Low Dk Epoxy Resin Materials FCBGA Package Substrates
FCBGA PACKAGE SUBSTRATES Manufacturer.FCBGA Package Substrates Manufacturer specializes in crafting advanced substrates tailored for Flip Chip Ball Grid Array (FCBGA) packages. Our cutting-edge facility employs state-of-the-art technology to ensure precision and reliability in every substrate produced. With a commitment to innovation and quality, we cater to the diverse needs of electronic manufacturers, delivering substrates optimized for performance, durability, and miniaturization. From concept to production, our experienced team adheres to stringent quality standards, guaranteeing the utmost satisfaction for clients relying on our substrates to power their next-generation electronic devices.
In today’s booming electronics industry, FCBGA packaging substrates and Low Dk epoxy resin material PCBs have attracted much attention due to their unique properties and wide range of applications. This article takes an in-depth look at these two key technologies, revealing their central role in modern electronics design and manufacturing.
FCBGA, or ball grid array packaging, is a packaging technology widely used in electronic devices. It uses spherical solder balls to connect the chip and the substrate, providing a reliable packaging solution for high-performance circuits. Through highly dense ball grid arrays, FCBGA packaging substrates achieve excellent electrical connectivity and reliability, providing a solid foundation for the manufacture of complex electronic devices.
As electronic devices continue to pursue smaller size, higher performance and higher reliability, FCBGA packaging substrates have become an ideal choice to meet these requirements. Its unique high-density wiring technology, excellent thermal management performance and upgradeability and other key features will be analyzed in depth in this article. In addition, we will also explore the wide range of applications of FCBGA in the electronics industry, from consumer electronics to industrial automation, demonstrating its outstanding performance in different fields.
On the other hand, Low Dk epoxy resin material PCB is an important component of printed circuit boards, and its low dielectric constant (Dk) characteristics provide significant advantages for high-frequency applications. This material effectively reduces signal distortion during signal transmission while maintaining good electrical properties, providing innovative solutions for the design of communication equipment, radio frequency modules and other fields.
In this article, we will delve into the physical properties, electrical performance of Low Dk epoxy resin material PCB and its key role in high-frequency applications.
Through a comprehensive discussion of FCBGA packaging substrate and Low Dk epoxy resin material PCB, we aim to provide readers with a deep understanding of how both drive innovation in the electronics industry.
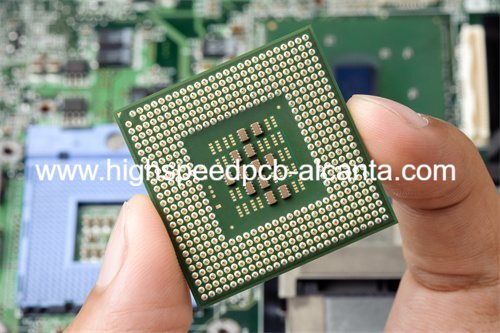
FCBGA PACKAGE SUBSTRATES Manufacturer
What is FCBGA packaging substrate?
FCBGA packaging substrate (Fine-pitch Ball Grid Array packaging substrate), as an advanced packaging technology, plays a vital role in the modern electronics field.
One of the core features of the FCBGA package substrate is its ball grid array arrangement. This means that at the bottom of the substrate, there is a dense and ordered array of ball grids. Through these tiny ball grids, electronic components can be firmly connected to the substrate. This structure not only makes the transmission of electrical signals more reliable, but also provides stable support for highly integrated chips.
Another important feature of this packaging technology is its excellent thermal performance. Since integrated circuits generate a large amount of heat when operating, the FCBGA package substrate effectively disperses and conducts heat to the outside of the substrate through its ball grid array structure. This heat dissipation mechanism helps maintain the chip operating within a safe temperature range, thereby improving the stability and reliability of the device.
FCBGA packaging substrates are widely used in modern electronic products, especially in application scenarios with high performance requirements, such as computers, communication equipment and embedded systems. Its highly integrated design not only achieves a compact layout of the circuit board, but also provides the possibility for lightweight and miniaturization of the device.
In general, FCBGA packaging substrates provide key support for the development of modern electronics with its advanced packaging technology, high-density connections and excellent heat dissipation performance. By using a precise ball grid array arrangement, it provides a reliable foundation for the stable operation of integrated circuits and lays a solid foundation for the performance improvement and innovation of electronic products.
What are the functions of FCBGA packaging substrate?
FCBGA packaging substrate (Fine-pitch Ball Grid Array) is a packaging technology widely used in the field of modern electronics. Let us have an in-depth understanding of the functions of FCBGA packaging substrate and clarify its importance in electronic devices.
The FCBGA packaging substrate has multiple functions and provides reliable support and connection for integrated circuits. First, it plays an important role in electrical connections. Through the precisely arranged ball grid array, the FCBGA package substrate achieves highly reliable signal transmission. This compact arrangement not only makes electrical connections more stable, but also increases the density of connections, adapting to the high-performance needs of modern electronic equipment.
Secondly, the FCBGA packaging substrate also plays a key role in heat dissipation. Electronic equipment generates a large amount of heat when running. If the heat cannot be effectively dissipated, it may cause chip performance to decrease or even malfunction. The FCBGA packaging substrate can effectively dissipate heat through its uniquely designed structure to ensure that the chip maintains a stable temperature during operation. This is crucial to ensure the reliability and stability of electronic equipment.
In addition, mechanical protection is also one of the functions of FCBGA packaging substrate. As the supporting structure of integrated circuits, packaging substrates can effectively protect chips from physical damage from the external environment.
Overall, the FCBGA packaging substrate performs excellent functions in providing electrical connections, thermal support, and mechanical protection. Through a dense ball grid array, it achieves highly reliable signal transmission while effectively dispersing heat to ensure that the chip maintains a stable temperature while running. This makes FCBGA packaging substrate an indispensable part in the design and manufacturing of modern electronic equipment, providing reliable and efficient solutions for various application fields.
What are the different types of FCBGA packaging substrates?
FCBGA packaging substrate, as an advanced integrated circuit packaging technology, presents various types, covering different layouts and connection densities. Understanding these types is critical to selecting the most appropriate package in a specific application.
First, we can consider the layout differences of FCBGA package substrates. In terms of layout, FCBGA packaging substrates can be divided into compact and standard types. Compact FCBGA packaging substrates usually use higher integration levels to package chips more compactly, making them suitable for applications with limited space. The standard FCBGA packaging substrate pays more attention to versatility and expansion of applicable scope, and is suitable for applications that require more flexible space layout.
Secondly, connection density is another key factor that determines the type of FCBGA package substrate. In terms of connection density, we can divide FCBGA packaging substrates into two categories: high density and standard density. The high-density FCBGA packaging substrate achieves more pins and higher signal density through a more compact layout and smaller solder ball pitch. This type is suitable for applications that require high signal transmission speed and density, such as high-performance computing and communications equipment. The standard-density FCBGA packaging substrate pays more attention to versatility and is suitable for some application fields that have less stringent signal density requirements.
During the application selection process, understanding these FCBGA package substrate types is critical to ensuring optimal performance in design and manufacturing. Different types of FCBGA packaging substrates have some unique advantages and limitations in terms of space utilization, signal transmission speed, and heat dissipation effect. Therefore, when selecting the FCBGA packaging substrate that is most suitable for a specific application, designers need to carefully consider layout and connection density requirements to take full advantage of this packaging technology. Such understanding helps ensure that electronic devices achieve optimal performance in various application scenarios and occupy a favorable position in market competition.
What is the relationship between FCBGA packaging substrate and IC packaging?
There is a close relationship between FCBGA packaging substrate (Fine-pitch Ball Grid Array) and integrated circuit (IC) packaging, which involves the classification of chip packaging technology and future development trends. Let’s delve deeper into these correlates to better understand how they interact in modern electronics.
First of all, FCBGA packaging substrate is an advanced packaging technology, mainly used to support high-density, high-performance integrated circuits. This packaging method uses a precision ball grid array to provide reliable electrical connection and heat dissipation support for the chip. Compared with traditional IC packaging, FCBGA packaging substrate has more advantages in connection density and heat dissipation performance, making it the first choice for many high-performance electronic devices.
When discussing the relationship between FCBGA and IC packaging, the primary consideration is chip packaging technology. With the continuous development of technology, chip packaging has covered a variety of different technical classifications, and FCBGA is one of the innovative packaging methods. This shows that FCBGA is not just a form of IC packaging, but has a unique position in different technical categories.
Paying attention to the development trend of chip packaging technology, we can see that requirements for higher performance and smaller size are constantly emerging. This promotes the continuous innovation and progress of FCBGA packaging substrate technology. As integrated circuits continue to evolve, packaging technology continues to adapt to new challenges and needs.
It is worth noting that there is a mutually promoting relationship between the development trend of IC packaging and the innovation of FCBGA. New chip design and performance requirements drive innovation in packaging technology, and the introduction of FCBGA packaging substrates provides effective solutions to these challenges.
Generally speaking, the relationship between FCBGA packaging substrate and IC packaging is not only reflected in technical complementarity, but also in that they jointly promote the development of the electronic field. By paying attention to the classification and future trends of chip packaging technology, we can better understand the close connection between them, providing more possibilities for the design and manufacturing of future electronic devices.
What is the difference between FCBGA packaging substrate and common PCB?
There are significant differences between FCBGA packaging substrates and traditional PCBs in many aspects. These differences not only involve their application in electronic devices, but also include key aspects such as PWBs, motherboards, substrates, and SLP.
First of all, a key difference between FCBGA packaging substrate (Fine-pitch Ball Grid Array packaging substrate) and traditional PCB (Printed Circuit Board) is its electrical connection structure. The FCBGA packaging substrate adopts a highly precise ball grid array arrangement to provide a more reliable electrical connection for the chip. This layout not only helps increase signal transmission speed, but also can cope with the needs of high-density integrated circuits, thereby optimizing the performance of electronic devices.
Secondly, as far as PWBs (Printed Wiring Boards) are concerned, FCBGA packaging substrates are usually more advanced and complex in design. By using precision wiring technology, it can achieve higher wiring density, effectively reduce the size of the circuit board, and provide smaller and lighter design solutions for electronic devices.
In terms of motherboards, FCBGA packaging substrates are usually used to support high-performance chips such as processors and graphics processing units. In comparison, traditional PCB may be used more for general electronic equipment, and its design pays more attention to versatility and cost-effectiveness.
As for the substrate, the substrate design of the FCBGA package substrate is more complex and better adapted to highly integrated chips. This design allows electronic devices to pack more functionality and performance into a relatively small size.
Finally, compared with SLP (Substrate-like PCB), the key differences between FCBGA packaging substrates lie in structure and application. FCBGA packaging substrates focus on providing electrical connections and heat dissipation support on high-performance chips, while SLP focuses more on providing PCB-like functions in a relatively thin structure.
Overall, the FCBGA packaging substrate has made it more widely used in high-performance electronic equipment through its highly precise design and advanced manufacturing technology, providing strong support for the development of modern electronic technology. Compared with traditional PCB, FCBGA packaging substrate shows unique advantages in electrical connection, performance optimization and size compression.
What are the main structures and production technologies of FCBGA packaging substrates?
As a key electronic packaging technology, FCBGA packaging substrate involves a number of innovative manufacturing processes in its main structure and production technology, especially represented by improved HDI manufacturing technology and semi-additive method.
First, we have an in-depth understanding of the structure of the FCBGA packaging substrate. The packaging substrate adopts a ball grid array layout and achieves stable support and efficient connection to the chip through fine pin arrangements. This structural design not only provides excellent electrical performance, but also provides reliable heat dissipation support for the chip to ensure that a good temperature is maintained in high-performance applications.
In terms of manufacturing technology, improved HDI manufacturing technology (High-Density Interconnect) is an important innovation in FCBGA packaging substrates. Through HDI technology, the inter-layer connection of the packaging substrate is realized, which greatly improves the density and performance of the circuit board. The advantage of this technology is that it allows more signal and power layers to be stacked in a limited space, resulting in higher integration and smaller package size. This is critical to the demands for thin, light, compact, and high performance in modern electronic devices.
On the other hand, the semi-additive method is another key technology in FCBGA packaging substrate manufacturing. Compared with the traditional full-additive method, the semi-additive method uses more refined processing technology during the manufacturing process, effectively reducing the width and spacing of the circuits, thereby improving the density and performance of the packaging substrate. This method also helps reduce manufacturing costs and improve production efficiency, making FCBGA packaging substrates more competitive.
Overall, an in-depth discussion of the structure and manufacturing technology of FCBGA packaging substrate reveals the advancement and innovation of this packaging technology. Through innovative manufacturing processes such as improved HDI manufacturing technology and semi-additive methods, FCBGA packaging substrates not only perform well in electrical connections, but also demonstrate excellent performance in high-density, high-performance applications, providing the key to the development of the modern electronics field. support. The continuous evolution of these technologies will further promote FCBGA packaging substrates to play a more important role in future electronic devices.
FAQs for FCBGA packaging substrates
When exploring the world of FCBGA (Fine-pitch Ball Grid Array) packaging substrates, we cannot ignore some common questions that relate to the core concepts and practical applications of this packaging technology. The following are answers to some key questions to help you better understand the importance of FCBGA packaging substrates and their role in the electronics field.
What are the advantages of FCBGA packaging substrate over other packaging technologies?
FCBGA packaging substrates stand out for their high density, reliable electrical connections and excellent heat dissipation performance. Compared with traditional packaging technology, its ball grid array arrangement and precision structure make it superior in supporting high-performance chips.
What application areas are FCBGA packaging substrates suitable for?
FCBGA packaging substrates perform well in applications that require a high degree of integration and reliability, such as computers, communication equipment, medical equipment, etc. Its design makes it particularly suitable for scenarios with high space and performance requirements.
How to optimize the heat dissipation performance of FCBGA packaging substrate compared with other packaging technologies?
The ball grid array of the FCBGA package substrate not only provides reliable electrical connections, but also effectively disperses the heat generated by the chip. This is achieved by optimizing material selection, thermal design and manufacturing processes.
What are the key technological innovations in the manufacturing process of FCBGA packaging substrates?
In the manufacturing process of FCBGA packaging substrate, advanced technologies such as improved HDI manufacturing technology and semi-additive method are adopted. These innovative manufacturing methods not only increase manufacturing efficiency, but also improve the performance of packaging substrates.
What key factors need to be paid attention to in the design of FCBGA packaging substrate?
When designing an FCBGA package substrate, key factors include layout optimization, electrical connection reliability, thermal design, and mechanical compatibility with the chip. Taking these factors into consideration ensures that the packaging substrate performs optimally in the actual application.
What is the future development trend of FCBGA packaging substrates?
In the future, FCBGA packaging substrates are expected to continue to develop to accommodate growing integration and performance requirements. With the continuous innovation of electronic technology, FCBGA packaging substrates will play a key role in more fields and promote the development of the entire industry.