What is Showa Denko Package substrate?
Showa Denko Package Substrate Manufacturer.Showa Denko is a leading manufacturer of package substrates, specializing in cutting-edge technology for electronic components. With a legacy of innovation spanning decades, Showa Denko stands as a pillar of reliability and excellence in the industry. Their commitment to quality craftsmanship and advanced manufacturing techniques ensures that their package substrates meet the rigorous demands of modern electronic devices. Showa Denko’s dedication to research and development continually pushes the boundaries of what is possible, making them a trusted partner for businesses seeking top-tier electronic solutions.
Showa Denko Package Substrate stands as a cornerstone in today’s electronic manufacturing realm, serving not only as a fundamental component within electronic devices but also as a vital conduit that links and bolsters key elements like chips and components. Crafted through advanced process technology, its manufacturing undergoes rigorous control, ensuring a precise and stable product. This meticulous approach lays a robust groundwork for the dependable operation of electronic goods.
The substrate boasts remarkable electrical performance characteristics. With superior thermal conductivity and electrical traits, it efficiently transmits signals and dissipates heat, guaranteeing operational stability and reliability in electronic equipment. Moreover, its compact design facilitates higher integration, enabling the accommodation of more components within a confined space, thereby enhancing device performance and functionality.
Additionally, the substrate’s material selection and process advantages confer exceptional resilience in demanding environments, such as high temperatures and pressures, catering to a myriad of complex application scenarios including automotive electronics and aerospace endeavors.
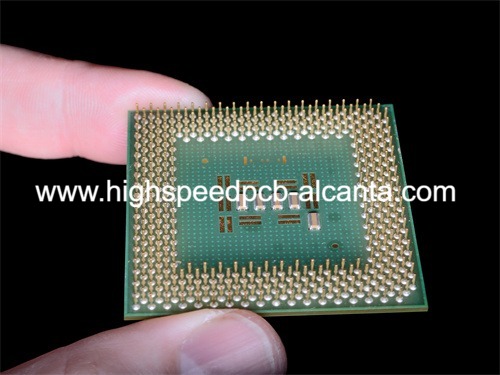
Showa Denko Package Substrate Manufacturer
In essence, Showa Denko Package Substrate stands as a linchpin material in electronic manufacturing. Its attributes and design not only foster seamless connectivity and support for crucial elements like chips and components but also underpin the performance and reliability of electronic products. By delving deeper into its characteristics and applications, we can effectively harness its potential to propel development and innovation within the electronics industry.
What types of Showa Denko Package Substrate are there?
Showa Denko Package Substrate is an essential element in electronic manufacturing, offering a diverse range of boards such as HDI boards and Rigid-Flex boards. Each variant boasts distinct design features and performance attributes, affording manufacturers flexibility and options in crafting electronic products. This article delves into the intricacies of Showa Denko’s Package Substrate types, elucidating their design nuances, performance metrics, and guidelines for selecting the optimal type based on specific requirements.
HDI board (High-Density Interconnect Board) is an important type of Showa Denko Package Substrate. Its design features are mainly reflected in the following aspects:
Highly integrated: HDI boards are highly integrated and can accommodate more components and circuits in a relatively small space. This allows electronic products to be designed more compactly and is suitable for miniaturization and lightweight application scenarios.
Multi-layer design: HDI boards usually adopt a multi-layer stack design to achieve more complex circuit connections through fine inner layer interconnections. This helps improve the board’s performance and signal transmission quality.
High-frequency applications: Because HDI boards have excellent signal integrity, they are especially suitable for high-frequency applications, such as communication equipment, wireless communication modules, etc.
Rigid-Flex board is another important type of Showa Denko Package Substrate. Its design and performance characteristics are as follows:
Rigid-flex boards seamlessly integrate rigid and flexible elements, offering a blend of stability and bendability. This unique design is particularly advantageous in applications necessitating curved forms and constrained spaces. By virtue of their flexibility, Rigid-flex boards efficiently utilize irregular spaces and accommodate specialized layouts. Furthermore, their combined rigidity and flexibility minimize connection points, enhancing system reliability and mitigating potential points of failure.
Why Choose Showa Denko Package Substrate?
The Showa Denko Package Substrate has established itself as the top choice for many customers due to its outstanding technical capabilities, consistent reliability, and tailored customization options. It effectively addresses customer concerns regarding product quality, technical assistance, and manufacturing efficiency, making it the preferred option in the market.
Renowned for its extensive R&D experience and technical strength, the company not only commands advanced production processes but also consistently introduces innovative products. This positions Showa Denko Package Substrate as a technology leader capable of meeting customers’ requirements for high performance and density.
The Showa Denko Package Substrate has established an impressive standing for its unmatched dependability. Dedicated to delivering excellence in both products and services, the company upholds rigorous quality assurance protocols to guarantee the consistency and credibility of every Package Substrate. This steadfast dedication results in lasting and dependable solutions for clientele.
Moreover, Showa Denko distinguishes itself by offering bespoke design and manufacturing services. Recognizing the distinct requirements of individual clients, the company is dedicated to crafting solutions that precisely align with their unique needs. Whether it involves tailored designs or comprehensive assistance throughout the manufacturing journey, Showa Denko provides expert technical support and customized services, guaranteeing customers achieve satisfactory outcomes.
Opting for Showa Denko Package Substrate epitomizes a wise decision. Its state-of-the-art technology, exceptional product reliability, and tailored design and manufacturing solutions have solidified its position as a trusted brand among customers. Irrespective of individual customer needs, Showa Denko guarantees the delivery of top-notch, reliable Package Substrate to enable success in today’s intensely competitive marketplace.
What is the manufacturing process of Showa Denko Package Substrate?
The production procedure of Showa Denko Package Substrate entails a meticulously orchestrated sequence aimed at attaining peak levels of product excellence and functionality. Herein, we delineate the meticulous steps involved in crafting Showa Denko Package Substrate and elucidate the methods employed to uphold the constancy of product quality and performance.
To commence, antecedent to the fabrication of Showa Denko Package Substrate, it is imperative to procure raw materials, encompassing substrate elements, metallization agents, insulation components, and the like. These materials necessitate adherence to stringent quality criteria to ensure the steadfastness and dependability of the end product.
The primary phase of the manufacturing process entails the conception and construction of the Motherboard. Serving as the cornerstone of the entire Package Substrate, the Motherboard dictates the arrangement and connectivity modalities of the circuitry. Showa Denko’s engineering cadre devises a Motherboard blueprint tailored to the client’s requisites and product specifications.
Subsequent to Motherboard fabrication is the production process of the Substrate. The Substrate serves as a pivotal element linking and supporting chips, components, and the like. Initially, a suitable substrate material is selected and subjected to processes such as cutting and polishing to yield a Substrate plate meeting specified criteria. Subsequently, metallization is executed on the Substrate’s surface to formulate circuitry connection pathways. This phase necessitates precision equipment and meticulous process oversight to ensure the requisite thickness of the metallization layer and the precision of the connecting pathways.
In the ultimate stage of the manufacturing process, the Motherboard and Substrate are amalgamated and interconnected. This stage mandates meticulous alignment and welding techniques to guarantee secure and reliable component interconnection. Simultaneously, stringent quality assessments are indispensable to ascertain conformity with design specifications and client prerequisites.
To safeguard the stability of product quality and performance, Showa Denko employs a rigorous quality management framework and quality assurance protocol. From the procurement of raw materials through manufacturing to final product delivery, multiple quality inspections and assessments are requisite to guarantee that each product batch meets exacting quality standards.
In summation, the manufacturing process of Showa Denko Package Substrate is an intricately calibrated and exacting endeavor. Through meticulous design and stringent quality oversight, we ensure that product quality and performance attain optimal levels, aligning with client needs and expectations.
In what fields is Showa Denko Package Substrate applied?
The Showa Denko Package Substrate plays a pivotal role in electronic manufacturing, finding widespread utilization across diverse sectors such as telecommunications, healthcare, automotive, and beyond. Its versatility and performance enhancements in these domains are elucidated below.
In telecommunications, the Showa Denko Package Substrate is extensively employed in equipment like smartphones, base stations, and optical networking gear. Its superior signal transmission capabilities and high-density configuration facilitate increased component integration in devices like mobile phones, ensuring robust data transmission reliability. Furthermore, its resilience to high temperatures renders it ideal for sustaining operational stability in demanding environments, such as those encountered in base station deployments.
Within the medical sphere, the Showa Denko Package Substrate finds application in a myriad of medical apparatus, including diagnostic imaging machinery and implantable devices. Its compact design and exceptional signal transmission qualities underpin advancements in equipment miniaturization and intelligence, while ensuring steadfast data transmission and control. Moreover, its reliability and ability to withstand elevated temperatures make it indispensable for medical equipment operating in rigorous conditions.
The Showa Denko Package Substrate is widely used in automotive applications, appearing in various electronic components such as electronic control units (ECUs), infotainment systems, and driver assistance mechanisms. Its high-density configuration and exceptional signal transmission properties enable the miniaturization and advancement of automotive electronics, while maintaining robustness in data handling and control. Moreover, its ability to withstand high temperatures ensures consistent performance in the automotive setting, bolstering the reliability and durability of electronic systems.
To summarize, the Showa Denko Package Substrate offers extensive versatility across telecommunications, healthcare, automotive, and other industries, serving as a crucial element in enhancing product performance and guaranteeing reliability. Its compact design, superior signal transmission capabilities, and thermal endurance position it as a preferred option for numerous electronic devices, thereby propelling industry progress and fostering innovation.
How to get Showa Denko Package Substrate?
You have a variety of avenues for acquiring Showa Denko Package Substrate. Initially, you have the option to make a direct purchase through Showa Denko’s authorized distribution channels. By reaching out to Showa Denko directly, you gain access to up-to-date product details, tailored solutions, and technical assistance. This method typically guarantees the acquisition of top-tier products, along with direct manufacturer support and assistance.
Showa Denko has many authorized agents around the world. These agents usually have close cooperation with Showa Denko and can provide localized sales and technical support. Through agents, you can obtain Showa Denko products more conveniently, reduce transaction time and costs, and get localized service and support when needed.
As your vendor, our firm also offers Showa Denko Package Substrate. We have forged a longstanding and reliable partnership with Showa Denko, enabling us to furnish you with a comprehensive service encompassing inquiry, procurement, and delivery. Through our establishment, you can streamline your purchasing process, ensuring prompt access to requisite products, accompanied by our adept technical assistance and post-sales support.
In essence, you have the option to procure Showa Denko Package Substrate either directly from Showa Denko’s official channels or through authorized agents like ourselves. Regardless of your chosen avenue, we are committed to furnishing you with premium-grade products and services tailored to your requirements, facilitating your success.
What factors affect the quotation of Showa Denko Package Substrate?
The quotation of Showa Denko Package Substrate is a complex issue that is affected by many factors. Here are some of the main factors:
Materials: The selection of materials is a critical factor in the production of Package Substrate, as it significantly influences the overall expenditure. Opting for premium-quality materials often entails increased costs, whereas opting for more economical alternatives can potentially compromise the performance and dependability of the final product.
Design complexity: The design complexity of Package Substrate is another important factor. Complex designs require more process steps and resources, increasing manufacturing costs. For example, if the design requires high-density interconnect (HDI) technology or complex multi-layer board structures, manufacturing costs may increase accordingly.
Production scale: Production scale will also have an impact on Package Substrate’s quotation. In broad terms, the economies of scale lead to a reduction in the per-unit cost of production as fixed expenses are distributed across a greater number of units. Conversely, smaller-scale production often entails higher unit costs for the product.
Technical requirements: Some special technical requirements may increase manufacturing costs. For example, if a customer requires specific technology or processing techniques, the manufacturer may need to invest additional resources to meet those requirements, affecting the final quote.
Market demand: The pricing of Showa Denko’s Package Substrate is also influenced by market demand. In instances of high demand, the manufacturer might reduce prices to attract more clients; conversely, in periods of low demand, prices may be raised to sustain profitability.
In conclusion, the pricing of Showa Denko’s Package Substrate is impacted by various elements, such as materials, design intricacy, production scale, technical specifications, and market demand. When selecting Package Substrate, customers should carefully consider these factors and engage in thorough communication with the manufacturer to ensure that the final pricing aligns with their expectations and requirements.
What are the common problems in using Showa Denko Package Substrate?
How to Choose the Right Showa Denko Package Substrate?
When selecting a Showa Denko Package Substrate, it’s essential to consider factors like application requirements, environmental conditions, and desired performance metrics. Ensuring compatibility with your specific project needs can help prevent issues down the line.
Are there specific thermal considerations that need attention when working with Showa Denko Package Substrate?
Thermal management is critical for electronic components’ longevity. Showa Denko Package Substrate users might encounter challenges related to heat dissipation. Utilizing proper heat sinks, thermal vias, and optimizing the overall PCB layout can help address thermal concerns effectively.
What components might exhibit compatibility issues with Showa Denko Package Substrate, and how can these be resolved?
Compatibility issues may arise with certain electronic components. Users should be aware of potential conflicts and ensure compatibility through thorough testing. Consulting Showa Denko’s technical support or adjusting design parameters can help resolve compatibility challenges.
Is there a risk of delamination or other structural issues with Showa Denko Package Substrate, and how can these be prevented?
Delamination and structural issues can affect the reliability of PCBs. Users may encounter such problems, especially in harsh operating conditions. Adhering to proper manufacturing processes, using suitable materials, and ensuring adherence to recommended handling guidelines can prevent delamination issues.
How can users optimize the performance of Showa Denko Package Substrate in high-frequency applications?
High-frequency applications may pose specific challenges for substrate materials. Users aiming for optimal performance in such scenarios should focus on impedance control, proper layer stacking, and utilizing advanced manufacturing techniques to meet the demands of high-frequency signals