Aluminum Nitride PCB Manufacturing.Aluminum Nitride PCB Manufacturing involves the production of printed circuit boards (PCBs) using aluminum nitride as the substrate material. This process is highly valued in industries requiring excellent thermal conductivity and electrical insulation. The resulting PCBs are ideal for high-power electronic devices, ensuring efficient heat dissipation and reliable performance in demanding applications such as LED lighting, power electronics, and automotive systems.
In the field of modern electronics, aluminum nitride printed circuit boards (Aluminum Nitride PCB) play an indispensable role as the backbone of almost all electronic devices. It is critical for engineers and hobbyists to understand the manufacturing process, materials, costs, and key elements of their design of aluminum nitride printed circuit boards. Aluminum nitride PCBs are favored in modern electronic designs due to their excellent thermal conductivity and mechanical strength, making them suitable for high-power electronic devices and high-frequency applications.
What is an aluminum nitride printed circuit board?
Aluminum Nitride Printed Circuit Board (Aluminum Nitride PCB) is one of the indispensable key components in electronic circuits. They carry the functions of various electronic devices and provide necessary mechanical support and electrical connections for electronic components. The manufacturing process of aluminum nitride PCBs involves establishing conductive paths on their surfaces, which are formed by etching or printing. These electrically conductive paths are made of a conductive material, usually copper, that conduct electrical current between electronic components, allowing the circuit to function.
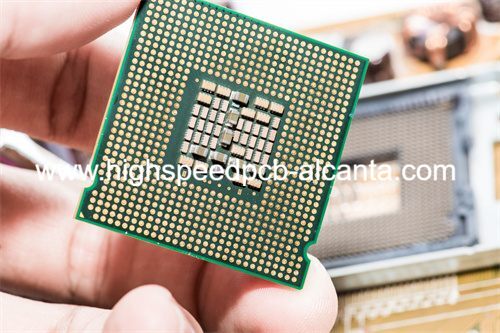
Aluminum Nitride PCB Manufacturing
One of the main functions of these circuit boards is to provide mechanical support between electronic components. On the circuit board, various electronic components (such as capacitors, resistors, integrated circuits, etc.) are installed and connected together to form a complete circuit system. The physical structure of the circuit board holds these components securely together, creating a reliable whole.
In addition to providing mechanical support, aluminum nitride PCBs also play an important role in electrical connections. Conductive paths are laid out on a circuit board to ensure proper connection and communication between electronic components. These paths are typically constructed from conductive materials, such as copper, which have good conductive properties and are able to efficiently carry electrical current and maintain the stability of the circuit.
Overall, aluminum nitride printed circuit boards play an irreplaceable role in modern electronic equipment. They provide the necessary mechanical support and electrical connections for electronic components to build various complex circuit systems. Through precise manufacturing processes and reliable design, aluminum nitride printed circuit boards have become a key component of the modern electronics industry, driving the continuous development and advancement of technology.
How to design aluminum nitride printed circuit boards?
Designing aluminum nitride printed circuit boards is a delicate and complex process that requires engineers to use specialized skills and tools to achieve optimal performance and reliability. The following are the key steps in designing an aluminum nitride printed circuit board:
The first step in design is to capture the schematic of the circuit. Engineers draw the various components, connections, and signal paths in a circuit in circuit design software to establish the circuit’s logical structure and functional relationships. Schematic capture ensures design accuracy and consistency, providing a foundation for subsequent placement and routing.
When performing component placement, engineers will select appropriate electronic components and place them on the surface of the PCB based on the functional requirements and space constraints of the circuit. The position and orientation of components has a significant impact on factors such as circuit performance and EMI (electromagnetic interference), so engineers need to carefully consider where each component is placed.
Wiring is the process of translating the electrical connections between components into a physical layout. Engineers need to consider factors such as signal integrity, electromagnetic compatibility (EMC), and thermal management to optimize routing. By using professional routing tools, engineers can automate routing and optimize signal paths to ensure optimal performance and reliability.
Layout involves determining the location and layout of various components on the PCB. Engineers need to consider board size, shape and location of external connectors, as well as thermal requirements and EMI controls. Through reasonable layout, PCB manufacturability and reliability can be maximized.
Throughout the design process, engineers also need to consider PCB manufacturability. This includes selecting the right materials, reducing process complexity, minimizing production costs, etc. By working closely with manufacturers and utilizing advanced design tools and techniques, engineers can optimize PCB designs to ensure a smooth production process.
In general, designing aluminum nitride printed circuit boards requires engineers to fully understand circuit design principles, use professional design tools, and focus on optimizing functionality, space utilization, and manufacturability throughout the design process. Through careful design and careful work, engineers can achieve high performance, reliability and economical aluminum nitride printed circuit board designs.
What is the aluminum nitride printed circuit board manufacturing process?
The manufacturing process of aluminum nitride printed circuit boards (Aluminum Nitride PCB) is a complex and precise process involving multiple critical steps to ensure the quality and reliability of the final product. These key steps are detailed below:
The first step in manufacturing aluminum nitride printed circuit boards is selecting the appropriate substrate. Aluminum nitride is often chosen as the substrate material due to its excellent thermal conductivity and electrical insulation properties. The quality and characteristics of the substrate are critical to the performance of the final product.
In the lamination stage, the prepared aluminum nitride substrate is stacked with other necessary layer materials (such as copper foil, insulation layer and copper clad layer) according to the design requirements. This step ensures the integrity and reliability of the circuit board.
In the copper pattern making stage, chemical etching or mechanical processing techniques are used to remove unnecessary parts of the copper foil to form the required wire and connection patterns on the circuit board. These copper wires will be used to connect electronic components and transmit electrical signals.
Drilling is the process of punching interconnected holes in a circuit board to create electrical connections between different layers. The precise location and size of the drilled holes is critical to ensuring proper functionality of the board.
Copper plating is the process of covering copper to the walls of a drilled hole in order to create an electrical connection. This ensures connectivity and stability between layers and enhances the board’s conductive properties.
Etching is the process of using chemical solutions to etch away unnecessary copper foil, leaving behind the designed copper pattern. Through etching, precise patterns of wires and connections are retained on the surface of the circuit board, laying the foundation for circuit functionality.
After the above key steps, the aluminum nitride printed circuit board manufacturing process is completed. The final printed circuit board has the characteristics of complete functions and high reliability, and can be used for the assembly and application of various electronic devices. This precise manufacturing process is an indispensable part of the modern electronics industry, providing solid support for technological innovation and development in various fields.
How to make aluminum nitride printed circuit boards?
Manufacturing Aluminum Nitride PCBs is a precise and meticulous process where each stage is critical to the quality and reliability of the final product. The following are the key steps in manufacturing aluminum nitride printed circuit boards:
The first step in manufacturing an aluminum nitride printed circuit board is to translate the design into an actual manufacturable layout. This includes routing according to the circuit schematic, determining the location of components, and taking into account various requirements for manufacturing and assembly.
Selecting the appropriate substrate material is critical to the performance of aluminum nitride printed circuit boards. The substrate is usually made of aluminum nitride ceramic material, which has good thermal conductivity and insulation. At this stage, the substrate will be prepared into the desired size and shape.
A thin layer of copper is chemically or physically deposited on a substrate. This copper layer will be used to form the conductive path for the circuit. The deposited copper layer must be uniform and of moderate thickness to ensure good conductivity and a reliable connection.
Photolithography is used to transfer the circuit pattern in the design to the surface of the copper layer. Through photolithography, photosensitive adhesive is coated on the copper layer, and then the designed pattern is projected onto the photosensitive adhesive, exposed and developed to form a conductive path on the copper layer.
At the final stage of the manufacturing process, printed circuit boards are thoroughly inspected and tested to ensure quality. This includes checking the continuity of conductive paths, the correct placement of components on the board, and any possible defects or damage.
Manufacturing aluminum nitride printed circuit boards requires strict adherence to each step to ensure the product’s quality and performance meet expected levels. Precision and detail at every stage play a key role in the success of the final product. Through careful design and high-standard manufacturing processes, aluminum nitride printed circuit boards can play an important role in a variety of applications, providing critical support for the performance and reliability of modern electronic devices.
How much does an aluminum nitride printed circuit board cost?
The cost of aluminum nitride printed circuit boards is one of the important factors that need to be carefully considered during the manufacturing process. These costs are affected by a variety of factors, chief among them size, complexity, materials, and quantity.
First of all, size is one of the important factors that determine the cost. Larger aluminum nitride PCBs require more materials and production resources, so they tend to be more expensive to manufacture. Conversely, smaller sized boards generally cost less.
Secondly, the complexity of the circuit board also has a significant impact on the cost. Complex circuit layouts, multi-layer designs, and high-density component placement increase the complexity of the manufacturing process, leading to higher costs. Simple designs often reduce manufacturing costs.
Materials are another important cost factor. Different types of substrate materials, conductive layer thickness, and pad solder mask materials will all have an impact on costs. High-performance materials typically add cost but may be necessary in some applications.
Finally, order quantity also affects costs. Typically, high-volume production reduces the cost per board because they make more efficient use of production equipment and resources. In contrast, low-volume production often results in increased unit costs.
Therefore, understanding these cost drivers is critical for budgeting and optimizing production expenses. Engineers and manufacturers need to carefully evaluate each factor and make trade-offs during the design and manufacturing process to ensure that the final aluminum nitride printed circuit board meets budget requirements and maintains good performance and quality.
What materials are aluminum nitride printed circuit boards made of?
Aluminum Nitride Printed Circuit Board (Aluminum Nitride PCB) is an increasingly popular high-performance circuit board in the electronics field. Its material selection is crucial and directly affects its performance, stability and applicable scenarios. Let’s take a closer look at the material composition of aluminum nitride printed circuit boards.
The substrate material of aluminum nitride printed circuit boards is one of its most important components. Traditional FR-4 fiberglass reinforced epoxy resin is one of the commonly used substrate materials. It has good insulation properties and mechanical strength and is suitable for most electronic applications. However, as the performance and heat dissipation requirements of electronic products continue to increase, aluminum nitride has become a favored substrate material. Aluminum nitride substrate has excellent thermal conductivity and stability, can effectively dissipate heat, and is suitable for high power density and high frequency applications, such as LED lighting, power amplifiers, etc.
On aluminum nitride printed circuit boards, the conductive layer usually consists of conductive copper wires. Conductive copper wires are arranged on the surface of the substrate to form paths for circuit connections and signal transmission. The design and layout of these conductive copper wires is critical to circuit performance, and factors such as signal transmission speed and electromagnetic compatibility need to be considered to ensure the stability and reliability of the circuit.
Solder mask is a layer of covering material used to protect circuit board pads, usually a solder mask ink. The pad solder resist plays a role in protecting the pad and preventing short circuits during the welding process. It can also improve the welding quality and reliability. For aluminum nitride printed circuit boards, it is critical to select the appropriate pad solder mask material to ensure soldering quality and long-term stability.
In addition to traditional substrate materials and conductive layers, aluminum nitride printed circuit boards can also use some advanced materials to meet specific design requirements. For example, flexible substrates can bend and bend circuits, making them suitable for applications with special shapes and limited space. Metal matrix composite panels have excellent thermal conductivity and mechanical strength and are suitable for applications with high heat dissipation requirements, such as automotive electronics, aerospace and other fields.
In summary, material selection for aluminum nitride printed circuit boards is critical to circuit performance and stability. Reasonable selection of substrate materials, conductive layers and pad solder mask materials, as well as the application of advanced materials, can provide more possibilities and flexibility for the design and manufacturing of electronic products to meet the needs of different application scenarios.
Who makes aluminum nitride printed circuit boards?
The manufacturing of aluminum nitride printed circuit boards is a complex and critical process that requires experienced manufacturers to ensure product quality and performance. In this field, choosing a reliable supplier is crucial, and our company is committed to being your partner of choice.
As a manufacturer of aluminum nitride printed circuit boards, we have advanced equipment and technology to meet various customer needs. Our manufacturing processes are carefully designed to ensure the highest standards at every stage. From raw material procurement to final product testing, we always put quality first.
Our team consists of experienced engineers and technicians with extensive industry knowledge and expertise. No matter what specific design or requirements your project requires, we are able to provide a custom solution to meet your needs.
Reliability and trustworthiness are critical considerations when selecting an aluminum nitride printed circuit board supplier. We are known for our excellent customer service and efficient delivery capabilities, always ensuring customer satisfaction. We are not only committed to providing customers with high-quality products, but also to establishing long-term and stable cooperative relationships.
Not only that, our company continuously invests in R&D and innovation to ensure that our manufacturing processes remain at the forefront of the industry. We constantly explore new materials and technologies to improve product performance and reliability.
No matter the size of your project, we are willing to work with you to provide you with the best aluminum nitride printed circuit board solution. By choosing us as your supplier, you can rest assured knowing that you will be supported by the highest quality products and services.
We are your reliable partner in the manufacturing of aluminum nitride printed circuit boards. We look forward to working with you to achieve success together!
What are the five qualities of great customer service?
In the modern business environment, providing excellent customer service is an integral part of business. Understanding and practicing the following five key traits can help businesses build great customer relationships, increase customer satisfaction, and drive business growth.
Responding promptly and effectively to customer inquiries and concerns is at the core of excellent customer service. No matter what question or issue a customer presents, it is crucial to respond quickly and provide a helpful solution. By responding quickly, companies demonstrate respect and value for their customers, enhancing their trust and loyalty.
Understanding and addressing your customers’ needs with compassion and understanding is the key to building great customer relationships. Actively listening to customer feedback and complaints and trying to understand the reasons behind their pain points and needs can help companies better meet customer expectations and build long-term relationships.
Consistently delivering on promises and commitments made to customers is the basis for building trust and loyalty. Customers expect businesses to deliver products or services on time and provide support and assistance when needed. By consistently delivering high-quality products and services, businesses can earn the trust of their customers and build a strong reputation.
Clear and transparent communication throughout the service process is key to ensuring smooth communication and understanding. Providing important information to customers in a timely manner, such as order status, delivery times, and product updates, can reduce misunderstandings and dissatisfaction, enhance customer trust in the company, and increase customer satisfaction.
Proactive problem solving and striving to achieve customer satisfaction are important components of great customer service. When customers encounter difficulties or problems, companies should act quickly to find solutions and ensure that the problem is resolved in a timely manner. Through proactive problem solving, businesses can increase customer satisfaction and earn their customers’ respect and trust.
To summarize, responsiveness, empathy, reliability, communication, and problem-solving skills are key attributes that build great customer service. By actively practicing these traits, businesses can enhance customer relationships, improve customer satisfaction, and succeed in a competitive marketplace.
Frequently Asked Questions
How can I optimize the thermal performance of Aluminum Nitride PCBs?
To optimize the thermal performance of Aluminum Nitride PCBs, several design strategies can be employed. These include increasing the thickness of the Aluminum Nitride substrate to enhance thermal conductivity, incorporating thermal vias to improve heat dissipation, and optimizing component placement to minimize thermal resistance. Additionally, utilizing advanced thermal management techniques such as metal-core PCBs or active cooling systems can further enhance thermal performance in demanding applications.
Are there any environmental considerations associated with Aluminum Nitride PCB manufacturing?
While Aluminum Nitride PCB manufacturing generally adheres to environmental regulations and standards, certain aspects of the process may pose environmental challenges. For example, the deposition and etching of metals during PCB fabrication may generate hazardous waste materials that require proper handling and disposal. Additionally, the use of specialized materials and chemicals in the manufacturing process may raise concerns regarding resource depletion and pollution. Implementing sustainable practices, such as recycling waste materials and reducing chemical usage, can mitigate the environmental impact of Aluminum Nitride PCB manufacturing.
What are the benefits of using Aluminum Nitride PCBs?
Aluminum Nitride PCBs offer several advantages, including high thermal conductivity, excellent electrical insulation properties, and compatibility with high-frequency applications. These properties make them ideal for use in power electronics, RF/microwave circuits, and LED lighting systems where efficient heat dissipation and signal integrity are crucial.
What is the typical thickness of Aluminum Nitride PCBs?
The typical thickness of Aluminum Nitride PCBs ranges from 0.5mm to 3.0mm, depending on the specific application requirements and manufacturing capabilities of the PCB fabrication facility.
Can Aluminum Nitride PCBs be used in high-power applications?
Yes, Aluminum Nitride PCBs are suitable for high-power applications due to their high thermal conductivity, which enables efficient heat dissipation and thermal management. They are commonly used in power supplies, motor control systems, and automotive electronics.