Advanced Cavity Circuit Board Manufacturer.Our company is an advanced cavity circuit board manufacturer, specializing in the production of high-precision, multi-layered PCBs with integrated cavities. We leverage cutting-edge technology to deliver exceptional performance and reliability for a wide range of applications, from telecommunications to aerospace. Our commitment to innovation ensures that we meet the most stringent industry standards and customer requirements.
Advanced Cavity Circuit Boards represent a significant evolution in PCB technology, incorporating recessed areas or cavities within the board to house components. These advanced designs offer numerous advantages, including improved signal integrity, enhanced thermal management, and space-saving capabilities. Such features make them indispensable in high-performance and compact electronic applications.
What is an Advanced Cavity Circuit Board?
An Advanced Cavity Circuit Board is a specialized type of printed circuit board (PCB) that includes one or more cavities or recessed areas designed to accommodate electronic components. These cavities can be precisely machined or etched into the substrate, allowing for the embedding of components such as chips, passive elements, and other critical parts.
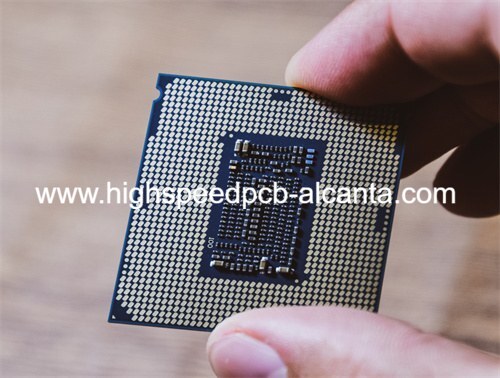
Advanced Cavity Circuit Board Manufacturer
Cavity Formation: The creation of cavities allows components to sit within the PCB rather than on its surface, leading to a more compact and integrated design.
Material Selection: High-performance materials are often used to ensure the board can withstand the manufacturing process and operational demands.
Precision and Customization: Advanced manufacturing techniques enable the precise placement of cavities and components, tailored to specific application requirements.
Design Reference Guide for Advanced Cavity Circuit Boards
Designing Advanced Cavity Circuit Boards involves several critical steps to ensure performance, reliability, and manufacturability:
Choosing the right materials is crucial. High-frequency laminates, ceramics, and composite materials are commonly used to provide the necessary electrical, thermal, and mechanical properties.
Size and Shape: The size and shape of the cavities are designed based on the components they will house. This involves detailed CAD modeling and simulation to ensure proper fit and function.
Depth Control: The depth of the cavities must be precisely controlled to ensure components are properly seated and protected.
Advanced Cavity Circuit Boards often require sophisticated thermal management strategies, such as:
Thermal Vias: Placing vias within and around the cavities to help dissipate heat.
Heat Sinks and Spreaders: Integrating heat sinks or spreaders within the board to manage high-power components.
Material Considerations: Using materials with high thermal conductivity to enhance heat dissipation.
Impedance Control: Maintaining controlled impedance through careful design of trace widths, spacing, and layer stack-up.
Signal Integrity: Ensuring signal integrity by minimizing crosstalk and signal loss through optimized routing and shielding techniques.
Ensuring the board can be manufactured reliably involves:
Precision Machining: Using advanced milling or laser etching techniques to create precise cavities.
Assembly Techniques: Developing assembly processes that ensure components are accurately placed and securely attached within the cavities.
Testing and Quality Control: Implementing rigorous testing and quality control measures to verify the board’s performance and reliability.
What Materials are Used in Advanced Cavity Circuit Boards?
The materials used in Advanced Cavity Circuit Boards must provide excellent electrical, thermal, and mechanical properties. Common materials include:
High-Frequency Laminates: Materials like Rogers or Taconic laminates are used for their low dielectric loss and stable performance at high frequencies.
Ceramics: Ceramic materials such as alumina or aluminum nitride offer high thermal conductivity and mechanical stability, making them suitable for high-power and high-frequency applications.
Composites: Composite materials that combine the benefits of ceramics and polymers provide a good balance of electrical, thermal, and mechanical properties.
Copper: Used for the conductive traces and pads, copper offers excellent electrical conductivity, which is essential for forming the electrical pathways and interconnections.
Solder Bumps and Balls: Lead-free solder bumps or balls are often used to attach components within the cavities, providing electrical connections and mechanical support.
What Size are Advanced Cavity Circuit Boards?
The size of Advanced Cavity Circuit Boards can vary widely depending on the application and design requirements. Factors influencing the size include:
Component Size and Layout: The size of the components and their layout within the cavities determine the overall dimensions of the PCB.
Application Requirements: Different applications have varying size constraints. For example, compact devices may require smaller PCBs with precise cavity placements, while larger systems may have more flexibility in size.
Standard and Custom Sizes: While some Advanced Cavity Circuit Boards are made in standard sizes, many are custom-designed to meet specific application needs, leading to a wide range of possible sizes.
The Manufacturing Process of Advanced Cavity Circuit Boards
The manufacturing process of Advanced Cavity Circuit Boards involves several precise and controlled steps:
CAD Design: Creating a detailed CAD design that incorporates all cavities, traces, and components.
Simulation: Using electromagnetic and thermal simulation tools to optimize the design and ensure it meets performance requirements.
Lamination: Preparing the selected laminate material, which may involve bonding multiple layers together.
Cavity Formation: Using milling, laser etching, or other advanced techniques to form the cavities.
Photo-etching: Transferring the circuit pattern onto the PCB using photo-etching techniques.
Plating: Plating the conductive traces and vias to establish electrical pathways.
Surface Mount Technology (SMT): Placing and soldering components onto the PCB using automated SMT processes.
Flip-Chip Bonding: For some applications, flip-chip bonding may be used to attach components within the cavities.
Electrical Testing: Conducting electrical tests to ensure all connections are intact and the board functions as intended.
Thermal Testing: Performing thermal tests to verify the board’s ability to dissipate heat and maintain performance.
Final Inspection: A thorough inspection to ensure the board meets all design specifications and quality standards.
The Application Area of Advanced Cavity Circuit Boards
Advanced Cavity Circuit Boards are used in various high-performance and compact electronic applications:
Telecommunications: Used in RF and microwave communication devices, where high-frequency signal integrity is crucial.
Aerospace and Defense: Employed in radar systems, avionics, and other critical defense electronics that require reliable performance in harsh environments.
Medical Devices: Integrated into medical imaging equipment, diagnostic tools, and other devices that demand precision and reliability.
Automotive: Utilized in advanced driver-assistance systems (ADAS), vehicle-to-everything (V2X) communication, and other automotive electronics.
Consumer Electronics: Found in compact and high-frequency consumer electronics like smartphones, tablets, and wearable devices.
What are the Advantages of Advanced Cavity Circuit Boards?
Advanced Cavity Circuit Boards offer several advantages:
Improved Signal Integrity: By embedding components within cavities, these boards reduce signal path lengths and minimize parasitic effects, enhancing signal integrity.
Enhanced Thermal Management: Cavities allow for better thermal management, as components can be placed closer to heat sinks and other thermal management features.
Space-Saving Design: Embedding components within the PCB saves space, enabling more compact and integrated designs.
Customizability: The ability to create custom cavity designs allows for tailored solutions that meet specific application requirements.
Durability and Reliability: High-performance materials and advanced manufacturing techniques ensure that Advanced Cavity Circuit Boards are durable and reliable.
FAQ
What are the main benefits of using Advanced Cavity Circuit Boards in high-performance applications?
Advanced Cavity Circuit Boards provide improved signal integrity, enhanced thermal management, space-saving designs, customizability, and reliability, making them ideal for high-performance applications.
How are cavities in Advanced Cavity Circuit Boards formed?
Cavities in Advanced Cavity Circuit Boards are typically formed through precise milling, laser etching, or other advanced techniques, allowing for the creation of custom-fit spaces for components within the PCB.
What materials are commonly used in Advanced Cavity Circuit Boards?
Common materials include high-frequency laminates like Rogers or Taconic, ceramics such as alumina or aluminum nitride, composite materials, and copper for conductive traces.
In which industries are Advanced Cavity Circuit Boards most commonly used?
Advanced Cavity Circuit Boards are commonly used in telecommunications, aerospace and defense, medical devices, automotive electronics, and high-frequency consumer electronics.
How do Advanced Cavity Circuit Boards improve thermal management?
Advanced Cavity Circuit Boards improve thermal management by allowing components to be placed closer to heat sinks and incorporating thermal vias and other features to efficiently dissipate heat.