AlN Substrate Manufacturer.An AlN substrate manufacturer specializes in producing aluminum nitride (AlN) substrates, which are critical for high-performance electronic applications. AlN substrates are known for their excellent thermal conductivity, electrical insulation properties, and mechanical strength. These characteristics make them ideal for use in power electronics, RF devices, and high-temperature applications. The manufacturing process involves precise control of material purity and substrate fabrication to ensure high quality and reliability. AlN substrates enable efficient heat dissipation and robust performance, making them a preferred choice in advanced electronic systems.
Aluminum Nitride (AlN) substrates are increasingly becoming the material of choice in various high-performance electronic applications. Known for their exceptional thermal conductivity and electrical insulating properties, AlN substrates are essential in industries that demand high thermal management and reliability. This article explores the concept, structure, materials, manufacturing process, applications, and advantages of AlN substrates.
What is an AlN Substrate?
An AlN substrate is a ceramic material primarily composed of aluminum nitride. AlN substrates are known for their excellent thermal conductivity, high electrical insulation, and robust mechanical properties. These characteristics make them ideal for applications in high-power electronics, LED lighting, and RF (Radio Frequency) components.
AlN substrates serve as the foundation for electronic circuits, providing both mechanical support and efficient thermal dissipation. As electronic devices continue to shrink in size while increasing in power density, the role of AlN substrates in maintaining performance and reliability becomes even more critical.
Structure of AlN Substrates
The structure of AlN substrates is designed to optimize their thermal and electrical properties. Key structural elements include:
The primary component of an AlN substrate is aluminum nitride, a ceramic material that combines high thermal conductivity with excellent electrical insulation. The purity and density of the AlN material significantly impact its performance.
AlN substrates often feature metallized surface layers that enable the mounting and interconnection of electronic components. These surface layers are typically made of metals like copper, gold, or silver, which provide excellent electrical conductivity and solderability.
Vias (vertical interconnect access) may be incorporated into AlN substrates to create electrical connections between different layers of a multilayer circuit. These vias are filled with conductive materials to ensure reliable electrical pathways.
To enhance durability and performance, AlN substrates can be coated with protective layers that guard against oxidation, moisture, and other environmental factors.
The microstructure of the AlN material, including grain size and orientation, plays a crucial role in determining its thermal and mechanical properties. Advanced manufacturing techniques are employed to control the microstructure and achieve the desired performance characteristics.
Materials Used in AlN Substrates
The materials used in the fabrication of AlN substrates are chosen for their ability to withstand high temperatures, provide electrical insulation, and support efficient thermal management. Key materials include:
The primary material, aluminum nitride, is valued for its high thermal conductivity (ranging from 170 to 320 W/m·K) and excellent electrical insulation. The quality of the AlN material, including its purity and density, directly impacts the performance of the substrate.
Metals such as copper, gold, and silver are used to create the conductive pathways on the surface of the AlN substrate. These metals offer high electrical conductivity and good solderability, making them ideal for electronic applications.
To enhance electrical insulation, dielectric coatings made of materials like silicon dioxide (SiO2) or silicon nitride (Si3N4) can be applied to the surface of the AlN substrate. These coatings help prevent electrical leakage and improve reliability.
Protective coatings, such as silicon carbide (SiC) or aluminum oxide (Al2O3), are used to shield the AlN substrate from environmental factors like moisture, oxidation, and mechanical wear. These coatings enhance the durability and longevity of the substrate.
The Manufacturing Process of AlN Substrates
The manufacturing process of AlN substrates involves several precise and controlled steps to ensure high quality and performance. Key steps include:
The process begins with the preparation of high-purity aluminum nitride powder. This powder is carefully controlled to ensure the desired particle size and distribution, which are critical for achieving the final properties of the substrate.
The AlN powder is formed into the desired shape using techniques such as tape casting, extrusion, or pressing. These methods allow for the creation of both simple and complex geometries, depending on the application requirements.
The formed AlN components are subjected to high-temperature sintering to densify the material and achieve the desired mechanical and thermal properties. Sintering typically occurs at temperatures above 1700°C in a nitrogen atmosphere to prevent oxidation.
After sintering, metallization layers are applied to the surface of the AlN substrate. This step involves depositing metal films, such as copper, gold, or silver, onto the substrate using techniques like sputtering, evaporation, or electroplating. The metallization layers form the conductive pathways necessary for electronic applications.
The metallized substrate undergoes patterning to create the desired circuit layout. Photolithography and etching techniques are commonly used to define the circuit patterns with high precision.
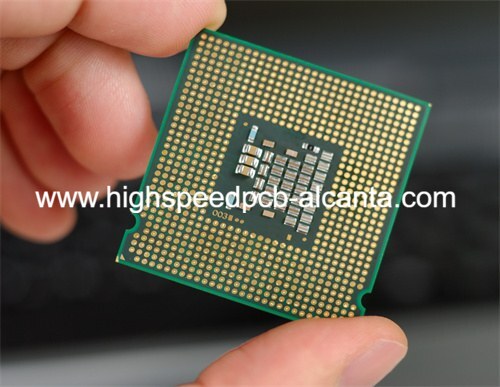
AlN Substrate Manufacturer
Vias are drilled into the substrate to create vertical electrical connections between different layers. These vias are then filled with conductive materials to establish reliable electrical pathways.
The final substrates undergo rigorous inspection and testing to ensure they meet all performance and reliability standards. Electrical testing, visual inspection, and automated optical inspection (AOI) are used to identify any defects or irregularities.
Application Areas of AlN Substrates
AlN substrates are used in a wide range of electronic applications across various industries. Key application areas include:
AlN substrates are ideal for high-power electronic devices, such as power transistors, diodes, and thyristors. Their excellent thermal conductivity ensures efficient heat dissipation, preventing overheating and improving device performance.
In the LED industry, AlN substrates are used as the base material for high-brightness LEDs. The high thermal conductivity of AlN helps manage the heat generated by LEDs, enhancing their efficiency and lifespan.
AlN substrates are commonly used in RF (Radio Frequency) components, such as amplifiers, filters, and resonators. The combination of high thermal conductivity and electrical insulation makes AlN an ideal material for high-frequency applications.
In the automotive industry, AlN substrates are used in power control units, sensors, and other electronic components that require high thermal management and reliability. The robust mechanical properties of AlN ensure durability in harsh automotive environments.
AlN substrates are used in telecommunications equipment, such as base stations, antennas, and transceivers. The high thermal conductivity and electrical insulation properties of AlN help maintain the performance and reliability of these devices under demanding conditions.
Advantages of AlN Substrates
AlN substrates offer several advantages that make them indispensable for modern electronic applications. These advantages include:
AlN substrates provide excellent thermal conductivity, ranging from 170 to 320 W/m·K. This property ensures efficient heat dissipation, preventing overheating and improving the performance and reliability of electronic devices.
AlN substrates offer high electrical insulation, making them ideal for applications that require both high thermal management and electrical isolation. This property helps prevent electrical leakage and enhances the reliability of electronic circuits.
The robust mechanical properties of AlN substrates ensure durability and reliability in demanding applications. AlN substrates can withstand high temperatures, mechanical stress, and environmental factors, making them suitable for a wide range of industries.
AlN substrates are chemically stable and resistant to oxidation, moisture, and other environmental factors. This property enhances the longevity and reliability of the substrate in various applications.
AlN substrates enable the miniaturization of electronic devices by providing high thermal and electrical performance in a compact form factor. This property supports the development of smaller and more powerful electronic components.
FAQ
What materials are commonly used in the metallization of AlN substrates?
Common materials used in the metallization of AlN substrates include copper, gold, and silver. These metals offer high electrical conductivity and good solderability, making them ideal for creating conductive pathways on the substrate surface.
How do AlN substrates improve thermal management in electronic devices?
AlN substrates improve thermal management by providing high thermal conductivity, which ensures efficient heat dissipation. This property prevents overheating and improves the performance and reliability of electronic devices, especially in high-power and high-frequency applications.
Can AlN substrates be used in automotive electronics?
Yes, AlN substrates are highly suitable for automotive electronics. They are used in power control units, sensors, and other electronic components that require high thermal management and reliability. The robust mechanical properties of AlN ensure durability in harsh automotive environments.
What are the key advantages of using AlN substrates in LED lighting?
The key advantages of using AlN substrates in LED lighting include high thermal conductivity, which ensures efficient heat dissipation, enhancing the efficiency and lifespan of LEDs. Additionally, the excellent electrical insulation and chemical stability of AlN substrates contribute to the reliability and performance of LED lighting systems.