What is DIP Package Substrate?
DIP Package Substrate Manufacturer.A DIP package substrate manufacturer specializes in crafting the foundational components crucial for Dual In-line Package (DIP) electronic devices. These substrates serve as the backbone, providing structural integrity and electrical pathways for integrated circuits. Meticulously engineered, they ensure optimal performance and reliability in various electronic applications. Utilizing advanced materials and precise manufacturing techniques, these manufacturers produce substrates tailored to meet the specific needs of diverse industries, ranging from consumer electronics to aerospace. Their dedication to quality and innovation underscores their pivotal role in enabling the seamless functioning of modern electronic systems.
DIP Package Substrate Manufacturer, high-layer/high-speed PCBs, BGA/FCBGA substrates, advanced Sap/Msap tech, fast delivery, stable quality. We offer Package Substrate from 2 layer to 20 layers.
DIP Package Substrate, that is, dual-row in-line packaging substrate, is a substrate specially designed for dual-row in-line (DIP) packaging components. In the manufacturing and integration process of electronic components, DIP Package Substrate plays a key supporting and connecting role. This type of substrate is primarily used to secure integrated circuits, resistors, and other common DIP package components to circuit boards. Its unique double-row pin structure makes this substrate easy to insert and solder to PCB (Printed Circuit Board).
DIP Package Substrate is designed with a dual-row pin layout, which means that the component’s pins are arranged in a row along both sides. This design facilitates the installation and replacement of components, while also improving the reliability of the circuit. Typically, DIP Package Substrate is made of fire-resistant fiberglass epoxy laminate (FR-4) or ceramic materials with good mechanical and electrical properties to meet various application needs.
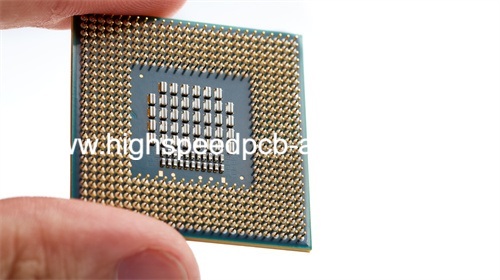
DIP Package Substrate Manufacturer
In the modern electronics industry, DIP Package Substrate plays a vital role. Not only do they provide strong support and connectivity, they also promote compact design and efficient performance of electronic devices. By understanding the features and advantages of DIP Package Substrate, engineers can better utilize this substrate to innovate and optimize circuit designs.
What types of DIP Package Substrate are there?
In PCB engineering, DIP (Dual In-Line) Package Substrate plays a vital role as the basis for various electronic components. It is crucial for engineers and hobbyists to understand the types of DIP Package Substrate and their respective characteristics. The following will introduce the main types of DIP Package Substrate and their characteristics:
FR-4 substrate is the most common type and is made from flame retardant fiberglass epoxy laminate. Its main features include high temperature resistance, chemical corrosion resistance, and high mechanical strength. FR-4 substrate is suitable for most general electronic equipment and has good insulation properties and cost-effectiveness.
Ceramic substrates have excellent thermal conductivity and stability and are suitable for applications in high temperature environments. Compared with other types of substrates, ceramic substrates can provide better heat dissipation effects, thereby ensuring the stable operation of electronic devices. Due to their high performance, ceramic substrates are often used in electronic devices that require high reliability and high temperature resistance, such as in the aerospace field.
Metal substrates have excellent thermal conductivity and heat dissipation properties and are suitable for electronic devices that require good thermal management. Metal substrates are usually made of aluminum substrates or copper substrates, and their surfaces are covered with a conductive layer and a protective layer. Metal substrates are widely used in LED lighting, power modules, automotive electronics and other fields to meet high power and high temperature requirements.
A flexible substrate is a flexible and elastic substrate, usually made of flexible polyester or polyimide materials. They are suitable for electronic devices that need to be bent and folded, such as smartphones, wearable devices, etc. Flexible substrates are thin, light, and bendable, making electronic product design more flexible and diverse.
By understanding the above types of DIP Package Substrate, engineers can choose the most appropriate substrate type according to specific application requirements to ensure excellent performance and reliability of electronic devices.
What are the advantages of using DIP Package Substrate?
Using DIP Package Substrate has many advantages compared with other boards, and these advantages play an important role in circuit design and engineering practice. Here are several advantages of using DIP Package Substrate:
First, DIP Package Substrate provides greater flexibility in the layout and installation of electronic components. Thanks to its dual-row in-line package design, components can be arranged more compactly, allowing for high-density circuit board layouts. This compactness allows electronic devices to be smaller and lighter, satisfying the constant pursuit of volume in modern electronic products.
Secondly, DIP Package Substrate performs well in thermal management. In particular, ceramic and metal substrate type DIP Package Substrate has excellent thermal conductivity and can effectively dissipate heat to ensure the stable operation of electronic components in high-temperature environments. This is particularly important for high-performance electronic equipment and industrial control systems.
In addition, DIP Package Substrate has good mechanical strength and durability. They are precision manufactured to withstand mechanical vibrations, shocks, and various stresses in the environment. This robustness ensures long-term reliability of electronic assemblies, reducing maintenance costs and failure rates.
In addition, DIP Package Substrate also has certain cost advantages in the production and assembly process. Compared with other high-end materials, such as ceramic substrates, the cost of the common FR-4 substrate is lower, which can reduce the overall production cost. This makes DIP Package Substrate the first choice for many electronics manufacturers and designers, especially for high-volume production products.
To sum up, compared with other boards, DIP Package Substrate has many advantages such as flexible layout, excellent thermal management, robustness and durability, and cost-effectiveness. In the field of electronic design and manufacturing, choosing the right substrate material is crucial, and DIP Package Substrate is the ideal choice to meet a variety of needs.
Why choose DIP Package Substrate?
There are several main reasons for choosing to use DIP Package Substrate over other types of boards in circuit design.
First, DIP Package Substrate is designed to accommodate dual-row in-line package components, which makes them more compatible with this type of component. Many electronic products use dual-row in-line package components, such as integrated circuits and resistors, so DIP Package Substrate has become the first choice.
Secondly, DIP Package Substrate provides a compact design, which contributes to the miniaturization and lightweight of electronic devices. This compactness is critical for circuit designs that require a high degree of integration, especially in space-constrained applications.
In addition, DIP Package Substrate usually has good thermal management performance. Certain types of DIP Substrate, such as ceramic and metal substrates, have excellent thermal conductivity properties and help to effectively disperse heat, thereby improving the reliability and performance stability of the circuit.
In addition, the cost of DIP Package Substrate is also relatively low, making it an affordable option. When mass production of electronic products is required, cost considerations are crucial, and DIP Package Substrate can reduce production costs while maintaining quality.
In summary, DIP Package Substrate was chosen for circuit design mainly because of its compatibility with dual-row in-line package components, compact design, excellent thermal management performance, and affordable cost. These features make DIP Package Substrate an ideal choice for many electronic product designs.
How to make DIP Package Substrate?
The process of manufacturing DIP Package Substrate involves several key steps, which are detailed below:
Substrate preparation: The first step in manufacturing DIP Package Substrate is to prepare the substrate. The substrate is usually made of materials such as fiberglass epoxy (FR-4) or ceramics. At this stage, the size and shape of the substrate are cut and processed according to the requirements of the final product.
Circuit Pattern: Next, the circuit pattern needs to be drawn on the substrate. This is typically accomplished by depositing a conductive material, such as copper, onto the surface of the substrate and using techniques such as photolithography and etching to define the conductors and connection points on the circuit board.
Component Installation: Once the circuit pattern is completed, installation of the DIP components can begin. These components include integrated circuits, resistors, capacitors, etc. On automated assembly lines, components are precisely positioned and glued to the appropriate locations on the substrate.
Soldering: Once the components are installed, soldering is required to ensure their electrical connection to the base plate. Soldering can be done through techniques such as traditional wave soldering or hot air reflow soldering. This ensures a solid connection between the component and the substrate.
Testing and Inspection: The last step is to test and inspect the manufactured DIP Package Substrate. The functionality and connectivity of each component can be ensured through the use of automated test equipment and visual inspection systems. The purpose of this phase is to catch and fix any potential manufacturing defects to ensure the quality and reliability of the final product.
Through this series of precise steps, manufacturers are able to produce standard-compliant DIP Package Substrate, providing a reliable foundation for the manufacturing of various electronic devices.
What are the applications of DIP Package Substrate?
As a key component of electronic devices, DIP Package Substrate is widely used in various fields and applications. Here are some of the main areas and applications:
DIP Package Substrate is widely used in the consumer electronics industry, such as smartphones, tablets, digital cameras, etc. In these devices, DIP Package Substrate carries various integrated circuits and components, including processors, memories, sensors, etc. Their compact design and reliable connectivity enable these electronic devices to achieve higher performance and smaller size.
In automotive electronic systems, DIP Package Substrate is widely used in control units, sensors, engine management systems, etc. Due to the harsh conditions of the automotive environment, the DIP Package Substrate needs to have high temperature resistance, vibration resistance and high reliability to ensure the stable operation of the automotive electronic system.
The field of industrial automation requires a large number of controllers, sensors and actuators, and these devices usually use DIP Package Substrate as the basis of the circuit board. In fields such as factory automation, robotics, and smart manufacturing, DIP Package Substrate plays a vital role in helping to achieve precise control of equipment and efficient production.
Communication equipment such as routers, switches, base stations, etc., require a large number of electronic devices to realize data transmission and communication functions. As a key component of these devices, DIP Package Substrate provides stable electrical connections and good thermal management performance, ensuring high reliability and stability of communication equipment.
LED lighting products require efficient power management and stable circuit design to ensure the brightness and stability of the lamps. DIP Package Substrate provides excellent thermal conductivity properties, which can effectively dissipate heat, extend the service life of LED lamps, and maintain their high efficiency.
In general, DIP Package Substrate plays an important role in many fields and applications, providing a stable and reliable foundation for the design of various electronic devices and systems. Its excellent performance and wide applicability make DIP Package Substrate an indispensable part of the electronic engineering field.
Where can I find DIP Package Substrate?
When looking for a reliable DIP Package Substrate supplier, choosing a suitable partner is crucial to ensuring product quality and project success. As a company with rich experience and good reputation, we are committed to providing high quality DIP Package Substrate and can meet your specific needs. Here are a few channels where you can find our DIP Package Substrate:
Company Website: Please visit our company website where you can find detailed information about our products and services. Our website provides an online catalog and product specifications so you can understand the types and features of DIP Package Substrate we offer.
Online Platforms: We also offer our products on major online platforms, including electronic component distributor websites and electronic markets. You can search our company name or product model on these platforms to find and purchase our DIP Package Substrate.
Trade Shows: We frequently attend trade shows and exhibitions within the industry, which are great opportunities to learn about our products and communicate with us directly. You can connect with us by attending these events and further discuss your project needs and customization requirements.
Sales Representatives: Our sales team is ready to assist and support you. You can contact our sales representatives via phone, email or online chat with your inquiries and needs. We will be happy to provide you with personalized solutions and support services.
Reputation in the industry: We have won the trust and recognition of customers in the industry with our high-quality products and professional services. You can get word-of-mouth and recommendations about our company and products by consulting peers or industry experts.
Overall, as a DIP Package Substrate supplier, we provide you with multiple options and convenient ways to obtain our products and ensure you get a satisfactory solution. Whether you are looking for standard products or customized services, we are dedicated to meeting your needs and contributing our expertise and experience to the success of your project.
What is the quote for DIP Package Substrate?
Obtaining a quote for DIP Package Substrate is not static and is affected by many factors. When considering price, the following factors need special consideration:
Substrate material: The material selection of DIP Package Substrate has an important impact on its performance and cost. Common materials include FR-4, ceramic and metal substrates. The prices of different materials vary greatly and directly affect the final quotation.
Board thickness and size: The thickness and size of the substrate also affects its cost. Thicker or larger substrates generally require more material and processing costs and therefore are more expensive.
Number of layers and complexity: The number of layers and circuit complexity of DIP Package Substrate will affect the complexity of the production process, thereby affecting the cost. More layers and more complex circuit designs usually mean higher costs.
Solder mask and metallization: Solder mask and metallization are important steps in substrate surface treatment and can affect welding quality and electrical performance. Different surface treatment processes may require additional costs.
Production quantity: Production quantity has a significant impact on the unit price. Generally speaking, large-volume production can achieve lower unit prices, while small-volume production has higher costs.
Special requirements and customized services: If customers have special requirements or need customized services, such as special mask colors, special testing requirements, etc., the cost may increase.
Suppliers and lead times: Different suppliers may have different quotes and lead times. Choosing reputable suppliers to ensure timely supply and good after-sales service is also one of the considerations.
To sum up, getting a quote for DIP Package Substrate requires taking into account multiple factors and weighing the different factors to find the solution that best suits your needs and budget.
Frequently Asked Questions (FAQs)
Can DIP Package Substrates be used for surface-mount components?
DIP Package Substrates are specifically designed for Dual In-Line Package components, which typically involve through-hole mounting. While it’s technically possible to adapt DIP substrates for surface-mount components, it may require additional design considerations and modifications to accommodate surface-mount technology.
Are DIP substrates compatible with lead-free soldering processes?
Yes, DIP substrates can be manufactured to be compatible with lead-free soldering processes. However, it’s essential to ensure that the substrate material and surface finishes are suitable for lead-free soldering to achieve reliable solder joints and comply with environmental regulations.
What are the typical lead times for manufacturing DIP Package Substrates?
Lead times for manufacturing DIP Package Substrates can vary depending on factors such as substrate material, complexity of the design, and production volume. Generally, lead times range from a few days to several weeks, with larger quantities and custom specifications potentially requiring longer production times. It’s advisable to consult with the substrate manufacturer to obtain an accurate lead time estimate based on specific project requirements.
How do DIP Package Substrates compare to other packaging solutions in terms of thermal performance?
DIP Package Substrates offer competitive thermal performance compared to alternative packaging solutions. Ceramic substrates, in particular, excel in thermal conductivity and stability, making them suitable for applications requiring efficient heat dissipation. Metal core substrates also provide enhanced thermal management capabilities, making them ideal for power electronics and LED applications. However, the choice of substrate material should be carefully evaluated based on the specific thermal requirements of the application.
Can DIP Package Substrates be reused or recycled?
While it’s technically possible to reuse or recycle DIP Package Substrates, practical considerations such as component removal, substrate condition, and environmental regulations may affect the feasibility of these processes. In some cases, substrates may undergo refurbishment or rework to extend their lifespan, but this typically requires specialized equipment and expertise. Recycling options for DIP substrates may vary depending on local regulations and the availability of recycling facilities for electronic components.