What are LCC Package Substrates?
LCC Package Substrate Manufacturer.An LCC Package Substrate Manufacturer specializes in producing Leadless Chip Carrier (LCC) package substrates, crucial components in semiconductor devices. They design and fabricate these substrates to provide reliable electrical connections and support for integrated circuits, ensuring optimal performance and durability in electronic applications. Their expertise includes advanced materials, precision engineering, and innovative manufacturing processes to meet the high standards of the electronics industry.
LCC Package Substrate Supplier, We offer BT base, Showa Denko/Ajinomoto high-speed Package substrates from 2 layer to 20, specializes in small pitch PCBs manufacturing.
LCC Package Substrates (low-cost ceramic package substrates) play an important role in PCB engineering. Simply put, they are a special type of substrate used in electronic packaging that is cost-effective and reliable. In PCB engineering, these substrates perform the critical task of supporting and connecting electronic components, such as chips, capacitors, resistors, etc. LCC Package Substrates are typically made of ceramic materials and therefore have excellent thermal conductivity and electrical properties. They are designed and manufactured to meet the needs of high-density integrated circuit packaging, providing reliable support and connections to ensure the proper operation of electronic devices.
In electronic packaging, the importance of LCC Package Substrates is self-evident. They provide a stable platform that enables various electronic components to operate in a closed environment while protecting them from the external environment. In addition, LCC Package Substrates also have good thermal conductivity properties, which can effectively disperse and remove the heat generated by electronic equipment, thus improving the stability and reliability of the equipment. Due to its reliability and performance advantages, LCC Package Substrates have been widely used in various application scenarios, including consumer electronics, automotive electronics, aerospace and other fields.
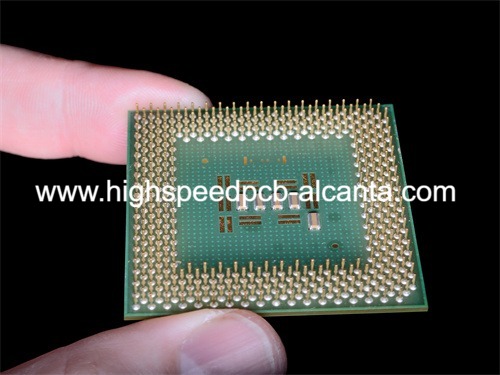
LCC Package Substrate Manufacturer
In short, LCC Package Substrates are not only an important part of PCB engineering, but also an indispensable key technology in the field of electronic packaging. They are designed and manufactured to high standards and stringent requirements to ensure optimal performance and reliability of electronic equipment. As technology continues to advance and market demand continues to grow, LCC Package Substrates will continue to play an important role in promoting the continued development and innovation of the electronics industry.
What types of LCC Package Substrates are there?
LCC Package Substrates, low-cost ceramic packaging substrates, are a special substrate type widely used in electronic packaging. In electronic engineering, there are several different types of LCC Package Substrates, each with its own unique characteristics and applicable scenarios.
First, let’s take a look at the main types of LCC Package Substrates:
Organic substrates are made of organic resin as the base material, usually using glass fiber reinforced resin (FR-4) as the main material. This type of LCC Package Substrates is lightweight, lower cost, and has good electrical performance. Due to its good processability and moderate thermal properties, LCC Organic Substrates are suitable for many consumer electronics and general application scenarios.
Ceramic substrates are made of ceramic materials with excellent thermal conductivity and mechanical strength. This type of LCC Package Substrates is typically used in applications requiring high performance and stability, such as high-frequency circuits, microwave modules, and power devices. Due to their high temperature resistance and good dimensional stability, LCC Ceramic Substrates perform well in a variety of harsh environments.
Metal substrates use metal materials (such as aluminum or copper) as the base material and have excellent heat dissipation properties. This type of LCC Package Substrates is particularly suitable for power electronics and LED lighting applications that require efficient heat dissipation. Due to its high thermal conductivity and good mechanical stability, LCC Metal Core Substrates can effectively reduce the operating temperature of electronic devices and improve their performance and reliability.
Flexible substrates use flexible materials (such as polyester film or polyimide) as the base material, which have excellent flexibility and bending properties. This type of LCC Package Substrates is suitable for compact and high-density electronic devices such as mobile devices, wearable devices, and flexible electronics. The main advantage of flexible substrates is their flexibility, allowing them to adapt to a variety of non-traditional shapes and curved designs.
In general, different types of LCC Package Substrates have their own characteristics and are suitable for different application scenarios. Understanding the differences and advantages and disadvantages between these types can help engineers and designers choose the most appropriate substrate to meet their project needs and performance requirements.
What are the advantages of LCC Package Substrates?
LCC Package Substrates (low-cost ceramic packaging substrate), as a special packaging substrate, have many advantages in electronic engineering. These advantages are not only reflected in performance, but also in terms of reliability. The following is a detailed introduction to the advantages of LCC Package Substrates:
LCC Package Substrates are known for their cost-effectiveness. LCC Package Substrates are less expensive to manufacture than traditional packaging substrates, making them ideal for mass production. This cost-effectiveness makes LCC Package Substrates a viable option for achieving high-performance packaging on a tight budget.
Despite their lower cost, LCC Package Substrates do not compromise on performance. This substrate design optimizes the transmission performance of the circuit and improves signal transmission rate and reliability. They can achieve higher operating frequencies and lower signal delays, thereby meeting today’s high-speed communication and data processing requirements.
Since electronic devices generate large amounts of heat when operating, good thermal management is crucial. LCC Package Substrates have excellent thermal conductivity properties and can effectively transfer and dissipate heat to keep the device within a safe operating temperature range. This helps improve the stability and reliability of the system and extends the service life of the equipment.
LCC Package Substrates offer greater design flexibility than traditional package substrates. They can easily implement multi-layer designs, allowing more functions and components to be integrated on a single substrate. This flexibility allows engineers to better optimize circuit layout and improve the performance and functionality of electronic devices.
LCC Package Substrates are highly productive due to their carefully optimized manufacturing process. This means volume production can be achieved faster, product time to market can be shortened, and rapid changes in market demand can be met.
In many applications, lightweight design is a crucial consideration. LCC Package Substrates are generally lighter than traditional package substrates, which helps reduce the weight of the entire electronic device and improves its portability and carrying comfort.
In summary, LCC Package Substrates have significant advantages in cost, performance, reliability and design flexibility, making them one of the most popular packaging substrate choices in today’s electronic engineering field.
Why choose LCC Package Substrates?
In today’s electronic packaging field, LCC Package Substrates (low-cost ceramic substrates) are attracting increasing attention and have become the first choice of many engineers and designers. Why choose LCC Package Substrates over traditional PCB? What are their advantages?
One of the great advantages of LCC Package Substrates is their significant cost effectiveness. While traditional PCB manufacturing involves complex processes and high costs, LCC Package Substrates use simpler manufacturing processes and materials, making them more cost-effective. For projects that require large-scale production and are cost-sensitive, LCC Package Substrates offer a competitive solution.
LCC Package Substrates excel in thermal management. Its ceramic substrate has good thermal conductivity and can effectively disperse and remove heat, helping to maintain a stable operating temperature of electronic components. This makes LCC Package Substrates particularly suitable for high-power electronic devices and applications requiring a high degree of thermal stability, such as automotive electronics and industrial control systems.
LCC Package Substrates offer higher performance and reliability than traditional PCBs. Its ceramic substrate has excellent mechanical strength and durability and is resistant to the adverse effects of vibration, shock and temperature changes. In addition, LCC Package Substrates’ materials and manufacturing processes are carefully designed to ensure stable electrical performance and signal transmission quality.
As electronic products become smaller, lighter, and more compact, the space and density requirements for PCB packaging are also increasing. LCC Package Substrates uses advanced packaging technology and materials to achieve higher device density and more compact layout, thereby meeting the needs of modern electronic products for high integration and miniaturization.
In summary, LCC Package Substrates are favored and widely selected mainly due to their significant cost-effectiveness, superior thermal management performance, high performance and reliability, and suitability for high-density packaging. In projects that need to meet demanding performance requirements and tight timelines, LCC Package Substrates provide a reliable solution that helps drive innovation and development in electronics.
What is the manufacturing process for LCC Package Substrates?
The manufacturing process of LCC Package Substrates is a precise and complex process that includes multiple critical steps to ensure excellent performance and reliability of the final product.
First, the first step in manufacturing LCC Package Substrates is to prepare the substrate. This includes selecting a suitable substrate material, usually a ceramic or organic material, and surface preparation to ensure subsequent coating and adhesion can proceed smoothly.
Next, comes the process of layer stacking on the substrate. In this step, conductive layers, insulating layers and other necessary layers are stacked layer by layer on the substrate through precise coating and stacking techniques. The combination and sequence of these layers is critical to the performance of the final product.
Then, patterning and board design take place. By using advanced photolithography and chemical processing methods, the designed circuit pattern is transferred to the substrate. This step requires highly precise equipment and process control to ensure the accuracy and stability of the circuit.
Next comes the metallization of the circuit board. Circuit connections and solder joints are made by plating a metal layer, usually copper or other conductive material, on the surface of a circuit board. This step not only enhances the circuit board’s electrical conductivity, but also improves its resistance to corrosion and wear.
This is followed by final assembly and testing. In this step, the board is connected to other components and undergoes rigorous performance testing and quality control. This includes a comprehensive inspection of circuit connectivity, voltage resistance, temperature stability, etc. to ensure that the product meets design requirements.
Finally, it’s packed and shipped. After final assembly and testing, the LCC Package Substrates are packaged, labeled and packaged according to customer requirements. Products can then be shipped to meet the needs of various industries.
Overall, the manufacturing process of LCC Package Substrates involves multiple critical steps, each of which requires a high degree of process control and precision equipment to ensure that the final product has excellent performance and reliability.
What are the applications of LCC Package Substrates?
LCC Package Substrates, as a cost-effective and superior-performance electronic packaging solution, plays a wide range of applications in various industries. Below we will explore its important applications in different fields:
In the field of automotive electronics, LCC Package Substrates are widely used in automotive electronic systems. These systems cover in-vehicle infotainment, in-vehicle navigation, body control and other functions, and require stable and reliable electronic component support. The excellent performance and reliability of LCC Package Substrates make it the first choice in the field of automotive electronics, ensuring the stable operation of vehicle electronic systems.
In consumer electronics, such as smartphones, tablets, smart home devices, etc., LCC Package Substrates also play an important role. These products require extremely compact designs and high performance from electronic components, and LCC Package Substrates’ small form factor and excellent thermal management capabilities make them ideal for achieving these requirements.
In the field of communications, LCC Package Substrates are widely used in network equipment, base stations, communication satellites and other equipment. These devices have strict requirements for high-frequency, high-speed data transmission, and the excellent electrical performance and high-frequency characteristics provided by LCC Package Substrates make it one of the core components of communication equipment.
The field of medical devices has particularly strict requirements on the stability and reliability of electronic products, so the application of LCC Package Substrates in medical devices is also very important. For example, medical monitoring equipment, diagnostic equipment, medical imaging equipment, etc. all require stable and reliable electronic component support, and the high reliability and excellent performance provided by LCC Package Substrates ensure the stable operation of these equipment.
In the field of industrial control, LCC Package Substrates are widely used in various industrial automation equipment, robotic systems, sensors and other equipment. These devices have strict requirements for harsh environments such as high temperature, high humidity, and high vibration. The excellent thermal management capabilities and durability provided by LCC Package Substrates make it the first choice in the industrial control field.
To sum up, LCC Package Substrates plays an important role in various fields such as automotive electronics, consumer electronics, communication equipment, medical equipment and industrial control, providing stable and reliable electronic packaging solutions for various application scenarios.
Where can I find LCC Package Substrates?
When looking for reliable LCC Package Substrates suppliers and manufacturers, critical information can be obtained through a variety of sources. As a supplier, our company is committed to providing high-quality LCC Package Substrates to our customers and ensuring they can easily find us. Here are some ways to obtain supplier information:
Searching the Internet for LCC Package Substrates suppliers and manufacturers via a search engine is a quick and effective way. Various company websites and online directories can be found using relevant keywords such as “LCC Package Substrates suppliers”, “LCC Package Substrates manufacturers”.
Attending trade shows and conferences within the industry is another way to learn about LCC Package Substrates suppliers. These events usually bring together professionals and vendors from various fields, providing excellent opportunities for networking and networking.
Join professional forums and social media groups related to PCB engineering to exchange experiences with peers and get recommendations and advice about suppliers. These platforms are often important channels for gaining insider information and connections within the industry.
Join relevant industry associations and organizations, such as the Institute of Electrical Engineers (IEEE) and the Semiconductor Industry Association, to obtain the latest information related to LCC Package Substrates and establish connections with suppliers.
As a supplier, our official website is the primary source of important information about our products and services. Our website provides a detailed description of LCC Package Substrates, as well as contact and customer support information.
Through the above channels, customers can easily find key information about our company as a supplier of LCC Package Substrates. We are committed to providing customers with quality products and services and establishing long-term and solid cooperative relationships with them.
What is the quote for LCC Package Substrates?
When selecting LCC Package Substrates, it is critical to understand their cost estimates and the steps to obtain a quote. This information is detailed below.
LCC Package Substrates cost estimates involve multiple factors, some of the key factors include:
Material Type and Quality: Different types of LCC Package Substrates have different material costs. The choice of organic substrates, ceramic substrates, metal core substrates, etc. will affect manufacturing costs.
Manufacturing Process: The complexity and requirements of the manufacturing process have a direct impact on costs. Highly customized processes may increase costs, while standardized processes are more cost-effective.
Quantity and size: The quantity and size of the order are also key factors that affect costs. Generally speaking, mass production reduces the cost of a single unit.
Custom Requirements: If the project has custom requirements, such as special layer stack-ups, surface treatments, or dimensions, these may increase the cost of LCC Package Substrates.
Steps to Get a Quote for LCC Package Substrates
Clarify requirements: Before asking suppliers for quotations, make sure you clearly understand the technical and mass production requirements of the project. Providing detailed technical specifications and quantity requirements will help obtain a more accurate quote.
Choose a supplier: It is crucial to choose a professional LCC Package Substrates supplier. Make sure they have a good reputation, advanced production equipment and quality assurance system.
Provide technical specifications: Provide technical specifications of LCC Package Substrates to potential suppliers, including dimensions, layer stackup, material requirements, etc. This will help suppliers more accurately assess production costs.
Request a Quote: Request a quote from selected suppliers. The quotation should include key information such as unit price, delivery time, payment terms, etc. It’s important to know their quote structure and additional fees in advance.
Compare Quotations: After receiving quotes from multiple suppliers, compare them carefully. Not only should you focus on price, but also consider the supplier’s delivery capabilities, quality assurance and after-sales service.
Negotiation and confirmation: Negotiate with suppliers to obtain more favorable prices and services based on comparison results. Once all details are confirmed, the supplier that best suits the project needs can be selected.
Understanding LCC Package Substrates’ cost estimates and the steps to obtain a quote is a critical step in ensuring the success of your project. Through reasonable cost estimation and selecting the right suppliers, you will be able to obtain high-quality LCC Package Substrates that meet the technical and commercial requirements of your project.
What are the frequently asked questions (FAQs) about LCC Package Substrates?
What are LCC Package Substrates and how do they differ from traditional PCBs?
LCC Package Substrates are specialized substrates used in electronic packaging. Unlike traditional PCBs, LCC Package Substrates offer enhanced thermal management, improved electrical performance, and cost-effectiveness, making them ideal for various applications in PCB engineering.
What types of LCC Package Substrates are available?
There are several types of LCC Package Substrates, including LCC Organic Substrates, LCC Ceramic Substrates, LCC Metal Core Substrates, and LCC Flex Substrates. Each type has unique properties suited for different electronic packaging needs.
What are the advantages of using LCC Package Substrates?
LCC Package Substrates offer numerous advantages, such as superior thermal management, enhanced electrical performance, cost-effectiveness, compact design, and high reliability. These advantages make them a preferred choice for electronic packaging applications.
How are LCC Package Substrates manufactured?
The manufacturing process of LCC Package Substrates involves substrate preparation, layer buildup using advanced techniques, and surface finishing to ensure optimal performance and reliability. This process requires precision and expertise to meet quality standards.
What are the main applications of LCC Package Substrates?
LCC Package Substrates find extensive use across various industries, including consumer electronics, automotive, aerospace, medical devices, and telecommunications. Their versatility and cost-effectiveness make them suitable for a wide range of applications.