What is high-frequency PCB?
High Frequency PCB Manufacturer.A high frequency PCB manufacturer specializes in crafting printed circuit boards engineered to transmit signals at elevated frequencies. These intricate boards are meticulously designed and fabricated using advanced materials and techniques to ensure minimal signal loss and maximum efficiency. With a focus on precision and performance, these manufacturers cater to industries such as telecommunications, aerospace, and medical devices, where reliable signal transmission is paramount. Their expertise lies in producing boards capable of handling frequencies ranging from hundreds of megahertz to several gigahertz, meeting the demands of cutting-edge technologies and facilitating seamless communication and data transfer.
Its superiority in handling weak signals and facilitating high-speed data transmission sets it apart from traditional circuit boards. To comprehend its nuances, we must explore different types, such as PTFE boards, radio frequency circuit boards (RF PCBs), microstrip lines, and coaxial lines, each tailored for specific characteristics and application scenarios. These differences empower high-frequency PCBs to adapt to diverse frequency requirements.
RF PCBs find common use in applications requiring wireless communications and radar systems, while microstrip and coaxial lines are integral for high-frequency transmission. PTFE boards, owing to their low loss and superior electrical performance, secure a position in high-frequency PCBs. Understanding the distinct characteristics of these boards aids informed design choices aligned with specific application needs.
Precision in signal transmission and reception, distinguishing them from traditional circuit boards, positions high-frequency PCBs as vital in wireless communications, radar systems, and other fields.
The manufacturing process of high-frequency PCBs demands meticulous attention to the steps of Motherboard and Substrate. This involves the selection of specialized materials, a sophisticated lamination process, and precise control of sheet properties. Only through a deep understanding of these steps can optimal performance be ensured.
Widely applied in communication equipment, radar systems, medical equipment, and satellite communications, high-frequency PCBs enhance equipment stability and reliability in high-frequency environments. Recognizing these application areas provides insight into the diverse roles of high-frequency PCBs across industries.
When acquiring high-frequency PCBs, readers can source them from professional PCB manufacturers or suppliers. The selection of a supplier should consider experience, manufacturing capabilities, and proficiency in high-frequency materials. Obtaining a quotation requires consideration of factors like board type, number of layers, special processes, etc. Open communication with suppliers ensures a reasonable quotation aligned with project needs.
What are the various types of high-frequency PCBs?
In the expansive realm of high-frequency PCBs, engineers have a plethora of options tailored to diverse application scenarios. The following delineates key types of high-frequency PCBs, highlighting their distinctive features and exemplary performance across various application domains:
Radio Frequency Circuit Board (RF PCB)
Characteristics:Specifically designed for RF signal transmission, RF PCBs boast low propagation loss and uphold high signal integrity. These boards often incorporate special materials and designs tailored for high-frequency environments.
Applications:Ubiquitous in communication equipment, satellite communications, and radar systems, RF PCBs effectively process complex radio frequency signals to ensure signal quality and stability.
Microstrip Line
Characteristics:A prevalent high-frequency transmission line structure, the microstrip line involves metal conductors on the surface of a dielectric substrate. This configuration delivers excellent high-frequency performance and low propagation loss.
Applications:Widely utilized in communication systems, antenna design, and microwave radio frequency modules, microstrip lines are adept at facilitating high-speed data transmission.
This diverse array of high-frequency PCB types caters to the unique demands of various applications, showcasing remarkable performance in their respective fields.
Application scenarios
In fields such as wireless communications, radar systems, medical equipment, and satellite communications, these high-frequency PCB types each exert unique advantages. The low-loss properties of PTFE boards make them an ideal choice in microwave communications, while RF PCBs ensure high-quality signal transmission in radio frequency systems. Microstrip lines and coaxial lines exhibit excellent performance in communication connections and RF modules, providing reliable solutions for various applications in high-frequency environments.
In conclusion, the array of high-frequency PCB types offers engineers a rich selection to address the exacting demands for signal quality, transmission performance, and stability across various application scenarios. With a range of high-frequency PCB options available, engineers have the flexibility to choose based on specific requirements, ensuring that their designs yield optimal results in diverse high-frequency environments.
What are the advantages of high-frequency PCB compared to traditional circuit boards?
In the rapidly advancing electronic landscape, high-frequency PCB technology distinguishes itself from traditional circuit boards by delivering exceptional signal integrity and electrical performance. Its distinct advantages make high-frequency PCBs more reliable, particularly in the domain of high-frequency communications.
Firstly, high-frequency PCBs stand out in signal integrity. Tailored for environments with elevated frequencies, their design optimizes electrical performance, mitigating signal distortion and ensuring more accurate signal transmission. The shorter wavelength of signals in high-frequency environments allows these PCBs to effectively minimize electromagnetic radiation and mutual inductance effects, thereby enhancing overall signal integrity.
Secondly, high-frequency PCBs demonstrate low-loss characteristics, addressing a critical concern in high-frequency signal transmission. The materials and processes employed in high-frequency PCBs effectively curtail signal energy loss, enabling them to maintain signal clarity, minimize signal attenuation, and ensure reliable communication over extended distances during high-frequency signal transmission.
In high-frequency communications, time is critical to the accuracy of the signal. Traditional circuit boards may cause unstable communication due to time delays in signal propagation, while high-frequency PCBs significantly reduce signal propagation delays through sophisticated electrical design and special board selection, ensuring real-time performance of high-speed communications.
High-frequency PCBs boast a notable strength in their ability to counter interference. In environments characterized by high frequencies, circuit boards are particularly vulnerable to external disruptions, such as electromagnetic radiation and radio frequency interference. The effectiveness of high-frequency PCB lies in its adeptness at mitigating the impact of external interference. This is achieved through the strategic incorporation of efficient shielding layers and the use of anti-interference materials, thereby enhancing the stability and reliability of the circuit.
When considering its outstanding attributes in signal integrity, low loss, low propagation delay, and anti-interference capabilities, it is evident that high-frequency PCB stands as the preferred choice in the realm of high-frequency communications. As communication technology advances, the role of high-frequency PCBs will persist as a linchpin, facilitating more reliable and efficient communication among electronic devices operating in high-frequency environments.
Why choose high frequency PCB instead of other circuit boards?
In the dynamic landscape of today’s electronics industry, the utilization of high-frequency PCB is increasingly becoming an integral component across various fields. Its exceptional capability to process weak signals and facilitate high-speed data transmission presents distinct advantages compared to traditional PCBs, resulting in its growing popularity in numerous scenarios.
First, high-frequency PCBs are excellent at handling weak signals. Weak signals are often critical parts of electronic equipment that require high sensitivity and precise control, such as the receiving end in communication systems. Because high-frequency PCB uses special materials and designs, it has lower signal loss and superior signal transmission characteristics, and can receive and process weak signals more accurately to ensure accurate transmission of information.
Furthermore, high-frequency PCBs exhibit superior performance in high-speed data transmission, a critical attribute given the escalating demand for digital communication and data processing.
The advantages of high-frequency PCBs manifest in several key aspects:
Low Signal Loss: By employing materials with low dielectric constants and low-loss properties, high-frequency PCBs minimize energy loss during signal transmission, ensuring a stable and efficient signal transmission process.
Precision Design:High-frequency PCBs excel in precision wiring and inter-layer connections, mitigating the impact of electromagnetic interference and crosstalk, thereby safeguarding the integrity of high-speed signals.
Better Impedance Matching: Critical in high-frequency applications, high-frequency PCBs are meticulously designed to match the impedance of transmission lines, thereby reducing signal reflection and ripples, and enhancing the overall quality of signal transmission.
Low Propagation Delay:The use of high-quality materials and specialized designs allows high-frequency PCB signals to propagate more swiftly, minimizing propagation delays and adapting seamlessly to scenarios that demand high real-time performance.
In scenarios demanding uncompromising signal integrity and top-tier performance, such as wireless communications, radio frequency identification (RFID), and radar systems, high-frequency PCBs have risen as the preferred solution. Their extensive integration not only drives the advancement of wireless communication technology but also lays a sturdy groundwork for innovation in high-tech domains. As a result, the industry has collectively embraced the consensus of prioritizing high-frequency PCBs over conventional circuit boards to guarantee system reliability, stability, and optimal performance.
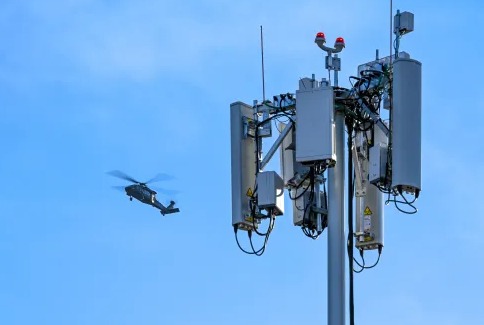
High Frequency PCB Manufacturer
What is the manufacturing process of high-frequency PCB?
This involves drawing circuit graphics, layering them one upon another, and designing the components and hierarchies required for high-frequency characteristics. During this process, engineers need to pay special attention to signal integrity, matching impedance, and signal lead layout to minimize signal loss and crosstalk.
Next, preparing Substrate is a crucial step. Substrate is the material responsible for connecting all levels in high-frequency PCB, so its preparation requirements are extremely high. In this process, precision lamination technology is usually used to ensure that the geometry and size of the signal transmission channels between layers are controlled within a very small error range. In addition, in order to prevent signals from being interfered during transmission, a special shielding layer is usually used in the Substrate layer.
What’s special is that the manufacturing process of high-frequency PCB requires highly precise process control. Any small error may have an irreversible impact on the transmission performance of high-frequency signals. In the manufacturing process of Motherboard and Substrate, manufacturers usually use advanced CNC processing equipment to ensure that every step can achieve sub-micron precision.
Moreover, the production of high-frequency PCBs demands rigorous quality control and testing procedures. Leveraging cutting-edge testing equipment, manufacturers conduct thorough assessments of finished products to verify compliance with design specifications and performance standards.
In essence, the manufacturing process for high-frequency PCBs encompasses not only the preparatory steps involved in conventional PCB production but also imposes heightened criteria for material selection, design intricacies, and processing precision. This intricate process is essential to guarantee the optimal performance of high-frequency PCBs in environments with elevated frequencies, establishing a dependable foundation for applications like wireless communications and radar systems.
In what fields are high-frequency PCBs widely used?
In the realm of communication equipment, the indispensability of high-frequency PCBs lies in their exceptional performance, serving as a linchpin for wireless communications and high-speed data transmission. With attributes like low propagation delay, minimal loss, and superior signal integrity, high-frequency PCBs are instrumental in pivotal applications such as 5G communication systems and base station antennas. The meticulous design and manufacturing of these PCBs ensure the heightened stability of communication signals, delivering faster and more reliable communication services to users.
The extensive use of high-frequency PCB technology extends to radar systems, where stringent demands for processing and transmitting high-frequency signals prevail. Their superior performance makes high-frequency PCBs well-suited for radio frequency (RF) and microwave applications, contributing to the excellent performance of radar systems in detection, target tracking, and beyond.
In the field of medical device manufacturing, technological advancements in high-frequency PCBs have proven beneficial. These PCBs find application in medical imaging equipment, vital signs monitoring instruments, and other medical devices, supporting precise signal processing and data transmission to uphold the accuracy of medical data. Their lightweight and compact characteristics facilitate the design of smaller, more portable medical equipment, aligning with the modern medical field’s requirements for both portability and high performance.
Satellite communications, a critical domain, also relies heavily on high-frequency PCBs. The substantial demand for high-frequency signal transmission in satellite communication systems is aptly met by the low signal loss and excellent electrical performance of these PCBs. They play a pivotal role in satellite transmitters, receivers, and entire communication links, ensuring efficient and reliable signal transmission.
In summary, the widespread adoption of high-frequency PCBs across diverse sectors such as communication equipment, radar systems, medical devices, and satellite communications underscores their unique advantages in processing high-frequency signals and addressing complex engineering needs. The evolving technologies in this domain are poised to catalyze further innovation, injecting fresh momentum into the future development of electronic engineering.
How to obtain high frequency PCB?
In the swiftly advancing realm of electronics, securing high-frequency PCBs and selecting the right supplier is paramount. Exploring various avenues and considering key factors can guide readers in this decision-making process.
Option One: Engaging with Professional PCB Manufacturers
Relying on professional PCB manufacturers stands out as one of the most dependable approaches to acquiring high-frequency PCBs. These companies typically boast substantial experience and employ advanced production equipment to deliver products that meet high-quality standards. Direct communication with manufacturers affords customers the opportunity to gain insights into production processes, quality assurance protocols, and service offerings. This direct engagement enhances understanding and confidence in the chosen supplier.
Path Two: Online Platforms and Markets
Online platforms and marketplaces offer a wide selection of high-frequency PCB suppliers. Some well-known electronic markets and B2B platforms have gathered many suppliers, providing convenient and fast product search and comparison functions. Through online platforms, customers can browse products, reviews and quotes from different suppliers to better make informed choices.
Path 3: Participate in industry exhibitions and activities
Engaging in industry shows and events offers an additional avenue for acquiring information on high-frequency PCBs. These gatherings typically assemble a multitude of PCB manufacturers and suppliers, affording customers a direct channel for communication. Attendees at these events have the chance to scrutinize products, stay abreast of the latest technological trends, and establish connections with potential suppliers, creating a dynamic environment for knowledge exchange and networking.
Key Considerations for Selecting a High-Frequency PCB Supplier
Experience and Reputation:Prioritize suppliers with a robust track record and a positive reputation. Opting for an experienced supplier ensures a reliable grasp of high-frequency PCB production, fostering confidence in their expertise.
Technical Proficiency:Assess the supplier’s technical capabilities, focusing on their utilization of advanced production technology and equipment. This scrutiny ensures their ability to meet the intricate manufacturing demands associated with high-frequency PCBs.
Customization Capabilities:For projects necessitating customized high-frequency PCBs, verify the supplier’s ability to accommodate specific design requirements. Ensure they possess the flexibility and expertise to tailor their products to meet unique project needs.
Why choose our company as a supplier?
The process involves several key steps to ensure a reasonable quote that aligns with project requirements:
Effective Communication:Establish clear and effective communication channels with suppliers from the outset. Clearly convey the project’s technical requirements, specifications, and mass production needs. A detailed project description aids suppliers in precisely understanding the desired high-frequency PCB characteristics.
Special Processes:Take note of any special processes involved, such as lamination techniques, impedance control, and the use of blind or buried vias. Including these details in the quote request helps avoid later complications and additional costs arising from process adjustments.
Supplier Selection:In addition to considering price, evaluate the supplier’s experience and expertise in the high-frequency PCB field. Seasoned suppliers are more likely to deliver high-quality products that meet specifications. Request case studies or customer testimonials related to similar projects to gauge their success in high-frequency PCB manufacturing.
Production Capabilities:Understand the supplier’s production capabilities. Inquire about production line equipment, quality control processes, and delivery times to ensure they can deliver high-quality products on schedule and in the required quantities.
Regular Communication:Maintain regular communication with the supplier throughout the process. Promptly address any unclear questions to assist suppliers in better comprehending project requirements, ensuring the accuracy and comprehensiveness of the final quotation.
In conclusion, obtaining a high-frequency PCB quote is a thorough and systematic process that demands effective communication, technical acumen, and attention to detail. By diligently following these steps, you can maximize the likelihood of securing a final high-frequency PCB quotation that not only meets performance expectations but also aligns with cost control objectives.
What are the common questions about high-frequency PCB that need to be answered?
What are the common design considerations for high-frequency PCBs?
Designers must consider trace geometry, layer stackup, grounding techniques, via placement, and thermal management to ensure optimal performance at high frequencies.
How does via placement affect high-frequency PCB performance?
Via placement can impact signal integrity. Properly spaced and designed vias can minimize signal distortion and impedance mismatches. Blind and buried vias may be used to reduce signal discontinuities.
How is signal integrity maintained in High Frequency PCBs?
Signal integrity is maintained through careful design practices, including controlled impedance routing, minimizing trace lengths, and using proper termination techniques. Proper grounding and shielding are also important.
What is the significance of controlled impedance in High Frequency PCBs?
Controlled impedance ensures that the characteristic impedance of transmission lines matches the system requirements. This helps in preventing signal distortion and reflections, thereby maintaining signal integrity.
Can standard PCB fabrication processes be used for High Frequency PCBs?
While many standard processes can be used, high-frequency PCBs may require special treatments and materials. Advanced fabrication processes, such as using specialized laminates and controlled impedance manufacturing, are often employed.
How can signal coupling in high-frequency PCBs be reduced?
Signal coupling between lines can be reduced by employing proper layout techniques and interlayer insulation design.
How do High-Frequency PCBs handle signal losses and reflections?
High-Frequency PCBs are designed to minimize signal losses through controlled impedance and proper material selection. Reflections are managed by impedance matching and designing with consideration for transmission line theory.