Aluminum Nitride Substrate Manufacturer.”Aluminum Nitride Substrate Manufacturer” specializes in crafting high-quality substrates crucial for electronic components. Our expertise lies in precision manufacturing processes that ensure superior thermal conductivity and electrical insulation, meeting the stringent demands of modern electronics.
The Aluminum Nitride (AlN) substrate is a cutting-edge material widely used in various high-performance electronic and thermal management applications. Known for its excellent thermal conductivity, electrical insulation properties, and mechanical strength, AlN substrates are indispensable in industries such as telecommunications, automotive, aerospace, and power electronics. This article delves into the properties, structure, manufacturing process, applications, and advantages of Aluminum Nitride substrates.
What is an Aluminum Nitride Substrate?
An Aluminum Nitride (AlN) substrate is a type of ceramic material composed primarily of aluminum and nitrogen. AlN substrates are renowned for their high thermal conductivity, which significantly surpasses that of many other ceramic materials. This exceptional thermal property makes AlN substrates highly effective in dissipating heat generated by electronic components, thereby enhancing the performance and longevity of electronic devices.
In addition to thermal conductivity, AlN substrates exhibit excellent electrical insulation, ensuring minimal electrical interference between adjacent electronic components. Their mechanical strength and durability further contribute to their suitability for demanding applications. AlN substrates are typically produced in the form of thin sheets or wafers, which can be tailored to specific dimensions and thicknesses to meet the requirements of various applications.
Structure of Aluminum Nitride Substrates
The structure of Aluminum Nitride substrates is characterized by a crystalline lattice composed of aluminum and nitrogen atoms. This crystalline structure is responsible for the material’s superior thermal and electrical properties. Key features of AlN substrates include:
AlN substrates have a hexagonal wurtzite crystal structure, which provides high thermal conductivity and excellent mechanical properties. This crystalline structure is highly stable, making AlN substrates suitable for use in high-temperature environments.
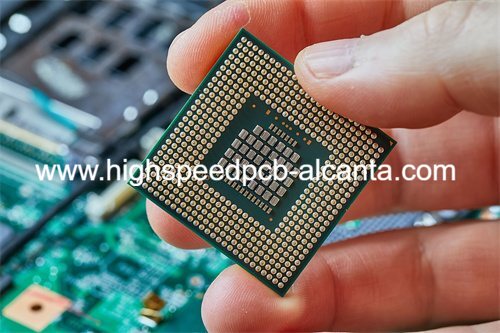
Aluminum Nitride Substrate Manufacturer
AlN substrates are often manufactured in thin film configurations, allowing for efficient heat dissipation and minimal thermal resistance. The thin film structure also enables precise control over the substrate’s thickness and surface finish.
AlN substrates are typically produced with high purity levels to ensure optimal performance. The absence of impurities in the material minimizes the risk of electrical interference and enhances thermal conductivity.
The surface finish of AlN substrates is critical for their performance in electronic applications. Advanced polishing techniques are used to achieve a smooth and uniform surface, reducing the likelihood of defects and improving the substrate’s overall reliability.
Materials Used in Aluminum Nitride Substrates
The primary material used in the production of Aluminum Nitride substrates is high-purity aluminum nitride powder. This powder is synthesized through various chemical processes to ensure its purity and consistency. Key materials and processes involved in the production of AlN substrates include:
The base material for AlN substrates is aluminum nitride powder, which is synthesized using methods such as carbothermal reduction or direct nitridation of aluminum. The powder must be of high purity to achieve the desired thermal and electrical properties.
Sintering additives, such as yttria (Y2O3) or calcium oxide (CaO), are often added to the aluminum nitride powder to enhance the sintering process. These additives help to densify the material and improve its mechanical strength.
Binder materials are used to hold the aluminum nitride powder together during the forming process. These binders are typically organic compounds that are removed during the sintering process to achieve a pure ceramic material.
Surface coatings, such as metallization layers, can be applied to AlN substrates to enhance their compatibility with electronic components. These coatings improve the adhesion of conductive materials and protect the substrate from environmental factors.
The Manufacturing Process of Aluminum Nitride Substrates
The manufacturing process of Aluminum Nitride substrates involves several intricate steps, each critical for achieving the high-performance characteristics required for advanced electronic applications. The process includes:
High-purity aluminum nitride powder is prepared using chemical synthesis methods. The powder is then mixed with sintering additives and binder materials to form a homogeneous mixture.
The mixture is formed into the desired shape using techniques such as tape casting, hot pressing, or extrusion. Tape casting involves spreading the mixture onto a flat surface to create thin sheets, while hot pressing and extrusion are used to create thicker substrates.
The formed substrates are subjected to a debinding process to remove the organic binder materials. This step involves heating the substrates in a controlled atmosphere to decompose and volatilize the binders.
The debound substrates are sintered at high temperatures to densify the material and achieve the desired mechanical and thermal properties. Sintering involves heating the substrates in a controlled environment to facilitate the bonding of aluminum nitride particles and the removal of any remaining impurities.
After sintering, the substrates are machined to achieve the desired dimensions and surface finish. Advanced polishing techniques are used to create a smooth and uniform surface, essential for high-performance electronic applications.
Optional surface coatings, such as metallization layers, can be applied to enhance the compatibility of the substrates with electronic components. These coatings are typically applied using techniques such as sputtering or electroplating.
Application Areas of Aluminum Nitride Substrates
Aluminum Nitride substrates are used in a wide range of applications across various industries due to their exceptional thermal and electrical properties. Key application areas include:
AlN substrates are widely used in power electronics, where efficient heat dissipation is critical. They are employed in power modules, semiconductor devices, and LED lighting to manage heat and improve performance.
In telecommunications, AlN substrates are used in high-frequency and microwave components, such as RF amplifiers and antennas. Their high thermal conductivity and electrical insulation properties make them ideal for these applications.
The automotive industry uses AlN substrates in advanced driver-assistance systems (ADAS), electric vehicle (EV) power systems, and infotainment systems. These substrates provide the necessary thermal management and reliability for automotive electronics.
In aerospace applications, AlN substrates are used in satellite communication systems, avionics, and radar systems. Their ability to withstand high temperatures and harsh environments makes them suitable for aerospace electronics.
AlN substrates are used in medical devices, such as imaging equipment and diagnostic instruments, where precise thermal management and electrical insulation are essential.
Advantages of Aluminum Nitride Substrates
Aluminum Nitride substrates offer several advantages that make them a preferred choice for high-performance electronic and thermal management applications. These advantages include:
AlN substrates have one of the highest thermal conductivities among ceramic materials, making them highly effective at dissipating heat generated by electronic components. This property is critical for preventing overheating and ensuring the reliable operation of electronic devices.
AlN substrates provide superior electrical insulation, minimizing the risk of electrical interference between adjacent components. This property is essential for maintaining signal integrity and ensuring the proper functioning of electronic circuits.
The robust mechanical properties of AlN substrates make them suitable for use in demanding environments. They can withstand thermal cycling, mechanical stress, and harsh conditions without compromising performance.
AlN substrates exhibit excellent chemical stability, resisting corrosion and degradation in various environments. This property ensures long-term reliability and performance in applications where chemical exposure is a concern.
FAQ
What makes Aluminum Nitride substrates suitable for high-performance electronic applications?
Aluminum Nitride substrates are ideal for high-performance electronic applications due to their high thermal conductivity, excellent electrical insulation, and robust mechanical properties. These characteristics enable efficient heat dissipation, minimal electrical interference, and reliable performance in demanding environments.
Can Aluminum Nitride substrates be used in high-temperature environments?
Yes, Aluminum Nitride substrates are highly suitable for high-temperature environments. Their excellent thermal stability and resistance to thermal cycling make them ideal for applications where high temperatures are a concern, such as power electronics and aerospace systems.
How do Aluminum Nitride substrates ensure effective thermal management?
Aluminum Nitride substrates ensure effective thermal management through their high thermal conductivity, which allows for efficient heat dissipation from electronic components. This property helps prevent overheating and enhances the performance and longevity of electronic devices.
What industries benefit the most from using Aluminum Nitride substrates?
Industries that benefit the most from using Aluminum Nitride substrates include power electronics, telecommunications, automotive electronics, aerospace, and medical devices. These industries require high-performance thermal management and electrical insulation, which AlN substrates provide.