Aluminum Nitride Substrate Manufacturer.As a leading Aluminum Nitride Substrate Manufacturer, we specialize in producing high-quality substrates that offer exceptional thermal conductivity and electrical insulation. Our state-of-the-art manufacturing processes ensure precision and reliability, making our products ideal for high-performance electronic applications, including power electronics, LED lighting, and RF devices. Trust our expertise to deliver advanced solutions tailored to meet your specific needs.
Aluminum nitride (AlN) substrates are essential in the field of electronics and semiconductor packaging due to their excellent thermal conductivity, electrical insulation properties, and mechanical strength. These characteristics make AlN substrates ideal for high-power and high-frequency applications. This article delves into the properties, manufacturing process, applications, and advantages of aluminum nitride substrates, highlighting their crucial role in modern electronics.
What is an Aluminum Nitride Substrate?
An aluminum nitride substrate is a type of ceramic material used in electronic and microelectronic applications. It serves as a foundation for mounting and interconnecting semiconductor devices, providing mechanical support, thermal management, and electrical insulation. AlN substrates are highly valued for their ability to efficiently dissipate heat, making them suitable for applications where thermal management is critical.
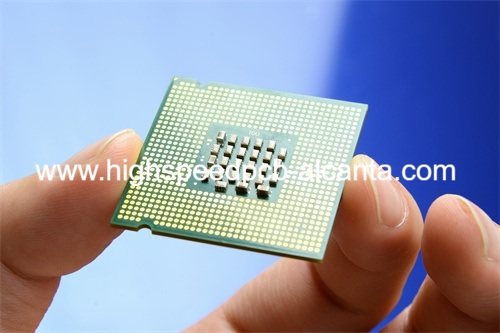
Aluminum Nitride Substrate Manufacturer
Properties of Aluminum Nitride Substrates
Aluminum nitride substrates possess a unique combination of properties that make them ideal for high-performance electronic applications:
AlN substrates have a thermal conductivity of up to 200 W/m·K, which is significantly higher than many other ceramic materials. This property allows them to efficiently dissipate heat generated by electronic components, reducing the risk of thermal damage and enhancing performance.
AlN is an excellent electrical insulator, with a high dielectric strength and low dielectric loss. This ensures that electronic signals are not interfered with by stray currents, maintaining signal integrity and reliability.
AlN substrates exhibit high mechanical strength and resistance to wear and thermal shock. This makes them durable and reliable under various operating conditions.
The coefficient of thermal expansion (CTE) of AlN closely matches that of silicon, making it compatible with silicon-based devices and reducing thermal stress during temperature changes.
AlN substrates are chemically stable and resistant to corrosion by most chemicals, ensuring long-term reliability in harsh environments.
The Manufacturing Process of Aluminum Nitride Substrates
The manufacturing process of aluminum nitride substrates involves several precise steps to ensure high quality and performance:
High-purity aluminum nitride powder is synthesized through methods such as carbothermal reduction or direct nitridation. The powder is then milled to achieve a fine and uniform particle size.
The AlN powder is formed into the desired shape using techniques such as tape casting, hot pressing, or extrusion. Tape casting is commonly used to produce thin, flat substrates.
The formed AlN green bodies are sintered at high temperatures (typically around 1800-1900°C) in a nitrogen atmosphere. Sintering densifies the material, enhancing its thermal and mechanical properties.
After sintering, the substrates undergo surface finishing processes such as grinding and polishing to achieve the desired surface roughness and flatness. This ensures good adhesion and contact with electronic components.
For applications requiring electrical connections, the substrates are metallized with conductive materials such as gold, silver, or copper. This involves processes like sputtering, electroplating, or screen printing to create conductive patterns on the substrate surface.
The finished substrates undergo rigorous quality control tests to ensure they meet the required specifications for thermal conductivity, mechanical strength, and electrical insulation.
Applications of Aluminum Nitride Substrates
Aluminum nitride substrates are used in a wide range of high-performance applications, including:
AlN substrates are used in power modules and semiconductor devices to efficiently dissipate heat generated by high-power components, ensuring reliable operation and extending device lifespan.
AlN substrates are suitable for high-frequency and microwave devices due to their excellent thermal and electrical properties. They are used in applications such as RF amplifiers, microwave filters, and antennas.
The high thermal conductivity of AlN substrates helps manage the heat generated by LEDs and other optoelectronic devices, improving performance and reliability.
AlN substrates are used in telecommunication equipment such as base stations and satellite communication systems, where efficient thermal management is essential for maintaining signal integrity.
In automotive applications, AlN substrates are used in components such as power inverters and motor controllers, where they help manage heat and ensure reliable operation under varying temperatures.
AlN substrates are used in medical devices that require reliable thermal management and electrical insulation, such as imaging equipment and diagnostic instruments.
Advantages of Aluminum Nitride Substrates
Aluminum nitride substrates offer several advantages that make them ideal for high-performance electronic applications:
The high thermal conductivity of AlN substrates allows for efficient heat dissipation, preventing overheating and improving the reliability and performance of electronic components.
AlN substrates provide excellent electrical insulation, ensuring that electronic signals remain clear and undisturbed by stray currents.
The high mechanical strength and thermal shock resistance of AlN substrates make them durable and reliable under various operating conditions.
The CTE of AlN closely matches that of silicon, reducing thermal stress and improving compatibility with silicon-based devices.
AlN substrates are chemically stable and resistant to corrosion, ensuring long-term reliability in harsh environments.
AlN substrates can be used in a wide range of applications, from power electronics and high-frequency devices to LEDs and medical devices.
FAQ
What makes aluminum nitride substrates suitable for high-power applications?
Aluminum nitride substrates are suitable for high-power applications due to their high thermal conductivity, which allows them to efficiently dissipate heat generated by high-power components. This helps prevent overheating and improves the reliability and performance of the devices.
How do aluminum nitride substrates improve the performance of LEDs?
Aluminum nitride substrates improve the performance of LEDs by efficiently managing the heat generated during operation. This helps maintain optimal operating temperatures, reducing the risk of thermal damage and extending the lifespan of the LEDs.
Can aluminum nitride substrates be used in harsh environments?
Yes, aluminum nitride substrates can be used in harsh environments due to their chemical stability and resistance to corrosion. They maintain their performance and reliability even in challenging conditions.
What are the common methods for metallizing aluminum nitride substrates?
Common methods for metallizing aluminum nitride substrates include sputtering, electroplating, and screen printing. These processes create conductive patterns on the substrate surface, enabling electrical connections for various applications.