ABF GL102R8HF Package Substrates Manufacturer.ABF GL102R8HF Package Substrates Manufacturer is a leading provider of advanced packaging substrates for electronic devices. Their expertise lies in crafting high-quality substrates that ensure superior performance, reliability, and miniaturization in various applications. With cutting-edge technology and a commitment to innovation, they cater to the evolving needs of the electronics industry, delivering solutions that meet stringent quality standards and enable the next generation of electronic devices.
ABF GL102R8HF packaging substrates play a vital role in today’s increasingly digital world. It is an integral part of electronic equipment and plays a key role in improving device performance. This article aims to comprehensively introduce the definition, design, manufacturing, application and advantages of ABF GL102R8HF packaging substrate, and provide an important reference for those involved in the electronics or technology field.
What are ABF GL102R8HF Package Substrates?
ABF GL102R8HF packaging substrate is a highly critical electronic component commonly used in various electronic devices. It is a flat substrate made of an insulating material, most commonly fiberglass reinforced epoxy laminate (FR4). On this substrate, various electronic components are mounted and connected to each other to build various circuits. These components may include processors, sensors, integrated circuits, and other necessary devices.
The manufacture of ABF GL102R8HF packaging substrates is usually a complex process. First, the surface of the substrate is coated with a layer of copper foil. Then, during the photolithography process, the designed circuit pattern will be transferred to the substrate surface. Subsequently, through chemical etching, the excess copper foil is removed, leaving only the designed circuitry. Next, the electronic components are installed into specific locations through processes such as welding. Finally, tests are performed to ensure proper operation of the circuit.
ABF GL102R8HF packaging substrates are widely used in various fields. This substrate is used in almost all electronic devices, from consumer electronics such as smartphones and tablets to industrial equipment and medical devices. They provide stable and reliable support for the functions of electronic devices and can meet the needs of different application scenarios.
Overall, ABF GL102R8HF packaging substrate plays a vital role in electronics manufacturing. They not only provide necessary support for electronic devices, but also provide the basis for innovation and technological progress.
ABF GL102R8HF Package Substrates design Reference Guide.
The ABF GL102R8HF Packaging Substrate Design Reference Guide is a comprehensive manual tailored for engineers and designers involved in PCB layout design. The purpose of this guide is to provide best practices, design rules, software tools, and techniques that are essential for efficient and reliable PCB design.
In this reference guide, engineers and designers will find a range of important information on the design of ABF GL102R8HF packaging substrates. First, the guide will detail the basic concepts and characteristics of the ABF GL102R8HF packaging substrate, including important information on its materials, dimensions, manufacturing processes, and more. These basics are critical to understanding how to design effectively.
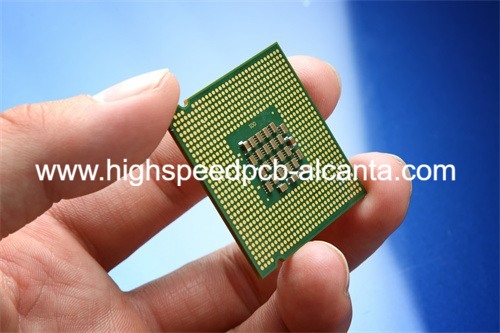
ABF GL102R8HF Package Substrates Manufacturer
Second, reference guides will provide best practices and design rules to ensure design reliability and performance. These rules cover aspects such as routing, pinout, signal integrity, and more to help designers avoid common design problems and ensure that designs meet expected requirements.
In addition, this guide will also introduce some commonly used software tools and technologies, such as CAD software, simulation tools, etc., that can help engineers and designers perform PCB design work more efficiently. By becoming proficient in these tools and techniques, designers can increase work efficiency and shorten design cycles.
Finally, the ABF GL102R8HF Packaging Substrate Design Reference Guide will also provide some practical case studies and application examples to help engineers and designers better understand how to apply theoretical knowledge to actual designs. These cases will demonstrate design methods and techniques in different application scenarios, providing designers with valuable experience and inspiration.
In short, the ABF GL102R8HF packaging substrate design reference guide will provide comprehensive and practical guidance for engineers and designers engaged in PCB layout design, helping them achieve efficient and reliable PCB design and promote the development and innovation of the electronics industry.
What material is used in ABF GL102R8HF Package Substrates?
ABF GL102R8HF packaging substrates are vital components of modern electronic devices, and their performance and reliability are largely dependent on the materials used. Typically, the main materials used in ABF GL102R8HF packaging substrates include FR4 and polyimide.
FR4 (fiberglass reinforced epoxy laminate) is a common PCB substrate material that is widely used in the manufacture of ABF GL102R8HF packaging substrates. It has excellent electrical insulation properties and mechanical strength, and can maintain stable performance under various environmental conditions. FR4 panels are laminated with fiberglass cloth and epoxy resin substrate. This structure makes it have good high temperature resistance and chemical corrosion resistance, making it suitable for various application scenarios.
Additionally, there is an increasing demand for flexible PCBs, especially in applications that require curved or curved designs. In these cases, polyimide is a common choice. Polyimide has excellent flexibility and high temperature resistance, allowing it to maintain stable electrical properties despite bending and deformation. Therefore, for some special applications, such as wearable devices, flexible displays, and medical equipment, ABF GL102R8HF packaging substrate may use polyimide as the substrate material.
In general, the material selection of ABF GL102R8HF packaging substrate is crucial, as it directly affects the performance, reliability and scope of application of electronic equipment. The use of high-quality materials such as FR4 and polyimide ensures that the ABF GL102R8HF packaging substrate performs well in a variety of application scenarios and meets user needs and expectations.
What size are ABF GL102R8HF Package Substrates?
ABF GL102R8HF packaging substrate dimensions vary depending on its specific application. They come in a wide range of sizes, from micro PCBs, such as those used in small electronics such as smartphones and wearable devices, to large PCBs, such as those used in industrial equipment or power electronics.
For micro PCBs, the size is usually very small because products such as smartphones, wearable devices, etc. require compact designs to meet the needs of portability and lightness. These PCBs need to accommodate a variety of electronic components, including processors, memories, sensors, etc., in extremely limited space, so they are typically only a few square centimeters in size and may feature multi-layer designs to increase wiring density.
In contrast, large PCBs used in industrial equipment or power electronics may require larger dimensions. These PCBs may need to accommodate more electronic components such as high-power processors, converters, sensors, etc., and often require more space for thermal dissipation and electromagnetic compatibility. Therefore, their size may reach tens of square centimeters or even larger.
Overall, the size of the ABF GL102R8HF packaging substrate depends on the specific electronic component size and the space available within the device. Design engineers need to size the PCB based on the requirements and constraints of the specific application to ensure it can be effectively integrated into the final product and meet performance and functional requirements.
The Manufacturer Process of ABF GL102R8HF Package Substrates.
The manufacturing process of ABF GL102R8HF packaging substrate is a precise and complex process that requires multiple critical steps to ensure that the quality and performance of the final product meet the design requirements. Below is a detailed description of the manufacturing process:
Substrate Preparation: The first step in the manufacturing process is substrate preparation. At this stage, substrate materials that meet the requirements are selected, cleaned and pre-treated to ensure that the flatness and roughness of the surface meet the requirements.
Copper Layer Deposition: Next is the deposition of the copper layer. This step involves depositing copper foil or copper film onto the surface of the substrate to form a conductive layer that provides the basis for subsequent circuit routing and connections.
Application and exposure of photoresist: In the photolithography process, a layer of photoresist is coated on the copper layer and exposed using a photolithography machine to transfer the designed circuit pattern to the photoresist.
Etching: After exposure, the substrate is placed in the etching solution. The portions not covered by the photoresist will be etched away, exposing the substrate beneath the copper layer. This results in the designed wire and pad pattern.
Drilling: Use a CNC drill to drill holes at designated locations so that they can be connected to the conductor layer during subsequent component installation.
Component mounting: Mounting electronic components on a substrate, which may involve a manual or automated process, depending on the equipment and technology level of the production line.
Soldering: After the components are installed, soldering is performed to ensure a good connection between the components and the substrate. This may involve traditional soldering techniques or surface mount technology (SMT).
Testing: The final step in the manufacturing process is testing the completed PCB. This includes functional, electrical and reliability testing to ensure the product meets specifications and operates reliably.
During the manufacturing process, some advanced technologies, such as surface mount technology (SMT) and plug-in mounting, may be used based on design requirements to meet different wiring and connection needs. Through strict quality control and precise process flow, ABF GL102R8HF packaging substrate can ensure reliable performance and stable electrical connections in various application scenarios.
The Application area of ABF GL102R8HF Package Substrates.
ABF GL102R8HF packaging substrates play a vital role in various industries today. Its application range is wide, covering fields such as consumer electronics, communications, automobiles, aerospace, medical equipment and industrial automation. The following are the main applications of ABF GL102R8HF packaging substrates in these industries:
In the field of consumer electronics, ABF GL102R8HF packaging substrates are widely used in various electronic devices, such as smartphones, tablets, smart home devices, and personal audio devices. They provide a compact circuit layout and reliable electrical connections, ensuring device performance and stability.
In the field of communications, ABF GL102R8HF packaging substrates are used to manufacture various communications equipment and network equipment, including base station equipment, routers, switches and optical fiber communication equipment. They provide high-density circuit layout and reliable signal transmission for communication equipment to meet the growing communication needs.
In the automotive industry, ABF GL102R8HF packaging substrates are widely used in automotive electronic systems, such as engine control units (ECUs), in-car entertainment systems, body control modules and safety systems. They provide stable performance under harsh environmental conditions, ensuring vehicle safety and reliability.
In the aerospace sector, ABF GL102R8HF packaging substrates are used to manufacture electronic systems for aerospace equipment such as aircraft, satellites and spacecraft. They are lightweight, strong and radiation resistant, making them suitable for use in harsh aerospace environments.
In the field of medical equipment, ABF GL102R8HF packaging substrates are used in various medical equipment, such as pacemakers, medical imaging equipment, monitoring instruments and surgical robots. They provide highly reliable circuit connections and precise signal transmission, ensuring the safety and stability of medical equipment.
In the field of industrial automation, ABF GL102R8HF packaging substrates are used to manufacture various industrial control equipment and automation systems, such as PLC (programmable logic controller), sensor controllers, robot control systems and industrial machine vision systems. They have highly reliable electrical connections and anti-interference capabilities, making them suitable for the complex requirements of industrial production environments.
In summary, ABF GL102R8HF packaging substrate plays a key role in industries such as consumer electronics, communications, automotive, aerospace, medical equipment, and industrial automation, and is an essential component of various electronic devices.
What are the advantages of ABF GL102R8HF Package Substrates?
ABF GL102R8HF packaging substrate has obvious advantages in electronic equipment manufacturing, mainly reflected in the following aspects:
The first is compactness. Compared to other wiring methods, the ABF GL102R8HF packaging substrate allows for a more compact layout, effectively miniaturizing electronic devices. This is particularly important for today’s pursuit of thin, light and portable consumer electronics products, which can make the device smaller and more convenient to carry while ensuring functional integrity.
Second is reliability. ABF GL102R8HF packaging substrates use standardized manufacturing processes to ensure consistent quality and reliability. This means that whether one or thousands of substrates are produced, the quality is reliable and users can use it with confidence.
The third is the ease of assembly. The automated assembly process greatly simplifies the production process, reduces labor costs, and improves production efficiency. This allows manufacturers to complete large-scale production more quickly and reduces the impact of human factors on product quality.
In addition, the ABF GL102R8HF packaging substrate has good customizability. Designed according to specific requirements, including complex circuits and component integration, allowing it to meet the needs of different products. This flexibility allows the substrate to adapt to various application scenarios, providing more possibilities for product development and innovation.
Finally, there is cost effectiveness. Large-scale production reduces unit costs, making the ABF GL102R8HF packaging substrate economical to manufacture at large scale. This allows manufacturers to offer products at more competitive prices while increasing profit margins without sacrificing quality.
In summary, ABF GL102R8HF packaging substrate has become an indispensable and important component in the field of electronic equipment manufacturing due to its advantages such as compactness, reliability, ease of assembly, customizability and cost-effectiveness, driving the development and development of the industry. Innovation.
FAQ
What applications are BF GL102R8HF packaging substrates suitable for?
ABF GL102R8HF packaging substrates are suitable for a wide range of applications, including but not limited to consumer electronics, communications equipment, automotive electronics, medical equipment and industrial control. Its high density and reliability make it ideal for many electronic devices.
What are the dimensions and thickness of the ABF GL102R8HF packaging substrate?
The size and thickness of the ABF GL102R8HF packaging substrate can be customized according to specific needs. Common sizes range from a few millimeters to tens of centimeters, while thicknesses typically range from tens of microns to several millimeters.
What is the manufacturing process of ABF GL102R8HF packaging substrate?
The process of manufacturing the ABF GL102R8HF packaging substrate includes steps such as substrate preparation, copper layer deposition, pattern photolithography, etching, drilling, metallization, component mounting and testing. Each step is precisely controlled to ensure the quality and performance of the final product.
How is the ABF GL102R8HF packaging substrate different from other types of substrates?
ABF GL102R8HF packaging substrates offer higher density and better performance than other substrates such as FR4 substrates. They are often used in applications requiring high-speed signal transmission and complex layouts, and have better thermal management capabilities.