Aluminum Substrate Manufacturer.An Aluminum Substrate Manufacturer specializes in producing high-quality aluminum substrates used in various electronic applications. These substrates offer excellent thermal conductivity, durability, and lightweight properties, making them ideal for high-power LED lighting, automotive electronics, and industrial power supplies. With advanced manufacturing techniques and strict quality control, an Aluminum Substrate Manufacturer ensures reliable performance and long-lasting products tailored to meet the specific needs of different industries.
Aluminum substrates are widely used in modern electronics due to their excellent thermal conductivity, mechanical strength, and cost-effectiveness. These substrates form the backbone of numerous electronic devices, providing a solid foundation for the placement of electronic components and ensuring efficient heat dissipation. In this article, we will delve into the characteristics, design considerations, materials, manufacturing processes, applications, and advantages of aluminum substrates, highlighting their significance in the electronics industry.
What is an Aluminum Substrate?
An aluminum substrate refers to a base material made primarily of aluminum, used in the construction of printed circuit boards (PCBs) and other electronic assemblies. The aluminum base provides structural support and enhances the thermal management of the device by efficiently dissipating heat generated by electronic components. These substrates are especially popular in high-power and high-temperature applications, where effective heat dissipation is crucial for the reliable operation of electronic devices.
Characteristics of Aluminum Substrates
Aluminum substrates possess several key characteristics that make them ideal for use in electronic applications:
Aluminum has excellent thermal conductivity, which allows it to effectively dissipate heat generated by electronic components. This helps in maintaining optimal operating temperatures and preventing overheating.
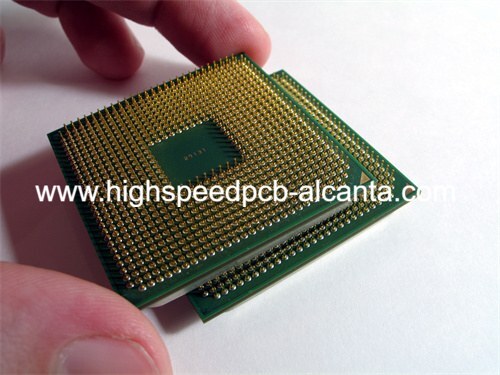
Aluminum Substrate Manufacturer
Aluminum substrates provide robust mechanical support, ensuring the durability and stability of the electronic assembly. This is particularly important in applications subject to mechanical stress or vibrations.
Aluminum is a lightweight material, making it suitable for applications where weight is a critical factor, such as in aerospace and portable electronic devices.
Aluminum is relatively inexpensive compared to other high-performance materials, offering a cost-effective solution for thermal management in electronic assemblies.
Aluminum substrates are often treated with surface coatings to enhance their corrosion resistance, ensuring long-term reliability in various environmental conditions.
Design Considerations for Aluminum Substrates
Designing aluminum substrates for electronic applications involves several important considerations to achieve optimal performance:
Effective thermal management is crucial in aluminum substrates. This includes designing heat sinks, thermal vias, and other cooling mechanisms to dissipate heat efficiently and maintain optimal operating temperatures.
The placement of components on the aluminum substrate must be carefully planned to ensure efficient heat dissipation and minimize thermal stress on sensitive components.
Although aluminum is an excellent conductor of heat, it also conducts electricity. Therefore, proper insulation between the aluminum base and the conductive traces is essential to prevent electrical short circuits.
The surface finish of the aluminum substrate plays a vital role in enhancing its corrosion resistance and solderability. Common finishes include anodizing, electroless nickel plating, and organic solderability preservatives (OSP).
The layout of conductive traces on the aluminum substrate must be optimized for signal integrity and minimal signal loss. This involves precise trace geometries and controlled impedance.
Materials Used in Aluminum Substrates
The choice of materials for aluminum substrates is crucial to achieving the desired performance:
The primary material used is aluminum, chosen for its excellent thermal conductivity, mechanical strength, and cost-effectiveness.
A dielectric layer is applied between the aluminum base and the conductive traces to provide electrical insulation. Common dielectric materials include polyimide, epoxy resin, and ceramic-filled polymers.
Copper is typically used for the conductive traces and pads due to its excellent electrical conductivity. Surface finishes such as gold, silver, or tin are often applied to enhance performance and reliability.
Manufacturing Process of Aluminum Substrates
The manufacturing process of aluminum substrates involves several precise steps to ensure high quality and performance:
The aluminum base is prepared by cutting it to the desired size and shape. The surface is then cleaned and treated to enhance adhesion.
A dielectric layer is applied to the surface of the aluminum base. This layer provides electrical insulation and ensures proper adhesion of the conductive traces.
The circuit patterns are created using photolithographic processes. A photosensitive film (photoresist) is applied to the copper surface, exposed to ultraviolet (UV) light through a mask, and developed to reveal the desired circuit patterns. The PCB is then etched to remove the unwanted copper, leaving behind the traces and pads.
Vias are drilled into the substrate to create vertical electrical connections between different layers. These holes are then plated with copper to establish conductive pathways.
Surface finishes such as ENIG (Electroless Nickel Immersion Gold) or immersion silver are applied to the contact pads to enhance solderability and protect the conductive traces from oxidation and corrosion.
The final substrates undergo assembly, where components are added. Rigorous testing, including signal integrity tests, impedance matching tests, and environmental stress tests, are conducted to ensure the substrates meet the required performance standards.
Applications of Aluminum Substrates
Aluminum substrates are used in a wide range of electronic applications:
Aluminum substrates are widely used in LED lighting applications due to their excellent thermal management properties, ensuring the longevity and performance of LED components.
These substrates are used in power electronic devices, such as power converters, inverters, and motor drives, where efficient heat dissipation is critical for reliable operation.
In the automotive industry, aluminum substrates are used in various electronic control units (ECUs), including engine control modules, battery management systems, and lighting systems.
Aluminum substrates are used in aerospace applications for their lightweight and thermal management properties, ensuring the reliable performance of electronic systems in demanding environments.
These substrates are used in consumer electronics, such as smartphones, tablets, and laptops, to enhance thermal management and improve the overall performance and reliability of the devices.
Advantages of Aluminum Substrates
Aluminum substrates offer several advantages that make them indispensable in electronic applications:
The excellent thermal conductivity of aluminum ensures efficient heat dissipation, preventing overheating and maintaining optimal operating temperatures.
Aluminum substrates provide robust mechanical support, ensuring the durability and stability of electronic assemblies.
The lightweight nature of aluminum makes it suitable for applications where weight is a critical factor.
Aluminum substrates offer a cost-effective solution for thermal management, making them an attractive option for various electronic applications.
Treated aluminum substrates offer good corrosion resistance, ensuring long-term reliability in various environmental conditions.
FAQ
What materials are commonly used in aluminum substrates?
Common materials used in aluminum substrates include an aluminum base for thermal conductivity and mechanical strength, a dielectric layer for electrical insulation, and copper for conductive traces. Surface finishes such as gold, silver, or tin are applied to enhance performance and reliability.
How do aluminum substrates improve LED lighting applications?
Aluminum substrates improve LED lighting applications by providing excellent thermal management, efficiently dissipating heat generated by the LEDs. This helps maintain optimal operating temperatures, enhancing the longevity and performance of LED components.
Can aluminum substrates be used in automotive electronics?
Yes, aluminum substrates are widely used in automotive electronics, including engine control modules, battery management systems, and lighting systems. Their thermal management properties and mechanical strength make them suitable for demanding automotive applications.
What are the common applications of aluminum substrates in consumer electronics?
In consumer electronics, aluminum substrates are used in smartphones, tablets, and laptops to enhance thermal management and improve the overall performance and reliability of the devices. The lightweight and cost-effective nature of aluminum makes it an attractive option for these applications.