What are Low Dk Epoxy Resin Materials PCBs?
Low Dk Epoxy Resin Materials PCBs Manufacturer.”Specializing in the production of low Dk epoxy resin materials, our company stands as a premier manufacturer of PCBs, catering to diverse industrial needs. With a focus on cutting-edge technology and meticulous craftsmanship, we engineer high-performance circuit boards that ensure optimal signal integrity and reliability. Our commitment to quality extends from material selection to manufacturing processes, guaranteeing products that meet stringent standards. Whether for telecommunications, aerospace, or automotive applications, our PCBs deliver unparalleled performance, setting new benchmarks in the industry. Trust us as your partner for innovative solutions in electronic manufacturing.”
In PCB design, the low dielectric constant holds significant importance as an electrical characteristic. This parameter gauges how much a material influences the propagation of electromagnetic waves, and a low dielectric constant indicates that the material has minimal impact on electromagnetic signals. For Low Dk Epoxy Resin Materials PCBs, this attribute yields multiple advantages.
Firstly, a low dielectric constant contributes to minimizing losses in signal transmission. In high-frequency applications, the energy loss on signal transmission lines is a critical consideration. The utilization of a low dielectric constant can diminish the capacitance of signal transmission lines, thereby curbing energy dissipation. This implies that under high-frequency conditions, Low Dk Epoxy Resin Materials PCBs can effectively transmit signals, mitigate signal attenuation, and enhance signal integrity.
In summary, the benefits derived from a low dielectric constant in Low Dk Epoxy Resin Materials PCBs primarily manifest in its positive impact on signal transmission performance. By diminishing the capacitance of signal transmission lines and mitigating crosstalk, these PCBs excel in high-frequency and high-performance applications. This excellence establishes a robust foundation for the reliability and stability of electronic products, making Low Dk Epoxy Resin Materials PCBs a preferred choice for engineers designing electronic devices that demand high performance and low signal distortion in complex electromagnetic environments.
Why choose Low Dk Epoxy Resin Materials PCBs?
A notable choice in this realm is the Low Dk Epoxy Resin Materials PCB, distinguished by its unique properties that confer significant advantages to the design of cutting-edge electronic devices.
Central to the appeal of Low Dk Epoxy Resin Materials PCBs in high-performance electronic devices is their markedly reduced dielectric constant (Low Dk). This property is pivotal, as the dielectric constant gauges a material’s responsiveness to an electric field.Low Dk Epoxy Resin Materials PCBs play a crucial role in enhancing circuit performance by mitigating these adverse effects.
Additionally, these PCBs showcase superior signal integrity, adeptly meeting the demands imposed by higher transmission rates in contemporary high-speed electronic equipment. Their low dielectric constant allows for the reduction of signal propagation delay and waveform distortion, ensuring a more reliable transmission of signals.
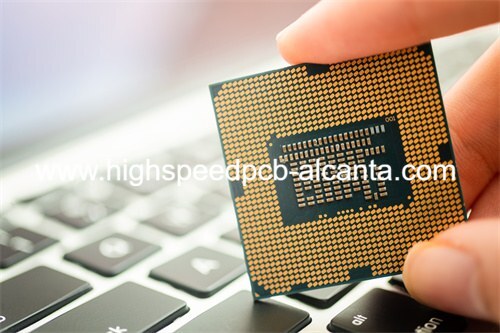
Low Dk Epoxy Resin Materials PCBs Manufacturer
Beyond this, the choice of Low Dk Epoxy Resin Materials PCBs translates into improved thermal performance compared to conventional materials, a critical aspect for high-power electronic equipment.
Their exceptional mechanical properties and resistance to corrosion enable stable operation under diverse and challenging conditions, establishing a robust foundation for the sustained and long-term use of electronic equipment.
In summary, the preference for Low Dk Epoxy Resin Materials PCBs over traditional materials is grounded in a deep understanding of the design requirements of high-performance electronic equipment. Their low dielectric constant, superior signal integrity, commendable thermal performance, and outstanding reliability position them as an ideal choice for the demands of contemporary advanced electronic equipment. In the ongoing pursuit of heightened performance and reliability, Low Dk Epoxy Resin Materials PCBs are poised to continue playing a pivotal role in the field of electronic engineering.
What is the manufacturing process of Low Dk Epoxy Resin Materials PCBs?
The production of PCBs using Low Dk Epoxy Resin Materials is an intricate and technology-intensive process, encompassing several critical stages to ensure the uniformity and high performance of the final product.
Initially, the material selection stands out as a pivotal step in the manufacturing of Low Dk Epoxy Resin Materials PCBs. Opting for an epoxy with a low dielectric constant is paramount to guarantee optimal board performance, particularly at high frequencies. This selection significantly influences the overall effectiveness of the circuit board, necessitating a delicate balance between dielectric properties, mechanical strength, and material processability.
Following material selection, layer-by-layer stacking emerges as another crucial phase in the manufacturing process. This step dictates the hierarchical structure of the circuit board, outlining internal inter-layer connections and the stacking arrangement between layers. For Low Dk Epoxy Resin Materials PCBs, the layer-by-layer stackup design must intricately consider the placement of low-dielectric constant materials to minimize signal transmission losses effectively.
Subsequently, chemical treatment became an important part of ensuring the quality and performance of circuit boards. This includes the use of chemical etching to define circuit patterns, blind via drilling to form internal connections, and metallization to enhance conductivity. For Low Dk Epoxy Resin Materials PCBs, these chemical processes specifically need to be precisely controlled to ensure other performance requirements are achieved while maintaining a low dielectric constant.
Throughout the entire manufacturing process, control of precision and consistency is critical. Any manufacturing errors can cause the board to degrade or fail.
These steps are often customized based on specific engineering needs to meet the customer’s unique requirements for board performance.
To sum up, manufacturing Low Dk Epoxy Resin Materials PCBs is a highly process-oriented task that requires manufacturers to maintain a high level of technology and precision at every step. Through these key steps, Low Dk Epoxy Resin Materials PCBs are able to maintain their excellent performance in high-frequency applications and become an important part of modern electronic engineering design.
What are the application fields of Low Dk Epoxy Resin Materials PCBs?
High-Speed Communication Field
In realms such as 5G communications and optical fiber communications, where signal transmission speed and stability are paramount, the role of Low Dk Epoxy Resin Materials PCBs is crucial. Their low dielectric constant effectively minimizes attenuation and signal distortion during transmission, making them extensively utilized in high-speed communication environments. Notably, these materials support high-frequency signal transmission, ensuring the clarity and stability of data over extended distances. Consequently, engineers frequently opt for Low Dk Epoxy Resin Materials PCBs when constructing high-speed communication base stations, data centers, and communication equipment, ensuring the swift and efficient transmission of data.
Radio Frequency Electronics Field
In the realm of radio frequency electronics, Low Dk Epoxy Resin Materials PCBs excel. Given that radio frequency equipment demands stability and efficiency in signal transmission at high frequencies, Low Dk Epoxy Resin Materials PCBs emerge as a fitting choice to meet these specific requirements.
For radio frequency applications such as wireless communication equipment, radar systems and satellite communications, engineers rely on the performance of Low Dk Epoxy Resin Materials PCBs to ensure stable operation of the system in complex electromagnetic environments. Its excellent dielectric properties and signal integrity make it occupy an important position in RF electronic design.
Medical electronics field
In the realm of medical electronics, stringent demands for high performance and adherence to industry-specific requirements, such as biocompatibility and reliability, are paramount. The distinctive value of Low Dk Epoxy Resin Materials PCBs in this sector lies in their unparalleled reliability and stability within medical devices.
Medical electronic equipment, including intricate devices like MRI machines, pacemakers, and internally implanted sensors, necessitates circuit boards that excel in both performance and stability. The low dielectric constant inherent in these boards mitigates signal transmission losses, ensuring heightened precision and reliability in medical equipment. Furthermore, the biocompatible nature of the material permits safe interaction with human tissue, aligning seamlessly with clinical standards for medical devices.
In summary, Low Dk Epoxy Resin Materials PCBs showcase exceptional performance across applications in high-speed communications, radio frequency electronics, and especially medical electronics. Their reliability and unique electrical and mechanical properties make them a preferred material for engineers shaping intricate electronic systems, laying a steadfast foundation for technological innovation and advancement in these specialized fields.
How to obtain Low Dk Epoxy Resin Materials PCBs?
Effective collaboration with professional suppliers and manufacturers is imperative for obtaining customized Low Dk Epoxy Resin Materials PCBs that align with specific design needs. In navigating this collaboration, the following detailed approach outlines how to engage with our company as the supplier:
As the electronics industry undergoes continuous development, the rising demand for Low Dk Epoxy Resin Materials PCBs underscores the significance of partnering with proficient suppliers and manufacturers to optimize their performance in circuit design.
This may involve detailed technical details on material selection, laminate construction, chemical treatments, etc. By discussing these critical issues with suppliers, design teams can better understand the manufacturing process of Low Dk Epoxy Resin Materials PCBs and ensure their successful application in projects.
For customized Low Dk Epoxy Resin Materials PCBs, the design team should be actively involved in the sample making and testing process. Working with suppliers to verify the feasibility of the design and verify whether samples perform as expected are important steps to ensure the success of the final product. This also provides an opportunity for both parties to work together to solve problems and optimize designs.
Throughout the collaborative process, the design team should meticulously consider the manufacturing capabilities and supply chain management of the chosen supplier. The supplier’s proficiency in production and their ability to adhere to scheduled deliveries are pivotal factors crucial for the successful execution of the project. Regular updates on production progress and comprehensive quality control reports serve as valuable tools for the design team, enabling them to monitor the project’s advancement and make necessary adjustments promptly.
In the grand scheme, establishing strategic relationships with suppliers stands out as the cornerstone of long-term success. By fostering trust-based connections with suppliers, design teams are better equipped to navigate project challenges, ensuring the optimal utilization of Low Dk Epoxy Resin Materials PCBs in circuit designs. This collaboration transcends a mere transactional relationship, evolving into a partnership that collectively propels technological innovation and project triumph.
How is the quotation of Low Dk Epoxy Resin Materials PCBs determined?
When obtaining a quotation for Low Dk Epoxy Resin Materials PCBs, multiple factors need to be considered to ensure that the final quotation not only fits the budget but also meets the design requirements. Here are the key factors in determining a quote and explore the effectiveness of direct communication with suppliers.
First of all, material cost is the primary factor in determining the quotation of Low Dk Epoxy Resin Materials PCBs. Low dielectric constant resins are typically more advanced and their preparation may involve high-performance chemistries, which has a direct impact on overall cost.
In addition, the degree of customization also has an important impact on the quotation. If specific specifications and a special level of custom design are required, it will increase the technical challenges of production and thus affect the overall cost. Therefore, when selecting Low Dk Epoxy Resin Materials PCBs, engineers need to weigh the specific requirements of the design against cost-effectiveness.
For engineers, direct communication with suppliers is one of the important ways to obtain accurate quotations. Direct communication helps to better understand the materials and services provided by the supplier, and allows for immediate feedback and suggestions. Suppliers may offer customized solutions for the design, detailing aspects such as material properties, production processes and costs.
However, engineers should remain open when communicating with suppliers and clearly communicate the key requirements of the design. This helps suppliers better understand the special features of the project and provide more accurate quotes. In addition, establishing a long-term cooperative relationship can help build mutual trust, make communication smoother, and potentially obtain more competitive prices and services.
In summary, obtaining an accurate quotation for Low Dk Epoxy Resin Materials PCBs requires comprehensive consideration of factors such as material cost, manufacturing process complexity, and degree of customization. Direct communication with suppliers is an effective way to ensure accurate quotes, which can lead to better cost-efficiency through in-depth understanding of materials and establishing good relationships. Such comprehensive considerations and active communication will help engineers better balance performance, cost and feasibility in their designs.
Frequently Asked Questions (FAQs)
What frequency ranges are Low Dk Epoxy Resin Materials PCBs suitable for?
Low Dk Epoxy Resin Materials PCBs are suitable for high frequency ranges, usually above GHz. Due to their low dielectric constant, this makes them ideal for processing high-frequency signals, reducing losses and crosstalk in signal transmission and improving overall performance.
How to ensure material consistency of Low Dk Epoxy Resin Materials PCBs during manufacturing process?
Strict quality control during the manufacturing process is key to ensuring material consistency of Low Dk Epoxy Resin Materials PCBs. Suppliers and manufacturers ensure that each production batch meets design specifications by using advanced process control and quality inspection technologies to avoid performance changes caused by material differences.
What application fields are Low Dk Epoxy Resin Materials PCBs suitable for?
Due to its excellent performance, Low Dk Epoxy Resin Materials PCBs are widely used in high-speed communication equipment, radio frequency electronics and medical electronics and other fields. Their low signal transmission loss makes them valuable for handling sensitive signals and maintaining signal integrity.
How to get customized Low Dk Epoxy Resin Materials PCBs?
Readers can get custom Low Dk Epoxy Resin Materials PCBs that meet their design needs by working directly with professional suppliers and manufacturers. Suppliers often provide tailor-made solutions to meet different engineering needs.
The answers to these FAQs are intended to help readers gain a more comprehensive understanding of Low Dk Epoxy Resin Materials PCBs so that they can choose and apply this material in electronic designs more confidently and wisely.