As a leading Antenna Cavity PCBs Manufacturer, we specialize in designing and producing high-quality printed circuit boards with integrated antenna cavities. Our advanced manufacturing techniques ensure superior signal performance, reduced interference, and enhanced reliability for wireless communication applications. Trust us for innovative solutions that meet the highest industry standards.
Antenna cavity PCBs (Printed Circuit Boards) are a specialized type of PCB designed to integrate antenna structures within cavities or recesses of the board. These PCBs are engineered to enhance the performance and miniaturization of wireless communication systems. By embedding antenna components directly into the PCB, these designs offer improved signal integrity, reduced interference, and greater design flexibility. Antenna cavity PCBs are crucial in various applications, including smartphones, IoT devices, automotive systems, and aerospace communications.
What is an Antenna Cavity PCB?
An antenna cavity PCB incorporates cavities or recesses that house antenna elements directly within the PCB structure. This design allows the antennas to be protected and integrated more seamlessly into the overall device architecture. The cavities are precisely engineered to match the dimensions and electrical characteristics required for optimal antenna performance. This integration helps in reducing the overall size of the device, enhancing signal transmission, and providing better protection to the antenna components from external environmental factors.
Antenna Cavity PCB Design Reference Guide
Designing an antenna cavity PCB involves careful consideration of various factors to ensure the antennas function optimally and the PCB maintains its structural integrity.
Material selection is vital to achieving the desired electrical and mechanical properties:
High-Frequency Substrates: Materials such as Rogers, Taconic, and PTFE (Polytetrafluoroethylene) are used for their low dielectric loss and stability at high frequencies.
Conductive Materials: Copper is typically used for conductive traces and antenna elements due to its excellent conductivity and ease of fabrication.
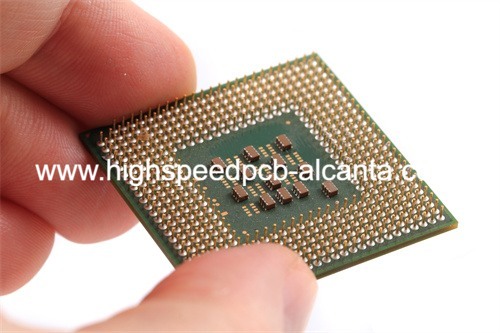
Antenna Cavity PCBs Manufacturer
Dielectric Materials: Low-loss dielectric materials are chosen to support high-frequency signal transmission and maintain signal integrity.
Signal Integrity: High signal integrity is maintained through careful impedance matching, minimizing parasitic effects, and optimizing the layout for signal paths.
Thermal Management: Effective thermal management is crucial to prevent overheating of components, using techniques like thermal vias and heat spreaders.
Mechanical Stability: Despite their specialized design, the substrates must provide robust mechanical support to withstand stresses during assembly and operation.
Reliability: Long-term reliability is ensured through the use of high-quality materials and precise manufacturing processes to prevent issues such as delamination and warping.
What Materials are Used in Antenna Cavity PCBs?
Materials used in antenna cavity PCBs are selected for their ability to meet stringent electrical and thermal performance requirements:
High-Frequency Substrates: Rogers, Taconic, and PTFE materials are commonly used for their low dielectric loss and high-frequency stability.
Conductive Metals: Copper is the preferred material for conductive traces and antenna elements due to its high conductivity and reliability.
Low-Loss Dielectric Materials: Advanced dielectric materials with low loss tangent and high dielectric constant support high-frequency signal transmission.
Encapsulation Materials: Specialized encapsulants protect the embedded antenna components and enhance mechanical stability.
What Size are Antenna Cavity PCBs?
The size of antenna cavity PCBs varies depending on the specific application and device requirements:
Thickness: Thickness can range from a few millimeters to several centimeters, depending on the number of layers and the depth of the cavities.
Length and Width: Dimensions are determined by the size of the antenna elements and the layout of the interconnections, ranging from a few millimeters for small devices to several centimeters for larger applications.
The Manufacturing Process of Antenna Cavity PCBs
The manufacturing process for antenna cavity PCBs involves several precise and controlled steps to ensure high quality and performance:
High-frequency substrates, conductive materials, and encapsulants are prepared and cut into appropriate sizes for processing.
Layers are fabricated by laminating conductive and insulating materials in a stack. Each layer is patterned using photolithography to define the circuitry.
Cavities are created using precise milling, laser ablation, or chemical etching techniques, ensuring accurate dimensions and placement.
Microvias and through-holes are drilled using laser or mechanical drilling techniques. These holes are then plated with copper to create electrical connections between layers.
Photolithography and etching processes are used to create fine-pitch circuitry on each layer, requiring high precision for accurate interconnections.
After layer fabrication, the layers are laminated together under heat and pressure. Antenna elements are placed into the cavities and secured with encapsulants. The assembled substrate undergoes rigorous testing, including electrical testing, thermal cycling, and mechanical stress tests, to ensure performance and reliability.
The Application Area of Antenna Cavity PCBs
Antenna cavity PCBs enable advanced capabilities in a wide range of applications:
In smartphones and tablets, antenna cavity PCBs support the integration of multiple antennas for wireless communication, enhancing connectivity and performance.
In IoT applications, these PCBs enable compact and efficient integration of antennas, facilitating reliable wireless communication in various smart devices.
In automotive applications, antenna cavity PCBs support advanced driver assistance systems (ADAS), vehicle-to-everything (V2X) communication, and infotainment systems.
In aerospace applications, these PCBs provide reliable and high-performance communication systems, ensuring robust connectivity in challenging environments.
In medical devices, antenna cavity PCBs support wireless communication for diagnostic and monitoring equipment, improving patient care and device functionality.
What are the Advantages of Antenna Cavity PCBs?
Antenna cavity PCBs offer several advantages that make them indispensable for advanced wireless communication applications:
Compact Design: The integration of antennas within cavities allows for the miniaturization of electronic packages, enabling more compact and portable devices.
Enhanced Performance: Optimized materials and design ensure high signal integrity, low power loss, and effective thermal management.
Improved Signal Integrity: The integration of antennas within the PCB reduces signal loss and interference, enhancing overall communication performance.
Greater Design Flexibility: The ability to embed antennas within the PCB allows for more innovative and flexible device designs.
Enhanced Protection: Antennas embedded within the PCB are better protected from environmental factors, improving their longevity and reliability.
FAQ
What are the key considerations in designing antenna cavity PCBs?
Key considerations include material selection for high-frequency performance, precise cavity design for optimal antenna integration, and ensuring mechanical stability and reliability.
How do antenna cavity PCBs differ from standard PCBs?
Antenna cavity PCBs feature integrated cavities for housing antenna elements, which allows for reduced overall height, improved signal integrity, and enhanced protection of antenna components compared to standard PCBs.
What is the typical manufacturing process for antenna cavity PCBs?
The process involves material preparation, layer fabrication, cavity formation, drilling and plating, circuit patterning, assembly, and rigorous testing to ensure high performance and reliability.
What are the main applications of antenna cavity PCBs?
These PCBs are used in mobile devices, IoT devices, automotive systems, aerospace communications, and medical devices, providing advanced functionality and reliability in these fields.