What is CSP packaging substrate?
CSP Package Substrate Manufacturer.A CSP (Chip Scale Package) substrate manufacturer specializes in crafting the vital foundation for cutting-edge microelectronics. With precision engineering and advanced materials, they produce substrates that form the backbone of compact, high-performance electronic devices. These substrates serve as the platform for mounting and connecting integrated circuits, ensuring optimal electrical conductivity and thermal management. Leveraging state-of-the-art manufacturing techniques, they meet the stringent demands of modern technology, enabling the seamless integration of microchips into a diverse array of applications, from smartphones and wearables to automotive electronics and beyond.
As an advanced packaging technology, CSP (Chip Scale Package) packaging substrate plays a vital role in the modern electronics field. So, what exactly is a CSP packaging substrate? How does it achieve a more compact and efficient connection between the chip and the substrate?
CSP packaging substrate is a compact packaging technology. Its core concept is to reduce the chip size to a package size that is equivalent to the chip, thus realizing the concept of “chip-scale packaging”. Traditional packaging technologies often require additional surrounding space to accommodate connectors and pads during the packaging process, while the CSP packaging substrate integrates these components within the scope of the chip packaging, minimizing the package size.
The compact design of the CSP packaging substrate makes the connection between the chip and the substrate tighter and more efficient. By packaging the chip directly onto the surface of the substrate, CSP packaging eliminates the length of the connection line between the chip and the substrate in traditional packaging, thereby significantly reducing signal transmission delay and improving signal transmission rate and stability. In addition, CSP packaging can also reduce the size and weight of the package, making it particularly suitable for applications with strict space requirements, such as mobile devices, consumer electronics and medical equipment.
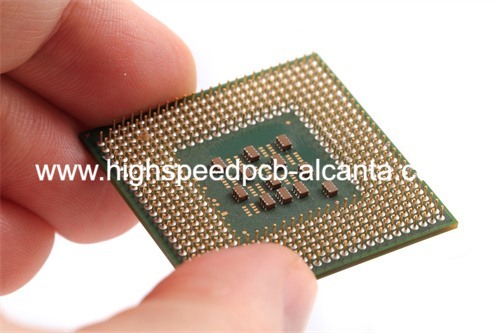
CSP Package Substrate Manufacturer
In general, CSP packaging substrate, as a compact and efficient packaging technology, achieves a more compact and efficient connection between the chip and the substrate by minimizing the package size and optimizing the connection design. This advanced packaging technology provides important support for the performance improvement and size reduction of electronic products, and also brings new opportunities and challenges to the development of various application fields.
What types of CSP packaging substrates are there?
As an indispensable part of the modern electronics industry, CSP packaging substrates come in various types. In this world, there are two main common types: organic substrates and inorganic substrates. Both types differ in materials, properties and applications.
Organic substrates typically use organic resin-based materials, most commonly FR-4 (fiberglass reinforced epoxy). This material has good electrical and mechanical properties and is relatively cheap. Organic substrates are suitable for many applications such as consumer electronics, communication equipment, and automotive electronics. Their manufacturing costs are relatively low and suitable for mass production.
Compared with organic substrates, inorganic substrates usually use ceramic materials, such as aluminum oxide (Alumina) or silicon nitride (Silicon Nitride). These materials have better thermal conductivity and high temperature resistance, making inorganic substrates suitable for applications requiring greater stability and reliability, such as high-power electronics, microwave and radio frequency circuits. Although inorganic substrates are more expensive to manufacture, this disadvantage is often offset by their superior performance in high-performance applications.
In general, both organic and inorganic substrates play an important role in the world of CSP packaging substrates, and each has unique advantages and scope of application. Selecting the appropriate packaging substrate type depends on the requirements of the specific application, including performance, cost and reliability considerations. As technology continues to develop and innovate, we can expect more types of packaging substrates to emerge to meet changing market demands.
This is a brief introduction to CSP packaging substrate types, I hope this can help you better understand and choose the packaging substrate type that suits your project needs.
What are the advantages of CSP packaging substrate?
CSP package substrate (Chip Scale Package Substrate) is one of the most anticipated packaging technologies in the modern electronics field. Compared with traditional packaging methods, it has shown many unique advantages and is therefore very popular. The following are the advantages of CSP packaging substrates:
The CSP packaging substrate is extremely compact in size, reducing the size of the chip to a comparable size, effectively saving space resources. This miniaturized design enables the CSP packaging substrate to perform well in products with limited volume such as mobile devices, making it possible for products to be lightweight and compact.
The CSP packaging substrate improves the communication speed and stability between chips through a more compact design and short-path connections. Compared with traditional packaging, CSP packaging substrates have higher performance in data transmission, power consumption control, etc., making them widely used in various application scenarios.
CSP packaging substrates have more effective thermal management capabilities due to their small size. The close arrangement between chips improves heat dissipation efficiency, helps reduce the temperature of the system, and ensures stable operation of the equipment for a long time. It is especially suitable for high-performance equipment that is sensitive to temperature.
The CSP packaging substrate has a compact design and tighter connections between chips, which greatly improves the integration of the system. In the same size space, the CSP packaging substrate can accommodate more functional modules, providing a broad space for device function expansion and performance improvement.
Although CSP packaging substrate technology has higher manufacturing costs than traditional packaging technology, its miniaturized design and high-performance characteristics can significantly save the cost of other system components, thereby achieving overall cost reduction. In addition, the high integration and reliability of CSP packaging substrates also bring lower costs to equipment maintenance and management.
To sum up, CSP packaging substrate has become one of the most favored packaging technologies in the electronics industry today due to its size advantage, high performance, excellent heat dissipation effect, high-density integration and cost-effectiveness. Its wide application in mobile devices, consumer electronics, medical equipment and other fields will open up a broader space for the development of intelligent connection technology and help usher in the intelligent era.
Why choose CSP packaging substrate?
In today’s rapidly developing technology field, choosing the right packaging technology is crucial. The CSP (Chip Scale Package) packaging substrate has attracted much attention and favor because of its unique features.
CSP packaging substrate is more compact and smaller than traditional packaging technology. Its size is equivalent to that of a chip, minimizing the area of the circuit board, making the device thinner, lighter and more portable, while improving the overall integration of the system.
Due to the small size of the CSP package substrate, the distance between the chip and the substrate is closer, which helps to manage the heat generated by the chip more effectively. This advantage makes CSP packaging substrates more outstanding in high-performance and high-density application scenarios, providing stable and reliable performance.
The CSP packaging substrate has a compact design and simple connections, enabling higher integration. By reducing connection paths and wire lengths, not only can signal transmission speeds be increased, but signal interference and power consumption can also be reduced, thereby improving system performance.
CSP packaging substrates are suitable for various fields, including mobile devices, consumer electronics, medical equipment, etc. Its small size and excellent performance make it an ideal choice for many modern electronic products, able to meet the size, performance and power consumption requirements of different industries.
Although CSP packaging substrates excel in performance and integration, their manufacturing costs are relatively low. Compared with traditional packaging technology, CSP packaging substrate design is simpler and the manufacturing process is more efficient, so it can save costs for manufacturers and improve competitiveness.
To sum up, CSP packaging substrates stand out among many packaging technologies due to their size advantages, good thermal management, high integration, wide applicability and cost-effectiveness. Choosing CSP packaging substrate means choosing a more advanced, more efficient and more reliable solution, which can bring huge advantages and opportunities to the design and manufacturing of electronic products.
How are CSP packaging substrates manufactured?
The manufacturing process of CSP (Chip Scale Package) packaging substrate is a precise and complex project, involving multiple key steps. From design to manufacturing to testing, every link is crucial. Let’s dive into the mysteries of this process.
First, the manufacturing of CSP packaging substrates begins in the design phase. At this stage, engineers use advanced CAD (computer-aided design) software to design the packaging substrate structure that meets the chip requirements and application needs. Factors such as wiring, component arrangement, and thermal management need to be taken into consideration during the design process to ensure that the packaging substrate can operate stably and reliably in actual applications.
Once the design is complete, the manufacturing phase begins. The first is substrate manufacturing, usually using organic or inorganic substrate materials. Organic substrates often use FR-4 materials, while inorganic substrates use materials such as ceramics. During the manufacturing process, the substrate is processed into a shape and size that meets the design requirements through cutting, drilling, chemical etching and other processes.
Next is chip packaging, which is one of the core steps in CSP packaging substrate manufacturing. In the chip packaging process, the chip is mounted on a substrate and connected to the substrate through soldering or other connection techniques. In addition, testing and quality control are required during the packaging process to ensure that the packaging is intact and meets specifications.
Finally, the manufactured CSP packaging substrate needs to undergo rigorous testing. This includes visual inspection, electrical performance testing, thermal dissipation performance testing and many other aspects. Only after passing various tests can the substrate be recognized as a qualified product and can be put into practical applications.
In general, the manufacturing process of CSP packaging substrates is a complex project that integrates design, manufacturing and testing, requiring precision operations and strict control by engineers. Only through careful polishing and inspection of every link can we produce stable and reliable CSP packaging substrates, providing efficient and compact solutions for various applications.
Through understanding of this manufacturing process, we can have a deeper understanding of the manufacturing principles and process flow of CSP packaging substrates, providing a more solid foundation for its application.
What fields are CSP packaging substrates suitable for?
CSP (Chip Scale Package) packaging substrate, as a compact packaging technology, has shown its broad application prospects in many fields. From smartphones to medical equipment, from consumer electronics to industrial automation, CSP packaging substrates are bringing revolutionary changes to all walks of life.
CSP packaging substrates are widely used in mobile devices, especially in products such as smartphones and tablets. Due to its small size, stable performance and good thermal management capabilities, CSP packaging substrates can meet the needs of modern mobile devices for high performance, high integration and thin and light design, bringing revolutionary changes to the mobile device industry.
In addition to mobile devices, CSP packaging substrates are also widely used in consumer electronics, such as headphones, watches, smart home devices, etc. Its small size and high performance make consumer electronics products more portable and intelligent, providing users with a more convenient and comfortable experience.
In the field of medical equipment, the high-density integration and good thermal management capabilities of CSP packaging substrates provide strong support for the research and development of medical sensors, health monitoring equipment and other medical devices. By using CSP packaging substrates, medical equipment can achieve more accurate and reliable data collection and processing, thereby improving the efficiency and accuracy of medical diagnosis and treatment.
In the field of industrial automation, the high performance and reliability of CSP packaging substrates provide technical support for the intelligence and automation of industrial control systems, sensors, robots and other equipment. With the help of CSP packaging substrates, industrial equipment can achieve more efficient data processing and communication, improve production efficiency and product quality, and promote the development of industrial automation.
In general, CSP packaging substrate, as an advanced packaging technology, is constantly expanding its application fields and bringing innovative changes to all walks of life. In the future, with the continuous advancement of technology and the continuous expansion of application scenarios, CSP packaging substrates will play a more important and extensive role, contributing more to the progress and development of human society.
How to obtain CSP packaging substrate?
In today’s high-tech field, CSP packaging substrate, as an advanced packaging technology, has an important impact on the performance and volume of various electronic devices. So, for you, as an electronic component supplier, how to obtain CSP packaging substrate? Here are some ways and suggestions:
As an electronic component supplier, you can obtain the products you need by working directly with CSP packaging substrate manufacturers. These manufacturers usually provide CSP packaging substrates of various specifications and models, which you can select and order according to customer needs.
In addition to working directly with manufacturers, you can also obtain CSP packaging substrates through electronic component distributors. These distributors often have relationships with multiple manufacturers and can offer a diverse selection of products with more flexibility in inventory and lead times to suit your business needs.
With the development of the Internet, many electronic component manufacturers and distributors have opened stores on various online market platforms. You can browse and purchase the required CSP packaging substrates through these platforms. This method is not only convenient and fast, but also allows you to enjoy certain price concessions and after-sales service.
Regular participation in industry exhibitions and exchange meetings is also one of the effective ways to obtain CSP packaging substrates. At these events, you can communicate and negotiate face-to-face with various manufacturers and distributors, learn about the latest product information and market trends, and provide strong support for your business development.
In general, as an electronic component supplier, you can obtain CSP packaging substrates through various channels such as direct cooperation with manufacturers, using distribution channels, using online market platforms, and participating in industry exhibitions. Choosing a method that suits your business needs and development direction will help you better serve your customers and promote the development and growth of your company’s business.
If you have any questions about the purchase of CSP packaging substrates or need further assistance, please feel free to contact us and we will wholeheartedly provide you with support and services.
What is the price of CSP packaging substrate?
In the modern electronics industry, CSP (Chip Scale Package) packaging substrate, as an advanced packaging technology, provides compact and efficient solutions for various electronic devices. However, for many people, understanding the price of CSP packaging substrates is crucial. So, what is the price of CSP packaging substrate? Let’s dig a little deeper.
First of all, it needs to be made clear that the price of CSP packaging substrates is affected by many factors, including but not limited to the following points:
Specifications and dimensions: The specifications and dimensions of the CSP packaging substrate have a direct impact on its price. Generally speaking, the smaller the size and the higher the specification, the cost of the CSP packaging substrate will be relatively higher.
Material cost: The materials used to manufacture CSP packaging substrates also have an important impact on their prices. High-quality materials and advanced manufacturing processes often result in increased costs.
Manufacturing process: Different manufacturing processes and technical levels will also directly affect the price of CSP packaging substrates. Advanced manufacturing processes may increase manufacturing costs, but often also improve product quality and performance.
Production volume: Production volume is another important factor affecting the price of CSP packaging substrates. Generally speaking, high-volume production reduces the cost per unit, while low-volume production increases costs.
Based on the combined influence of the above factors, the price range of CSP packaging substrates is quite wide, ranging from a few dollars to tens of dollars. The specific price depends on the customer’s needs and requirements, as well as the manufacturer’s pricing strategy.
Generally speaking, for mass-produced standard specification CSP packaging substrates, the price may be relatively low, usually between a few dollars to more than ten dollars per unit. For customized, high-performance CSP packaging substrates, the price may be higher, and may even exceed tens of dollars.
What are the common problems with CSP packaging substrates?
What are the typical reliability concerns associated with CSP package substrates?
CSP package substrates, despite their compact design and high integration capabilities, may face reliability challenges related to solder joint integrity, thermal management, and mechanical stresses. Ensuring robust design and manufacturing processes can mitigate these concerns.
How do thermal issues impact CSP package substrates, and how can they be addressed?
Thermal management is crucial for CSP package substrates, as their compact size may lead to increased heat concentration and potential performance degradation. Effective thermal dissipation techniques, such as improved material selection, optimized layout designs, and proper heat sinking, are essential for maintaining device reliability.
What are the main causes of electrical failures in CSP package substrates?
Electrical failures in CSP package substrates can arise from various factors, including inadequate signal routing, poor interconnect design, and insufficient power distribution. Thorough testing and analysis during the design phase can help identify and address potential electrical issues early on.
How do manufacturing defects affect the quality of CSP package substrates?
Manufacturing defects, such as voids in solder joints, substrate warpage, and material inconsistencies, can significantly impact the reliability and performance of CSP package substrates. Strict quality control measures and advanced inspection techniques are essential for minimizing manufacturing defects and ensuring product quality.
What measures can be taken to enhance the reliability of CSP package substrates?
To improve the reliability of CSP package substrates, several measures can be implemented, including optimizing material selection, refining manufacturing processes, conducting thorough reliability testing, and implementing robust failure analysis methodologies.