What is WLP Package Substrate?
WLP Package Substrate Manufacturer.The WLP Package Substrate Manufacturer specializes in crafting advanced substrates tailored for Wafer Level Packaging (WLP) applications. With cutting-edge technology and precise engineering, they produce substrates that ensure optimal performance and reliability in semiconductor devices. Their dedication to innovation and quality control makes them a trusted partner for semiconductor companies seeking top-tier packaging solutions. From materials selection to final product delivery, they uphold stringent standards, enabling the seamless integration of their substrates into diverse electronic devices, driving efficiency and performance in the ever-evolving tech landscape.
In PCB engineering, WLP Package Substrate represents an important technology, which has a profound impact on the development of electronic packaging. WLP Package Substrate is a base material used to carry semiconductor devices and provide necessary structural support and electrical connections. This technology packages semiconductor devices at the wafer level, hence its name. WLP Package Substrate plays a key role in integrating semiconductor devices onto a single substrate, providing important support for the manufacturing and design of electronic devices.
WLP Package Substrate makes electronic packaging more compact and efficient by packaging semiconductor devices at the wafer level. It provides a reliable platform for semiconductor devices, enables electrical connections between devices, and provides the structural support required for thermal management. Compared with traditional packaging technology, WLP Package Substrate has significant advantages in improving device performance and reducing packaging volume.
WLP Package Substrate plays an integral role in PCB engineering. It provides more flexibility and innovation in the design and manufacturing of electronic equipment, making the equipment more compact, lighter, and with higher performance and reliability. By using WLP Package Substrate, engineers can develop more advanced and efficient electronic devices, driving the development of the entire industry.
What types of WLP Package Substrate are there?
As an important part of PCB engineering, WLP Package Substrate covers a variety of types, each type is different in terms of materials, performance and applications.
Organic substrates are typically resin-based materials such as laminates or epoxy resins. This type of WLP Package Substrate has advantages in cost and manufacturing, and is suitable for many common application scenarios.
Ceramic substrates offer excellent thermal conductivity and reliability, making them suitable for high temperature, high frequency and high power applications. Ceramic substrates generally cost more than organic substrates, but are more suitable in specific applications.
Metal substrates have good heat dissipation properties and are suitable for electronic devices that require efficient heat dissipation. This type of WLP Package Substrate is usually used in LED lighting, power modules and other fields.
Flexible substrates provide flexibility and reliability in applications that require bending or bending. This type of WLP Package Substrate is suitable for wearable devices, curved displays, etc.
High-density interconnect substrates allow for more compact device integration and higher signal density, and are typically used in applications requiring a high degree of integration, such as smartphones, tablets, etc.
Each type of WLP Package Substrate has its unique features and advantages, and engineers should comprehensively consider them based on specific application needs and performance requirements when selecting.
What are the advantages of using WLP Package Substrate?
Using WLP Package Substrate has significant advantages over other boards, which are mainly reflected in the following aspects:
First, one of the biggest advantages of WLP Package Substrate is its superior size advantage. Compared with traditional packaging technology, WLP Package Substrate allows direct packaging of devices at the wafer level, so it has great advantages in terms of size. This means that more compact and lightweight electronic device designs can be achieved to meet the demand for thinness and lightness, especially for portable devices and embedded systems.
Secondly, WLP Package Substrate has excellent thermal management performance. Since the packaged devices are directly integrated on the substrate, the heat dissipation path is shorter and heat conduction is more efficient. This effectively reduces the heat generated by the device during operation and improves heat dissipation efficiency, thereby ensuring the long-term stability and reliability of the device.
In addition, WLP Package Substrate also performs well in terms of electrical performance. By optimizing wiring design and material selection, WLP Package Substrate can reduce signal loss and electromagnetic interference, improving the overall performance and reliability of electronic equipment. This enables WLP Package Substrate to perform well in high-frequency, high-speed and high-density applications, providing strong support for the development of advanced electronic products.
In addition, using WLP Package Substrate can also reduce manufacturing costs. Compared with traditional packaging processes, the manufacturing process of WLP Package Substrate is more simplified and efficient, reducing material waste and production time, thereby reducing overall costs. This is of great significance for large-scale production and cost-sensitive applications, and can save companies a lot of costs.
In summary, WLP Package Substrate has obvious advantages over other boards, including size advantages, excellent thermal management properties, superior electrical properties and reduced manufacturing costs. These advantages make WLP Package Substrate an important choice in the design of modern electronic equipment, promoting the continuous innovation and development of the electronics industry.
Why choose WLP Package Substrate?
In the field of electronic packaging, it is crucial to select the appropriate substrate material, and WLP (Wafer Level Packaging) Package Substrate plays an important role here. Compared with traditional boards, WLP Package Substrate has a series of unique features, making it the first choice for many application fields.
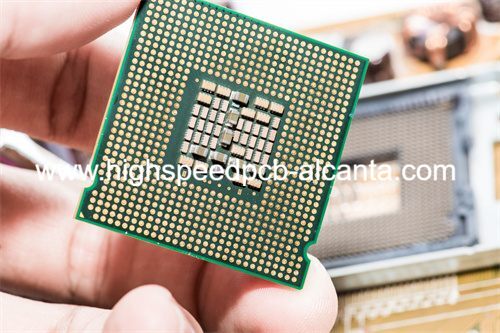
WLP Package Substrate Manufacturer
First, one of the biggest advantages of WLP Package Substrate is the higher degree of integration and density it enables. In the traditional packaging process, semiconductor chips are individually packaged and then connected to the PCB, which takes up a lot of space and limits the packaging density. In contrast, WLP Package Substrate allows packaging at the wafer level, and components are packaged and connected directly on the wafer, thereby achieving a more compact packaging structure and improving device integration and density.
Secondly, WLP Package Substrate has excellent thermal management performance. For high-power-density applications, such as automotive electronics, communication equipment, etc., thermal issues have always been a key factor restricting device performance and reliability. By packaging the device directly on the substrate, WLP Package Substrate effectively shortens the thermal path and improves heat conduction efficiency, thereby achieving better thermal management performance and ensuring the stability and reliability of the device.
In addition, WLP Package Substrate also has lower inductance and resistance, as well as shorter signal transmission paths, thereby improving signal transmission rate and reliability. This is particularly important for high-frequency applications and communication equipment, ensuring fast response and stable transmission of signals, improving equipment performance and user experience.
Finally, the manufacturing process of WLP Package Substrate is becoming increasingly mature, and the supply chain is stable and reliable. With the continuous development of technology, the manufacturing process of WLP Package Substrate has been continuously improved and optimized. At the same time, production capacity has been continuously improved and costs have been gradually reduced, providing reliable support for a wide range of application fields.
To sum up, compared with other boards, WLP Package Substrate has higher integration density, excellent thermal management performance, lower electrical performance loss and stable and reliable supply chain advantages, so it is favored in many electronic application fields. It has become the mainstream choice in today’s electronic packaging field.
What is the process of manufacturing WLP Package Substrate?
Manufacturing WLP Package Substrate is a delicate and complex process that requires multiple critical steps to complete. Below we will take an in-depth look at the process of manufacturing WLP Package Substrate:
The first step in manufacturing WLP Package Substrate is to prepare the semiconductor wafer (wafer). These wafers are usually made of silicon material and are processed and cleaned through advanced processes to ensure the flatness and purity of the surface.
Next, the wafer needs to be thinned, reducing its thickness to the desired size. This is usually achieved through techniques such as chemical mechanical polishing (CMP) or ion etching. The thinned wafer is thinner and lighter, which is beneficial to the subsequent packaging process.
The aging layer is formed on the wafer, usually using techniques such as chemical vapor deposition (CVD) or physical vapor deposition (PVD) to protect the wafer surface and provide good adhesion.
Next, an on-chip metallization layer (UBM) is formed on the wafer surface for subsequent formation of solder balls. This step ensures the reliability and stability of the electrical connection.
By applying heat and appropriate pressure to the wafer, the solder ball material (usually a tin-lead alloy) is melted and formed into a spherical shape. These solder balls are used to make connections with other components.
A supplemental layer (RDL) is formed on the surface of the wafer for signal transmission and connection between different chips. This step is usually achieved through processes such as photolithography and etching.
Finally, the completed WLP Package Substrate is finally encapsulated, usually using epoxy resin encapsulation or other protective layers to ensure the stability and reliability of the circuit board.
Through the above steps, WLP Package Substrate can be manufactured. This process requires highly sophisticated equipment and technology to ensure that the quality and performance of the finished product meet requirements.
What are the application scenarios of WLP Package Substrate?
WLP Package Substrate has a wide range of applications in various fields, and its innovation and flexibility make it an ideal choice for a variety of electronic devices. The following are the main application scenarios of WLP Package Substrate in different fields:
WLP Package Substrate is widely used in consumer electronics, such as smartphones, tablets, wearable devices and Internet of Things (IoT) devices. Due to the increasing size and performance requirements of these devices, the miniaturization and high integration characteristics of WLP Package Substrate make it a key factor in the design.
In the automotive industry, WLP Package Substrate is used in applications such as advanced driver assistance systems (ADAS), infotainment systems and vehicle electrification. Automotive electronic components have strict requirements on environmental conditions such as high temperature, high pressure and vibration, and WLP Package Substrate provides excellent thermal management performance and reliability, making it the first choice for automotive electronic design.
In the aerospace and defense fields, WLP Package Substrate is used to manufacture a variety of equipment, including avionics, radar systems, and satellite communications equipment. Since these applications have extremely high requirements for lightweight and high reliability, the features of WLP Package Substrate can meet these needs while providing excellent performance and stability.
The field of medical equipment has very strict requirements for high performance, high reliability and long-term stability, and WLP Package Substrate is being favored for its excellent thermal management and electrical performance. For example, applications such as implantable medical devices, diagnostic equipment and monitoring systems can all benefit from the features of WLP Package Substrate.
In the field of communication equipment, such as network infrastructure, base stations and optical communication equipment, WLP Package Substrate also plays an important role. Its superior electrical performance and thermal management characteristics help improve device performance and reliability while meeting the requirements of different communication standards and technologies.
Overall, WLP Package Substrate has broad application prospects in many fields, and its flexibility, reliability and excellent performance make it an indispensable part of today’s electronic engineering.
How to obtain WLP Package Substrate?
WLP Package Substrate is an indispensable and key component in modern electronic engineering. To obtain high-quality, reliable WLP Package Substrate, choosing the right supplier is crucial. Here are the factors to consider when looking for a reliable WLP Package Substrate supplier:
First, make sure the supplier you choose has a good reputation and extensive experience. When evaluating a vendor, consider its reputation within the industry, customer feedback, and relationships with other partners.
Ensure that the WLP Package Substrate provided by the supplier meets relevant quality standards and certification requirements. This includes inspecting the product’s materials, manufacturing processes, and quality control of the finished product.
Look for suppliers who can provide professional technical support and customized solutions. They should be able to understand your specific needs and provide appropriate suggestions and solutions to ensure that WLP Package Substrate is an exact match for your project.
Consider the supplier’s supply chain management capabilities and stability. A reliable supplier should be able to guarantee timely delivery and have the flexibility to respond to disruptions or changes in the supply chain.
Finally, consider the cost-effectiveness of WLP Package Substrate. Compare different suppliers and evaluate whether the prices they offer match the quality of the products and service levels.
After considering the above factors, our company, as a professional WLP Package Substrate supplier, can meet your needs. We have rich experience and a professional team dedicated to providing high-quality, reliable products and providing customized solutions to meet our customers’ specific needs. By choosing us as your supplier, you can be assured of high-quality WLP Package Substrate to provide strong support for your projects.
What is the quote for WLP Package Substrate?
The cost of WLP Package Substrate is one of the important factors affecting the manufacturing of electronic equipment. Understanding its quotation involves many aspects, including material costs, manufacturing processes, customization needs, etc. Here are some important considerations regarding the cost of acquiring WLP Package Substrate:
Material cost: Different types of WLP Package Substrate use different materials, such as organic-based materials, ceramic-based materials, etc. The cost of these materials will directly affect the final quotation. Generally speaking, the cost of ceramic-based materials is relatively high, while the cost of organic-based materials is more moderate.
Manufacturing process: The complexity of the process for manufacturing WLP Package Substrate will also affect its cost. Precision manufacturing processes require more equipment and technical support, thus increasing costs. For example, WLP Package Substrate, which is manufactured using advanced nanoprocessing technology, is relatively expensive.
Customization requirements: If the customer has special customization requirements, such as specific sizes, special materials or customized functions, the corresponding customization costs will also be included in the quotation. Customization requirements often increase costs, but can also meet customer-specific application needs.
Supplier Selection: Quotes provided by different suppliers may vary. Some suppliers may have scale advantages or advantages in manufacturing technology and therefore be able to provide more competitive quotes. Therefore, choosing the right supplier is also one of the important factors affecting the cost of WLP Package Substrate.
Quantity and lot size: Typically, the larger the purchase quantity, the lower the cost. Suppliers usually determine their quotations based on the quantity and batch size of the order, so large-volume purchases usually result in better prices.
Overall, the cost of obtaining WLP Package Substrate is affected by a variety of factors. Customers need to comprehensively consider factors such as material costs, manufacturing processes, customization requirements, supplier selection, and purchase quantities to ensure they get the best solution that meets their budget and needs.
Frequently Asked Questions (FAQs)
What distinguishes WLP Package Substrate from traditional PCB materials?
WLP Package Substrate differs from traditional PCB materials in its application at the wafer level, providing enhanced miniaturization and integration capabilities.
How does WLP Package Substrate contribute to improved thermal management?
WLP Package Substrate facilitates efficient heat dissipation, ensuring optimal thermal performance in electronic devices, particularly in high-power applications.
What are the key considerations for selecting the appropriate type of WLP Package Substrate?
Factors such as application requirements, thermal conductivity, electrical performance, and reliability play crucial roles in selecting the suitable WLP Package Substrate.
How does the manufacturing process of WLP Package Substrate differ from conventional PCB manufacturing?
The manufacturing process of WLP Package Substrate involves specialized techniques such as wafer thinning, redistribution layer formation, and underfill encapsulation, distinct from traditional PCB fabrication methods.
What are the primary applications of WLP Package Substrate in modern electronics?
WLP Package Substrate finds extensive use in various industries, including consumer electronics, automotive, aerospace, medical devices, and telecommunications, owing to its compact size and superior performance.
Can WLP Package Substrate be customized for specific project requirements?
Yes, WLP Package Substrate can be tailored to meet specific project requirements, offering flexibility in design and functionality to accommodate diverse applications.