What is PGA Package Substrate?
PGA Package Substrate Manufacturer.PGA Package Substrate Manufacturer, High speed and high frequency materials Substrates supplier, BT Core, Showa Denko Core/Ajinomoto core high-speed substrates, specializes in small pitch Package Substrates and HDI PCBs.
In modern PCB engineering, PGA (Pin Grid Array) Package Substrate is regarded as a key component in the field of electronic packaging. It is a substrate used to carry integrated circuits, providing solid connections and structural support for electronic components. The core design of PGA Package Substrate is to achieve high-density wiring and reliable connections, allowing the circuit board to accommodate more pins and provide more stable signal transmission.
The importance of PGA Package Substrate is self-evident. In modern electronic products, especially high-performance computers, communication equipment and consumer electronics, more integrated circuits and components need to be carried to achieve more complex functions and performance. PGA Package Substrate provides a reliable foundation for these electronic products through its excellent signal transmission characteristics, reliable connectivity and stable structural support.
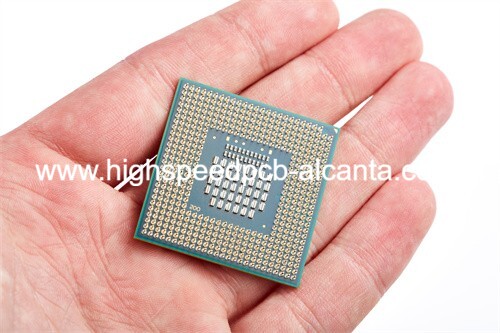
PGA Package Substrate Manufacturer
In addition, PGA Package Substrate also plays an important role in packaging and heat dissipation management of large-scale integrated circuits. They have excellent thermal conductivity properties and can help effectively disperse the heat generated by integrated circuits and maintain the stable performance of electronic products.
Overall, PGA Package Substrate plays an integral role in modern PCB engineering. They not only provide support and connections for electronic components, but also provide critical support for the performance, reliability and stability of electronic products. With the continuous development of electronic products and the improvement of intelligence level, the importance of PGA Package Substrate will become increasingly prominent.
What types of PGA Package Substrate are there?
PGA (Pin Grid Array) Package Substrate is a key component in the field of modern electronic packaging. It has many types, each type has its unique characteristics and advantages.
Organic PGA substrate is a common type of PGA Package Substrate, which usually uses epoxy resin as the base material. This type of substrate has the advantages of lightweight, low cost and good processability, making it suitable for most consumer electronics.
Ceramic PGA substrate uses ceramic material as the base material, which has excellent thermal conductivity and mechanical strength, so it performs well in high temperature and high frequency applications. They are commonly used in automotive electronics, medical devices and aerospace.
Metal substrates use metal materials (such as aluminum or copper) as the base material, which have excellent heat dissipation properties and are suitable for electronic products with high heat dissipation requirements, such as LED lighting and power modules.
The flexible PGA substrate is made of flexible materials (such as polyester film) and has excellent flexibility and bendability. It is suitable for applications that require bending or folding, such as wearable devices and flexible electronic products.
Each type of PGA Package Substrate has specific advantages and scope of application, and choosing the appropriate type depends on specific application needs and performance requirements. Therefore, when designing electronic products, engineers need to consider various factors to ensure that the most suitable PGA Package Substrate type is selected to achieve the best performance and reliability.
What are the advantages of PGA Package Substrate?
PGA Package Substrate has many advantages over traditional boards. These advantages not only improve the performance of electronic products, but also promote technological progress in the field of PCB engineering. Here are its main advantages:
First of all, PGA Package Substrate performs outstandingly in thermal management. Due to the increasing integration and power density of modern electronic devices, thermal issues have become increasingly prominent. PGA Package Substrate uses optimized thermal conductive materials and designs to effectively dissipate heat, helping to reduce the operating temperature of components and improve system stability and reliability.
Secondly, PGA Package Substrate has excellent characteristics in terms of electrical performance. Through precise wiring and design, PGA Package Substrate can reduce loss and delay during signal transmission and improve the signal integrity and performance of electronic products. This advantage is particularly important for high-frequency applications and systems with high data transmission rate requirements.
In addition, the structural design of PGA Package Substrate is flexible, diverse and highly adaptable. Designers can choose different types of PGA Package Substrate, such as organic, ceramic, or metal substrates, as well as flexible substrates, based on the requirements of specific applications to achieve the best balance of performance optimization and space utilization.
In addition, the manufacturing process of PGA Package Substrate is becoming increasingly mature and the production efficiency is high. Modern manufacturing technology makes the manufacturing process of PGA Package Substrate more precise and controllable, greatly shortening the production cycle and improving product quality and consistency. This provides strong support for the rapid development and launch of electronic products.
Finally, the cost-effectiveness of PGA Package Substrate is obvious. Although there may be a higher initial investment in some aspects, the overall cost of PGA Package Substrate is generally more competitive given the performance benefits and long-term stability it provides. This makes it ideal for a variety of electronic products, especially for applications requiring high performance and reliability.
To sum up, PGA Package Substrate has brought revolutionary changes to the design and manufacturing of electronic products and contributed to the development and innovation of the industry with its superior thermal management, electrical performance, flexible design, efficient manufacturing and cost-effectiveness. Injected new vitality.
Why use PGA Package Substrate?
In modern PCB engineering, choosing the right substrate is critical to product performance and reliability. As an advanced option, PGA Package Substrate has many advantages over traditional boards, especially in specific scenarios, its application is more suitable.
First, PGA Package Substrate has significant advantages in thermal management. Due to its structural design and material properties, the PGA substrate is able to disperse and conduct heat more effectively, allowing electronic components to maintain stable operation in high-temperature environments. This makes PGA Package Substrate particularly suitable for high-performance equipment, enclosed spaces, and scenarios that require long-term stable operation, such as automotive electronic systems, aerospace equipment, etc.
Secondly, PGA Package Substrate has excellent electrical performance. Due to its special structural design and material selection, the PGA substrate can provide more stable signal transmission and lower signal loss, thus ensuring the reliability and stability of electronic equipment. This makes PGA Package Substrate have broad application prospects in high-frequency applications, communication equipment and other fields that require high signal quality.
In addition, the structural design of PGA Package Substrate allows higher density component layout and smaller size circuit boards. This gives PGA substrates significant advantages in lightweight, compact design and miniaturized products, such as applications in consumer electronics such as smartphones and wearable devices.
In general, PGA Package Substrate has superior thermal management capabilities, electrical performance, and size advantages compared to other boards, making it more suitable in high-temperature environments, high-frequency applications, and scenarios with high product size requirements. . Therefore, when selecting a substrate, taking into account the specific needs of the product and the working environment, PGA Package Substrate can often provide a more reliable and higher-performance solution.
How to make PGA Package Substrate?
The manufacturing of PGA Package Substrate is a complex and precise process involving multiple steps to ensure its accuracy and consistency. The following is an overview of the manufacturing process of PGA Package Substrate:
The first step in the manufacturing process is to prepare the substrate. This may involve selecting an appropriate substrate material, such as an organic, ceramic or metal substrate, cutting and cleaning according to application needs, ensuring the surface is flat and free of contamination.
Next, a layer stacking process creates a multi-layered structure on the substrate. This involves applying a thin film or coating to the surface of a substrate and then stacking the different layers together to form a composite structure. Each layer has specific functionality and circuit layout, which requires a high degree of precision and accuracy.
Once the layer stacking is complete, next is the process of circuit patterning. This involves using photolithography or similar techniques to define circuit patterns on a stacked structure. These patterns will determine the connections and functionality of the circuit and therefore must be positioned and defined very accurately.
After completing the circuit patterning, the next step is the metallization process. This involves depositing metal into the openings of the circuit pattern to create conductive paths. Commonly used metals include copper, nickel, gold, etc., which provide good electrical conductivity and corrosion resistance.
Once circuit metallization is complete, the surface needs to be treated to improve its durability and solderability. This may involve applying overlays or pads to ensure that electronic components can be reliably connected to the PGA Package Substrate.
The final stage of the manufacturing process involves inspection and testing of the PGA Package Substrate. This includes using high-precision equipment to check the integrity of circuit connections, surface quality and overall performance. Any defects or issues discovered will be corrected or repaired to ensure the quality and reliability of the final product.
Through the above steps, the manufacturing process of PGA Package Substrate is completed. Each step must be precisely controlled and managed to ensure that the final product meets design requirements and has stable performance.
What are the applications of PGA Package Substrate in various industries?
As an important part of modern PCB engineering, PGA Package Substrate plays a key role in various industries. The following will discuss its applications in consumer electronics, automobiles, aerospace, medical equipment, communications and other fields and its improvement in product performance.
In the field of consumer electronics, PGA Package Substrate is widely used in products such as smartphones, tablets, and smart wearable devices. By using PGA Package Substrate, these devices can achieve higher integration and smaller size, thereby improving device performance and portability and meeting consumer demand for portable electronic products.
In the automotive industry, PGA Package Substrate is used in vehicle electronic systems, such as engine control units (ECUs), vehicle entertainment systems, navigation systems, etc. PGA Package Substrate has good vibration resistance and high temperature resistance, can adapt to the harsh requirements of the automotive working environment, and improves the reliability and stability of the vehicle electronic system.
In the aerospace field, PGA Package Substrate is used in aerospace electronic equipment, such as flight control systems, radar systems, satellite communication systems, etc. Its lightweight and high-strength characteristics make the equipment more suitable for spacecraft carrying requirements, and its high performance ensures the stable operation of the equipment in extreme environments.
In the field of medical equipment, PGA Package Substrate is widely used in various medical equipment, such as medical imaging equipment, implantable medical equipment, vital sign monitoring equipment, etc. The high integration and high performance of PGA Package Substrate help improve the accuracy and reliability of medical equipment, while meeting the medical industry’s requirements for equipment accuracy and stability.
In the field of communications, PGA Package Substrate is used in communications infrastructure, network equipment, optical communication equipment, etc. Its high frequency characteristics and excellent signal transmission performance can meet the needs of communication equipment for high-speed data transmission, and its high reliability ensures the stable operation of the communication network.
To sum up, PGA Package Substrate is widely used in industries such as consumer electronics, automobiles, aerospace, medical equipment, and communications. Its excellent performance helps improve the performance and reliability of products in various industries, and promotes modern The development and progress of science and technology.
Where can I find PGA Package Substrate?
Finding a trustworthy PGA Package Substrate supplier is crucial to ensure the successful implementation of the project and the reliability of product quality. As representatives of our company, we are committed to providing you with high-quality PGA Package Substrate solutions that meet your customized needs and standard substrate options.
First, we recommend you conduct an online search to find a trustworthy supplier. Entering relevant keywords into a search engine, such as “PGA Package Substrate supplier” or “electronic substrate manufacturer,” yields many potential options.
Second, you can find suppliers by attending industry shows and exhibitions. These shows usually bring together many electronics manufacturers and suppliers, providing an opportunity to communicate directly with them and learn about their products and services.
Additionally, you can obtain supplier information by referring to professional organizations and forums within the industry. On these platforms, you can learn about other companies’ experiences and lessons learned, as well as their reviews and recommendations for different suppliers.
As a reliable PGA Package Substrate supplier, we are committed to providing customers with high-quality products and excellent services. We offer a wide range of customization options to meet your specific project needs. Whether it’s a custom design for a specific industry or standardized substrate selection, we can meet your needs.
Our team has the experience and expertise to help you choose the best PGA Package Substrate solution for your project. Whether you require small batch production or a large-scale order, we can provide you with a flexible and reliable service.
By choosing us as your PGA Package Substrate supplier, you can trust us with your important projects and we will be happy to provide you with a satisfactory solution.
What is the quote for PGA Package Substrate?
The quotation of PGA Package Substrate is a complex and critical issue, which involves the comprehensive consideration of multiple factors. When calculating the price of PGA Package Substrate, the following aspects are usually considered:
Substrate type: Different types of PGA Package Substrate have differences in manufacturing processes and material costs. For example, the prices of organic PGA substrates, ceramic PGA substrates, and metal PGA substrates may differ.
Material cost: The manufacturing process of PGA Package Substrate requires the use of specific substrate materials, metallization layers, insulation layers, etc. The cost of these materials will directly affect the final quote.
Manufacturing process: Manufacturing PGA Package Substrate requires a series of precise process steps, including plate processing, circuit production, metallization, surface treatment, etc. Different manufacturing processes may have different impacts on costs.
Quantity requirements: Ordering different quantities of PGA Package Substrate will affect the unit price. Generally speaking, large quantity orders can get more competitive prices.
Customization requirements: If customers have special customization requirements, such as special sizes, materials or surface treatments, this may result in additional customization costs.
Time of demand: If the customer requires expedited delivery, additional expedited fees may apply.
Therefore, when ordering PGA Package Substrate, customers need to communicate in detail with the supplier to clarify their needs and budget constraints. Suppliers usually provide customized quotation plans based on customers’ specific requirements to ensure the best price/performance and meet customer needs.
Frequently Asked Questions (FAQs)
How do I choose the right PGA Package Substrate for my project?
Selecting the appropriate PGA Package Substrate involves considering factors such as the specific application requirements, thermal management needs, electrical performance criteria, and budget constraints. Consultation with experienced engineers and substrate manufacturers can provide valuable insights and guidance in making informed decisions.
How does PGA Package Substrate contribute to thermal management?
PGA Package Substrates are designed to efficiently dissipate heat generated by electronic components, thereby enhancing thermal management within the PCB assembly. The substrate’s material properties, thermal conductivity, and layout optimization play crucial roles in maintaining optimal operating temperatures and prolonging the lifespan of electronic devices.
Is PGA Package Substrate compatible with surface mount technology (SMT)?
Yes, PGA Package Substrates are compatible with surface mount technology (SMT). They offer a reliable foundation for mounting surface-mounted components, facilitating seamless integration into electronic assemblies. Proper design considerations and manufacturing techniques ensure compatibility and compatibility with SMT processes.
What environmental standards do PGA Package Substrates adhere to?
PGA Package Substrates adhere to various environmental standards and regulations, depending on the specific materials and manufacturing processes involved. Common standards include RoHS (Restriction of Hazardous Substances) compliance, which restricts the use of certain hazardous substances in electronic products, ensuring environmental sustainability and safety.