What is POP packaging substrate?
POP Package Substrate Manufacturer.A leading POP package substrate manufacturer, renowned for its cutting-edge technology and unwavering commitment to quality. With state-of-the-art facilities and a team of seasoned experts, they specialize in crafting substrates tailored to meet the exacting demands of modern electronic packaging. Their innovative solutions cater to diverse industries, ensuring optimal performance and reliability. From design conception to production, they prioritize precision and efficiency, delivering substrates that seamlessly integrate into various applications. Trusted by top-tier clients worldwide, they continue to push boundaries, setting new standards in the ever-evolving landscape of packaging technology.
POP package substrate (Package on Package Substrate) is an advanced electronic packaging technology that stacks multiple packaging layers together to form a highly integrated packaging solution. Compared with traditional packaging technology, POP packaging substrate has higher integration and more optimized performance. It is one of the key technologies for realizing miniaturization and high performance of modern electronic products.
In traditional packaging technology, electronic components are usually packaged in a single packaging layer, while in POP packaging substrates, multiple packaging layers are stacked together vertically or horizontally. This multi-layer stacked design allows electronic components with different functions to be integrated more compactly, thereby achieving more functions in a limited space. At the same time, POP packaging substrates can also improve the performance and speed of electronic components and reduce power consumption, allowing electronic products to achieve better performance in a smaller size.
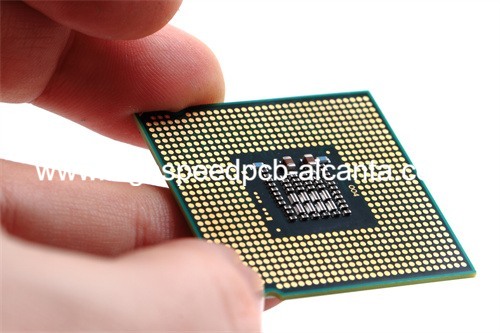
POP Package Substrate Manufacturer
In general, POP packaging substrate is an advanced packaging technology that achieves higher integration and optimized performance through multi-layer superposition design. It is one of the important technologies for realizing miniaturization and high performance of modern electronic products. .
What are the advantages of using POP packaging substrate?
As an advanced packaging technology, POP packaging substrates bring many advantages. Compared with other packaging technologies, they can significantly improve the performance and functionality of electronic components.
First, the POP packaging substrate has a higher level of integration. By stacking multiple packaging layers together, the POP packaging substrate can achieve more functions in a limited space, which means that more electronic components can be accommodated in the same size, thus improving the performance and functionality of the product. .
Secondly, POP packaging substrates can optimize the performance of electronic components. Due to the tight connection and layout between packaging layers, the delay and loss of signal transmission can be reduced, and the response speed and work efficiency of electronic components can be improved. This is particularly important for applications requiring high-speed data processing and real-time performance.
In addition, POP packaging substrates can also reduce power consumption. By optimizing the layout and connection of the packaging layer, the energy loss in the circuit can be reduced, the energy efficiency ratio of electronic equipment can be improved, and the battery life can be extended. This is particularly important for products with limited power sources such as mobile devices.
In addition, the POP packaging substrate is also conducive to the miniaturization design of the product. Compared with traditional packaging technology, POP packaging substrates are more compact in size, which can make products thinner, lighter and more portable, improve the appearance and portability of products, and meet the needs of modern consumers for fashionable and portable products.
In summary, the use of POP packaging substrates can effectively improve the performance and functions of electronic components, reduce power consumption, promote miniaturization design of products, and provide important support for the development and innovation of electronic equipment.
Why choose POP packaging substrate instead of other boards?
When designing electronic products, why choose POP packaging substrate instead of other packaging technologies? This issue relates to many aspects such as product performance, reliability and cost-effectiveness. POP packaging substrate has shown obvious advantages in many aspects, so it has become the first choice of many manufacturers and designers.
First of all, POP packaging substrate has the advantage of high integration. Due to its multi-layer packaging stack design, the POP packaging substrate can implement more functions and components in a limited space. This highly integrated feature makes the design of circuit boards more compact, providing the possibility for miniaturization of electronic products. Especially in today’s consumer electronics products that pay more and more attention to thinness, lightness and portability, the use of POP packaging substrates can better meet market demand.
Secondly, POP packaging substrates perform well in performance optimization. Due to the stacked structure of the package, the POP package substrate can more effectively reduce the signal transmission distance and increase the communication speed between electronic components, thus improving the overall performance of the product. In addition, POP packaging substrates can also reduce power consumption, making electronic products more energy-saving and efficient during use.
In addition, the POP packaging substrate also has good reliability and stability. The package stack design can effectively reduce the size of the circuit board, while increasing the connection density between components and reducing the possibility of external interference, thereby improving product stability and reliability. This is particularly important for some application scenarios that require high product performance and stability, such as industrial control systems, medical equipment and other fields.
To sum up, choosing POP packaging substrate instead of other packaging technologies is mainly due to its advantages in high integration, performance optimization, reliability and stability. With the continuous development and innovation of electronic products, POP packaging substrates will continue to play an important role, bringing more possibilities and opportunities to the electronics industry.
How are POP packaging substrates made?
Manufacturing POP packaging substrates is a precise and complex process involving multiple steps and expertise. The following is a typical process for manufacturing POP packaging substrates:
First, the process of manufacturing POP packaging substrates begins in the design phase. Designers determine the structure, layout and functionality of the packaging substrate based on the customer’s needs and specifications. During the design process, consideration needs to be given to how packaging layers are stacked, connected, and the placement of individual components to ensure that the final product meets performance and space requirements.
During the manufacturing process, it is crucial to select high-quality materials suitable for POP packaging. These materials may include substrate materials, packaging layer materials, connection materials, etc. When preparing materials, strict inspection and pre-processing are required to ensure that their quality and stability meet requirements.
Once the materials are ready, you can start laying the encapsulation layers together. This process involves precise positioning and connections to ensure alignment and stability between the various packaging layers. Typically, manufacturers use automated equipment and precision tools to complete this step to ensure production efficiency and quality.
After lamination and connection are completed, the packaging substrate usually undergoes a heat pressing and curing process. This step is intended to strengthen the connection and improve the stability and reliability of the encapsulation layer. By controlling temperature and pressure, you can ensure that the packaging substrate is not deformed or damaged during the manufacturing process.
Finally, the manufactured POP packaging substrate needs to undergo rigorous testing and verification to ensure that its performance and quality meet standard requirements. These tests may include visual inspection, electrical testing, reliability testing, etc. to ensure that the package substrate can function properly and have long-term stable performance.
To sum up, the process of manufacturing POP packaging substrates involves multiple key steps such as design, material preparation, lamination connection, hot press curing and test verification. Through precise processes and strict quality control, manufacturers can produce high-quality, reliable POP packaging substrates, providing strong support for the development and innovation of electronic products.
In what fields are POP packaging substrates used?
As an advanced packaging technology, POP packaging substrate has been widely used in many fields and has brought significant improvements to product performance in these fields.
In consumer electronics products such as smartphones, tablets, and digital cameras, POP packaging substrates are widely used. These devices require high performance and multi-function within a limited space, and POP packaging substrates can meet these needs. By using POP packaging technology, these devices can achieve higher processing speeds, lower power consumption, and have more powerful multi-tasking capabilities, thus improving the user experience.
In fields such as industrial control systems and automation equipment, POP packaging substrates are also used. Products in these fields have extremely high requirements for stability, reliability and processing capabilities, and the use of POP packaging substrates can provide higher integration and performance optimization. These advantages enable industrial control systems to respond to various control instructions more quickly and accurately, improving production efficiency and product quality.
In the field of medical equipment, the requirements for miniaturization, high performance and stability of equipment are increasing day by day, and POP packaging substrates can meet these requirements. Medical equipment often needs to integrate multiple functions within a limited space while ensuring the reliability and safety of the equipment. The use of POP packaging substrates can achieve high-performance computing, precise control and reliable operation of equipment, providing strong support for medical diagnosis, treatment and monitoring.
In addition to the above fields, POP packaging substrates are also used in professional fields such as aerospace, automotive electronics, communication equipment, etc. These fields have extremely high requirements for high performance, high reliability and long-term stable operation of electronic equipment. The use of POP packaging substrates can meet these requirements and provide more flexible solutions for various application scenarios.
To sum up, POP packaging substrates have been widely used in many fields, and by improving product performance and functions, they have provided important support for the development and innovation of these fields.
How to obtain POP packaging substrate?
Want to get POP packaging substrates to meet your project needs? Here are some avenues and how to obtain a packaging substrate that meets your needs through suppliers.
When looking for POP packaging substrates, the first thing to consider is establishing connections with professional suppliers. Often, electronic component suppliers are the most straightforward choice. By communicating directly with the supplier, you can receive expert advice and support to ensure that the packaging substrate selected meets your project needs. At the same time, suppliers can also provide detailed information about product features, technical parameters and prices to help you make a wise choice.
Another way to obtain POP packaging substrates is through the online electronic components market. Many online marketplaces offer a wide variety of electronic components, including various types of packaging substrates. By searching and comparing products and quotes from different suppliers on these markets, you can find a packaging substrate that meets your needs and purchase it conveniently.
In addition to professional suppliers and online markets, participating in electronic component exhibitions is also one of the effective ways to obtain POP packaging substrates. At these exhibitions, you can communicate face-to-face with various suppliers and manufacturers, learn about the latest product and technology trends, discover packaging substrates that meet your needs, and establish long-term cooperative relationships.
In short, if you want to obtain a POP packaging substrate that meets your needs, you can do so through a variety of ways, such as directly contacting professional suppliers, searching and comparing in the online market, and participating in electronic component exhibitions. No matter which method you choose, effective communication with your supplier and a full understanding of product characteristics are key to ensuring you receive a satisfactory packaging substrate.
What is the price of POP packaging substrate?
When selecting and purchasing POP packaging substrates, there are a series of key factors to consider. These factors not only cover the characteristics of the product itself, but are also closely linked to the market, supply chain and other factors, affecting the final price of the packaging substrate. The key factors to consider when purchasing POP packaging substrates and how these factors affect the price will be discussed in detail below.
The specifications and performance of POP packaging substrate are the primary factors that determine the price. Different specifications and performance requirements will lead to different choices of production processes, materials and technologies, thus affecting manufacturing costs. Generally speaking, packaging substrates with high performance and special specifications tend to be more expensive.
The production process and materials used of the packaging substrate will directly affect the cost. Advanced production processes and high-quality materials usually mean higher manufacturing costs, thus affecting the final sales price. Choosing appropriate production processes and materials is an important part of finding a balance between performance and cost.
Different manufacturers and supply chains may have different pricing strategies. Some well-known manufacturers usually set higher prices because of their technical strength and quality assurance, while some emerging manufacturers may attract customers with competitive prices. In addition, the stability of the supply chain will also have a certain impact on prices.
Purchase quantity and delivery time are also important factors affecting the price of POP packaging substrates. Generally speaking, large-volume purchases can enjoy more competitive prices, while urgent delivery may require higher fees to ensure timely delivery.
Market demand and competitive conditions are also key factors affecting price. When market demand is high, suppliers may adjust prices to respond to market changes. At the same time, competition among different suppliers will also have an impact on the price of packaging substrates.
Some suppliers may offer additional technical support and after-sales services, which are often reflected in the product price. Buyers can evaluate the value of these services based on their own needs and consider whether they are worth the extra cost.
To sum up, when purchasing POP packaging substrates, you need to comprehensively consider multiple factors such as specifications, performance, production processes, materials, manufacturers, purchase quantity, delivery time, market competition, and technical support. Through rational evaluation and selection, buyers can better meet project needs and control the price of packaging substrates within a reasonable range.
Frequently Asked Questions FAQS
What is POP Package Substrate?
POP Package Substrate refers to an advanced packaging technology that involves stacking multiple packaging layers together to create a compact and high-performance packaging solution for electronic components.
What are the types of POP Package Substrate?
There are two main types of POP Package Substrate: Vertical Stack and Horizontal Stack. Vertical Stack involves stacking two packaging layers vertically, while Horizontal Stack involves stacking two packaging layers horizontally.
What are the advantages of using POP Package Substrate?
Using POP Package Substrate offers several advantages, including higher integration, optimized performance, and space-saving design. It allows for increased functionality in a smaller form factor and improved overall performance of electronic devices.
Why choose POP Package Substrate over other boards?
POP Package Substrate offers higher integration and performance optimization compared to traditional packaging solutions. Its compact design and improved performance make it ideal for modern electronic devices requiring high functionality in a small footprint.
How is POP Package Substrate manufactured?
Manufacturing POP Package Substrate involves several steps, including design and layout, material preparation, stacking and bonding, and testing and validation. These steps ensure the production of high-quality POP Package Substrate that meets industry standards.