5G Package Substrate Manufacturer.”5G Package Substrate Manufacturer” refers to a company specializing in the production of advanced substrates crucial for 5G technology, ensuring high-speed connectivity and reliability in electronic devices.
Among the rapidly developing communication technologies, 5G technology is becoming the focus of global attention. The key to 5G communications lies in advanced packaging technology, in which 5G package substrate (Package Substrate) plays an important role. This article will delve into the definition, design, materials, manufacturing processes, application areas and advantages of 5G packaging substrates, aiming to provide readers with a comprehensive understanding.
What is 5G Package Substrate?
5G packaging substrate is a key electronic component designed to support and connect high-frequency, high-speed 5G communication equipment. It plays an important role in modern communication technology, not only providing stable electrical connections, but also effectively managing heat and achieving isolation functions.
In the context of 5G networks, data transmission speeds and frequencies have increased significantly, so packaging substrates must have specific functions and performance. First of all, it needs to be able to support high-frequency signal transmission to ensure the stability and reliability of data in a high-speed network environment. Through optimized design and selection of appropriate materials, such as high-frequency FR4 materials, 5G packaging substrates can effectively reduce signal attenuation and crosstalk, thereby improving communication efficiency.
Secondly, the 5G packaging substrate also undertakes the important tasks of heat dissipation and isolation. High-speed transmission and processing of large amounts of data will generate a lot of heat, and good heat dissipation design can effectively conduct and disperse the heat to maintain the stability and reliability of the equipment when operating under high loads. At the same time, the isolation function of the packaging substrate can prevent electromagnetic interference (EMI), ensure that different signals do not interfere with each other, and improve the overall performance of the system.
The design and manufacturing of 5G packaging substrates requires a high degree of technical complexity and precision. The manufacturing process involves the selection of substrate materials, optimization of circuit layout, deposition and etching of metal layers, and precise installation of components. Advanced surface mount technology (SMT) and through-hole technology (Through-Hole) are widely used to meet the requirements for miniaturization, high performance and reliability of complex electronic devices.
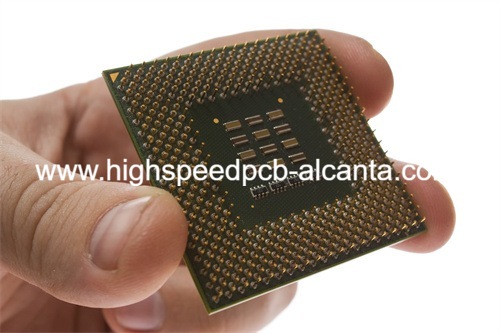
5G Package Substrate Manufacturer
In short, 5G packaging substrate is not only a core component of 5G communication equipment, but also an important technical support for promoting the development of 5G technology. By providing stable electrical connections, optimized signal transmission, effective thermal management and reliable electromagnetic isolation, it provides a solid foundation and key guarantee for the rapid development and intelligent application of modern communication technology.
5G Package Substrate design Reference Guide.
The rapid development of 5G communication technology has promoted the design and application of 5G package substrate (Package Substrate) to become the focus of electronic engineers and designers. In order to ensure the stability and reliability of 5G equipment under high frequency and high speed conditions, reference guidelines for designing 5G packaging substrates are crucial.
When designing 5G packaging substrates, best practices are the foundation. This includes understanding and following design principles applicable to high-frequency and high-speed circuits, such as reducing losses and crosstalk in signal transmission, optimizing power transfer efficiency, and effectively managing heat and electromagnetic interference.
Design rules play a key role in ensuring 5G packaging substrate design accuracy and performance optimization. These rules cover aspects such as trace width and spacing, layer spacing, impedance control, component placement and packaging selection to ensure signal integrity and electrical characteristics meet specification requirements.
Modern design software tools are an integral part of the design process. These tools can simulate and verify circuit layout, optimize routing paths, perform electrical characterization analysis, and generate documentation and files required for manufacturing. Commonly used software includes Cadence Allegro, Mentor Graphics PADS, Altium Designer, etc.
Layout technology directly affects the performance and reliability of 5G packaging substrates. Good layout techniques should include sensible component placement, minimizing signal path lengths and crossovers, effectively managing electromagnetic compatibility (EMC), and ensuring proper thermal design.
The goal of the 5G Packaging Substrate Design Reference Guide is to provide engineers and designers with clear guidance to help them overcome design challenges in 5G communications and ensure that the design achieves the expected efficiency and reliability. By in-depth understanding and application of these guidelines, designers can better achieve innovation, optimize designs, and promote the widespread application and development of 5G technology around the world.
What material is used in 5G Package Substrate?
5G packaging substrate plays a key role in modern communication technology, and its selection of materials is crucial to ensuring device stability and performance. Typically, 5G packaging substrates use high-frequency FR4 material, which is a glass fiber-reinforced epoxy laminate. High-frequency FR4 is known for its excellent electrical insulation properties and mechanical strength, and is particularly suitable for the needs of high-frequency 5G applications.
First of all, the electrical insulation properties of high-frequency FR4 materials are extremely excellent. In the 5G communication frequency band, the signal transmission speed and frequency are very high, requiring the packaging substrate to effectively isolate and maintain signal integrity. The low dielectric constant and dielectric loss angle of high-frequency FR4 are the key to maintaining signal stability under high-frequency conditions. This material can effectively reduce signal transmission loss and improve the reliability and efficiency of data transmission.
Secondly, high-frequency FR4 materials have superior mechanical strength and can withstand various environmental challenges and physical pressures that equipment may encounter when operating. This mechanical strength not only ensures the stability of the packaging substrate during assembly and use, but also extends the service life of the equipment. In addition, high-frequency FR4 materials also have good heat resistance and chemical resistance, adapting to application needs in various complex environmental conditions.
For design engineers and manufacturers of 5G packaging substrates, choosing high-frequency FR4 materials is not only a technical advantage, but also an economically wise move. The widespread application of high-frequency FR4 makes it highly accessible and cost-effective in the market, which facilitates mass production.
In short, high-frequency FR4 material is the preferred material for 5G packaging substrates. Its excellent electrical properties and mechanical properties ensure that 5G equipment can operate stably and transmit data in high-speed and high-frequency communication environments. In the future, with the further popularization and application expansion of 5G technology, high-frequency FR4 materials will continue to play an important role, providing a solid foundation and support for innovative development in the communications field.
What size are 5G Package Substrate?
The rapid development of 5G communication technology has promoted the diversification and highly specialization of package substrates (Package Substrate). Packaging substrate plays a key role in 5G equipment, and its size and shape depend on specific application needs and technical requirements.
First, for micro packaging, such as 5G modules used in smartphones and wearable devices, the packaging substrate is usually designed to be very small and delicate. This kind of micro-package needs to integrate multiple functions in a limited space, such as processors, communication chips, radio frequency modules, etc., so the packaging substrate must have a high degree of integration and excellent thermal management capabilities. At the same time, in order to adapt to the thin and light design trend of mobile devices, these packaging substrates often need to have high mechanical strength and durability.
Secondly, for larger packaging substrate applications, such as high-power, high-frequency equipment such as industrial equipment and 5G base stations, the size of the packaging substrate becomes wider and more complex. These applications require more space to accommodate multiple large components and more complex circuit designs, while also requiring the packaging substrate to have excellent electrical and thermal properties as well as good signal transmission and impedance control capabilities. In industrial environments, these packaging substrates also need to be able to withstand harsh working conditions and frequent equipment operations to ensure long-term stable performance and reliability.
Regardless of size, the design and manufacturing of 5G packaging substrates must strictly follow highly technological processes and precise dimensional control. Advanced manufacturing technologies such as surface mount technology (SMT) and high-precision CNC drilling equipment enable packaging substrates to achieve complex layouts and multi-level connection structures at the micron level to meet the challenges of different size and performance requirements.
In summary, 5G packaging substrates come in a wide range of sizes, from tiny to huge, adapting to the needs of different 5G application scenarios. The design and manufacturing of these packaging substrates is not only related to the functionality and performance of the equipment, but also directly affects the stability and efficiency of the entire 5G communication network. As 5G technology continues to evolve and application scenarios expand, packaging substrates will continue to play a key role in promoting the progress and development of global communications technology.
The Manufacturer Process of 5G Package Substrate.
The manufacturing process of 5G packaging substrate is a complex and precise process involving multiple key steps. Each step is crucial and directly affects the quality and performance of the final product.
First, the fabrication process starts with substrate preparation. High-frequency FR4 or similar material substrates are usually used. These materials have excellent electrical properties and mechanical strength and are very suitable for high-frequency 5G applications. The substrate preparation stage ensures that the surface is smooth, clean, and pre-treated to facilitate smooth progress of subsequent process steps.
Next comes the copper layer deposition. A thin layer of copper is applied to the surface of the substrate. This layer of copper will be used to form conductive paths and solder joints to support the functionality of the circuit board. The uniformity and thickness control of the copper layer are critical for subsequent photolithography and etching processes to ensure the accuracy and stability of the circuit.
Photolithography and development are one of the key steps in the manufacturing process. The desired circuit pattern is formed by coating the copper layer with photoresist, exposing it using a photolithography mask, and then developing to remove the unexposed portions of the photoresist. This step determines how the board will be routed and connected.
This is followed by etching, which chemically removes the copper layer not protected by photoresist, leaving behind the required wires and connectors. Precise control of the etching process and good waste disposal are crucial for environmental protection and resource utilization.
Drilling is to create holes at specific locations and levels for subsequent component installation and circuit connections. Drilling precision and positional accuracy have a significant impact on the functionality and reliability of circuit boards.
The component mounting stage involves placing electronic components precisely at predetermined locations on the circuit board. This process can be achieved through automated surface mount technology (SMT), ensuring high efficiency and high-precision assembly. For some components, such as high-power electronic components or components that require higher mechanical strength, through-hole assembly technology (Through-Hole) may be used to ensure the firmness and reliability of the connection.
Soldering is the process of attaching components to a circuit board and forming electrical connections. Through thermal welding or other modern welding technologies, ensure the solidity of the solder joints and the stability of the electrical contacts to support long-term stable operation of the equipment.
Finally, there is the testing phase, where the functionality and performance of the board are verified through a rigorous testing process. This includes electrical testing, functional testing and possibly environmental testing to ensure the product meets design specifications and customer needs.
In summary, the manufacturing process of 5G packaging substrates not only requires advanced technology and equipment support, but also strict quality control and process management to ensure that each manufacturing step reaches high standards, thereby supporting the stability and stability of 5G communication technology. Reliability development.
The Application area of 5G Package Substrate.
As an important part of modern communication technology, 5G packaging substrate plays a key role in many fields. It not only supports high-speed and high-frequency data transmission, but also provides the necessary foundation for performance improvement and function expansion of various electronic devices. The following are the main applications of 5G packaging substrates in consumer electronics, communication equipment, automotive electronics and medical equipment:
In the field of consumer electronics, such as smartphones, tablets, smart home devices, etc., 5G packaging substrates play a key role. With the popularization of 5G technology, consumers’ demand for high-speed data transmission and smooth Internet experience continues to increase. The high-frequency transmission capabilities and compact design of 5G packaging substrates enable these devices to support faster and more stable connections, meeting modern users’ needs for instant communication and large-capacity data transmission.
In the field of communication equipment, such as base station equipment, network routers and optical fiber communication equipment, the application of 5G packaging substrates is also crucial. These devices need to be able to handle large amounts of data traffic and maintain efficient communication connections. The 5G packaging substrate provides stable high-frequency transmission and excellent thermal management capabilities through optimized circuit design and material selection, ensuring the reliability and stability of the device during long-term operation.
In the field of automotive electronics, 5G packaging substrates are widely used in vehicle infotainment systems, Internet of Vehicles communication modules and driving assistance systems. With the development of autonomous driving technology, vehicle-mounted equipment has increasingly higher requirements for high-speed and low-latency data transmission. 5G packaging substrates can meet these needs and provide reliable data processing and fast communication connections, thereby enhancing the intelligence and safety performance of vehicles.
In the field of medical equipment, such as medical imaging equipment, remote health monitoring systems and wearable medical devices, the application of 5G packaging substrates is rapidly expanding. These devices require stability and accuracy at high frequencies and high data transfer rates. 5G packaging substrates help medical equipment achieve more accurate data collection and processing by providing highly integrated circuit designs and reliable signal transmission paths, improving the efficiency and quality of medical services.
In short, the application of 5G packaging substrates in multiple fields such as consumer electronics, communication equipment, automotive electronics, and medical equipment provides key support for achieving high-speed, high-frequency data transmission and processing. With the continuous advancement of technology and the expansion of application scenarios, the importance and application scope of 5G packaging substrates will further expand, promoting the development of various industries in the direction of intelligence and high efficiency.
What are the advantages of 5G Package Substrate?
The rapid development of 5G communication technology is driving the demand for more advanced packaging technology in communication equipment. As a key component, 5G packaging substrate shows significantly different advantages from other packaging technologies in many aspects.
First of all, 5G packaging substrates have outstanding performance in high-frequency transmission capabilities. Through optimized design and selected materials, these substrates ensure stability and reliability at high frequencies. This feature is particularly important for 5G communication requirements. It can effectively reduce signal attenuation and interference and ensure fast transmission and accurate reception of data.
Secondly, the 5G packaging substrate has excellent heat dissipation effect. As the power density of equipment increases, good heat dissipation performance can effectively maintain the efficient operation of the equipment. The packaging substrate is designed to efficiently transfer heat from the electronic device to the external environment, preventing device performance degradation or damage due to overheating.
Third, 5G packaging substrates have unique advantages in integration. Its design can achieve a high degree of integration of complex circuits in a limited space, which not only saves space, but also reduces the complexity of circuit wiring and improves the stability and reliability of the overall system.
Fourth, 5G packaging substrates have a high degree of customization capabilities. Manufacturers can customize designs based on specific application scenarios and customer needs, and flexibly adjust the shape, size and circuit layout of the substrate to maximize performance and adaptability to meet the needs of different markets.
Finally, the cost-effectiveness of 5G packaging substrates is significant. With the maturity of the manufacturing process and the implementation of mass production, the cost of a single piece has been greatly reduced, making it particularly suitable for large-scale applications and the consumer electronics market. This cost-effectiveness not only promotes the popularization and application of technology, but also promotes the market competitiveness of 5G communication equipment.
To sum up, the 5G packaging substrate provides key support and driving force for the development of 5G communication technology with its significant advantages in high-frequency transmission capabilities, heat dissipation effects, integration, customization and cost-effectiveness, indicating that Its important position and broad application prospects in the future communications industry.
FAQ
What is the difference between 5G packaging substrate and traditional packaging technology?
5G packaging substrate is different from traditional packaging technology in many aspects. First of all, it needs to support higher frequency and faster data transmission, so it has stricter requirements in material selection, design layout and manufacturing process. Traditional packaging technology often cannot meet the high-frequency and high-speed requirements of 5G communication equipment, while 5G packaging substrates specifically optimize electrical performance and signal integrity to ensure the stability and reliability of data transmission.
What is high frequency FR4 material? Why use it in 5G packaging?
High-frequency FR4 material is a special glass fiber reinforced epoxy laminate with excellent electrical insulation properties and mechanical strength, and is particularly suitable for 5G packaging substrates. It can effectively control loss and interference in signal transmission, support high-frequency data transmission, and also provide good heat dissipation effects to ensure long-term stable operation of the equipment.
What are the main manufacturing steps for 5G packaging substrates?
The main steps in manufacturing 5G packaging substrates include: substrate preparation (selecting and processing substrate materials), copper layer deposition (forming a conductive layer on the substrate), photolithography and development (using a photomask to print circuit patterns onto the substrate), etching (removing unnecessary copper), drilling (reserving holes for mounting electronic components), component mounting (precisely mounting electronic components to the substrate), soldering (connecting electronic components and wires), testing (verifying circuit function and performance )wait.
What are the specific applications of 5G packaging substrates in communication equipment?
5G packaging substrates are widely used in 5G communication equipment, such as base stations, antennas, radio frequency modules, etc. They not only support high-speed, high-frequency data transmission and processing, but also maintain stability and reliability under complex environmental conditions. Through optimized design and manufacturing processes, 5G packaging substrates provide important support for the development of modern communication technology.