What are the characteristics of MEGTRON6 PCB?
MEGTRON6 PCB Manufacturer.MEGTRON6 PCB Manufacturer, a stalwart in the electronics industry, embodies precision and innovation. Renowned for crafting cutting-edge printed circuit boards, their name resonates with reliability and excellence. With meticulous attention to detail, they engineer boards that redefine standards, ensuring optimal performance in diverse applications. Their commitment to technological advancement and stringent quality control measures cements their position as leaders in the field. From concept to realization, MEGTRON6 PCB Manufacturer remains the preferred choice, trusted by clients worldwide for their unparalleled expertise and unwavering dedication to excellence.
In today’s high-tech electronics field, MEGTRON 6 PCB (Printed Circuit Board) has emerged with its excellent performance and innovative features, I will give you an in-depth explanation of the unique features of MEGTRON 6 PCB.
This article will delve into the unique features of MEGTRON 6 PCB, from high-frequency characteristics, low-distortion design, thermal stability to environmentally friendly materials, to show you the leading position of this packaging substrate in the electronics industry. As technology advances at a rapid pace, MEGTRON 6 PCB is not just a material choice, but a key enabler of innovative and sustainable practices. Come with me as I step into this fascinating area of technology to reveal what makes it unique.
Ultra-low Loss, Highly Heat Resistant Circuit Board Materials
Ultra-low loss, highly heat-resistant circuit board materials are a key technology in the current electronic field. They have excellent performance and are widely used in high-frequency, high-speed, and high-density electronic equipment and communication systems. This advanced material exhibits outstanding properties in multiple aspects, providing a reliable foundation for the design and manufacturing of modern electronic products.
First, this circuit board material is known for its ultra-low losses. Transmission loss is the energy lost by electrical signals during transmission. Ultra-low loss means that the circuit can transmit signals more efficiently, reducing the possibility of signal attenuation and distortion. This material improves system performance by using advanced dielectric materials and optimizing conductive properties to reduce energy loss when signals are transmitted through the circuit board. In high-frequency and high-speed communication systems, ultra-low loss circuit boards are crucial to ensure signal quality and stability.
Additionally, an inherent benefit of this circuit board material lies in its exceptional heat resistance. In numerous application scenarios, electronic equipment is required to function reliably in elevated temperature environments, such as automotive engine control systems, avionics equipment, and industrial automation systems. The material demonstrates a remarkable ability to endure extremely high temperatures, preserving its structural integrity and properties without experiencing performance deterioration or material degradation due to elevated temperatures. This heightened level of heat resistance serves as a crucial factor in safeguarding the reliability and long-term stability of electronic devices, particularly when subjected to extreme conditions.
In addition, this circuit board material typically has excellent mechanical strength and chemical stability, allowing it to perform well in complex manufacturing and use environments. The multi-layer construction ensures overall strength and stability, while special coatings and coverings provide additional protection against chemical and moisture attack.
These advanced circuit board materials, characterized by ultra-low-loss and exceptional heat resistance, find extensive application in communication base stations, radio frequency electronics, satellite communications, high-performance computers, and medical equipment. Their outstanding performance not only enhances the capabilities of electronic equipment but also contributes to cost savings in maintenance and prolongs the lifespan of the equipment. In the dynamic landscape of electronics technology, these cutting-edge circuit board materials are poised to persist as key contributors, propelling innovation and progress within the field.
Low Dielectric Constant(Dk) GlassCloth– LaminateR -5775(N) / PrepregR-5670(N)
The low dielectric constant (Dk) glass cloth laminate R-5775(N)/prepreg R-5670(N) stands out as an advanced circuit board material renowned for its exceptional electrical and mechanical properties. Widely employed in high-frequency applications and communication systems, this material has become a cornerstone in modern electronics manufacturing.
A defining characteristic of this material is its remarkably low dielectric constant (Dk). The dielectric constant gauges how a material influences the speed of electromagnetic waves within an electric field. The low Dk value of R-5775(N)/R-5670(N) signifies minimal impact on the propagation of high-frequency signals, leading to reduced dispersion and distortion in signal transmission. This quality makes it particularly well-suited for high-frequency applications like radio frequency (RF) circuits and microstrip antennas, ensuring stable signal transmission and upholding signal integrity.
Secondly, the material uses glass cloth as the base material, which has excellent mechanical strength and wear resistance. This strength allows it to maintain shape and stability during complex manufacturing processes, while the wear resistance allows the final circuit board to have a longer service life. This is particularly important for applications that require high reliability and long life, such as communication base stations and satellite communication systems.
In addition, R-5775(N)/R-5670(N) also exhibits excellent thermal stability and chemical resistance. This makes it suitable for applications operating in high-temperature environments, such as automotive engine control systems and military communications equipment. At the same time, its chemical resistance helps the material maintain stability in harsh environments and is not corroded by chemical substances, ensuring long-term reliable operation of the circuit board.
Finally, the manufacturing process of R-5775(N)/R-5670(N) is carefully designed to ensure material consistency and stability. This consistency is critical for mass production and high-quality electronics manufacturing, ensuring that every circuit board has the same performance characteristics.
The low dielectric constant glass cloth laminate R-5775(N)/prepreg R-5670(N) stands out as an advanced material highly favored in the realm of electronic manufacturing. Renowned for its low Dk value, exceptional mechanical properties, thermal stability, and chemical resistance, this material proves to be exceptionally versatile for a diverse array of high-performance applications.
Particularly well-suited for mobile, networking, and wireless applications that demand high-speed and ultra-low loss circuit materials, the MEGTRON 6 Family continues to set the benchmark in the industry.
MEGTRON 6 provides excellent high-density interconnect (HDI) and thermal performance.
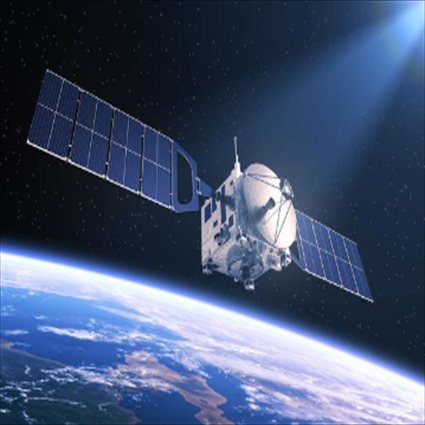
MEGTRON6 PCB Manufacturer
Standard E Glass Cloth – LaminateR-5775/PrepregR-5670
Standard E glass cloth is a common and important glass fiber reinforced material, which is widely used to manufacture composite materials with high strength, corrosion resistance and excellent insulation properties. Among them, R-5775 is a laminate of E glass cloth and resin-based materials, while R-5670 is a prepreg of E glass cloth and resin-based materials.
First of all, E-glass cloth is made of E-glass fiber, which has excellent mechanical properties and chemical stability. E-glass fiber is a type of glass fiber whose name comes from the English word “Electrical”, indicating its good performance in electrical insulation. This makes E-glass cloth particularly suitable for applications requiring high strength and electrical insulation properties, such as the manufacture of electrical equipment and electronic components.
R-5775 is an E-glass cloth and resin-based laminate, which means it is made by bonding E-glass cloth and resin together to form a multi-layer structure. This structure gives the material greater strength and rigidity, making it suitable for applications that need to withstand large mechanical stresses, such as aerospace, automotive manufacturing and building structures.
R-5670 is a prepreg made of E glass cloth and resin-based materials, also called prepreg glass cloth. Prepregs are glass cloths that have been impregnated with resin during the manufacturing process and do not need to be re-added before use. Such a design simplifies the manufacturing process, improves manufacturing efficiency, and ensures even distribution of resin in the material. R-5670 prepregs typically need to be cured under specific temperature and pressure conditions to form composites with good mechanical properties and chemical stability.
Both materials find extensive applications in various industrial contexts. R-5775 is frequently employed in the fabrication of structural components demanding high strength and excellent corrosion resistance, such as aircraft and automotive parts. Its robust strength and rigidity enable it to endure intricate mechanical stresses, while its resistance to corrosion ensures optimal performance in challenging environments. On the other hand, R-5670 prepreg is commonly utilized in the production of composite parts necessitating precision molding, such as high-performance ships and satellite reflectors.
Overall, standard E-glass cloth, R-5775 laminate and R-5670 prepreg are all key materials in modern engineering, and their excellent performance and wide range of applications provide reliable solutions for multiple industries. In the ever-evolving world of technology and engineering, these materials will continue to play a key role, driving innovation and progress in a variety of fields.
The MEGTRON 6 Family, including MEGTRON 6(G), MEGTRON 6(K), MEGTRON 6(N), are the original PCB industry standards. The products are ideal for mobile, networking, and wireless applications requiring high-speed, ultra-low loss circuit materials.
MEGTRON 6 provides excellent high-density interconnect (HDI) and thermal performance.
R-5775(K)/R-5670(K)
Specification / Laminate R-5775
Property | Units | Test Method | Condition | Typical Value | ||
THERMAL | Glass Transition Temp ( Tg) | C | DSC | As received | 185 | |
DMA | As received | 210 | ||||
Thermal Decomposition Temp ( Td ) | C | TGA | As received | 410 | ||
Time to Delam ( T288 ) |
Without Cu | min | IPC TM-650 2.4.24.1 | As received | > 120 | |
With Cu | min | IPC TM-650 2.4.24.1 | As received | > 120 | ||
CTE :α1 | X- axis | ppm/C | IPC TM-650 2.4.24 | < Tg | 14~16 | |
Y – axis | ppm/C | IPC TM-650 2.4.24 | < Tg | 14~16 | ||
Z – axis | ppm/C | IPC TM-650 2.4.24 | < Tg | 45 | ||
CTE :α2 | Z – axis | ppm/C | IPC TM-650 2.4.24 | > Tg | 260 | |
ELECTRICAL | Volume Resistivity | MΩ-cm | IPC TM-650 2.5.17.1 | C-96/35/90 | 1*10⁹ | |
Surface Resistivity | MΩ | IPC TM-650 2.5.17.1 | C-96/35/90 | 1×10⁸ | ||
Dielectric Constant (Dk ) |
@1MHz | ⁻ | IPC TM-650 2.5.5.9 | C-24/23/50 | 3.71 | |
@10GHz | ⁻ | IPC TM-650 2.5.5.9 | C-24/23/50 | 3.61 | ||
Dissipation Factor (Df) |
@1MHz | ⁻ | IPC TM-650 2.5.5.9 | C-24/23/50 | 0.002 | |
@10GHz | ⁻ | IPC TM-650 2.5.5.9 | C-24/23/50 | 0.004 | ||
PHYSICAL | Water Absorption | % | IPC TM-650 2.6.2.1 | D-24/23 | 0.14 | |
Peel Strength | 1oz(H-VLP) | kN/m | IPC TM-650 2.4.8 | As Received | 0.8 | |
Flammability | ⁻ | UL | C-48/23/50 | 94V-0 | ||
Sample thickness ;29.5 mil=0.750mm(Core Type 30) | ||||||
The data in the above table are not guaranteed values. |
R-5775(N)/R-5670(N)
Specification / Laminate R-5775(N)
Property | Units | Test Method | Condition | Typical Value | ||
THERMAL | Glass Transition Temp ( Tg) | C | DSC | As received | 185 | |
DMA | As received | 210 | ||||
Thermal Decomposition Temp ( Td ) | C | TGA | As received | 410 | ||
Time to Delam ( T288 ) |
Without Cu | min | IPC TM-650 2.4.24.1 | As received | > 120 | |
With Cu | min | IPC TM-650 2.4.24.1 | As received | > 120 | ||
CTE :α1 | X- axis | ppm/C | IPC TM-650 2.4.24 | < Tg | 14~16 | |
Y – axis | ppm/C | IPC TM-650 2.4.24 | < Tg | 14~16 | ||
Z – axis | ppm/C | IPC TM-650 2.4.24 | < Tg | 45 | ||
CTE :α2 | Z – axis | ppm/C | IPC TM-650 2.4.24 | > Tg | 260 | |
ELECTRICAL | Volume Resistivity | MΩ-cm | IPC TM-650 2.5.17.1 | C-96/35/90 | 1*10⁹ | |
Surface Resistivity | MΩ | IPC TM-650 2.5.17.1 | C-96/35/90 | 1×10⁸ | ||
Dielectric Constant (Dk ) |
@1MHz | ⁻ | IPC TM-650 2.5.5.9 | C-24/23/50 | 3.40 | |
@12GHz | ⁻ | *Note 1 | C-24/23/50 | 3.35 | ||
Dissipation Factor (Df) |
@1MHz | ⁻ | IPC TM-650 2.5.5.9 | C-24/23/50 | 0.002 | |
@12GHz | ⁻ | *Note 1 | C-24/23/50 | 0.004 | ||
PHYSICAL | Water Absorption | % | IPC TM-650 2.6.2.1 | D-24/23 | 0.14 | |
Peel Strength | 1oz(H-VLP) | kN/m | IPC TM-650 2.4.8 | As Received | 0.8 | |
Flammability | ⁻ | UL | C-48/23/50 | 94V-0 | ||
Sample thickness ;29.5 mil=0.750mm(Core Type 30) | ||||||
Note 1:Balanced-Type Circular Disk Resonance Method |
R-5775(G)/R-5775(G)
Specification / Prepreg R-5670(N)
1GHz ; IPC TM650-2.5.5.9
6-50GHz ; Balanced-Type Circular Disk Resonance Method
Typical Thickness (um) | Typical Df | |||||||||
1GHz | 6GHz | 12GHz | 18GHz | 23GHz | 29GHz | 34GHz | 40GHz | 45GHz | 50GHz | |
60 | 0.002 | 0.003 | 0.004 | 0.004 | 0.004 | 0.005 | 0.005 | 0.005 | 0.005 | 0.005 |
68 | 0.002 | 0.003 | 0.004 | 0.004 | 0.005 | 0.005 | 0.005 | 0.005 | 0.005 | 0.006 |
74 | 0.002 | 0.003 | 0.004 | 0.004 | 0.005 | 0.005 | 0.005 | 0.005 | 0.005 | 0.006 |
77 | 0.002 | 0.003 | 0.004 | 0.004 | 0.004 | 0.004 | 0.005 | 0.005 | 0.005 | 0.005 |
89 | 0.002 | 0.003 | 0.004 | 0.004 | 0.004 | 0.005 | 0.005 | 0.005 | 0.005 | 0.005 |
104 | 0.002 | 0.003 | 0.004 | 0.004 | 0.005 | 0.005 | 0.005 | 0.005 | 0.005 | 0.006 |
118 | 0.002 | 0.003 | 0.004 | 0.004 | 0.005 | 0.005 | 0.005 | 0.005 | 0.005 | 0.006 |
98 | 0.002 | 0.003 | 0.004 | 0.004 | 0.004 | 0.004 | 0.004 | 0.005 | 0.005 | 0.005 |
106 | 0.002 | 0.003 | 0.004 | 0.004 | 0.004 | 0.004 | 0.004 | 0.005 | 0.005 | 0.005 |
125 | 0.002 | 0.003 | 0.004 | 0.004 | 0.004 | 0.004 | 0.004 | 0.005 | 0.005 | 0.005 |
132 | 0.002 | 0.003 | 0.004 | 0.004 | 0.004 | 0.004 | 0.004 | 0.005 | 0.005 | 0.005 |
What are the advantages and features of MEGTRON 6 PCB?
At the forefront of electronic engineering, MEGTRON 6 PCB has become a key technology leading the trend with its unique performance characteristics. In what aspects does MEGTRON 6 excel? Let’s dive deeper into the diverse benefits this high-performance material offers, from signal integrity to thermal performance, to reveal its contribution to electronic device functionality and reliability.
Signal Integrity: A Bridge to the World
MEGTRON 6 PCBs stand out for their excellent signal integrity. Its low dielectric constant and low dissipation factor enable it to effectively reduce distortion and attenuation in signal transmission. This not only ensures accurate transmission of data, but also makes it ideal for high-frequency applications. From communication equipment to radio frequency modules, the signal transmission performance of MEGTRON 6 is undoubtedly one of the keys to promoting advanced electronic engineering.
Thermal performance: Robust temperature control performance
Ensuring the steadfast performance of electronic equipment is intricately tied to exceptional thermal capabilities, and MEGTRON 6 has achieved remarkable strides in this domain. Its outstanding thermal conductivity serves as a breakthrough, efficiently dissipating the heat produced within the circuit. This ensures that chips and components consistently maintain an optimal temperature during operation. Beyond enhancing equipment efficiency, this attribute also extends the service life of components, underlining MEGTRON 6’s significant contribution to prolonged and reliable electronic functionality.
Reliability and stability: a solid foundation for the future
MEGTRON 6 PCB demonstrates compelling performance in terms of reliability and stability. Its material design and manufacturing process ensure the board’s consistency and stability, both in extreme temperatures and in high-frequency applications. This provides a solid foundation for all types of electronic equipment, ensuring that they always operate reliably in different environments and working conditions.
High frequency applications: ideal for meeting challenges
In the context of today’s increasing number of high-frequency applications, MEGTRON 6 PCB has become an ideal choice due to its excellent performance. Its low dielectric loss and outstanding signal fidelity enable excellent performance in the microwave band and RF fields. From 5G communication equipment to radar systems, MEGTRON 6 has demonstrated strong adaptability in high-frequency electronic engineering.
MEGTRON 6 PCB is the leading choice in electronic engineering due to its excellent signal integrity, thermal performance, reliability and performance in high-frequency applications. It is not only a bridge connecting the world, but also a guarantee for the stable operation of future electronic equipment. With MEGTRON 6 PCB, we move towards a more innovative and reliable era of electronic engineering.
What are the application scenarios of MEGTRON 6 PCB?
In today’s rapidly developing electronics field, MEGTRON 6 PCB has found wide applications in many key industries due to its excellent performance characteristics. Let’s take a closer look at how MEGTRON 6 performs in each specific application scenario.
Telecommunications field
MEGTRON 6 PCB plays a key role in telecommunications equipment. Its low dielectric constant and low dissipation factor make it ideal for high-frequency communication equipment. Whether it is RF modules for base station antennas or fiber optic communications for high-speed data transmission, MEGTRON 6 demonstrates excellent signal integrity and transmission performance.
Aerospace
In the aerospace field, the requirements for electronic components are particularly demanding, and MEGTRON 6 PCB meets this challenge. Its high temperature stability and reliability make it a first choice for aerospace electronic systems. From aircraft navigation systems to satellite communications equipment, MEGTRON 6 plays a vital role in ensuring equipment stability and performance.
Medical equipment
In the realm of medical equipment, where precision and reliability are paramount, MEGTRON 6 PCBs stand out as exemplary electronic components. Renowned for their elevated electrical performance and unwavering stability, these PCBs prove highly fitting for a spectrum of medical devices. This includes applications in medical imaging equipment, patient monitoring systems, and surgical devices, where the exacting demands of the healthcare field are met with the superior qualities of MEGTRON 6 PCBs.
Vehicle electronics
With the rapid development of automotive electronics technology, MEGTRON 6 PCB plays a key role in automotive electronic systems. From in-car entertainment systems to advanced driver assistance systems, MEGTRON 6 provides solid support for the reliability and performance of automotive electronics through its high-frequency and high-speed data transmission capabilities.
Automated industry
In the field of industrial automation, MEGTRON 6 PCB is widely used in various control systems and sensors. Its high temperature resistance and corrosion resistance make it suitable for harsh industrial environments. From smart manufacturing to automated warehousing systems, MEGTRON 6 provides a reliable electronic foundation for industrial equipment.
Overall, MEGTRON 6 PCB has successfully penetrated into many fields such as telecommunications, aerospace, medical, automotive electronics and industrial automation with its excellent electrical performance and reliability. Whether in high-frequency communications or applications in extreme environments, MEGTRON 6 has demonstrated its excellence in cutting-edge technology and continues to meet the stringent requirements of different industries and applications.
What are the differences between MEGTRON 6 PCB and traditional materials?
In today’s evolving electronics manufacturing landscape, selecting the right Printed Circuit Board (PCB) material is critical to electrical performance, reliability and overall efficiency. As a high-performance material, MEGTRON 6 PCB shows significant differences compared with traditional PCB materials, bringing substantial improvements to the performance of electronic equipment.
Differences in electrical performance
First, let’s look at the electrical performance comparison. MEGTRON 6 PCB stands out for its excellent electrical properties, with low dielectric constant and dielectric losses. In comparison, traditional PCB materials may perform more mediocre in these aspects. This difference directly affects the quality and speed of signal transmission. Using MEGTRON 6 PCB can effectively reduce signal distortion and improve the stability of signal transmission, especially in high-frequency applications.
Improved reliability
In terms of reliability, MEGTRON 6 PCB provides guarantee for the long-term stable operation of electronic equipment through its excellent heat resistance and chemical corrosion resistance. In comparison, traditional PCB materials may not perform well in high-temperature environments and are easily affected by chemicals. Taking extreme applications such as aerospace and aerospace as an example, the superior performance of MEGTRON 6 PCB can ensure that the circuit board can still operate reliably under extreme conditions and avoid system failures caused by material problems.
Improvement of overall efficiency
MEGTRON 6 PCB also performs well in terms of overall efficiency. Its excellent thermal conductivity and thermal conductivity help dissipate heat and ensure that electronic equipment maintains good temperature control when operating at high loads. In contrast, traditional PCB materials can face issues with overheating and performance degradation. By using MEGTRON 6 PCB, electronic equipment can work more efficiently, extend its service life, and reduce maintenance costs.
Overall, MEGTRON 6 PCB offers a compelling, advanced option to the electronics manufacturing industry through its superior performance in electrical performance, reliability and overall efficiency. Its wide range of applications and practical effects prove its important role in promoting the performance and innovation of electronic devices.
What is the manufacturing and production technology of MEGTRON 6 PCB?
When exploring the manufacturing and production technology of MEGTRON 6 PCB, we will gain an in-depth understanding of the essence of its manufacturing process and technology. The complexity and technical content of this process directly determine the high-performance characteristics of MEGTRON 6 PCB.
First, we focus on the structural details of the MEGTRON 6 PCB, which is the cornerstone of its superior performance. Its base material adopts advanced structural design to cope with the stringent requirements of high-frequency applications. Key components include a high-performance polyimide substrate, special reinforcements and a precisely controlled lamination process. These careful structural designs enable MEGTRON 6 PCB to perform well in high-frequency environments, ensuring the stability of telecommunications, radio frequency and other high-frequency applications.
Secondly, the manufacturing technology of MEGTRON 6 PCB shows unprecedented advancement. Improved high-density jack (HDI) manufacturing technology is adopted, which not only increases the density of components on the circuit board, but also significantly reduces the circuit length, helping to reduce signal transmission delay and distortion. Through the improved semi-processing method, the production process is more refined, ensuring the flatness of the circuit board surface and the consistency of electrical properties.
In addition, the manufacturing process of MEGTRON 6 PCB adopts an advanced semi-additive method, which is widely adopted in circuit board manufacturing. Compared with traditional methods, the semi-additive method reduces the generation of waste during the process and improves manufacturing efficiency. This innovative manufacturing technology not only helps improve the performance of MEGTRON 6 PCB, but also conforms to the pursuit of sustainable development in modern manufacturing.
Finally, a precisely controlled production process ensures the quality and stability of MEGTRON 6 PCB. Advanced photolithography technology, electroless copper plating process and high temperature and high pressure lamination process all provide a solid foundation to ensure its performance. Every step is subject to strict quality control to ensure the final product meets high standards of electrical performance and reliability.
Overall, the excellence of MEGTRON 6 PCB’s manufacturing and production technology lies in the fine design of its structure and the advanced manufacturing processes employed. These factors complement each other and lay a solid foundation for MEGTRON 6 PCB’s excellent performance in the high-performance field.
What are the Frequently Asked Questions (FAQs) for MEGTRON 6 PCB?
As a star in the field of electronic engineering, MEGTRON 6 PCB has attracted widespread attention. Here, we will answer some frequently asked questions about MEGTRON 6 PCB to help readers better understand the application of this high-performance material in electronic manufacturing.
What is MEGTRON 6 PCB?
MEGTRON 6 PCB is a high performance material designed for advanced PCB applications. Its excellent electrical properties, including low dielectric constant and dielectric dissipation factor, make it excellent in high-frequency applications.
What are the advantages of MEGTRON 6 PCB over traditional materials?
Compared with traditional materials, MEGTRON 6 PCB has a series of significant advantages. First, its excellent electrical properties make it excellent in signal transmission, helping to improve the stability and performance of circuits. Secondly, MEGTRON 6 PCB has excellent thermal performance and can effectively dissipate heat to ensure that electronic equipment remains stable during high-load operations.
In which application scenarios does MEGTRON 6 PCB perform particularly well?
MEGTRON 6 PCB excels in many areas, especially in demanding applications. From communications equipment to aerospace technology, the high performance of MEGTRON 6 PCB makes it the first choice for a variety of advanced technologies.
Can the reliability of circuits be improved by using MEGTRON 6 PCB?
Yes, using MEGTRON 6 PCB can significantly improve the reliability of the circuit. Its stable electrical properties and excellent material properties help reduce signal distortion in the circuit, thereby enhancing the stability and reliability of the entire system.
Are MEGTRON 6 PCBs suitable for High Density Interconnect (HDI) technology?
MEGTRON 6 PCB is ideally suited for high-density interconnection technologies. Its advanced manufacturing technology and material properties make it ideal for implementing complex circuit layouts and designs, driving the development of high-density interconnect technology.
Does using MEGTRON 6 PCB require special manufacturing processes?
Yes, using MEGTRON 6 PCB usually requires some special manufacturing processes. Its material properties require a more precise manufacturing process to ensure that the final product can fully utilize the superior properties of MEGTRON 6.
By answering these frequently asked questions, we hope readers can better understand the characteristics of MEGTRON 6 PCBs and their potential applications in electronics manufacturing. The introduction of MEGTRON 6 brings new possibilities to electronic engineering and provides a reliable foundation for the development of high-performance electronic equipment.