Ajinomoto GX92 Package Substrate Manufacturer.Ajinomoto GX92 Package Substrate Manufacturer specializes in crafting cutting-edge substrates for packaging solutions. With a dedication to quality and innovation, they engineer substrates that cater to diverse industrial needs, ensuring optimal performance and reliability. Their expertise lies in developing materials that enhance product protection, shelf life, and sustainability. From food packaging to electronic components, they deliver tailored solutions that meet stringent standards and exceed customer expectations. Ajinomoto GX92’s commitment to excellence makes them a trusted partner for businesses seeking superior packaging substrates that elevate their products in the market.
With the continuous development of electronic technology, Ajinomoto GX92 packaging substrate has become an important part of modern electronic products. As a key carrier for connecting and supporting various electronic components, Ajinomoto GX92 packaging substrate plays an irreplaceable role in ensuring circuit stability and improving performance and reliability. This article will delve into the key role and characteristics of Ajinomoto GX92 packaging substrate to help readers better understand and apply this key technology.
What is Ajinomoto GX92 Package Substrate?
Ajinomoto GX92 packaging substrates are an integral part of today’s electronics industry. As an advanced electronic component carrier, it carries a variety of functional components and assembles them together in an orderly manner to form a complex and efficient circuit system. These circuit systems can be the smartphones and tablets we use in our daily lives, or they can be automated control systems or medical equipment in the industrial field.
This substrate is typically made from a high-quality base material, such as premium FR-4 fiberglass reinforced epoxy resin, which has excellent electrical conductivity and thermal properties. This enables the Ajinomoto GX92 packaging substrate to effectively transfer current and dissipate heat in the circuit, providing a reliable foundation for the stable operation of electronic equipment. Its excellent electrical conductivity ensures stable transmission of circuit signals, while its excellent thermal performance helps keep electronic components within a suitable operating temperature range and prevent performance degradation or damage caused by overheating.
In addition to providing reliable physical support and electrical connections, the Ajinomoto GX92 packaging substrate also has high density and dimensional accuracy, allowing it to accommodate more components in a limited space and ensure a compact layout between them. This compact design makes electronic equipment lighter and more compact, and also helps simplify the production process and improve production efficiency.
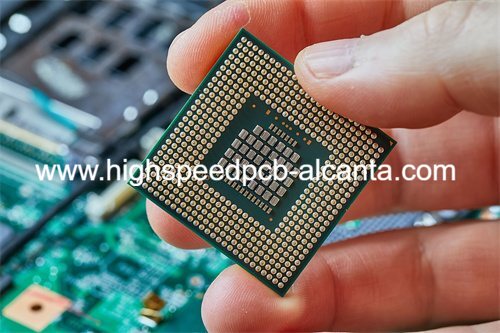
Ajinomoto GX92 Package Substrate Manufacturer
In general, Ajinomoto GX92 packaging substrate is not only one of the key components of electronic equipment, but also an important driving force for the development of modern technology. It provides a solid foundation for performance optimization and function realization of various electronic products, and helps electronic technology continue to move forward.
Ajinomoto GX92 Package Substrate design Reference Guide.
Designing the Ajinomoto GX92 packaging substrate is a complex and critical process that directly affects the performance and stability of electronic devices. When designing, engineers need to consider multiple factors to ensure that the final product meets the expected requirements.
First, circuit layout is one of the key steps in the design process. A good circuit layout can minimize signal interference and electromagnetic interference and improve the stability and reliability of the circuit. Engineers need to rationally arrange the location and connection of electronic components to avoid performance problems caused by confusing wiring.
Secondly, size specifications are also one of the important factors to be considered during the design process. Ajinomoto GX92 packaging substrate has flexible size selection, but reasonable size planning still needs to be carried out according to specific application scenarios and space constraints during the design process. Engineers need to ensure that the baseboard dimensions match the device’s enclosure and leave enough space for heat dissipation and assembly.
In addition, heat dissipation requirements are also an important factor that cannot be ignored during the design process. As the power of electronic devices continues to increase, heat dissipation has become one of the key challenges in the design process. Engineers need to properly design the heat dissipation structure to ensure that electronic components can maintain an appropriate temperature during operation and avoid performance degradation or failure caused by overheating.
The Design Reference Guide provides engineers with valuable advice and tips to help them take full advantage of the performance benefits of the Ajinomoto GX92 packaging substrate. Through reasonable circuit layout, size specifications and heat dissipation design, engineers can ensure that the final product has stable performance and excellent reliability to meet the needs of different application scenarios.
What material is used in Ajinomoto GX92 Package Substrate?
Ajinomoto GX92 packaging substrate is a high-performance electronic component carrier whose high-quality materials are key to its stability and durability. First, the Ajinomoto GX92 uses an advanced FR-4 base material, a composite material with excellent electrical properties and mechanical strength. FR-4 base material has excellent heat resistance and insulation properties, which can effectively reduce the deformation and leakage of circuit boards, thus improving the stability of the circuit. In addition, FR-4 substrate also has good processing properties and can meet the design needs of various complex circuit boards.
In addition to high-grade FR-4 base material, Ajinomoto GX92 also uses high-quality copper foil as the material of the conductive layer. High-quality copper foil has high conductivity and good welding performance, which can ensure efficient transmission and reliable connection of the circuit. Through carefully selected copper foil materials, the Ajinomoto GX92 packaging substrate not only has good electrical conductivity, but can also effectively reduce heat accumulation on the circuit board and improve the overall heat dissipation effect.
In addition, the Ajinomoto GX92 features carefully selected pad materials and overlays to further enhance its performance and reliability. The pad material has been specially treated to have excellent corrosion resistance and welding reliability, ensuring the stability and durability of the welding joints. The covering layer can effectively protect the circuit board from the external environment and extend the service life of the circuit board.
To sum up, the Ajinomoto GX92 packaging substrate is made from high-quality materials, including high-grade FR-4 base material, high-quality copper foil, and selected pad materials and overlays. The selection of these high-quality materials not only ensures the stability and durability of the circuit board, but also improves its performance and reliability, making it an ideal choice for a variety of advanced electronic devices.
What size are Ajinomoto GX92 Package Substrate?
Ajinomoto GX92 packaging substrate is a core component of modern electronic equipment, and its flexible size selection is a highlight of its design. This size flexibility allows it to adapt to the needs of a variety of different application scenarios, from micro electronic devices to large industrial control systems, you can find the right Ajinomoto GX92 packaging substrate size.
For miniature electronic devices, size compression is critical. Miniature devices often require more functionality and components to fit into a limited space, so the Ajinomoto GX92 packaging substrate offers a variety of small form factor options. These micro-sized Ajinomoto GX92 packaging substrates can be easily integrated into small electronic devices such as smartphones, wearable devices, smart home products, etc., providing them with stable and reliable circuit support.
At the same time, for large-scale industrial control systems, stability and reliability are key considerations. Ajinomoto GX92 packaging substrates are available not only in small size options, but also in larger sizes to meet the needs of industrial-grade equipment. These large-sized Ajinomoto GX92 packaging substrates have stronger heat dissipation capabilities and circuit layout flexibility, can carry more electronic components, and maintain stable operation in harsh industrial environments.
Overall, the size flexibility of Ajinomoto GX92 packaging substrates provides an ideal solution for a variety of electronic devices of varying sizes and application scenarios. Whether you are pursuing miniaturization for portable equipment or industrial control systems that require stability and reliability, you can find the most suitable size option in the Ajinomoto GX92 packaging substrate series. This flexibility brings greater freedom and creativity to the design of electronic equipment, and promotes the continuous innovation and development of electronic technology.
The Manufacturer Process of Ajinomoto GX92 Package Substrate.
The manufacturing process of Ajinomoto GX92 packaging substrate is a complex and precise process involving multiple links to ensure that the final product meets high quality standards. Here’s a closer look at the process:
Design phase
Before the Ajinomoto GX92 packaging substrate can be manufactured, it first needs to be designed. The design team uses professional circuit design software to design key parameters such as circuit layout and wiring paths based on customer requirements and application needs. The key to the design phase is to ensure that the circuit layout is reasonable, stable, and meets the required functionality and performance requirements.
Printing stage
After the design is completed, the next step is to print the design pattern onto the substrate material. Patterns of conductive and insulating layers are typically printed onto the substrate surface using screen printing or photolithography techniques. The key to this step is to ensure accurate printing, clear patterns, and precise alignment between the different layers.
Etching stage
After printing is complete, unwanted portions of material need to be removed from the substrate to form conductive paths and circuit connections. This process is called etching and is usually performed using chemical etching or mechanical cutting. Strict control of etching time and temperature is an important factor in ensuring circuit quality.
Assembly stage
After the etching is completed, the circuit pattern on the substrate has been formed, and the next step is the process of assembling various electronic components onto the substrate. This includes steps such as soldering components, mounting chips, connecting wires, etc. The assembly phase requires a high degree of precision and skill to ensure that each component is connected correctly and soldered well.
Strict quality control is a vital part of the entire manufacturing process. Each stage requires rigorous inspection and testing to ensure the product meets design requirements and customer expectations. Advanced production technology, such as the application of automated equipment and precision instruments, is also a key factor in ensuring that each Ajinomoto GX92 packaging substrate has consistent high quality standards. This rigorous manufacturing process and high-level technology ensure the reliability and stability of Ajinomoto GX92 packaging substrates in various application scenarios, providing a solid foundation for the development of modern electronic products.
The Application area of Ajinomoto GX92 Package Substrate.
As a high-performance electronic component carrier, Ajinomoto GX92 packaging substrate is widely used in modern technology fields. Its application fields cover electronic communications, industrial automation, automotive electronics, medical equipment and other fields. Its reliability and stability make it ideal for a variety of advanced electronic devices.
In the field of electronic communications, Ajinomoto GX92 packaging substrates are widely used in wireless communication equipment, network equipment and satellite communication systems. Whether used for mobile communication base stations, wireless routers or satellite receivers, Ajinomoto GX92 packaging substrates can provide stable circuit support to ensure efficient operation of communication equipment.
In the field of industrial automation, Ajinomoto GX92 packaging substrates are used in various industrial control systems, robots, sensors and automation equipment. Its stability and durability enable it to withstand harsh industrial environmental conditions, ensuring reliable operation and efficient production of industrial equipment.
In the field of automotive electronics, Ajinomoto GX92 packaging substrates are widely used in key components such as automotive electronic control units (ECUs), in-vehicle entertainment systems, and navigation systems. Its anti-seismic and vibration performance and high temperature tolerance ensure the stable operation of automotive electronic equipment under various road conditions and environmental conditions.
In the field of medical equipment, Ajinomoto GX92 packaging substrates are used in medical imaging equipment, vital sign monitoring instruments, treatment equipment and other medical devices. Its high-precision circuit design and stable electrical performance provide reliable data collection and processing support for medical equipment, ensuring the accuracy and safety of medical equipment.
Overall, Ajinomoto GX92 packaging substrate has become one of the indispensable core components in various advanced electronic equipment due to its excellent performance characteristics. Its wide application in many fields provides strong support and driving force for the development and progress of modern science and technology.
What are the advantages of Ajinomoto GX92 Package Substrate?
When talking about the advantages of Ajinomoto GX92 packaging substrate, we have to first mention its excellent performance in stability. Compared with traditional circuit assembly methods, Ajinomoto GX92 packaging substrate uses advanced materials and manufacturing processes to ensure the stability and reliability of the circuit. Its materials are made of high-grade FR-4 base material and high-quality copper foil, which makes the circuit board have excellent durability and corrosion resistance and can operate stably in harsh environmental conditions.
In addition, the Ajinomoto GX92 packaging substrate’s smaller footprint gives it greater flexibility in design and integration. Compared with traditional circuit assembly methods, Ajinomoto GX92 packaging substrates can achieve a more compact design, thereby occupying less space in electronic devices, making the product more lightweight and portable, and also conducive to the beautiful and neat appearance of the product.
What’s more worth mentioning is that the ease of mass production of Ajinomoto GX92 packaging substrates is also one of its advantages. Using modern production processes and automated equipment, large quantities of Ajinomoto GX92 packaging substrates can be efficiently produced, thereby reducing production costs and improving production efficiency. This provides electronics manufacturing companies with a greater competitive advantage, allowing them to meet market demand faster and accelerate the product launch process.
Therefore, it is precisely because of these advantages that Ajinomoto GX92 packaging substrates have become an integral part of modern electronic manufacturing. Whether in consumer electronics or industrial control systems, Ajinomoto GX92 packaging substrates play a vital role, providing reliable support for the stable operation and performance improvement of various electronic devices. As technology continues to develop and the scope of applications continues to expand, it is believed that Ajinomoto GX92 packaging substrate will continue to play its important role in promoting continued innovation and progress in the electronics industry.
FAQ
What is the difference between Ajinomoto GX92 packaging substrate and traditional substrate?
Ajinomoto GX92 packaging substrate uses advanced materials and manufacturing processes to provide higher stability and reliability than traditional substrates. They usually have smaller size, higher density and better thermal conductivity, making them suitable for more complex circuit designs and high-performance electronic equipment.
What is the thermal conductivity of the Ajinomoto GX92 packaging substrate?
The Ajinomoto GX92 packaging substrate uses high-quality thermally conductive materials and designs to ensure that circuit components can effectively dissipate heat during work. This excellent thermal conductivity can improve the performance stability of electronic equipment, extend its service life, and reduce failure rates.
What is the size range of Ajinomoto GX92 packaging substrates?
Ajinomoto GX92 packaging substrates are available in a wide range of sizes and can be customized to meet customer specific needs. From micro electronic devices to large industrial control systems, you can find the right Ajinomoto GX92 packaging substrate size and shape.
What is the production lead time for Ajinomoto GX92 packaging substrate?
The lead time for producing Ajinomoto GX92 packaging substrates depends on the specific specifications and order volume. Typically, production lead time can be anywhere from a few days to a few weeks, but may also be affected by specific processes and customization requirements. Our production team is committed to providing an efficient production process to meet our customers’ time requirements.