Alumina substrate Manufacturer.As a leading Alumina substrate manufacturer, we specialize in producing high-quality, durable substrates that excel in thermal conductivity and electrical insulation. Our state-of-the-art manufacturing processes ensure precision and reliability, making our Alumina substrates ideal for various high-performance electronic applications. Partner with us for innovative solutions and exceptional service in the world of advanced ceramics.
Alumina substrates are widely used in the electronics industry due to their excellent thermal, electrical, and mechanical properties. These substrates are made from aluminum oxide (Al2O3), a ceramic material known for its high thermal conductivity, electrical insulation, and resistance to wear and corrosion. Alumina substrates are used in a variety of applications, including semiconductor packaging, microwave circuits, and LED lighting.
What is an Alumina Substrate?
An alumina substrate is a ceramic base material used in the fabrication of electronic circuits and components. Alumina, or aluminum oxide (Al2O3), is a white, crystalline material that offers a unique combination of properties, making it ideal for high-performance electronic applications. These substrates are typically manufactured through a sintering process, where alumina powder is compacted and heated to form a dense, rigid structure.
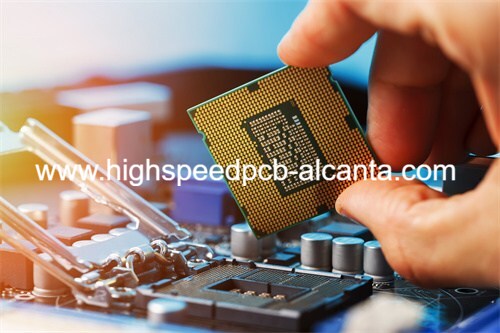
Alumina substrate Manufacturer
Alumina substrates are valued for their high thermal conductivity, excellent electrical insulation, and mechanical strength. These properties make them suitable for use in environments where high temperatures and electrical isolation are critical. Additionally, alumina substrates are resistant to chemical and physical wear, ensuring long-term reliability and performance.
Alumina Substrate Design Reference Guide
Designing alumina substrates involves careful consideration of material properties, manufacturing processes, and application requirements. The following sections provide an overview of the key aspects involved in the design and application of alumina substrates.
The properties of alumina substrates make them highly desirable for a range of electronic applications. Key material properties include:
Thermal Conductivity: Alumina substrates offer high thermal conductivity, which allows for efficient heat dissipation in electronic devices. This property is crucial for preventing overheating and ensuring the reliability of high-power components.
Electrical Insulation: Alumina is an excellent electrical insulator, providing high dielectric strength and resistance to electrical breakdown. This makes it ideal for isolating electrical circuits and preventing short circuits.
Mechanical Strength: Alumina substrates exhibit high mechanical strength and hardness, making them resistant to mechanical wear and damage. This ensures durability and longevity in demanding applications.
Chemical Resistance: Alumina is chemically inert and resistant to corrosion and oxidation, allowing it to maintain its properties in harsh environments.
Dimensional Stability: Alumina substrates offer excellent dimensional stability, maintaining their shape and size under varying thermal and mechanical conditions.
What Materials are Used in Alumina Substrates?
Alumina substrates are primarily composed of high-purity aluminum oxide (Al2O3). However, the specific composition and additives may vary depending on the application and desired properties. Key materials used in alumina substrates include:
High-Purity Alumina: The base material for alumina substrates is high-purity aluminum oxide. The purity level of the alumina affects its thermal, electrical, and mechanical properties.
Additives: Additives such as magnesium oxide (MgO) or zirconium oxide (ZrO2) may be incorporated to enhance specific properties such as sinterability, mechanical strength, or thermal stability.
Metallization Materials: Conductive materials such as gold, silver, or copper are used for metallization. The choice of metallization material depends on factors such as electrical performance, thermal conductivity, and compatibility with the substrate.
What Size are Alumina Substrates?
The size of alumina substrates varies depending on the application and specific design requirements:
Thickness: Alumina substrates typically have thicknesses ranging from a few hundred micrometers to several millimeters. The thickness is chosen based on factors such as mechanical strength, thermal management, and electrical insulation requirements.
Dimensions: The length and width of the substrates are determined by the size of the electronic components and the layout of the system. Substrates can be manufactured in various shapes and sizes to accommodate different applications, from small chips to large circuit boards.
The Manufacturing Process of Alumina Substrates
The manufacturing process of alumina substrates involves several precise and controlled steps to ensure high quality and performance:
High-purity alumina powder is prepared and treated to ensure uniform particle size and distribution. Additives may be incorporated to enhance specific properties.
The alumina powder is formed into the desired shape using methods such as tape casting, dry pressing, or extrusion. This step creates a green body, which is a compacted but unsintered substrate.
The green body is subjected to high temperatures in a sintering furnace. During sintering, the powder particles bond together to form a dense, rigid structure. This process enhances the mechanical strength and thermal conductivity of the substrate.
After sintering, the substrates are machined to achieve precise dimensions and surface finishes. Techniques such as grinding, lapping, and polishing are used to obtain the desired surface quality and flatness.
Metallization involves applying a conductive layer to the substrate surface to create electrical circuits. Common methods include screen printing, sputtering, and electroplating. The choice of metallization technique depends on the application and performance requirements.
The Application Area of Alumina Substrates
Alumina substrates are used in a wide range of high-performance applications:
In semiconductor packaging, alumina substrates provide excellent thermal management and electrical insulation, ensuring the reliability and performance of integrated circuits (ICs).
In microwave circuits, alumina substrates offer low dielectric loss and high thermal conductivity, making them ideal for high-frequency applications such as radar and communication systems.
In LED lighting, alumina substrates provide efficient heat dissipation, enhancing the performance and lifespan of LEDs.
In power electronics, alumina substrates are used in power modules and other high-power components, providing robust thermal management and electrical insulation.
In automotive electronics, alumina substrates are used in sensors, control units, and other electronic systems, offering reliability and performance in harsh environments.
What are the Advantages of Alumina Substrates?
Alumina substrates offer several advantages that make them indispensable in high-performance applications:
High Thermal Conductivity: Alumina substrates provide efficient heat dissipation, preventing overheating and ensuring the reliability of high-power components.
Excellent Electrical Insulation: Alumina substrates offer high dielectric strength and resistance to electrical breakdown, ensuring electrical isolation and preventing short circuits.
Mechanical Strength: Alumina substrates exhibit high mechanical strength and hardness, making them resistant to mechanical wear and damage.
Chemical Resistance: Alumina is chemically inert and resistant to corrosion and oxidation, allowing it to maintain its properties in harsh environments.
Dimensional Stability: Alumina substrates offer excellent dimensional stability, maintaining their shape and size under varying thermal and mechanical conditions.
FAQ
What are the key considerations in designing an alumina substrate?
Key considerations include thermal management, electrical performance, mechanical integrity, and long-term reliability. The design should incorporate features such as heat sinks, thermal vias, and appropriate metallization techniques to ensure optimal performance.
How do alumina substrates differ from other ceramic substrates?
Alumina substrates offer a unique combination of high thermal conductivity, excellent electrical insulation, mechanical strength, and chemical resistance. These properties make them suitable for high-performance applications where other ceramic substrates may not provide the same level of performance.
What is the typical manufacturing process for alumina substrates?
The process involves powder preparation, forming, sintering, machining and finishing, and metallization. Each step is carefully controlled to ensure high quality and performance.
What are the main applications of alumina substrates?
Alumina substrates are used in semiconductor packaging, microwave circuits, LED lighting, power electronics, and automotive electronics, providing advanced functionality and reliability in demanding environments.