Low Dk Epoxy Resin Materials IC PACKAGING SUBSTRATES
IC PACKAGING SUBSTRATES Manufacturer.An IC packaging substrates manufacturer is a specialized entity focused on crafting the fundamental platforms that host integrated circuits (ICs). These substrates serve as the physical foundation for ICs, providing electrical connections and structural support crucial for their functionality. Utilizing advanced materials and precise engineering, these manufacturers produce substrates tailored to diverse applications, from consumer electronics to industrial systems. With a blend of cutting-edge technology and meticulous craftsmanship, they ensure the reliability, performance, and scalability of IC packaging solutions, contributing indispensably to the intricate ecosystem of modern electronics.
IC packaging substrate plays an indispensable role in the modern electronics industry and is a key component to ensure the smooth operation of integrated circuits (ICs). In this era of rapid technological development, the demand for IC equipment is growing day by day, and the importance of IC packaging substrates as the basis for connecting and supporting ICs has become increasingly prominent.
IC packaging substrates not only provide a stable physical platform to connect tiny chips to larger circuit systems, but also ensure efficient performance of IC devices by providing effective thermal management and electrical connections. Its design and quality directly affect the stability, reliability and performance of electronic equipment.
While pursuing higher performance, low dielectric constant epoxy resin materials have become an important innovation in PCBs design. The wide application of low Dk materials in PCBs is expected to reduce signal attenuation and delay in signal transmission, thereby improving the efficiency of the entire system. The introduction of this material not only improves the speed and quality of signal transmission, but also helps reduce the power consumption of electronic devices.
In summary, IC packaging substrates and low-Dk epoxy resin materials complement each other in the electronics industry and jointly promote the advancement of technology. In this introduction, we will delve into the key role of IC packaging substrates and the innovative applications of low-Dk epoxy resin materials in PCBs, revealing their irreplaceable position in promoting innovation in electronic technology.
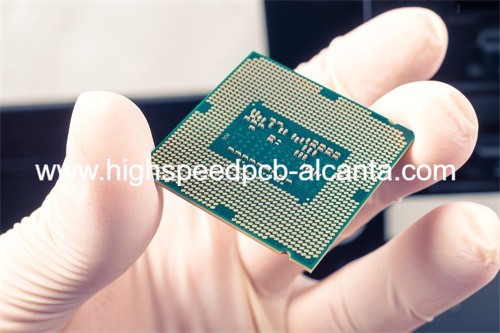
IC PACKAGING SUBSTRATES Manufacturer
What is the definition of IC Packaging Substrate?
IC Packaging Substrate is a critical material in modern electronics, specifically designed to support and connect integrated circuit (IC) components. As the key intermediary between ICs and printed circuit boards (PCBs), IC Packaging Substrate plays an integral role in electronic devices. Its definition covers several key aspects, from its basic functionality to its close relationship with the PCB.
The IC Packaging Substrate is specifically defined as a specialized material designed to provide support and connectivity for integrated circuit components. It transcends being a mere component within electronic devices, emerging as a fundamental element crucial for the normal operation of ICs. Its distinctive structure and characteristics endow it with the capacity to fulfill critical functions within electronic systems, ensuring the stable operation of equipment.
Situated between integrated circuits and PCBs, the IC Packaging Substrate assumes a pivotal role. Serving as an interface, it not only facilitates the seamless transmission of electrical signals but also furnishes essential mechanical support. Through the precision-engineered attributes of this material, integrated circuits within electronic devices can effectively communicate with their surrounding environment and other components, harmonizing the entire system for optimal functionality.
The role of this key material goes beyond signal transmission, it also plays a key role at the mechanical level. IC Packaging Substrate provides the necessary mechanical support to protect IC components from the external environment and stress.
Overall, IC Packaging Substrate is a key component in electronic equipment, providing basic support and signal transmission channels for integrated circuits. Its well-designed structure and versatility make it an indispensable element in modern electronics. By deeply understanding the definition and functions of IC Packaging Substrate, we can better appreciate and understand its key role in promoting the development of electronic technology.
What functions does IC Packaging Substrate have?
IC Packaging Substrate is a key component in modern integrated circuit packaging. Its main functions revolve around electrical connection, mechanical support and thermal management, providing a solid foundation for the stable operation of integrated circuits.
First, IC Packaging Substrate enables efficient electrical signal transmission between integrated circuits and printed circuit boards (PCBs) through its excellent electrical connection capabilities. The semiconductor packaging substrate’s inherent capability facilitates seamless communication among internal components, fostering coordinated functioning of the entire system. Distinguished by design features like multi-level and high-density interconnections, the IC packaging substrate expedites the transmission of electrical signals within, significantly enhancing the data transmission efficiency of the overall system.
Secondly, IC Packaging Substrate provides strong mechanical support and provides a solid physical foundation for precision IC components. The importance of this support is to protect IC components from external stresses and ensure their stable operation under various environmental conditions. By using different materials and layers of design, IC Packaging Substrate is able to accommodate integrated circuits of various sizes and shapes, providing them with a secure home.
Finally, IC Packaging Substrate plays a key role in thermal management. By effectively dissipating heat, IC Packaging Substrate helps maintain the optimal operating temperature of integrated circuits. As modern integrated circuits continue to develop, their power consumption and heat are also on the rise. Therefore, the design of IC Packaging Substrate needs to consider how to effectively transfer the generated heat to the external environment to avoid performance problems caused by overheating. Using advanced heat dissipation materials and structural design, IC Packaging Substrate can effectively manage the temperature of the integrated circuit to ensure its stable operation under various load conditions.
What types of IC Packaging Substrate are there?
IC Packaging Substrate is a key technology that provides important support for the packaging of integrated circuits. This area covers many types of Substrate, each carefully designed to meet different performance and application requirements. Let’s take a closer look at the main types of IC Packaging Substrate:
Package Substrate Type
Single-layer Substrate: Single-layer Substrate is a type of encapsulation with a simple basic structure and suitable for specific scenarios. It is typically used in applications requiring lower complexity and cost, providing a solid foundation for the IC.
Multi-layer Substrate: Multi-layer Substrate adopts a layered design and provides more complex connections and support by superimposing multiple layers. This type is suitable for applications with higher requirements on electrical connection performance and device density.
High Density Interconnect (HDI) Substrate: HDI Substrate is an advanced technology that enables smaller, thinner packages by using fine lines and high-density component layout. It is widely used in modern electronic equipment, providing an ideal solution for high performance and compact design.
Chip packaging technology
On the other hand, the type of IC Packaging Substrate is also closely related to chip packaging technology. Different technologies affect the design and performance of Substrate. The following are some common chip packaging technology classifications:
Flip chip: Flip chip technology flips the chip and installs it on the Substrate, and achieves electrical connection through direct welding. This technology is typically used in high-performance applications, providing shorter signal transmission paths and better thermal performance.
Wire bonding represents a conventional chip packaging technique wherein metal wires are employed to establish connections between the chip and the substrate. Renowned for its reliability and stability, this method finds widespread adoption across diverse applications and industries.
A comprehensive comprehension of the various IC packaging substrates and their interplay with chip packaging technology is crucial for gaining insights into developmental trends within this pivotal domain. The ongoing evolution of these technologies not only propels advancements in integrated circuits but also lays a sturdy groundwork for the innovation of electronic products.
What is the difference between Package Substrates and PCBs?
While IC Packaging Substrates and printed circuit boards (PCBs) share some similarities, crucial distinctions exist, primarily evident in the following aspects:
Firstly, regarding the realm of PWBs and PCBs, PCBs play a broader role, encompassing the entire circuit board. PCBs stand as the core of electronic equipment, facilitating the connection and transmission of electronic components and supporting all facets of the entire system. In contrast, IC Packaging Substrates are more narrowly focused on the integration and interconnection of integrated circuits. Specifically designed to offer support and protection to integrated circuits, they furnish the necessary electrical connections and mechanical support for these components.
Secondly, the difference between the motherboard and Substrate is that the motherboard contains multiple ICs and other components. It is the skeleton of the entire electronic device and is responsible for coordinating the communication and collaborative work between the various parts. Substrates, by contrast, focuses on individual ICs or smaller components. They provide the support these tiny but vital electronic components need to ensure they function properly while maintaining a high level of integration throughout the system.
Finally, it is worth noting that PCB-like Substrate (SLP) and HDI Substrate represent the continued evolution of Substrate design. These emerging technologies demonstrate the need for higher performance and tighter integration while driving Substrate innovation. For example, SLP (PCB-like Substrate) offers the possibility of miniaturization and lightweighting of modern electronic devices with its higher density and smaller size. HDI Substrate further improves the performance and reliability of the circuit board by using high-density interconnection technology.
Overall, although IC Packaging Substrates and PCBs play an integral role in electronic devices, there are obvious differences in their focus and application areas. Understanding these key differences is critical for engineers and those working in the electronics industry because they directly impact decisions made during the design and manufacturing process. This also reflects the evolving trend in the electronics field to adapt to the needs of increasingly complex and compact integrated circuits.
What are the main structures and production technologies of IC Packaging Substrates?
IC Packaging Substrates are an important part of today’s advanced electronic technology. Their structure and manufacturing technology play a key role in ensuring the stable operation and efficient performance of integrated circuits (ICs).
Structure of IC Packaging Substrates
The structure of IC Packaging Substrates covers multiple levels, and material selection and design factors are crucial. First, they often contain multiple layers that serve different functions within the overall structure. High-Density Interconnect (HDI) Substrates are one type that have multiple fine layers that allow for more compact circuit designs.
In a hierarchy, the choice of material is crucial. Common materials include substrates, conductor materials, and insulating layers. These materials need to have superior electrical properties, mechanical strength, and high temperature resistance to ensure that the IC can operate reliably in various environments.
Design considerations are also an integral part of the IC Packaging Substrates structure. Design needs to consider factors such as circuit layout, signal transmission paths, heat distribution, etc. to maximize overall performance and ensure the stability of the electronic system.
Manufacturing Technology of IC Packaging Substrates
IC Packaging Substrates’ manufacturing technology uses a variety of advanced methods, including improved HDI manufacturing and innovative semi-additive methods.
Improved HDI manufacturing: HDI manufacturing is a high-density interconnect technology that enables smaller, lighter and higher-performance substrates through the use of microscopic lines and vias. This manufacturing technique allows for more electrical connections, improving signal transmission efficiency while reducing the overall size of the circuit board.
Semi-additive method: The innovative semi-additive method uses a method of adding semiconductor materials, which is different from the traditional complete addition method. This method reduces manufacturing costs while improving production efficiency, providing a feasible solution for the mass production of IC Packaging Substrates.
Sophisticated manufacturing technologies play a pivotal role in empowering IC Packaging Substrates to meet the escalating demands for high performance and reliability, particularly in the context of ever-more intricate and compact electronic devices. A comprehensive grasp of the structure and manufacturing intricacies of IC Packaging Substrates is crucial for a nuanced understanding of its significance in the contemporary electronics industry. This knowledge not only underscores its current importance but also establishes a robust groundwork for future technological innovations in the field.
Frequently Asked Questions about IC Packaging Substrates
IC Packaging Substrates play a key role in modern electronics, but with them come a series of questions about their structure and manufacturing. Here are detailed answers to some frequently asked questions:
What is the structure of IC Packaging Substrates?
The structure of IC Packaging Substrates mainly consists of multi-layer designs, constructed using different materials. Among them, the high-density interconnect (HDI) Substrate adopts an advanced hierarchical layout to achieve more compact integration.
What is the main difference between Package Substrate and Printed Circuit Board (PCB)?
IC Packaging Substrates focuses on the packaging and connection of integrated circuits, while PCB covers a wider range of circuit boards. PCBs usually include multiple IC Packaging Substrates to build a complete electronic system.
How do emerging technologies impact the manufacturing of IC Packaging Substrates?
In recent years, some emerging technologies have emerged, such as Substrate-Like PCBs (SLP) and improved HDI manufacturing technology, which continue to promote the evolution of IC Packaging Substrates, improving their performance and density.
How is thermal management implemented in IC Packaging Substrates?
IC Packaging Substrates uses advanced heat dissipation design to effectively manage the heat generated by integrated circuits through thermal conduction materials and structural optimization to ensure that the equipment operates at ideal temperatures.
What innovations are there in packaging substrate production technology?
In addition to traditional manufacturing methods, modern IC Packaging Substrates adopt innovative processes such as improved HDI manufacturing technology and semi-additive methods to improve production efficiency and manufacturing accuracy.
What is the role of IC Packaging Substrates in electronic systems?
As the key media between IC and PCB, IC Packaging Substrates realizes the efficient transmission of electrical signals and provides mechanical support for IC components. It is an indispensable part to ensure the reliable operation of electronic systems.
The answers to these questions reveal the importance of IC Packaging Substrates in today’s highly complex electronic systems and how evolving technologies are driving their critical role in integrated circuit packaging. By gaining a deeper understanding of these aspects, we can better respond to increasingly complex electronic needs and promote continuous technological advancement.