, the trend of miniaturization is becoming more and more significant. Therefore, aviation circuit boards need to remain precise and compact in size while ensuring the integrity and reliability of their functions.
Standardization and customization: flexible application of dimensions
In the size design of aviation circuit boards, standardization and customization are two important considerations. Standardized dimensions are available for common avionics equipment such as flight control systems and communications systems, which helps reduce production costs and increase productivity. For some special needs and customized avionics systems, the size often needs to be customized according to specific application scenarios and functional requirements to ensure system performance and stability.
Key technologies and size optimization
In the size design of aviation circuit boards, key technologies play a vital role. For example, the use of advanced miniaturization technology can achieve a high degree of integration and compact layout of electronic components, thereby effectively reducing the size of the circuit board. In addition, the use of multi-layer board design and high-density interconnection technology can also effectively optimize the size and performance of circuit boards.
The size of aviation circuit boards is an important consideration in the design of avionics systems. It needs to adapt to evolving technology trends and take into account the actual needs of aircraft design. Through the flexible application of standardization and customization, combined with the continuous innovation of key technologies, the size of aviation circuit boards will be more precise and compact, providing more reliable support for the development and application of avionics systems.
I hope this article can help you better understand the dimensional characteristics of aviation circuit boards and their importance in the aviation field. If you have any questions about this or need further information, please feel free to contact us.
The Manufacturer Process of Aviation PCB.
The manufacturing process of aviation circuit boards is a precise and complex process that requires multiple critical steps to ensure the quality and reliability of the final product. The manufacturing process of aviation circuit boards will be introduced in detail below:
Design
The first step in manufacturing an aerospace circuit board is to design it. The design process involves determining the board’s functionality, layout and routing, and selecting appropriate materials. During the design phase, engineers need to take into account the special requirements of avionics systems, such as earthquake resistance and high temperature resistance.
Printing
After the design is completed, the next step is to convert the design into the printing of the actual circuit board. The printing process uses special printing equipment to print the circuit pattern on the substrate of the circuit board. The substrate usually used is fiberglass-reinforced epoxy resin (FR-4).
Etching
After printing, chemical etching is used to remove the unnecessary metal parts from the circuit board, leaving the required circuit connections. The etching process is accomplished by applying a specific chemical solution to the circuit board, requiring precise control of time and temperature to ensure accuracy.
Assemble
After etching is complete, next comes the assembly process of mounting the electronic components onto the circuit board. This involves the precise soldering of components such as chips, resistors, capacitors, etc. onto printed circuit boards. The assembly of aviation circuit boards usually requires the use of high-precision automated equipment to ensure the accuracy and reliability of connections.
During the manufacturing process, strict quality control and process control are crucial. Aviation circuit boards must meet strict standards and specifications to ensure their stability and reliability in the aviation environment. Therefore, multiple quality checks and tests are required during the manufacturing process to ensure that each step meets requirements.
Highly automated manufacturing equipment and precise process control are key factors to ensure the performance and stability of aviation circuit boards. Only through careful design and strict quality control can high-quality aviation circuit boards that meet the requirements of avionics systems be produced.
The Application area of Aviation PCB.
Aviation circuit boards play a key role in various electronic systems in civil aviation, military aviation, and aerospace. They are widely used in various key systems, including flight control systems, communication systems, navigation systems, etc., providing important support for aircraft performance, safety and reliability.
In the field of civil aviation, aviation circuit boards are used in all aspects of passenger aircraft, cargo aircraft and various civil aviation aircraft. For example, the aviation circuit board in the flight control system is responsible for processing flight data, controlling flight attitude, and ensuring the stability and safety of the aircraft. The aviation circuit board in the communication system is responsible for handling voice communications, data transmission, and communication connections between the aircraft and the ground control center. The aviation circuit board in the navigation system is used to process position information, navigation data, and ensure the precise navigation and positioning of the aircraft in the air.
In the field of military aviation, aviation circuit boards have a wider range of applications. In addition to flight control, communication and navigation systems, more complex and diverse electronic systems are included. For example, military aircraft’s weapon control systems, reconnaissance systems, electronic countermeasures systems, etc. all require high-performance aviation circuit boards to support their functions. These circuit boards are not only required to be stable and reliable, but also need to have certain anti-interference and concealment properties to cope with complex combat environments and threats.
In the aerospace field, aviation circuit boards also play an indispensable role. Aviation circuit boards are used in various satellite systems, spacecraft control systems, and key equipment in manned space missions. They need to be able to work in extreme space environments and have a high degree of stability and reliability to ensure the normal operation and mission execution of the spacecraft.
In general, aviation circuit boards have a wide range of applications in civil aviation, military aviation and aerospace fields, involving flight control, communications, navigation and other aspects. They provide indispensable components for the performance, safety and reliability of aircraft. support and guarantee. With the continuous progress and development of aviation technology, the application prospects of aviation circuit boards will be broader, injecting new power and vitality into the development of the aviation field.
What are the advantages of Aviation PCB?
Compared with traditional circuit boards, aviation circuit boards have the following significant advantages:
High reliability
Aviation circuit boards use high-quality materials and manufacturing processes to ensure the stability and reliability of the system in extreme environments. In the aviation field, electronic systems often need to operate under harsh conditions such as high temperature, high pressure, and vibration, so the stability of circuit boards is crucial. Using high-quality materials and strict manufacturing processes, aviation circuit boards can effectively withstand the challenges of these extreme environments and ensure the safe operation of aircraft.
High density integration
Aviation circuit boards use precise design and manufacturing processes to achieve a compact layout of electronic components and improve system integration and performance. In avionics systems, space and weight are often very valuable resources, so electronic components need to be integrated into as small a space as possible. Aviation circuit boards use advanced layout and wiring technology to achieve high-density integration, maximize space savings, and improve system performance and efficiency.
Efficient production
Aviation circuit boards utilize automated manufacturing equipment and process optimization to improve production efficiency and reduce costs. In the manufacturing process of avionics systems, efficient production is crucial. Aviation circuit board manufacturing usually requires multiple complex steps, such as design, printing, etching, assembly, etc. The use of automated equipment and process optimization can greatly improve production efficiency, shorten the manufacturing cycle, and reduce production costs, thereby making the avionics system more efficient. Competitive.
To sum up, aviation circuit boards have become an indispensable key component of electronic systems in the aviation field due to their advantages such as high reliability, high-density integration and efficient production. With the continuous development and progress of aviation technology, aviation circuit boards will continue to play an important role in promoting the continuous improvement of the performance and reliability of avionics systems and promoting the sustainable development of the aviation industry.
FAQ
What is the difference between aviation circuit boards and ordinary circuit boards?
Aviation circuit boards are different from ordinary circuit boards in material selection, design requirements and manufacturing processes. First of all, aviation circuit boards need to use high-quality, high-temperature-resistant, and high-pressure-resistant special materials to ensure stability and reliability in extreme environments. Secondly, in terms of design, avionics circuit boards need to take into account the weight and space constraints of avionics systems and design compact and efficient layouts. In addition, the manufacturing process requirements of aviation circuit boards are more stringent, requiring the use of highly automated manufacturing equipment and precise process control to ensure the quality and reliability of circuit boards.
What aspects need special attention in the design of aviation circuit boards?
When designing aviation circuit boards, special attention needs to be paid to the following aspects. The first is layout and routing to avoid signal interference and electromagnetic interference and optimize the performance of the circuit board. The second is material selection. Materials that are resistant to high temperatures and high pressures need to be selected to ensure stability and reliability in extreme environments. Additionally, a compact and efficient circuit board layout needs to be designed taking into account the weight and space constraints of the avionics system. Finally, attention needs to be paid to electromagnetic compatibility (EMC) issues to ensure that aviation circuit boards work properly without interfering with other equipment.
What is the manufacturing process of aviation circuit boards?
The manufacturing process of aviation circuit boards includes multiple steps such as design, printing, etching, and assembly. First, the circuit board is designed according to the system requirements and key parameters such as layout and wiring, material selection and so on are determined. The circuit pattern is then printed onto the special material substrate using printed circuit technology. Next, excess metal is removed through chemical etching techniques to form circuit patterns. Finally, the components are installed and welded to complete the manufacturing of the aviation circuit board. Throughout the entire manufacturing process, each step needs to be strictly controlled to ensure the quality and reliability of the circuit board.
What are the application areas of aviation circuit boards?
Aviation circuit boards are widely used in various electronic systems in civil aviation, military aviation and aerospace fields, including flight control systems, communication systems, navigation systems, etc. They play an important role in improving aircraft performance, safety and reliability. Aviation circuit boards are also used in fields such as drones, aircraft maintenance and monitoring systems, promoting the continuous development and innovation of aviation technology.