What is MEGTRON 8 PCB?
MEGTRON 8 PCB Manufacturer.MEGTRON 8 PCB Manufacturer is a leading provider of advanced printed circuit boards, renowned for its cutting-edge technology and unwavering commitment to quality. Specializing in the production of MEGTRON 8 PCBs, they excel in delivering high-performance solutions tailored to diverse industry needs. With state-of-the-art manufacturing facilities and a team of skilled professionals, they ensure precision engineering and superior reliability in every product. From concept to completion, MEGTRON 8 PCB Manufacturer sets the benchmark for innovation and excellence, driving forward progress in electronics manufacturing with unparalleled expertise and dedication.
In the modern electronics industry, packaging substrates play a key role, and one of the materials that has attracted much attention is MEGTRON 8 PCB. MEGTRON 8 represents advanced technology and excellent performance, becoming the choice of electronic equipment manufacturers pursuing excellence. This article will provide an in-depth introduction to the unique features of MEGTRON 8 PCB and reveal its leading position in the field of packaging substrates.
As electronic technology continues to evolve, the requirements for packaging substrates are also increasing, requiring more advanced and reliable materials to meet market demands. In this field, MEGTRON 8 PCB stands out due to its excellent features and performance. This article will lead readers to have an in-depth understanding of the key characteristics, manufacturing process and wide application of MEGTRON 8 PCB in the electronics industry. It aims to present readers with a comprehensive and clear picture and interpret the unique position of MEGTRON 8 in the field of packaging substrates. By delving into its benefits and future trends, we’ll reveal how this material is driving the electronics industry forward.
Ultra-low Loss, Highly Heat Resistant Circuit Board Materials
Ultra-low transmission loss and high heat resistance circuit board materials are innovative electronic materials that are critical to meeting the performance, reliability and operation requirements of modern electronic equipment in high-temperature environments. This advanced circuit board material plays an important role in communications, radio frequency electronics, high-performance computers and other fields through its unique properties.
First, the material has the excellent property of ultra-low transmission loss. In electronic communications and radio frequency applications, signal transmission loss is a key consideration. This circuit board material effectively reduces energy loss during signal transmission by using optimized conductive layers and dielectric materials. Low transmission loss means signals can be transmitted over longer distances and at higher frequencies, improving system performance and response speed. This is particularly critical for applications requiring high frequency and large data transmission, such as 5G communications and high-speed data transmission.
Secondly, the circuit board material exhibits excellent high heat resistance. High temperature stability allows the circuit board to maintain reliability under extreme conditions, ensuring that the device can operate normally in various environments.
In addition to low transmission losses and high thermal resistance, the circuit board material also exhibits excellent mechanical strength and chemical resistance. This enables it to maintain stability in various complex manufacturing and use environments and extend the service life of the equipment.
This circuit board material, renowned for its ultra-low transmission loss and exceptional heat resistance, has found extensive applications across diverse sectors, encompassing communication base stations, satellite communications, high-performance computers, and medical equipment. As the demand for higher frequencies and increasingly intricate electronic systems continues to surge, the significance of this material is poised to escalate further. The ongoing refinement of its performance characteristics will drive advancements in the electronic manufacturing industry, catering to the demands of high-performance applications, fostering the evolution of innovative technologies, and contributing to the enhanced performance of electronic equipment.
Laminate R-5795(U)/ Prepreg R-5690(U) Laminate R-5795(N)/ Prepreg R-5690(N)
Laminate R-5795(U) / Prepreg R-5690(U) and Laminate R-5795(N) / Prepreg R-5690(N) represent a sophisticated pair of laminate and prepreg materials extensively employed in high-performance electronics and communication systems. Renowned for their exceptional performance and adaptability, both material families offer dependable solutions for the production of intricate circuit boards.
First, the Laminate R-5795(U) / Prepreg R-5690(U) series has excellent electrical conductivity and mechanical strength. This conductive property makes it ideal for high frequency and radio frequency electronic applications, ensuring stable and reliable signal transmission. In terms of mechanical strength, this series of materials maintains structural integrity under various environmental conditions, thereby reducing the risk of circuit board damage during manufacturing, transportation and use.
Secondly, the Laminate R-5795(N) / Prepreg R-5690(N) series emphasizes its high temperature resistance. The material’s ability to remain stable in extreme temperature environments makes it suitable for applications that require high temperature resistance, such as aerospace and automotive engine control systems. This family of materials performs well in high-temperature environments, not only maintaining circuit board performance but also ensuring reliable system operation.
Two series of prepreg segments, R-5690(U) and R-5690(N), play a key role in the circuit board manufacturing process. Prepreg is fiberglass cloth impregnated with resin and is used to prepare the chip layers of multilayer circuit boards. These prepregs have excellent lamination properties and are able to form strong laminate structures under high temperature and pressure conditions.
Both material series meet the stringent requirements for performance and reliability set by the electronics manufacturing industry. Their outstanding capabilities in high-frequency, radio-frequency, and high-temperature environments position them as the preferred choice in critical fields like communication base stations, satellite communication equipment, radar systems, and high-performance computers. This not only enhances system performance but also contributes to prolonged equipment lifespan and reduced maintenance costs.
In essence, the comprehensive attributes of the Laminate R-5795(U) / Prepreg R-5690(U) and Laminate R-5795(N) / Prepreg R-5690(N) material series solidify their standing as highly sought-after materials in the dynamic landscape of the electronics manufacturing industry.Favored material selection. As technology continues to develop, these two series of materials will continue to promote innovation in the electronics industry and provide a reliable foundation for more advanced electronic devices and systems in the future.
Designed for high-speed communication network equipment such as routers and switches, MEGTRON 8 multi-layer circuit board material features the industry’s lowest transmission loss. This contributes to larger capacity and higher-speed data communication and may reduce power consumption because of the lower transmission loss.
The MEGTRON 8 family supports 800GbE used for next-generation high-speed communication technology and offers about a 30% improvement in transmission loss compared to MEGTRON 7.
R-5795(N)/R-5690(N)
Specification / Laminate R-5795(N) & R-5795(U)
Property | Units | Test Method | Condition | Typical Value | |||
R-5795(N) Low-Dk glass |
R-5795(U) Ultra Low-Df glass |
||||||
PHYSICAL | DMA | As received | 220 | 220 | |||
Thermal Decomposition Temp ( Td ) | C | TGA | As received | 370 | 370 | ||
Time to Delam ( T288 ) |
With Cu | min | IPC TM-650 2.4.24.1 | As received | > 120 | > 120 | |
CTE :α1 | X – axis | ppm/C | IPC TM-650 2.4.24 | < Tg | 17~20 | 17~20 | |
Y – axis | ppm/C | IPC TM-650 2.4.24 | < Tg | 17~20 | 17~20 | ||
Z – axis | ppm/C | IPC TM-650 2.4.24 | < Tg | 50 | 50 | ||
CTE :α2 | Z – axis | ppm/C | IPC TM-650 2.4.24 | > Tg | 270 | 270 | |
Dielectric Constant (Dk ) |
@14GHz | ⁻ | IPC TM-650 2.5.5.9 | C-24/23/50 | 3.13 | 3.08 | |
Dissipation Factor (Df) |
@14GHz | ⁻ | IPC TM-650 2.5.5.9 | C-24/23/50 | 0.0016 | 0.0012 | |
Water Absorption | % | IPC TM-650 2.6.2.1 | D-24/23 | 0.06 | 0.06 | ||
Peel Strength | 1oz(H-VLP3) | kN/m | IPC TM-650 2.4.8 | As Received | 0.7 | 0.7 | |
Flammability | ⁻ | UL | C-48/23/50 | 94V-0 | 94V-0 | ||
Sample thickness ;32 mil (0.8 mm) #1078 x 10 ply | |||||||
The data in the above table are not guaranteed values. |
R-5795(U)/R-5690(U)
Specification / Laminate R-5795(N) & R-5795(U)
Property | Units | Test Method | Condition | Typical Value | |||
R-5795(N) Low-Dk glass |
R-5795(U) Ultra Low-Df glass |
||||||
PHYSICAL | Glass Transition Temp (Tg) | C | DMA | As received | 220 | 220 | |
Thermal Decomposition Temp ( Td ) | C | TGA | As received | 370 | 370 | ||
Time to Delam ( T288 ) |
With Cu | Min | IPC TM-650 2.4.24.1 | As received | > 120 | > 120 | |
CTE :α1 | X – axis | ppm/C | IPC TM-650 2.4.24 | < Tg | 17~20 | 17~20 | |
Y – axis | ppm/C | IPC TM-650 2.4.24 | < Tg | 17~20 | 17~20 | ||
Z – axis | ppm/C | IPC TM-650 2.4.24 | < Tg | 50 | 50 | ||
CTE :α2 | Z – axis | ppm/C | IPC TM-650 2.4.24 | > Tg | 270 | 270 | |
ELECTRICAL | Dielectric Constant (Dk ) |
@14GHz | ⁻ | *Note 1 | C-24/23/50 | 3.13 | 3.08 |
Dissipation Factor (Df) |
@14GHz | ⁻ | *Note 1 | C-24/23/50 | 0.0016 | 0.0012 | |
PHYSICAL | Water Absorption | % | IPC TM-650 2.6.2.1 | D-24/23 | 0.06 | 0.06 | |
Peel Strength | 1oz(H-VLP3) | kN/m | IPC TM-650 2.4.8 | As Received | 0.7 | 0.7 | |
Flammability | ⁻ | UL | C-48/23/50 | 94V-0 | 94V-0 | ||
Sample thickness ;32 mil (0.8 mm)=0.750mm(1078 X 10ply) | |||||||
The data in the above table are not guaranteed values. |
Package substrate: the cornerstone of MEGTRON 8 PCB?
In the technological wave led by MEGTRON 8 PCB, the packaging substrate is like a solid cornerstone, supporting the peak of its vigorous development. As a PCB engineer with ten years of work experience, I delved into this key area and understood the key role of the packaging substrate in the entire MAGTRON 8 PCB system.
In this fascinating world, packaging substrates play a key supporting role, serving as the solid foundation for integrated circuits (ICs). Its role is not just simple support, but also has a profound impact on the overall performance of electronic equipment. The design and quality of the packaging substrate are directly related to the stability, reliability and performance excellence of the entire circuit.
Packaging substrates effectively support and connect integrated circuits by providing a stable platform to ensure their normal operation in electronic devices. Its material selection, hierarchical structure and manufacturing process are carefully designed to respond to the needs of different application scenarios and working environments.
When we deeply understand the role of the packaging substrate in MEGTRON 8 PCB, we find that it is not only a physical support structure, but also a complex and critical component. Its highly conductive properties, excellent thermal management characteristics, and excellent transmission capabilities for high-frequency signals enable the entire MAGTRON 8 PCB system to perform excellently in complex and demanding electronic environments.
During the design phase, engineers need to carefully consider the layout, size and materials of the package substrate to ensure it blends perfectly with the integrated circuit and maximizes performance. This process requires not only considering the overall architecture of the MEGTRON 8 PCB, but also fully understanding the working principles and performance requirements of the integrated circuit.
Therefore, the packaging substrate is not only the cornerstone of the MAGTRON 8 PCB, but also a key driver of its superior performance and reliability. Its design and manufacturing level directly affect the performance of the entire PCB system, providing reliable support for the stable operation of electronic equipment. In this field of rapidly changing technology, a deep understanding of the role of packaging substrates will be a source of continuous exploration and innovation for PCB engineers.
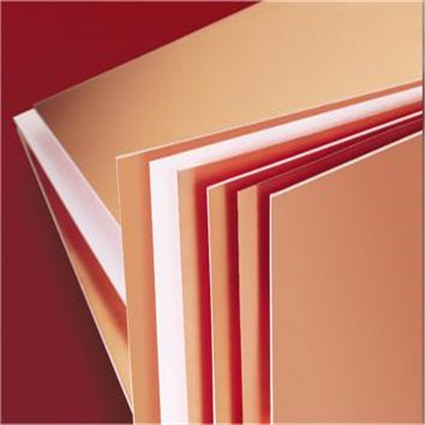
MEGTRON 8 PCB Manufacturer
MEGTRON 8 PCB Features: Revealing Its Power?
As an outstanding representative in today’s PCB engineering field, MEGTRON 8 PCB has become the mainstay in improving the performance of electronic equipment with its excellent functions and unique characteristics. Its power lies in its critical role in signal integrity, thermal management and overall reliability, breathing new life into our electronic lives.
Excellent guarantee of signal integrity
MEGTRON 8 PCB shows unparalleled superiority in ensuring signal integrity. Its advanced design and material selection ensure the stability of signal transmission and effectively reduce the risk of signal distortion. Whether it is high-frequency or low-frequency applications, MEGTRON 8 PCB demonstrates excellent protection of signal integrity, making it an ideal choice for all types of electronic equipment.
Innovative applications of thermal management
Thermal management is a vital aspect in the design of modern electronic equipment, and MEGTRON 8 PCB excels in this regard through its unique thermal management properties. The excellent thermal conductivity of its material and structural design effectively disperse and dissipate heat, ensuring that electronic components always maintain a suitable temperature during work. This not only improves the efficiency of electronic equipment, but also extends the service life of components.
Guarantee of overall reliability
MEGTRON 8 PCB provides excellent overall reliability for electronic equipment. The material’s high stability and oxidation resistance allow it to maintain excellent performance in a variety of environmental conditions, thereby reducing the risk of equipment damage and repair. Under extreme working conditions, MEGTRON 8 PCB can still work robustly, ensuring continued reliability of the equipment.
Overall, MEGTRON 8 PCB provides strong support for electronic devices with its excellent signal integrity, thermal management and overall reliability. Whether it is communication equipment, medical equipment or consumer electronics, MEGTRON 8 PCB has demonstrated its unique value in improving performance and reliability. As a PCB engineer with ten years of experience, I deeply understand the importance of MEGTRON 8 PCB and believe that it will continue to lead the innovation trend of electronic technology.
MEGTRON 8 Different Types of PCBs: Diverse Looks?
MEGTRON 8 PCB leads the way with its engineering excellence and flexibility, displaying stunning diversity. This new realm of PCB technology is not only an improvement in standard configurations, but also an exquisite pursuit of professional design, providing tailor-made solutions for various industries.
When exploring the different types of MEGTRON 8 PCBs, we first need to understand how they are tailored to meet the needs of various industries. This tailor-made process is not a simple parameter adjustment, but deeply integrated into the technical, performance and environmental requirements of the specific industry. Each MEGTRON 8 PCB variant is a perfect representation of this process.
Starting from standard configuration, MEGTRON 8 PCB offers excellent performance for general purpose applications. Its advanced materials and processes ensure excellence in signal integrity, thermal management and reliability. This makes MEGTRON 8 PCB ideal for a wide range of electronic devices, ranging from consumer electronics to communications equipment.
However, this is just the tip of the iceberg in the diverse features of MEGTRON 8 PCB. What is even more eye-catching is its professional design, tailored to industry needs. For example, in the medical field, the need for high precision and reliability may drive MEGTRON 8 PCBs to adopt more complex hierarchies and advanced materials to ensure the stability and performance of medical devices.
For automotive electronics, MEGTRON 8 PCB may be designed as a solution that can withstand extreme temperatures and vibration environments, ensuring the reliability of vehicle electronic systems. This professional design goes beyond that, as MEGTRON 8 PCB is more than just a circuit board, it is an innovative tool adapted to the challenges of different industries.
The diversity of MEGTRON 8 PCBs lies in the range of options available. Whether it is a general-purpose application pursuing excellent performance or in-depth optimization for specific industry needs, MEGTRON 8 PCB can provide a highly flexible and reliable solution.
MEGTRON 8 PCB vs. Traditional PCB: Bridging the Gap?
In today’s rapidly developing electronic field, MEGTRON 8 PCB, as an innovative and reliable technology, shows significant differences compared with traditional PCB. Its advanced features, especially PCB-like substrates (SLP) and high-density interconnect (HDI) substrates, make MEGTRON 8 uniquely advantageous in PCB engineering.
One of the most significant differences between MEGTRON 8 PCB and traditional PCB is the packaging substrate technology it uses. Traditional PCBs usually use conventional materials, and MEGTRON 8 has become a representative of the new generation of PCB technology with its excellent thermal stability and mechanical strength. This characteristic performs better especially in high-temperature and high-frequency environments, providing a solid foundation for the reliability of electronic equipment.
MEGTRON 8 stands out with its distinctive Printed Circuit Board (PCB)-like substrate (SLP) and High-Density Interconnect (HDI) substrate, offering a unique proposition in the world of electronic components. The SLP technology employed by MEGTRON 8 enables a more compact PCB packaging, facilitating smaller and lighter electronic designs. Beyond the space-saving benefits, this compactness allows for more intricate circuit designs, enhancing the overall capabilities of electronic equipment.
Complementing this innovation is the HDI technology, further elevating the density and performance of MEGTRON 8 PCBs. The integration of HDI technology enhances signal transmission, reducing both the distance and delay in signal transmission compared to traditional PCBs. This, in turn, significantly improves the response speed of the entire system—an invaluable advantage in scenarios demanding high performance and low latency, such as communication equipment and high-performance computing systems.
Moreover, the unique design of MEGTRON 8 PCB extends its advantages to thermal management. With exceptional thermal conductivity and stability, it excels in dissipating heat, effectively lowering system temperatures. This not only enhances the efficiency and lifespan of electronic components but also holds particular significance for applications with high power density, such as power modules and radio frequency (RF) equipment.
In summary, MEGTRON 8 PCB bridges the gap with traditional PCBs by incorporating advanced substrate technologies like PCB-like substrates (SLP) and High-Density Interconnect (HDI) substrates. Its stellar performance plays a pivotal role in the design and manufacturing of electronic equipment, unlocking new possibilities for future PCB engineering. As engineers pursue smaller, more efficient, and more reliable electronic solutions, MEGTRON 8 PCB emerges as a preferred choice, marking a significant stride towards the realization of these objectives.
MEGTRON 8 PCB structure and production technology complexity?
MEGTRON 8 PCB, as a leader in PCB engineering, its excellent performance not only stems from its unique design, but also from its complex and precise structure and advanced production technology.
When exploring the structure of MEGTRON 8 PCB, we found that its design is not a simple stack of layers, but an ingenious engineering construction. Its substrate uses improved high-density interconnect (HDI) manufacturing technology, which means circuit components are laid out more compactly, helping to improve circuit performance and stability. Through HDI, MEGTRON 8 PCB can accommodate more components in a relatively small space, allowing electronic devices to achieve an ideal balance between size and performance.
But this is just the tip of the iceberg, as an innovative semi-additive method is used in the production of MEGTRON 8 PCB. This method uses more refined processes during the manufacturing process to reduce the spacing between components and improve the integration of components on the board. The use of the semi-additive method makes the wires finer, reduces the signal transmission delay, and further improves the performance of the PCB. The application of this manufacturing method plays a decisive role in meeting the needs of modern electronic equipment for high performance and high stability.
The manufacturing process of MEGTRON 8 PCB does not stop here. What is even more eye-catching is that it adopts improved HDI manufacturing technology. The core of this technology is to achieve precise control of the circuit board and improve the performance of the PCB through multi-layer stacking and miniaturization processes. Compared with traditional PCB manufacturing methods, the application of this technology makes MEGTRON 8 PCB perform better in high frequency and high-speed transmission.
Overall, the sophistication of MEGTRON 8 PCB’s construction and production technology are the cornerstones of its outstanding performance. Through continuously innovative HDI manufacturing and semi-additive methods, MEGTRON 8 PCB not only achieves precision design in structure, but also reaches an advanced level in production technology, providing excellent performance and reliability for electronic equipment.
Frequently Asked Questions (FAQs): Revealing the secrets of MEGTRON 8 PCB?
As we delve deeper into MEGTRON 8 PCB technology, we cannot ignore the common questions surrounding this fascinating field. Here, we’ll pull back the technical veil on the MEGTRON 8 PCB and answer questions frequently asked by engineers and enthusiasts, from its compatibility with a variety of applications to its key role in environmental sustainability.
Which application areas are MEGTRON 8 PCB suitable for?
The design flexibility of MEGTRON 8 PCB makes it suitable for a wide range of applications. Whether in communications equipment, consumer electronics, medical equipment or aerospace, MEGTRON 8 PCBs demonstrate superior performance and reliability. Its high frequency transmission and superior signal integrity make it ideal for high performance electronic systems.
Does MEGTRON 8 PCB meet environmental standards?
Yes, MEGTRON 8 PCB is designed to comply with modern environmental requirements. The technologies and materials used in its manufacturing process comply with the latest environmental regulations. In addition, the reliability and durability of MEGTRON 8 PCBs ensure a long service life and reduce the generation of electronic waste.
How does MEGTRON 8 PCB handle thermal management?
MEGTRON 8 PCB excels in thermal management. Its material and structural design help to effectively disperse and conduct heat, ensuring that electronic equipment maintains a stable temperature when operating under high loads. This makes MEGTRON 8 PCB a vital choice for heat-sensitive applications.
Is the MEGTRON 8 PCB easy to maintain?
Yes, MEGTRON 8 PCBs are designed with ease of maintenance in mind. Its construction and material selection help simplify maintenance processes, reduce maintenance costs, and reduce downtime. This is a significant advantage for many industries.
By answering these frequently asked questions, we not only reveal the technical secrets of MEGTRON 8 PCB, but also highlight its superior performance in every aspect. As an important innovation in the field of electronic engineering, MEGTRON 8 PCB’s outstanding performance in compatibility, sustainability, thermal management performance and maintainability make it the first choice for today’s advanced electronic systems. Whether you are an engineer or an enthusiast, understanding every aspect of this technological marvel will provide profound insights into future developments.
Conclusion: MEGTRON 8 PCB – Shaping the future of electronics?
Through in-depth exploration of MEGTRON 8 PCB, we not only understand its outstanding performance in the field of electronic equipment, but also see its key role in the future development of PCB engineering. Let us review the contribution of MEGTRON 8 PCB in the evolution of electronics and its role in shaping the future of PCB engineering by summarizing the important points.
First of all, the role of the packaging substrate cannot be ignored. As this fundamental component, MEGTRON 8 PCB provides solid support for integrated circuits through its superior features such as high-density interconnect (HDI) and PCB-like substrate (SLP). This allows it to perform well in a variety of environmental conditions, ensuring the signal integrity and stability of the device.
Secondly, the diversity of MEGTRON 8 PCB is impressive. Different types of MEGTRON 8 PCB are carefully designed according to the needs of different industries, and have been widely used in communications, medical, automotive and other fields. This flexibility makes MEGTRON 8 PCB ideal for meeting diverse engineering needs.
In terms of structure and production technology, MEGTRON 8 PCB adopts advanced manufacturing processes, such as improved HDI manufacturing technology and semi-additive method. This not only improves production efficiency, but also further enhances product reliability and performance.
Reflecting on this journey of exploration, the impact of MEGTRON 8 PCB on the realm of electronic equipment becomes unmistakably evident. Its role extends beyond providing a robust foundation for current technological developments; it serves as a trailblazer for the future of PCB engineering. Through this guest article, my aim is to convey a comprehensive understanding of MEGTRON 8 PCB, underscoring its distinctive value within the PCB engineering domain.
Should there be specific aspects requiring more in-depth coverage or if you wish to incorporate additional information, please feel free to provide further guidance. MEGTRON 8 PCB not only stands out as a highlight in contemporary PCB engineering but also emerges as a guiding force for future developments, making significant contributions to the ongoing progress in the field of electronics.