What is the thermal performance of MEGTRON4 PCB?
MEGTRON4 PCB Manufacturer.MEGTRON4 PCB Manufacturer specializes in crafting high-quality printed circuit boards (PCBs) engineered with MEGTRON4 material, renowned for its exceptional electrical performance and reliability. With state-of-the-art manufacturing facilities and a team of skilled professionals, we deliver precision-crafted PCB solutions tailored to meet the diverse needs of industries such as telecommunications, aerospace, automotive, and more. Our commitment to innovation and quality ensures that every MEGTRON4 PCB we produce meets stringent industry standards, offering unparalleled durability and performance for even the most demanding applications. Trust MEGTRON4 PCB Manufacturer for your next project’s circuitry needs.
MEGTRON 4 PCB, one of the leaders in the electronics industry, is highly regarded for its superior performance and reliability. Constructed of advanced materials and processes, MEGTRON 4 PCBs demonstrate exceptional performance in a variety of electronic applications.
In today’s increasingly complex and high-performance electronic devices, thermal performance is critical to ensuring stable component operation. This article will conduct an in-depth study of the thermal performance of MEGTRON 4 PCB and explore its performance and unique advantages in high-temperature environments. Through detailed analysis and case presentations, we will reveal the core position of MEGTRON 4 PCB in the electronics industry and its key role in promoting the advancement of future electronic technology.
Low Transmission Loss And Highly Heat-Resistant Multi-Layer Circuit Board Material
Multilayer circuit board materials, characterized by low transmission loss and exceptional heat resistance, represent a significant technological breakthrough in the electronics industry, offering crucial support for the design and manufacturing of contemporary electronic devices. This advanced material’s distinctive characteristics position it as a preferred choice, particularly in the realms of communications and high-performance computing.
Firstly, the low transmission loss attributes of this multilayer circuit board material render it highly proficient in transmitting high-frequency signals. Transmission loss, denoting the energy dissipation during signal transmission in a circuit, is minimized, allowing signals to travel more efficiently with minimal attenuation. This becomes imperative in applications demanding exceptionally high signal quality, such as high-frequency communication systems, radio frequency electronics, and radar systems. Through meticulous selection and design of conductive layers and dielectric materials, this material optimizes the transmission efficiency of electrical signals, thereby enhancing system performance.
Secondly, a notable feature of this multilayer circuit board material is its high heat resistance. In numerous applications, electronic devices may operate within elevated temperature environments, ranging from automotive engine rooms to aerospace equipment and high-performance computers. The material’s ability to reliably function under extreme temperature conditions ensures that circuit performance remains unaffected. Its high temperature resistance empowers electronic equipment to operate dependably in diverse extreme environments, ultimately elevating system stability and reliability.
In addition, this multilayer circuit board material has excellent mechanical strength and chemical stability. The multi-layer structure design can provide sufficient mechanical support to ensure that the circuit board is not easily deformed or damaged during long-term use. At the same time, its chemical resistance makes it more durable in harsh environments and can cope with some highly chemically corrosive work scenarios.
The application of this material widely involves many fields such as communications, radio frequency electronics, radar technology, high performance computing and satellite communications. In these fields, the requirements for circuit performance, transmission efficiency and stability are extremely high, and multi-layer circuit board materials with low transmission loss and high heat resistance can meet these challenging needs.
In general, low transmission loss and high heat resistance multilayer circuit board materials are one of the key factors driving the continuous advancement of electronic technology. As the performance and reliability requirements of electronic equipment continue to increase, the research and application of this advanced material will continue to promote the development of the electronics industry and provide a solid foundation for innovative electronic products.
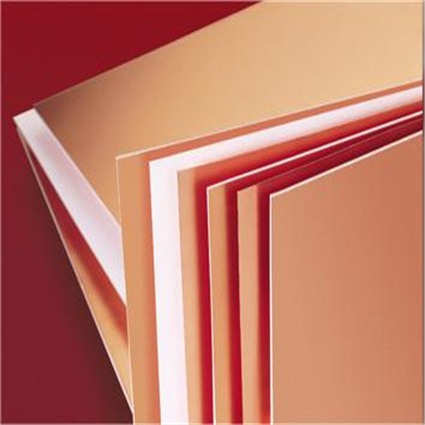
MEGTRON4 PCB Manufacturer
MEGTRON 4 – Laminate R-5725/Prepreg R-5620
MEGTRON 4 is an advanced multi-layer circuit board material composed of Laminate R-5725 and Prepreg R-5620, which offers excellent performance and properties suitable for high-frequency applications. This material is widely used in electronics manufacturing, especially in communications, radio frequency electronics and high-speed computing to meet the demand for high-performance circuit boards.
Laminate R-5725 serves as the foundational material for MEGTRON 4, leveraging advanced glass fiber-reinforced materials. This substrate stands out with exceptional mechanical strength and dimensional stability, rendering it well-suited for intricate circuit board designs. With notable high-frequency attributes and a low dielectric constant, Laminate R-5725 excels in demanding applications, minimizing signal transmission losses and enhancing both the speed and accuracy of signal transmission.
Prepreg R-5620 is the prepreg part of MEGTRON 4 and is responsible for providing adhesion between different layers of the circuit board. This prepreg uses a unique resin system with excellent thermal and chemical stability, allowing it to remain stable in complex manufacturing environments. The use of Prepreg R-5620 ensures the interlayer bonding strength of the circuit board while providing sufficient flexibility so that the circuit board can adapt to diverse design needs.
The combined design of MEGTRON 4 offers several advantages. First, it has excellent high-frequency characteristics and is suitable for applications requiring frequent signal transmission and processing. Its low dielectric constant and low loss tangent ensure stable signal transmission at high frequencies, reduce signal attenuation, and improve system performance.
Secondly, MEGTRON 4’s excellent thermal stability enables it to maintain stable performance in high-temperature environments, which is particularly important for some high-performance applications, such as aerospace and automotive electronic control systems. The material’s thermal expansion coefficient matching also reduces the risk of circuit board deformation due to temperature changes, ensuring system reliability and durability.
Finally, MEGTRON 4’s excellent chemical stability enables it to resist chemical corrosion, extending the service life of circuit boards and reducing maintenance and replacement costs.
Taken together, MEGTRON 4 is an advanced multi-layer circuit board material. Its design consisting of Laminate R-5725 and Prepreg R-5620 enables it to perform well in high frequency, high temperature and complex environments. It provides a reliable solution for the electronics manufacturing industry and promotes the continuous development of high-performance electronic equipment.
The following are some data for reference only:
R-5725/R-5620
Specification / Laminate R-5725
Property | Units | Test Method | Condition | Typical Value | ||
THERMAL | Glass Transition Temp ( Tg) | C | DSC | As received | 176 | |
TMA | As received | 170 | ||||
DMA | As received | 210 | ||||
Thermal Decomposition Temp ( Td ) | C | TGA | As received | 360 | ||
Time to Delam ( T288 ) |
Without Cu | min | IPC TM-650 2.4.24.1 | As received | > 120 | |
With Cu | min | IPC TM-650 2.4.24.1 | As received | 30 | ||
CTE :α1 | X – axis | ppm/C | IPC TM-650 2.4.24 | < Tg | 12~14 | |
Y – axis | ppm/C | IPC TM-650 2.4.24 | < Tg | 13~15 | ||
Z – axis | ppm/C | IPC TM-650 2.4.24 | < Tg | 35 | ||
CTE :α2 | Z – axis | ppm/C | IPC TM-650 2.4.24 | > Tg | 265 | |
ELECTRICAL | Volume Resistivity | MΩ-cm | IPC TM-650 2.5.17.1 | C-96/35/90 | 1*10⁹ | |
Surface Resistivity | MΩ | IPC TM-650 2.5.17.1 | C-96/35/90 | 1×10⁸ | ||
Dielectric Constant (Dk ) |
@1MHz | ⁻ | IPC TM-650 2.5.5.9 | C-24/23/50 | 3.89 | |
@1GHz | ⁻ | IPC TM-650 2.5.5.9 | C-24/23/50 | 3.83 | ||
Dissipation Factor (Df) |
@1MHz | ⁻ | IPC TM-650 2.5.5.9 | C-24/23/50 | 0.005 | |
@1GHz | ⁻ | IPC TM-650 2.5.5.9 | C-24/23/50 | 0.005 | ||
PHYSICAL | Water Absorption | % | IPC TM-650 2.6.2.1 | D-24/23 | 0.14 | |
Peel Strength | 1oz | kN/m | IPC TM-650 2.4.8 | As Received | 1.2 | |
Flammability | ⁻ | UL | C-48/23/50 | 94V-0 | ||
Sample thickness ;32 mil (0.8 mm) #3313 x 8 ply | ||||||
The data in the above table are not guaranteed values. |
1MHz – 1GHz ; IPC TM650-2.5.5.9
Core Type |
Actual Thickness | Cloth Style |
Typical Resin Content (%) |
Typical Dk | Typical Df | |||||
mil | mm | 1MHz | 100MHz | 1GHz | 1MHz | 100MHz | 1GHz | |||
2 | 2.0 | 0.050 | 106 X 1 | 72 | 3.39 | 3.39 | 3.38 | 0.005 | 0.005 | 0.006 |
2 | 2.0 | 0.050 | 1067 X 1 | 66 | 3.58 | 3.56 | 3.56 | 0.005 | 0.005 | 0.005 |
2.5 | 2.4 | 0.060 | 1080 X 1 | 59 | 3.82 | 3.79 | 3.77 | 0.005 | 0.005 | 0.005 |
3 | 3.1 | 0.080 | 1080 X1 | 65 | 3.64 | 3.61 | 3.6 | 0.005 | 0.005 | 0.005 |
3.4 | 3.5 | 0.090 | 1078 X 1 | 68 | 3.54 | 3.50 | 3.47 | 0.005 | 0.005 | 0.006 |
3.5 | 3.5 | 0.090 | 106 X 2 | 69 | 3.51 | 3.48 | 3.46 | 0.005 | 0.005 | 0.006 |
3.5 | 3.5 | 0.090 | 3313 X 1 | 51 | 4.10 | 4.05 | 4.01 | 0.004 | 0.005 | 0.005 |
4 | 3.9 | 0.100 | 3313 X 1 | 57 | 3.89 | 3.85 | 3.83 | 0.005 | 0.005 | 0.005 |
4 | 3.9 | 0.100 | 1067 X 2 | 66 | 3.58 | 3.56 | 3.56 | 0.005 | 0.005 | 0.005 |
4.5 | 4.3 | 0.110 | 2116 X 1 | 51 | 4.10 | 4.05 | 4.01 | 0.004 | 0.005 | 0.005 |
4.7 | 4.7 | 0.120 | 1080 X 2 | 57 | 3.89 | 3.85 | 3.83 | 0.005 | 0.005 | 0.005 |
5 | 5.1 | 0.130 | 2116 X 1 | 56 | 3.93 | 3.88 | 3.86 | 0.005 | 0.005 | 0.005 |
5 | 5.1 | 0.130 | 1080 X 2 | 60 | 3.80 | 3.76 | 3.73 | 0.005 | 0.005 | 0.005 |
5 | 5.1 | 0.130 | 1078 X 2 | 59 | 3.82 | 3.79 | 3.77 | 0.005 | 0.005 | 0.005 |
5.5 | 5.5 | 0.150 | 1080 X 2 | 63 | 3.69 | 3.66 | 3.65 | 0.005 | 0.005 | 0.005 |
6 | 5.9 | 0.150 | 1080 X 2 | 65 | 3.64 | 3.61 | 3.60 | 0.005 | 0.005 | 0.005 |
6 | 5.9 | 0.150 | 1504 X 1 | 49 | 4.14 | 4.10 | 4.07 | 0.004 | 0.005 | 0.005 |
6 | 5.9 | 0.150 | 1078 X 2 | 65 | 3.64 | 3.61 | 3.60 | 0.005 | 0.005 | 0.005 |
Understand the role of packaging substrate?
Before delving into the intricacies of MEGTRON 4 PCB, it’s essential to grasp the fundamental functions of packaging substrates and their pivotal role in electronic devices. As an indispensable element in modern electronic equipment, packaging substrates play a crucial role by providing essential functions such as electrical connections, mechanical support, and heat dissipation. This critical component lays the groundwork for the seamless operation of electronic elements.
A primary function of packaging substrates is to facilitate electrical connections. They house diverse electronic components, including chips, resistors, and capacitors, interconnecting them through precisely designed wires and through holes to establish a complete circuit. In this process, the significance of MEGTRON 4 PCB becomes evident. This advanced printed circuit board distinguishes itself with exceptional electrical performance and signal integrity. Its notable attributes, such as high thermal conductivity and excellent dielectric properties, position it as an optimal choice in electronic devices, particularly in applications demanding high performance and intricate circuits.
In addition to electrical connections, the package substrate also provides mechanical support. Electronic components of various sizes and shapes need to be securely anchored in equipment to prevent damage from mechanical vibration and external pressure. With its excellent mechanical strength and stability, MEGTRON 4 PCB provides reliable support for electronic components and ensures reliable operation of equipment in various environments.
Additionally, heat dissipation is another critical function of the packaging substrate. As the performance of electronic equipment continues to improve, the heat generated by components also increases accordingly. Good heat dissipation design is the key to ensuring long-term stable operation of the equipment. MEGTRON 4 PCB, with its excellent thermal conductivity, effectively disperses and transfers heat, reduces equipment temperature, and improves the working efficiency and life of electronic components.
At its core, comprehending the fundamental functions of a packaging substrate lays the groundwork for appreciating the exceptional capabilities of MEGTRON 4 PCB. The substrate’s prowess in electrical connection, mechanical support, and heat dissipation positions it as an essential and pivotal component in contemporary high-performance electronic devices. Before delving into the intricacies of MEGTRON 4, a more profound grasp of the packaging substrate’s role is instrumental in unraveling the genuine value inherent in this cutting-edge technology.
What are the functions of MEGTRON 4 PCB?
In today’s vast field of electronic engineering, MEGTRON 4 PCB stands at the forefront with its excellent performance and versatility. As a new generation benchmark for printed circuit boards, MEGTRON 4 has injected new vitality into the development of electronic systems, and its unique features span all aspects from signal integrity to thermal management.
First of all, MEGTRON 4 PCB has an eye-catching performance in improving signal integrity. Its superior electrical performance ensures high stability and accurate transmission of signals. The transmission of high-frequency signals is crucial in modern electronic equipment, and MEGTRON 4 PCB effectively improves the performance of the entire system by reducing losses in signal transmission. This feature makes MEGTRON 4 PCB the first choice in demanding application scenarios, such as communication equipment and high-speed data transmission systems.
Secondly, MEGTRON 4 PCB shows strong strength in thermal management. As electronic devices become increasingly compact and power consumption continues to increase, thermal issues have become an important factor affecting system reliability and longevity. MEGTRON 4 PCB uses advanced materials and designs to effectively disperse and conduct heat, ensuring that electronic components maintain stable temperatures under difficult working conditions.
Beyond its primary functions, MEGTRON 4 PCB demonstrates outstanding anti-interference capabilities against electromagnetic compatibility (EMC), effectively mitigating electromagnetic interference within the system and ensuring the seamless operation of equipment. Moreover, its exceptional mechanical properties and durability elevate MEGTRON 4 PCB to prominence in challenging environments and applications demanding heightened reliability.
Overall, MEGTRON 4 PCB, as a new generation of printed circuit boards, plays a key role in improving signal integrity and improving thermal management. Its unique functions make it a mainstay in the field of electronic engineering, leading the development direction of future electronic equipment.
How does MEGTRON 4 PCB compare to traditional PCB?
In the field of modern electronic packaging, MEGTRON 4 PCB exhibits a series of eye-catching unique features and superior advantages compared with traditional PCB. As a keyword focus, MEGTRON 4’s significant role in chip packaging technology and classification makes it stand out.
First of all, MEGTRON 4 PCB’s performance in chip packaging technology is eye-catching. Its advanced packaging technology allows the chip to be laid out more compactly on the PCB, thereby achieving higher integration. This not only helps improve equipment performance, but also achieves significant advantages in space utilization. Compared with traditional PCB, MEGTRON 4’s innovation in chip packaging provides broader possibilities for the design and manufacturing of electronic devices.
Secondly, MEGTRON 4’s diversity in chip assortments is one of its unique features. Different types of chips require different packaging technologies and materials, and MEGTRON 4 PCB can adapt to the packaging needs of various chips through its flexible design and versatility. This enables it to perform optimally in a variety of application scenarios, from high-performance computers to small embedded systems.
In addition to its outstanding performance in chip packaging technology, MEGTRON 4 also surpasses traditional PCBs in overall performance. Its excellent performance in signal integrity provides more reliable data transmission for electronic devices. At the same time, the superior thermal management characteristics ensure the stability of the equipment during high-load operation and further extend the life of the equipment.
When it comes to chip sorting, MEGTRON 4’s versatility and flexibility make it the first choice for a variety of industries. From high-end communication equipment to advanced medical instruments, MEGTRON 4 can handle complex chip packaging needs, providing a reliable and flexible solution for manufacturers of various electronic products.
Overall, by comparing MEGTRON 4 PCB with traditional PCB, we can clearly see its leading position in chip packaging technology and classification. Its unique characteristics not only improve device performance and reliability, but also bring new possibilities for innovation in the field of electronic packaging. MEGTRON 4, as an advanced printed circuit board, is pointing the direction for the development of future electronic equipment with its unique advantages.
Different types of packaging substrates with MEGTRON 4?
In today’s electronics industry, there are many types of packaging substrates, and MEGTRON 4 PCB has emerged as an important packaging substrate material in the market. Let’s delve into the various packaging substrate types to better understand MEGTRON 4’s suitability and applications in this area.
First of all, the types of packaging substrates include common FR-4 substrates, high-frequency RF boards, and multi-layer boards. FR-4 substrates are widely used in general electronic applications, while high-frequency RF boards are more focused on wireless communication equipment such as antennas and radar systems. Multilayer boards, on the other hand, achieve higher integration by stacking multiple conductor layers on a single substrate.
However, when we focus on high performance and complex applications, MEGTRON 4 PCB starts to show its uniqueness. MEGTRON 4 stands out for its excellent dielectric properties, excellent thermal conductivity and excellent mechanical strength. This makes it widely applicable in high frequency applications and complex electronic systems.
MEGTRON 4 PCB excels in high-frequency settings, adeptly minimizing signal transmission losses and enhancing signal integrity. Its remarkable thermal conductivity makes it an ideal choice for applications sensitive to heat, contributing to the maintenance of stable operating temperatures for electronic components. Furthermore, the robust mechanical strength of MEGTRON 4 PCB equips it to navigate intricate environments and accommodate high-density component layouts, thereby guaranteeing the reliability and stability of electronic systems.
In practical applications, MEGTRON 4 PCB is widely used in communication equipment, medical instruments, aerospace and other fields. Especially for applications that require extremely high signal transmission, thermal management and reliability, MEGTRON 4 is often the first choice.
Overall, the unique performance of MEGTRON 4 PCB in the field of packaging substrates makes it stand out in different types of applications, providing strong support for the development of high-performance electronic systems. An in-depth understanding of the characteristics of various packaging substrates enables us to better appreciate the value and application prospects of MEGTRON 4 in electronic engineering.
What is the difference between MEGTRON 4 PCB and traditional PCB?
In the field of electronic packaging, MEGTRON 4 PCB is creating a new paradigm, which presents eye-catching differences in several key aspects compared with traditional printed circuit boards (PCBs). Let’s dig deeper into the differences, covering printed circuit boards (PWBs), motherboards, substrates, substrate-like PCBs (SLP), and high-density interconnect (HDI) substrates.
The evolution of printed circuit boards (PWBs)
MEGTRON 4 PCB significantly changes the face of printed circuit boards (PWBs) through its superior materials and manufacturing processes. Compared with traditional PWBs, MEGTRON 4 exhibits higher thermal stability and mechanical strength, making it perform better under high temperatures, high frequencies and complex environments.
Motherboard innovation
The motherboard is the core of electronic equipment, and MEGTRON 4 PCB injects new life into it. Its excellent signal integrity and thermal conductivity allow the motherboard to play a greater role in highly integrated systems, providing a significant improvement in the overall performance of the device.
Substrate superior performance
The limitations of traditional substrates are their challenges with high-frequency signals and thermal management. MEGTRON 4 PCB has successfully overcome these obstacles with its excellent dielectric properties and thermal conductivity, allowing the substrate to perform well in high-frequency applications and complex circuit layouts.
Innovation of substrate-like PCB (SLP)
Substrate-like PCBs (SLPs) are an integral part of modern electronic equipment, and MEGTRON 4 PCBs make SLP designs more flexible while maintaining high performance and stability through their high integration and superior reliability.
The evolution of high-density interconnect (HDI) substrates
In the field of high-density interconnect (HDI) substrates, MEGTRON 4 once again breaks through traditional limitations. Its advanced manufacturing technology and material selection have enabled HDI substrates to achieve significant improvements in space utilization, signal transmission speed and heat dissipation.
MEGTRON 4 PCB is not only a new type of printed circuit board, but also a revolutionary force in the field of electronic packaging. Through differences from traditional PCBs in terms of PWBs, motherboards, substrates, SLP and HDI substrates, MEGTRON 4 demonstrates its excellent performance and diversified applications, opening up a new situation for the development of future electronic equipment.
The main structure and production technology of MEGTRON 4 PCB?
As the leader in the field of printed circuit boards, MEGTRON 4 PCB’s excellent performance is not only reflected in its functions, but also deeply derived from its complex and precise main structure and advanced production technology.
The main structure
The primary structural design of MEGTRON 4 PCB is designed to provide excellent signal transmission, thermal management and electrical performance. Among them, key components include highly conductive copper foil layers, dielectric material layers and the latest generation packaging technology. The high conductivity of the copper foil layer ensures fast signal transmission, while the superior dielectric material layer provides excellent insulation and heat dissipation properties. This structural design makes MEGTRON 4 PCB competent in a variety of applications, from high-speed communications to complex electronic equipment.
Manufacturing process
The exceptional performance of MEGTRON 4 PCB hinges on its sophisticated manufacturing process. Leveraging state-of-the-art High-Density Interconnect (HDI) technology, the circuit achieves shorter signal transmission paths by minimizing the distance between components. This advancement not only enhances circuit board integration but also effectively mitigates the risk of electromagnetic interference, ensuring a stable transmission of high-frequency signals. The result is an optimized response speed of the circuit, underlining the significance of advanced manufacturing techniques in achieving superior performance in MEGTRON 4 PCBs.
In addition, MEGTRON 4 PCB adopts an improved semi-additive method, which achieves higher circuit density and smaller component size through precise material stacking and precise patterning process. This advanced manufacturing technology not only improves PCB performance but also enhances its reliability and stability.
HDI manufacturing technology
High-density interconnect manufacturing technology plays an important role in the manufacturing process of MEGTRON 4 PCB. Through multiple layers of fine circuit layers and precise apertures, HDI technology achieves higher circuit density and smaller component spacing, providing greater design freedom for circuits. This flexibility not only increases the integration level of the circuit board, but also reduces the overall size, meeting the needs of modern electronic equipment for lightweight and miniaturization.
Taken together, the excellent performance of MEGTRON 4 PCB comes not only from its advanced manufacturing process, but also from its carefully designed main structure. This combination makes MEGTRON 4 PCB an indispensable and key component in today’s electronic field, providing reliable electronic solutions for a variety of applications.
MEGTRON 4 PCB FAQs
What is MEGTRON 4 PCB?
MEGTRON 4 PCB is an advanced printed circuit board using the latest technology and materials designed to provide superior performance and reliability. Its core features include enhanced signal integrity and superior thermal management, making it ideal for electronic system designs.
How is MEGTRON 4 PCB different from traditional PCB?
Compared with traditional PCB, MEGTRON 4 PCB has significant advantages in signal transmission, thermal endurance and electrical performance. Its unique structure and advanced manufacturing technology make it stand out in high-performance applications.
What application scenarios is MEGTRON 4 PCB suitable for?
MEGTRON 4 PCB is suitable for various application scenarios, including communication equipment, medical equipment, automotive electronics and high-performance computing. Its versatility and reliability make it the first choice in many fields.
How does MEGTRON 4 PCB improve thermal management of electronic systems?
MEGTRON 4 PCB uses advanced heat dissipation materials and designs to effectively improve the thermal management performance of electronic systems. This means higher efficiency and longer component life, especially in high-temperature environments.
Is specialized manufacturing technology required to use MEGTRON 4 PCB?
The manufacturing technology of MEGTRON 4 PCB is relatively high, but it is compatible with conventional PCB manufacturing processes. However, in order to give full play to its advantages, it is recommended to adopt advanced HDI manufacturing technology and improved semi-additive method in the manufacturing process.
What is the cost of MEGTRON 4 PCB?
MEGTRON 4 PCBs may be slightly more expensive than traditional PCBs, but their performance improvements and long-term reliability more than justify the cost. In critical applications requiring high performance and reliability, the advantages far outweigh the cost difference.
Can MEGTRON 4 PCB be used in all electronic systems?
MEGTRON 4 PCB is a general purpose printed circuit board suitable for most electronic systems. However, when selecting, the requirements of the specific application should be considered to ensure that its superior performance matches the needs of the system.