Ajinomoto GZ41R2H Package Substrate Manufacturer.A leading ceramics substrate manufacturer, renowned for precision and innovation in material engineering, specializes in crafting high-performance substrates for diverse industries. With state-of-the-art facilities and a dedicated team of experts, they meticulously design and produce substrates tailored to exact specifications, ensuring superior thermal conductivity, mechanical strength, and electrical insulation. Their commitment to quality extends from rigorous quality control measures to continuous research, driving advancements in ceramic technology. Trusted by global clients, they provide reliable solutions for critical applications, establishing themselves as pioneers in the field of ceramic substrate manufacturing.
With the continuous development of electronic equipment, Ajinomoto GZ41R2H packaging substrate has become a key technical solution in the electronics industry with its excellent performance and reliability. As a core component that connects and supports electronic components, it plays an important role in promoting the realization of circuit functions. With the widespread use of electronic products such as smartphones, tablets, and electric vehicles, the demand and importance of Ajinomoto GZ41R2H packaging substrates are increasing.
What is Ajinomoto GZ41R2H package substrate?
The Ajinomoto GZ41R2H package substrate is a vital part of today’s electronic devices, playing a key role in connecting and supporting electronic components. As a basic structure, it provides a stable platform for various circuits, allowing electronic devices to function properly. Specifically, the Ajinomoto GZ41R2H package substrate realizes the function of the circuit by mounting electronic components (such as capacitors, resistors, integrated circuits, etc.) on its surface and connecting these components through wires. These wires are usually made of materials with excellent electrical conductivity properties (such as copper) to ensure good electrical signal transmission and connection stability.
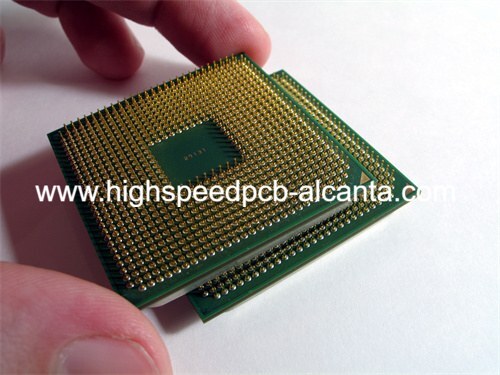
Ajinomoto GZ41R2H Package Substrate Manufacturer
In addition, the Ajinomoto GZ41R2H packaging substrate also plays a role in protecting and isolating electronic components, making them less susceptible to interference and damage from the external environment. By covering the surface of the packaging substrate with a layer of special insulating material, such as solder film and silk screen, short circuits between components and unexpected circuit failures can be effectively prevented, thereby improving the reliability and stability of electronic equipment.
In short, the Ajinomoto GZ41R2H packaging substrate is not only a support structure for electronic equipment, but also a key component to achieve circuit functions. Its design and manufacturing directly affect the performance and reliability of the equipment, so it has an extremely important status and value in the field of electronic engineering.
Ajinomoto GZ41R2H package substrate design Reference Guide.
When designing the Ajinomoto GZ41R2H package substrate, there are some key principles and guidance that need to be followed to ensure that the final product is high-performance, reliable and cost-effective. Here are some suggestions for designing the Ajinomoto GZ41R2H package substrate:
Package Selection
Selecting the appropriate package type and size is critical to the performance of the circuit. Select the appropriate Ajinomoto GZ41R2H package substrate size and shape based on circuit function and layout requirements.
Hierarchical Design
Reasonable hierarchical structure design can improve circuit performance and layout flexibility. Consider separating signal, power, and ground layers and ensuring proper interlayer connections and impedance matching.
Wiring Plan
Careful planning of cabling can minimize signal interference and power consumption. Avoid wiring crossovers and long lines, and try to use the shortest path to connect components.
Thermal Design
Consider the heat generated in the circuit and take appropriate heat dissipation measures, such as heat sinks or thermal pads, to ensure that components operate within a safe temperature range.
EMI/EMC Considerations
During the design process, electromagnetic interference (EMI) and electromagnetic compatibility (EMC) should be considered, and necessary shielding measures and filter design should be taken to ensure that the circuit complies with relevant electromagnetic standards.
Pad Design
Design appropriate pad size and spacing to facilitate manual or automatic welding and ensure good welding quality and reduce welding defects.
Component Layout
Properly arrange component layout, taking into account signal transmission paths, heat distribution, and maintenance convenience to optimize circuit performance and maintainability.
Anti-static Protection
Take appropriate anti-static measures, such as electrostatic protective ground wires and electrostatic dischargers, to prevent static electricity from damaging circuits and components.
Testing And Validation
After the design is completed, comprehensive testing and verification are performed to ensure that the circuit meets the design specifications and performance requirements, and necessary corrections and optimizations are made.
The above are some key principles and guidance to consider when designing the Ajinomoto GZ41R2H package substrate. By following these guidelines, an Ajinomoto GZ41R2H package substrate with superior performance, reliability and stability can be designed to meet the needs of various applications.
What material is used in Ajinomoto GZ41R2H package substrate?
Ajinomoto GZ41R2H packaging substrate is a key electronic device infrastructure, and the materials used in its manufacturing process play a vital role. The following is an introduction to these materials:
First of all, glass fiber is one of the main constituent materials of the Ajinomoto GZ41R2H packaging substrate. This material is widely used to create the basic structure of substrates and is favored for its excellent mechanical strength and high temperature resistance. Fiberglass provides the backbone of the substrate, allowing it to withstand the stresses associated with the installation and use of electronic components.
Secondly, copper is another important material used for the conductive layer of the Ajinomoto GZ41R2H package substrate. The conductive layer is a key part of the circuit connection, and copper is chosen as the material for the conductive layer because it has excellent conductive properties and good processability. The copper layer is chemically processed and etched to form the wires and connection points on the circuit board, making electrical connections between electronic components.
In addition, solder film is also one of the essential materials in the manufacturing process of Ajinomoto GZ41R2H packaging substrate. Solder film is applied to the surface of the substrate to protect the conductive layer and provide a surface for soldering connections. It provides a stable connection during soldering and ensures good contact and conductivity between electronic components and substrates.
Finally, silk screen is the material used to print logos and markings on the surface of the Ajinomoto GZ41R2H package substrate. Silk screen printing is usually used to print logos, component numbers, warning messages, etc. on substrates to help users correctly identify and use electronic devices.
To sum up, the materials used in the manufacturing process of the Ajinomoto GZ41R2H packaging substrate include glass fiber, copper, solder film and silk screen, etc., which together constitute the basic structure of the substrate and ensure it has excellent conductive properties, stability and reliability properties to meet the needs of electronic devices in various application fields.
What size are Ajinomoto GZ41R2H package substrate?
The Ajinomoto GZ41R2H package substrate is an essential component in electronic devices, and its size and specifications vary depending on the application, with different designs from small to large, simple to complex. In modern electronic products, Ajinomoto GZ41R2H packaging substrates meet various needs with their various sizes and specifications.
First, for small electronic devices, such as smartphones, tablets, etc., the Ajinomoto GZ41R2H packaging substrate usually adopts a smaller size. These packaging substrates require compact designs to fit into the small size of the device while ensuring good circuit connections and signal transmission. Therefore, these substrates may adopt micro-packaging technologies such as BGA (ball grid array) packaging to achieve higher integration and smaller size.
On the other hand, for large electronic equipment, such as computer servers, industrial control systems, etc., the Ajinomoto GZ41R2H packaging substrate usually has larger size and higher complexity. These substrates may need to support more electronic components and more complex circuit designs to meet the device’s performance requirements. Therefore, they may be relatively larger in size to accommodate more circuits and connectors while maintaining good thermal and signal integrity.
In addition to size, Ajinomoto GZ41R2H package substrates may also have different specifications, including number of layers, line width/line spacing, aperture size, etc. These specifications vary based on specific application and design requirements to ensure stable and reliable operation of the substrate in a variety of environmental and operating conditions.
Overall, the size and specifications of the Ajinomoto GZ41R2H package substrate play a vital role in electronic device design. Whether it is a small portable device or a large industrial system, it is inseparable from the support and application of these substrates. As technology continues to advance and market demands continue to change, the size and specifications of the Ajinomoto GZ41R2H packaging substrate will continue to evolve and improve to meet the needs of future electronic products.
The Manufacturer Process of Ajinomoto GZ41R2H package substrate.
The manufacturing process of the Ajinomoto GZ41R2H package substrate is a precise and complex process involving multiple critical steps to ensure the quality and reliability of the final product. The individual steps of this manufacturing process are described in detail below:
Design Phase
The process of manufacturing the Ajinomoto GZ41R2H package substrate begins in the design phase. At this stage, engineers use professional design software to draw wiring diagrams and lamination diagrams for the packaging substrate based on the customer’s needs and specifications. The design process needs to consider factors such as circuit layout, signal transmission paths, placement of electronic components, and heat dissipation to ensure that the final product can meet performance requirements.
Prototyping
Once the design is complete, a prototype of the Ajinomoto GZ41R2H package substrate is produced. Typically, prototyping uses rapid prototyping techniques such as PCB prototyping for use in subsequent testing and verification. The key goals of the prototyping phase are to verify the correctness and feasibility of the design, as well as to identify possible problems and room for improvement.
Etching
After the prototype verification is passed, the next step is to enter the formal production stage. The first is the etching process, which uses chemical etching or mechanical processing methods to remove the copper layer on the substrate according to the designed pattern to form wires and connection points. The etching process requires highly precise control to ensure the accuracy and connectivity of each circuit path.
Drilling
After etching is complete, holes need to be drilled into the substrate to mount the electronic components and make connections. The drilling process usually uses a CNC drilling machine or laser drilling machine to accurately drill and position holes according to the requirements on the design drawings. Accuracy and precision in drilling are critical for subsequent assembly and welding.
Assemble
The last critical step is to mount the electronic components on the Ajinomoto GZ41R2H package substrate and solder them. This involves delicate manual operations or automated production lines. During the assembly process, engineers need to ensure the correct location and positioning of each component and connect it to the substrate through soldering techniques. After assembly is completed, strict quality inspection and functional testing are required to ensure that the product’s performance and reliability meet expected standards.
Through these carefully designed and precision-operated steps, the Ajinomoto GZ41R2H package substrate is produced, providing reliable support and connection for the performance and functionality of various electronic devices.
The Application area of Ajinomoto GZ41R2H package substrate.
The Ajinomoto GZ41R2H package substrate is used in a wide range of industries, and its versatility and reliability make it an indispensable part of many fields.
Consumer Electronics
In the field of consumer electronics, Ajinomoto GZ41R2H packaging substrates are widely used in devices such as smartphones, tablets, digital cameras, game consoles, and home appliances. Its high-density, high-performance design allows electronic products to be more compact while providing stable and reliable circuit connections, meeting the needs of modern consumer electronics for high performance and miniaturization.
Car
In the automotive industry, Ajinomoto GZ41R2H packaging substrates are used in automotive electronic systems, including in-car entertainment systems, navigation systems, engine control units, airbags, and in-vehicle communication systems. Its high temperature resistance and vibration resistance ensure stable and reliable operation in harsh automotive environments.
Aerospace
In the aerospace field, Ajinomoto GZ41R2H packaging substrates are widely used in high-end equipment such as aircraft, satellites, navigation equipment and spacecraft. Its lightweight and high-strength design meets the strict weight and performance requirements of aerospace equipment, while providing stable and reliable circuit connections to ensure the normal operation of the equipment.
Medical Equipment
In the field of medical equipment, Ajinomoto GZ41R2H packaging substrates are used in various medical equipment, including medical diagnostic instruments, implantable medical equipment, medical monitoring systems, etc. Its high-density and high-reliability design ensures the stable operation of medical equipment and meets the needs of the medical field for accurate and reliable electronic equipment.
Communication
In the field of communications, Ajinomoto GZ41R2H packaging substrate is widely used in base station equipment, communication network equipment, optical fiber communication equipment, etc. Its high-speed signal transmission and stable and reliable characteristics ensure the efficient operation of communication equipment and meet the requirements for high performance and high stability in the communication field.
In general, Ajinomoto GZ41R2H packaging substrates play an important role in various fields such as consumer electronics, automobiles, aerospace, medical equipment, and communications, providing strong support for the development of modern technology.
What are the advantages of Ajinomoto GZ41R2H package substrate?
The Ajinomoto GZ41R2H package substrate offers many advantages over other wiring methods, making it ideal for use in electronic devices.
First, the Ajinomoto GZ41R2H package substrate offers excellent compactness. Due to its exquisite design, it can accommodate a large number of electronic components in a small space, making the circuit board more compact and saving equipment space.
Secondly, the Ajinomoto GZ41R2H package substrate has a high degree of reliability. Using high-quality materials and advanced manufacturing processes, the substrate has excellent performance and stability, and can maintain stable working status under various environmental conditions, reducing the risk of equipment failure.
In addition, the Ajinomoto GZ41R2H package substrate offers mass production convenience. The design and manufacturing process of the substrate has been carefully optimized to achieve efficient mass production, greatly reducing production costs, ensuring product quality and consistency, and meeting the needs of mass production.
Finally, the Ajinomoto GZ41R2H package substrate offers excellent design flexibility. Designers can flexibly design and customize the substrate according to actual needs, achieve customization of functions, meet the needs of different application scenarios, and improve the competitiveness and applicability of the product.
In summary, Ajinomoto GZ41R2H packaging substrate has become an ideal choice in electronic equipment due to its compactness, reliability, mass production convenience and design flexibility, providing reliable and efficient solutions for various industries.
FAQ
How reliable is the Ajinomoto GZ41R2H package substrate?
Ajinomoto GZ41R2H package substrates are known for their high reliability. Through precision manufacturing processes and quality control, as well as rigorous testing and verification, these packaging substrates ensure stable operation under various environmental conditions and long-term performance and durability.
How is the thermal management of the Ajinomoto GZ41R2H package substrate?
The Ajinomoto GZ41R2H packaging substrate has excellent thermal management properties and can effectively disperse the heat generated by electronic devices, thereby ensuring stable operation of the device under high load conditions. These packaging substrates are typically designed with good heat dissipation structures and can be customized to specific application needs.
What is the cost of the Ajinomoto GZ41R2H package substrate?
The cost of the Ajinomoto GZ41R2H package substrate depends on several factors, including size, materials, complexity, and production volume. Generally speaking, as the scale increases and the technology matures, the cost will decrease accordingly.