ABF GZ41R2H Package Substrates Manufacturer.ABF GZ41R2H Package Substrates Manufacturer specializes in crafting advanced package substrates, catering to the intricate needs of cutting-edge electronic devices. With a commitment to innovation and precision engineering, they deliver substrates of unparalleled quality, crucial for ensuring the reliability and performance of semiconductor packages. Leveraging state-of-the-art technologies and a depth of expertise, they offer a comprehensive range of solutions tailored to meet diverse industry requirements. From compact microelectronic assemblies to robust integrated systems, ABF GZ41R2H stands as a cornerstone in the realm of package substrate manufacturing, driving forward the possibilities of modern electronics.
ABF GZ41R2H Package Substrates is a high-performance printed circuit board (PCB) material designed to meet high-density, high-frequency packaging requirements. In modern electronic equipment, packaging substrates play a vital role, and ABF GZ41R2H packaging substrates have become the material of choice for many high-end electronic products due to their excellent electrical performance and reliability. Its excellent performance characteristics provide reliable support for high-frequency applications. It also performs well in high-density interconnection, thermal performance and manufacturing processes, meeting the stringent requirements of modern electronic equipment for packaging substrates.
What are ABF GZ41R2H Package Substrates?
ABF GZ41R2H Package Substrates is a high-performance packaging substrate material designed to meet the high-density, high-frequency, and high-reliability packaging requirements of today’s electronic equipment. As a type of printed circuit board (PCB), ABF GZ41R2H Package Substrates uses advanced materials and manufacturing processes to ensure that it can perform well in various complex application scenarios.
This packaging substrate material has excellent electrical and thermal properties, can provide stable signal transmission characteristics at high frequencies, and is suitable for demanding application scenarios such as 5G communications and wireless networks. At the same time, its high-density interconnection design allows more devices to be integrated into a small package, thereby achieving miniaturization and lightweighting of electronic products.
ABF GZ41R2H Package Substrates also have excellent thermal stability and heat dissipation performance, which helps reduce the operating temperature of electronic devices and improve system reliability and stability. This feature is especially important in high-power-density application scenarios, such as servers, high-performance computers, etc.
In terms of manufacturing process, ABF GZ41R2H Package Substrates adopts advanced manufacturing processes and strict quality control standards to ensure product quality and consistency. Each packaging substrate undergoes rigorous testing and verification to ensure that it meets design requirements and customer needs.
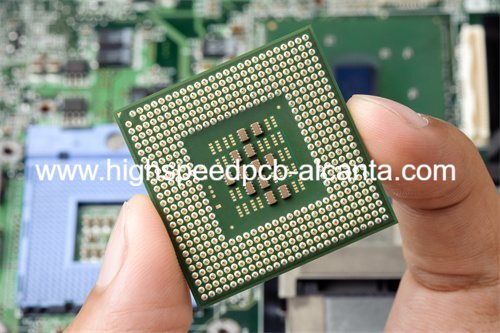
ABF GZ41R2H Package Substrates Manufacturer
In general, ABF GZ41R2H Package Substrates is a high-performance, highly reliable packaging substrate material that is widely used in communications, computers, consumer electronics, automotive electronics and other fields, providing strong support and promotion for the development of the electronics industry. force.
ABF GZ41R2H Package Substrates design Reference Guide.
ABF GZ41R2H packaging substrate is a key material used in high-performance electronic packaging, and its design involves several critical steps and considerations. This guide will provide you with reference suggestions on how to design the ABF GZ41R2H package substrate.
Design planning
Before starting the design, you first need to clarify the overall requirements and functions of the circuit. Determine the number, size, and layout of components required, taking into account the circuit’s high-frequency characteristics and thermal management needs.
Schematic design
Use CAD software to draw a schematic diagram of the circuit, including all components, connections and pin definitions. Ensure the accuracy and completeness of the schematic diagram for subsequent PCB layout and wiring work.
Component layout
Place various components reasonably on the PCB board, taking into account electrical performance, signal integrity and thermal management. Based on the connection relationships and signal transmission paths between devices, layout optimization is performed to minimize signal interference and crosstalk.
Wiring
Connect the pins of each device to ensure signal integrity and power integrity. Avoid long lines, crossing lines and sharp turns, and try to use the shortest and most direct path to reduce signal transmission delay and power loss.
Check and verify
Conduct Design Rule Checks (DRC) and Electrical Rule Checks (ERC) to ensure designs are spec-compliant and error-free. At the same time, simulation analysis and electrical performance testing are performed to verify the reliability and stability of the design.
Generate Gerber files
After the design is completed, the Gerber files and drilling files required for manufacturing are generated. Make sure the file is formatted correctly and contains all necessary layer information and special process requirements.
Manufacturing preparation
Prepare the materials and processes required for manufacturing, and select the appropriate manufacturer for production. Work closely with manufacturers to ensure quality control and delivery times during production.
Through the design and preparation of the above steps, you can better achieve the design goals of the ABF GZ41R2H package substrate and ensure that the performance and reliability of the final product reach the expected level.
What material is used in ABF GZ41R2H Package Substrates?
The materials used in the ABF GZ41R2H package substrate are critical to its high performance and reliability. This packaging substrate is made by laminating copper foil on a specific substrate material to enable interconnection and functionality between electronic devices. The following are the materials commonly used in ABF GZ41R2H package substrates:
Substrate material
The substrate material of the ABF GZ41R2H package substrate is usually fiberglass reinforced epoxy resin (FR4). FR4 has excellent mechanical strength and heat resistance, as well as good electrical properties, and is suitable for high-density, high-frequency packaging applications.
Conductive layer
In the ABF GZ41R2H package substrate, copper foil is used as a conductive layer to form circuit patterns and interconnections. Copper foil has good electrical conductivity and processability, and can meet the requirements of high-density and high-frequency circuits.
Solder mask
The solder mask is an important part of the ABF GZ41R2H package substrate and is used to protect the circuit pattern and pads from environmental erosion and external influences. Common solder mask materials include epoxy resin and polyimide, which have good corrosion resistance and insulation properties.
Silk screen layer
The silk screen layer is usually located on the surface of the packaging substrate and is used to print information such as logos, patterns, and text to facilitate identification and positioning during production and maintenance.
Other materials
In addition to the above main materials, the ABF GZ41R2H packaging substrate may also include filling materials, reinforcement materials and auxiliary materials to improve the mechanical strength, thermal performance and processing performance of the substrate.
To sum up, the material used in the ABF GZ41R2H packaging substrate has good electrical properties, mechanical properties and heat resistance, can meet the requirements of high-end electronic products for high-density and high-frequency packaging, and provides reliable support for the development of the electronics industry. and protection.
What size are ABF GZ41R2H Package Substrates?
ABF GZ41R2H package substrate (Package Substrates), as a high-performance and highly reliable packaging substrate material, plays a key role in modern electronic equipment. In addition to its superior electrical performance and reliability, its size is also one of the important factors for its wide range of applications.
The size of the ABF GZ41R2H package substrate is generally designed and customized according to specific application requirements. Due to the wide variety of electronic products, the size of the packaging substrate also varies depending on the application. However, typically, ABF GZ41R2H package substrates are available in a wide range of sizes to meet electronic product designs with various size requirements.
Generally speaking, the size of the ABF GZ41R2H package substrate can range from a few millimeters to tens of centimeters. For small electronic products, such as smartphones, tablets, etc., the size of the packaging substrate may be smaller, generally ranging from a few centimeters to tens of centimeters. For large electronic equipment, such as servers, industrial control equipment, etc., the size of the packaging substrate may be larger, reaching tens of centimeters or even larger.
In addition, the ABF GZ41R2H package substrate can be customized to meet specific design needs. Some applications may require very specific sized packaging substrates, in which case the design can be custom designed to meet the customer’s specific size and functional needs.
In general, the size of the ABF GZ41R2H package substrate has greater flexibility and customizability, and can be designed and manufactured according to different application requirements. This makes it have broad application prospects in various electronic products and provides strong support for the development of the electronics industry.
The Manufacturer Process of ABF GZ41R2H Package Substrates.
The manufacturing process of ABF GZ41R2H packaging substrate is a complex and precise process, involving careful design and strict control of multiple links. This manufacturing process is described in detail below:
Design preparation
Before manufacturing the ABF GZ41R2H package substrate, the circuit requirements and functionality first need to be accurately determined. Design engineers will generate corresponding design documents based on product requirements, including circuit schematics, layout drawings and related specifications.
Substrate preparation
Choose high-quality substrate materials for the ABF GZ41R2H that have good dielectric properties and mechanical strength. The copper foil is laminated to the surface of the substrate to form a basic conductive layer, laying a solid foundation for subsequent circuit formation.
Graphics transfer
Using advanced exposure and etching processes, the designed circuit pattern is transferred to the substrate surface. During the exposure process, the circuit pattern is projected onto the sensitive photoresist layer through a photomask to form a temporary photolithography pattern. The subsequent etching process will gradually etch away the unnecessary copper foil layer according to the photolithography pattern, thereby forming a circuit pattern.
Metalization
After pattern transfer, the circuit pattern needs to be metallized to form conductive paths and pads. This step is usually completed through electroless copper plating or other metallization processes, which enhances the conductivity of the circuit pattern and provides the necessary conditions for subsequent welding and connection.
Drilling
According to the requirements in the design document, drill the substrate at the specified location. These holes are used to provide interconnections between circuits and for mounting and connecting devices. The location and size of the drill holes need to be precisely controlled to ensure the stability and reliability of the circuit.
Surface treatment
After drilling is completed, the solder mask and silk screen layers are processed on the surface of the substrate. The solder mask layer is used to protect the circuit from erosion by the external environment, while the silk screen layer is used to mark the location and parameters of circuit components to improve the circuit’s recognizability.
Testing and Inspection
Finally, the manufactured ABF GZ41R2H package substrate is fully tested and inspected. This includes electrical testing, visual inspection, and other relevant performance tests to ensure the product meets design requirements and standards. Only through strict testing and inspection can the quality and reliability of the product be guaranteed.
Through the above manufacturing process, the ABF GZ41R2H packaging substrate can meet high-quality and high-performance requirements and meet the application needs of various high-end electronic products.
The Application area of ABF GZ41R2H Package Substrates.
ABF GZ41R2H packaging substrate, as a high-performance packaging substrate material, is widely used in the field of modern electronics. Its superior electrical performance and reliability make it the first choice in many industries. The following is the application range of ABF GZ41R2H package substrate in different fields:
Communication field
The rapid development of 5G technology has put forward higher requirements for communication equipment, and the ABF GZ41R2H packaging substrate is the ideal choice to meet these needs. It is widely used in key components such as 5G base stations, communication equipment and antennas, providing reliable support for high-speed data transmission and stable connections.
Computer field
In areas such as high-performance computers, servers, and data centers, ABF GZ41R2H packaging substrates play a vital role. Its high-density interconnection and excellent thermal performance make it a key component for massively parallel computing and big data processing.
Consumer Electronics
Consumer electronics such as smartphones, tablets and laptops have increasing requirements for packaging substrates. ABF GZ41R2H packaging substrate provides important support for the design and manufacturing of these devices with its miniaturization, high performance and stable and reliable characteristics.
Vehicle electronics
Automotive electronic systems have extremely high requirements for stability and reliability, and ABF GZ41R2H packaging substrate is one of the materials that meets these requirements. It is widely used in key components such as in-vehicle computers, in-vehicle entertainment systems, and advanced driver assistance systems (ADAS) to provide intelligent and safe performance for vehicles.
Industrial control
Industrial control fields such as industrial automation equipment, robotic systems and sensor modules also have increasingly higher requirements for packaging substrates. ABF GZ41R2H package substrate plays an irreplaceable role in industrial control systems with its highly reliable performance and stable operating characteristics.
In general, ABF GZ41R2H packaging substrate has broad application prospects in many fields such as communications, computers, consumer electronics, automotive electronics and industrial control. With the continuous advancement of technology and the expansion of application scenarios, I believe it will have more extensive and in-depth applications in the future.
What are the advantages of ABF GZ41R2H Package Substrates?
As a leading packaging solution, the advantage of ABF GZ41R2H packaging substrate lies not only in its excellent performance and reliability, but also in its advanced manufacturing process and strong adaptability and customizability. Here’s a closer look at these benefits:
Superior performance
ABF GZ41R2H package substrates are known for their excellent electrical and thermal performance. Its high-quality dielectric materials and precise manufacturing processes ensure low-loss, low-latency signal transmission, thus meeting the high-frequency and high-speed requirements of high-end applications. In addition, the excellent thermal conductivity performance effectively reduces the operating temperature of electronic devices, extends the life of the equipment, and ensures the stability and reliability of the system.
High reliability
ABF GZ41R2H packaging substrate has been rigorously tested and verified to have stable and reliable performance. Its manufacturing process strictly follows international standards and quality management systems, ensuring product consistency and reliability. Through long-term stability testing under various harsh environmental conditions, the ABF GZ41R2H package substrate has demonstrated its excellent performance under extreme operating conditions, making it the first choice for many critical applications.
Advanced manufacturing technology
ABF GZ41R2H packaging substrate uses advanced manufacturing processes and materials to ensure product quality and consistency. Its manufacturing process includes the latest micro-machining technology and advanced surface treatment technology, allowing the product to have higher precision and better surface flatness. In addition, the ABF GZ41R2H packaging substrate pays attention to environmental protection and sustainability in material selection and complies with international environmental standards.
Adaptable
ABF GZ41R2H packaging substrate has a wide range of application prospects and is suitable for various complex application scenarios. Whether it is 5G base stations in the communications field or ADAS systems in the automotive electronics field, the ABF GZ41R2H packaging substrate is capable of doing the job. Its excellent performance and reliability make it an ideal choice for a variety of high-end electronic products.
Good customizability
The ABF GZ41R2H package substrate can be custom designed according to customer needs to meet the needs of specific applications. Whether it is size, layer, or material selection, personalized design can be carried out according to customer requirements. This flexibility allows the ABF GZ41R2H packaging substrate to better adapt to the needs of different customers and provide them with optimized solutions.
To sum up, ABF GZ41R2H packaging substrate has become the preferred solution for many high-end electronic products due to its superior performance, high reliability, advanced manufacturing process, strong adaptability and good customizability. With the continuous development and innovation of the electronics industry, it is believed that the ABF GZ41R2H packaging substrate will play an increasingly important role in the future, injecting new vitality into the development of the electronics industry.
FAQ
What fields is ABF GZ41R2H packaging substrate suitable for?
ABF GZ41R2H packaging substrate is widely used in communications, computers, consumer electronics, automotive electronics and industrial control. Its high frequency characteristics and high-density interconnection make it an ideal choice for 5G base stations, high-performance computers, smartphones, vehicle-mounted computers, and industrial automation equipment.
What is the manufacturing process of ABF GZ41R2H package substrate?
The process of manufacturing ABF GZ41R2H package substrate includes steps such as design preparation, substrate preparation, pattern transfer, metallization, drilling, surface treatment and test inspection. Through advanced manufacturing processes and strict quality control, we ensure that our products have stable and reliable performance.
What are the advantages of ABF GZ41R2H packaging substrate compared to other materials?
The ABF GZ41R2H package substrate offers excellent high frequency characteristics, high density interconnection, excellent thermal performance and high reliability. It has advanced manufacturing technology and strong adaptability, and can be customized and designed according to customer needs to meet the needs of different application scenarios.
What are the common applications for ABF GZ41R2H package substrate?
ABF GZ41R2H packaging substrate is widely used in 5G base stations, communication equipment, high-performance computers, smartphones, vehicle-mounted computers, industrial automation equipment and other fields. Its stable and reliable performance provides strong support for the performance improvement of various electronic products.
How long is the manufacturing cycle of ABF GZ41R2H package substrate?
The lead time for manufacturing ABF GZ41R2H package substrates depends on complexity and volume and generally ranges from days to weeks. Through efficient production processes and strict plan management, we ensure that products are delivered on time and meet customer needs.