Aluminum Nitride Ceramic PCB Manufacturing.Aluminum Nitride Ceramic PCB Manufacturing involves creating printed circuit boards (PCBs) using aluminum nitride as the substrate material. This process leverages the excellent thermal conductivity and electrical insulation properties of aluminum nitride, making it ideal for high-power and high-frequency applications. The manufacturing steps include substrate preparation, circuit patterning, and component assembly, ensuring robust performance in demanding electronic environments such as aerospace, automotive, and telecommunications.
In the field of electronics, aluminum nitride ceramic PCBs stand out for their engineering excellence. These special boards, made of advanced materials, play a vital role in high-performance electronic devices. However, for many, the process by which they are made remains shrouded in mystery. In this comprehensive guide, we’ll delve into the world of aluminum nitride ceramic PCB manufacturing, revealing its subtleties and importance.
What is Aluminum Nitride Ceramic PCB?
Aluminum nitride ceramic PCB, the full name of aluminum nitride ceramic printed circuit board, is a special and powerful electronic component. It is manufactured using aluminum nitride ceramic material, which makes its performance far beyond the traditional A printed circuit board.
First, aluminum nitride ceramic PCBs are known for their excellent thermal conductivity. Thermal conductivity refers to a material’s ability to conduct heat, and aluminum nitride ceramics excel in this area. For high-power electronic equipment, heat dissipation is crucial. The high thermal conductivity of aluminum nitride ceramic PCB can effectively transfer heat from the electronic device to the external environment, ensuring the stable operation of the equipment.
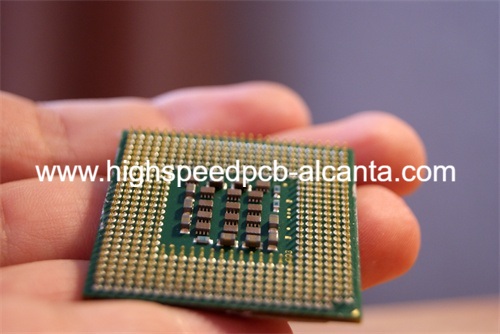
Aluminum Nitride Ceramic PCB Manufacturing
Secondly, aluminum nitride ceramic PCBs have excellent mechanical strength. Compared with traditional substrate materials such as FR-4, aluminum nitride ceramics are stronger and more durable. This allows it to maintain stable performance in various harsh environments and is not susceptible to external shock or vibration, thus improving the reliability and service life of the equipment.
Finally, aluminum nitride ceramic PCBs are preferred for their superior reliability. For applications that require high-frequency performance, such as wireless communications, RF and microwave equipment, stable and reliable circuit boards are critical. The material properties and manufacturing process of aluminum nitride ceramic PCB ensure its excellent performance in high-frequency environments, enabling precise signal transmission and stable working conditions.
Overall, aluminum nitride ceramic PCBs have become the electronic component of choice for many high-power and high-frequency applications due to their excellent thermal conductivity, mechanical strength, and reliability. It can not only improve the performance and stability of the equipment, but also meet various harsh working environment requirements, providing strong support for the development of modern electronic technology.
How to design aluminum nitride ceramic PCB?
Designing aluminum nitride ceramic PCB requires a meticulous planning and design process. This process not only requires the professional skills of engineers, but also requires the use of professional software. First, engineers start by creating circuit diagrams starting from the customer’s needs and technical specifications. This step is critical in the design process as it determines the overall layout and connections of the PCB. Through circuit diagrams, engineers can clarify the connection relationships between various components and their locations on the PCB board.
Next, engineers will place various electronic components on the PCB board according to the circuit diagram. When placing components, they need to consider the spatial relationships between components, signal transmission paths, and heat dissipation. To maximize PCB performance, engineers precisely calculate the position of each component to ensure it interacts effectively with other components.
Another key aspect of designing an aluminum nitride ceramic PCB is designing an optimized trace pattern. Traces are the wires connecting electronic components, and their quality and layout directly affect the performance and stability of the PCB. Engineers will use professional software to draw traces to ensure that their length, width and layout meet design requirements. Especially in high-power and high-frequency applications, the design of traces is particularly important as they need to be able to efficiently transmit signals and dissipate heat to avoid overheating and signal interference.
In addition, engineers will use professional software for simulation and verification to ensure that the designed PCB meets performance and reliability requirements. They will simulate PCB performance under different working conditions, analyze and optimize it. Through these simulation efforts, engineers can identify potential problems early and make adjustments and improvements before actual manufacturing.
To sum up, designing aluminum nitride ceramic PCB is a complex and precise task that requires engineers to give full play to their professional skills and experience. By using professional software for circuit diagram design, component placement and trace optimization, engineers can design aluminum nitride ceramic PCBs with excellent performance, stability and reliability to meet the needs of different application fields.
What is the manufacturing process of aluminum nitride ceramic PCB?
The manufacturing process of aluminum nitride ceramic PCB is a highly sophisticated and complex process that requires multiple precise steps. These steps will be described in detail below to show the overall picture of aluminum nitride ceramic PCB manufacturing.
The first step in manufacturing an aluminum nitride ceramic PCB is substrate preparation. At this stage, the aluminum nitride ceramic substrate is carefully inspected and cleaned to ensure that the surface is free of any impurities or dirt. This step is crucial to ensure the smooth progress of subsequent processing.
Next, the designed PCB pattern will be transferred to the prepared substrate. This process is typically accomplished using photolithography techniques, in which a light-sensitive coating is applied to the substrate surface and a mask lithography machine is used to project a design pattern onto the coating.
Once the pattern has been successfully transferred to the substrate, the next steps involve drilling holes. Laser drilling technology is widely used in the manufacturing of aluminum nitride ceramic PCBs as it can provide high precision and efficiency. These drilled holes will be used to mount electronic components and connect traces.
After drilling is completed, the next step is to metallize the surface of the substrate. This means coating the surface of the drilled hole with a layer of metal, usually copper or gold, to create a conductive layer and connection points. The metallization process typically involves coating a substrate surface with a layer of conductive material and then depositing the metal in the desired areas through chemical or electroplating methods.
After the metallization is complete, the next step is to paint the art. This stage involves printing the required patterns and markings onto the surface of the substrate for subsequent assembly and testing. These patterns typically include component locations, connection points, and identification.
Finally, after the artistic painting is complete, the substrate undergoes a series of surface treatment steps to enhance its mechanical strength and durability. This may include applying a protective surface coating or covering to protect the substrate from environmental factors.
Through these precise steps, the aluminum nitride ceramic PCB manufacturing process is completed. Each stage requires the support of advanced machinery and professional technology to ensure the integrity and quality of the final product. These PCBs play a vital role in high power and high frequency applications due to their superior performance and reliability.
How much does an aluminum nitride ceramic PCB cost?
The cost of aluminum nitride ceramic PCBs is a key factor to consider. The price of these PCBs depends on several factors, including the board’s size, complexity, and manufacturing quantity. First, the size of the board directly affects the amount of material required and the cost of processing. Larger boards generally require more material and may require more processing steps, so the cost will be relatively higher. At the same time, the complexity of the board is also one of the important factors that determine the cost. Complex designs may require more process steps and precision machining, which increases manufacturing costs. For example, if the board needs to have high-density traces, fine apertures, or complex structures, the manufacturing cost will increase accordingly.
In addition, manufacturing quantity will also affect the cost of aluminum nitride ceramic PCB. Typically, high-volume production allows economies of scale to be achieved, resulting in lower unit costs. On the contrary, small batch production may require more manpower and resource investment, so the cost will be relatively high. Therefore, for applications that require mass production, costs can be effectively reduced through bulk orders.
Although aluminum nitride ceramic PCBs may cost slightly more than traditional alternatives, their superior performance and reliability fully justify this cost. For many high-power and high-frequency applications, the advantages of aluminum nitride ceramic PCBs are irreplaceable. Its excellent thermal conductivity and mechanical strength can effectively solve heat dissipation and mechanical stress problems, thereby improving system performance and reliability. So while the cost of aluminum nitride ceramic PCBs may be higher, the advantages in long-term use and performance requirements often offset this cost difference.
What materials are used in aluminum nitride ceramic PCBs?
The material selection of aluminum nitride ceramic PCB (Aluminum Nitride Ceramic PCB) is crucial and directly affects its performance and reliability. This particular type of printed circuit board consists primarily of an aluminum nitride ceramic substrate and conductive traces, which are typically made from metallic materials such as copper or gold.
First, let’s look at aluminum nitride ceramic substrates. Aluminum nitride ceramics are advanced materials with excellent thermal conductivity and mechanical strength. Compared with traditional substrate materials, such as FR-4 (fiberglass reinforced epoxy resin), aluminum nitride ceramics have higher thermal conductivity, allowing them to effectively conduct and dissipate heat, thereby maintaining the stable operation of electronic components. temperature. In addition, aluminum nitride ceramics also have good dimensional stability and resistance to chemical corrosion, making them suitable for applications that require long-term stable operation in harsh environments.
Secondly, conductive traces play an important role in connecting electronic components in aluminum nitride ceramic PCBs. Typically, conductive traces are made of highly conductive metals such as copper or gold. Copper is a common choice because it conducts electricity well, is moderately cost-effective, and is relatively easy to process. For some high-end applications, such as radio frequency (RF) circuits or high-frequency circuits, gold conductive traces may be more suitable because gold has lower resistance and better high-frequency performance, which can reduce signal attenuation and loss.
When selecting these materials, engineers focus not only on their electrical properties, but also on their reliability and stability in harsh environments. Therefore, aluminum nitride ceramic PCB can work stably under extreme conditions such as high temperature, high frequency and high pressure, ensuring the long-term reliability and performance of electronic equipment.
To summarize, the material selection for aluminum nitride ceramic PCBs is carefully considered to achieve optimal thermal conductivity, electrical performance, and reliability. The combination of an aluminum nitride ceramic substrate and copper or gold conductive traces has made this PCB the first choice for many high-performance applications, driving the development and advancement of modern electronics technology.
Who is making aluminum nitride ceramic PCBs?
In the process of manufacturing aluminum nitride ceramic PCBs, supplier selection is crucial. As a professional PCB manufacturing company, we understand the importance of the supply chain, so we control the production of aluminum nitride ceramic PCBs internally to ensure product quality and reliability.
Our company has advanced production equipment and technical teams that can precisely control the quality and precision of each manufacturing step. From the procurement of raw materials to the delivery of finished products, we strictly follow the ISO quality management system to ensure that each PCB board meets the highest standards.
Our supplier is our own factory, we can not only manage production schedule and quality control independently, but also be able to flexibly meet customers’ customized needs. Whether it is a small batch order or large-scale production, we are able to deliver high-quality aluminum nitride ceramic PCBs in a timely manner to meet our customers’ needs.
In addition, our company also has an experienced technical team that can provide customers with professional technical support and solutions. Whether it’s design consultation or production advice, we are able to provide our customers with timely and accurate services to ensure their projects go smoothly.
Overall, our company, as a manufacturer and supplier of aluminum nitride ceramic PCB, is committed to providing customers with high quality, reliability and customized solutions. We will continue to work hard to continuously improve our technical level and service quality to create greater value for our customers.
What are 5 qualities of a good customer service?
In the aluminum nitride ceramic PCB manufacturing industry, providing excellent customer service is crucial. Here are five key qualities of good customer service:
First and foremost, responding promptly to customer inquiries and questions is key. Whether it’s about order status, technical details, or other issues, timely communication builds customer trust and ensures customer satisfaction.
Secondly, having deep knowledge and expertise is equally crucial. Throughout the manufacturing process, customers may have various technical questions or require professional advice. Therefore, providing support with in-depth knowledge and expertise to effectively address customer concerns and provide insightful guidance.
Third, empathy and understanding of customer needs and challenges are key service qualities. Understanding your customers’ needs and empathizing with the challenges they face helps develop customized solutions to meet your customers’ specific needs.
Fourth, flexibility is one of the necessary conditions for providing excellent customer service. As the market and customer needs continue to change, flexibly adjusting the manufacturing process and service solutions can better meet customer needs and provide customized solutions.
Ultimately, transparent and honest communication is key to ensuring customer satisfaction. Providing timely information about delivery times, pricing, and technical capabilities, as well as communicating honestly about issues and challenges you may encounter, can help build strong, long-term customer relationships.
In the aluminum nitride ceramic PCB manufacturing industry, through the above key characteristics, good customer relationships can be established, customer satisfaction can be improved, and thus the development and growth of the enterprise can be promoted.
FAQS
Can Aluminum Nitride Ceramic PCBs be used in high-power applications?
Yes, Aluminum Nitride Ceramic PCBs are well-suited for high-power applications due to their exceptional thermal conductivity and mechanical strength. In high-power electronic systems where efficient heat dissipation is critical, Aluminum Nitride Ceramic PCBs excel, allowing for the effective management of heat generated by power components. Additionally, Aluminum Nitride Ceramic PCBs offer excellent electrical insulation properties, making them suitable for high-voltage applications where insulation reliability is essential. Whether used in power amplifiers, RF transmitters, or power converters, Aluminum Nitride Ceramic PCBs provide the reliability and performance needed for demanding high-power applications.
What advantages do Aluminum Nitride Ceramic PCBs offer over traditional PCB materials?
Aluminum Nitride Ceramic PCBs offer several distinct advantages over traditional PCB materials. Firstly, they boast exceptional thermal conductivity, allowing for efficient dissipation of heat generated by electronic components. This thermal management capability makes them ideal for applications requiring high-power operation or operating in harsh environmental conditions where temperature control is critical.
What are the key advantages of using Aluminum Nitride Ceramic PCBs over traditional PCB materials?
Aluminum Nitride Ceramic PCBs offer several distinct advantages over traditional materials. Firstly, their exceptional thermal conductivity allows for efficient heat dissipation, making them ideal for high-power applications where heat management is critical. Secondly, aluminum nitride ceramic boasts excellent mechanical strength and reliability, ensuring durability in demanding environments. Additionally, these PCBs exhibit superior electrical insulation properties, reducing the risk of short circuits and enhancing overall performance. Overall, Aluminum Nitride Ceramic PCBs provide unmatched performance and reliability compared to conventional alternatives.
Is the manufacturing process of Aluminum Nitride Ceramic PCBs environmentally friendly?
While Aluminum Nitride Ceramic PCB manufacturing involves advanced processes, many manufacturers prioritize environmental sustainability. By implementing measures such as waste reduction, recycling programs, and adopting eco-friendly materials and practices, manufacturers strive to minimize their environmental footprint. Additionally, some companies invest in renewable energy sources to power their manufacturing facilities, further reducing their carbon emissions. While challenges remain, the industry is committed to advancing environmentally conscious practices to mitigate its impact on the environment.