What is Cavity PCB?
Cavity PCB Manufacturer.A Cavity PCB Manufacturer specializes in crafting printed circuit boards (PCBs) with cavities, intricate recesses within the board. These specialized boards are designed for specific applications where components need protection or precise fitting. The manufacturer employs advanced techniques to create these cavities, ensuring high precision and reliability. From medical devices requiring shielding to aerospace applications demanding lightweight yet durable solutions, the expertise of a Cavity PCB Manufacturer is indispensable. Their innovative approach combines technology and craftsmanship to meet the unique needs of various industries, driving advancements in electronic design and manufacturing.
Cavity PCB (grooved printed circuit board) is an innovative design that leads the forefront of printed circuit board technology. It cleverly combines rigid and flexible characteristics, bringing new possibilities to the field of electronic packaging. Its unique feature is the groove structure designed on its surface, which provides a more flexible solution for the layout of integrated circuits and other components.
In the design of Cavity PCB, the clever combination of rigid and flexible materials makes this printed circuit board highly customizable. The traditional combination of rigid boards and flexible boards usually has limitations in connection points, and Cavity PCB makes the connection between these boards more flexible by introducing grooves on the surface, while increasing the overall bending flexibility.
The design drew inspiration from a thorough comprehension of the spatial limitations and intricate layout demands inherent in electronic packaging. The incorporation of a groove structure enhances the available space for electronic components, granting designers greater flexibility in arranging and organizing integrated circuits, sensors, connectors, and other elements. This innovative design not only fulfills the criteria for high performance and miniaturization but also proves adaptable to diverse application scenarios.
The groove structure provides larger insertion and installation space for components, reduces the possibility of mechanical conflict, and improves component stability and reliability. This design makes Cavity PCB ideal for implementing highly complex circuit layouts in limited space.
Overall, Cavity PCB is unique in its innovative design that aims to overcome the limitations of traditional circuit boards in terms of space utilization and layout. By integrating rigid and flexible properties and introducing groove structures on the surface, Cavity PCB brings more flexible and high-performance solutions to the field of electronic packaging and will play an increasingly important role in future electronic product design.
What are the types of Cavity PCB?
As an emerging technology in the field of electronic packaging, Cavity PCB does cover a variety of different types, including single-layer and multi-layer structures. Each type is designed and carefully optimized for a specific application area to meet the needs and challenges of different projects.
First of all, the single-layer Cavity PCB mainly achieves the integration and packaging of electronic components by creating a groove structure on the single-layer circuit board. This design is suitable for scenarios with strict space requirements, such as some embedded systems, lightweight equipment, or products that require flexible design. The single-layer structure of Cavity PCB has lower manufacturing costs and a more simplified manufacturing process, making it an ideal choice for some small and medium-sized projects.
Secondly, the multi-layer Cavity PCB achieves more complex circuit layout and larger-scale component integration by embedding grooves on multiple levels. This design is suitable for applications with higher requirements on performance and complexity, such as high-performance computing equipment, communication base stations and industrial control systems. The multi-layer structure of Cavity PCB allows for more circuit levels, providing higher integration and design freedom while maintaining a smaller overall size.
Different types of Cavity PCBs offer distinct features and advantages tailored to specific needs. The single-layer structure prioritizes compactness and flexibility, making it ideal for lightweight and small electronic products. On the other hand, the multi-layer structure is designed for heightened performance and complexity, making it suitable for large systems and high-demand applications.
Moreover, Cavity PCB designs can be customized to meet the specific requirements of individual projects. This includes the ability to tailor parameters such as the shape, size, and location of the grooves, ensuring adaptability to the unique needs of diverse applications.
When choosing Cavity PCB, a reasonable choice of single-layer or multi-layer structure based on the specific needs of the project will better promote the innovation and performance improvement of electronic products.
What are the advantages of Cavity PCB?
Cavity PCB (grooved printed circuit board) has shown impressive advantages in the field of electronic packaging. Compared with traditional printed circuit boards, it is not only highly customizable, but also has excellent heat dissipation performance and more flexible layout. options, these advantages make Cavity PCB the first choice among many innovative product designs.
First, Cavity PCB’s high degree of customizability provides engineers with extensive design freedom. Its unique groove structure allows the circuit board to be flexibly laid out in three-dimensional space to better adapt to devices of different shapes and sizes. This customizability makes Cavity PCB an ideal choice to meet special design needs, especially as modern electronic products become increasingly miniaturized. The flexibility of Cavity PCB provides designers with more room for innovation.
Furthermore, Cavity PCB excels in heat dissipation performance due to its innovative groove structure, which provides an expanded surface area for efficient heat dissipation. This attribute is particularly crucial for high-performance electronic equipment like servers and communication devices. The exceptional heat dissipation capability of Cavity PCB contributes to lowering the temperature of electronic components, enhancing system stability and reliability, thereby ensuring prolonged operational integrity.
Moreover, Cavity PCB offers heightened flexibility in layout options. The incorporation of the groove structure enables the circuit board to accommodate a greater number of components while facilitating a more compact design within confined spaces. This feature is especially pivotal in the design of contemporary electronic products, particularly in domains like mobile devices, smart wearables, and medical devices, where spatial efficiency stands as a critical factor for product success. Cavity PCB empowers designers with enhanced possibilities to craft sophisticated and potent products through its versatile layout options.
Taken together, Cavity PCB has become the first choice in today’s innovative product design with its high degree of customizability, excellent heat dissipation performance and more flexible layout options. In the trend of pursuing smaller, high-performance electronic devices, Cavity PCB has demonstrated its excellent advantages in meeting special design needs, improving heat dissipation efficiency, and achieving more compact designs. In the future, with the continuous development of technology, Cavity PCB is expected to continue to play an important role in the field of electronic packaging and promote the continuous emergence of innovative products.
Why choose Cavity PCB?
Cavity PCB (cavity printed circuit board) has emerged in the field of electronic engineering. Its unique groove structure provides electronic engineers with unprecedented design freedom, thus attracting widespread attention and applications. On the question of why Cavity PCB is chosen, we need to delve into its unique features compared to traditional printed circuit boards and under what circumstances it is more suitable.
First of all, the most striking feature of Cavity PCB is that its surface contains groove structures. This special design gives Cavity PCB a more flexible physical form, allowing it to adapt to various complex electronic product designs. Compared with traditional printed circuit boards, Cavity PCB’s groove structure can accommodate components and components, achieving a higher degree of integration, helping to solve the needs of modern electronic products for small, lightweight, and high performance.
The design freedom of Cavity PCB is a unique advantage over other circuit boards. Electronic engineers can arrange and organize circuit components more flexibly without the limitations of traditional floor plans. The groove structure not only allows three-dimensional layout of components, but also provides more possibilities for optimal design of circuits. This design freedom makes Cavity PCB ideal for complex circuit needs, especially where space is used efficiently.
Compared with traditional printed circuit boards, the differences of Cavity PCB are not only reflected in the structure, but also include unique features in performance and applicable scenarios. In designs where space is limited or special shapes are required, Cavity PCB can fit better and provide a higher degree of integration. Its groove structure not only reduces the weight of the circuit board, but also optimizes heat dissipation performance, making it suitable for electronic products with high heat dissipation requirements.
In the design of high-performance, miniaturized and lightweight electronic products, Cavity PCB shows its obvious advantages. For example, mobile devices, medical monitoring instruments, and some military application scenarios have strict requirements on the size and performance of circuit boards. Cavity PCB provides an ideal solution through its unique design.

Cavity PCB
What is the manufacturing process of Cavity PCB?
The production of Cavity PCBs involves a highly intricate and precise manufacturing process with multiple crucial steps, each significantly influencing the performance and reliability of the final product. A comprehensive understanding of the Cavity PCB manufacturing process requires special attention to key aspects such as groove preparation, multi-layer structure stacking, and metallization.
The initial focus in Cavity PCB manufacturing is on the preparation of grooves, a pivotal step that employs advanced cutting techniques like CNC cutting machines or laser cutting. These techniques meticulously create groove structures on the substrate surface. Beyond determining the overall shape of the circuit board, these grooves provide adaptable space for subsequent component installation and wiring. Achieving precision in the groove preparation process is crucial, demanding meticulous control to ensure that each circuit board maintains a consistent groove shape and size, adhering closely to design specifications.
During the manufacturing process, these layers are precisely stacked together to form an overall circuit board structure. This process requires precise layer-to-layer alignment to ensure uninterrupted signal transmission and power distribution within the circuit. At the same time, the choice of insulating materials and metal layers between layers is also crucial, affecting the insulation and conductive properties of the circuit board.
Finally, metallization is an integral part of Cavity PCB manufacturing. This step involves applying a metallized coating to a metal layer on or within the circuit board to achieve electrical conductivity in the circuit. In the manufacture of Cavity PCB, metallization must be precise to the micron level to ensure reliable and stable connections for each wire and pad. Manufacturers often use high-precision techniques such as chemical deposition and electroplating to achieve the required conductive properties.
Precision and process control are critical throughout the Cavity PCB manufacturing process. Deviation in any step can result in degraded board performance or manufacturing defects. Therefore, manufacturers use strict quality control and testing methods during the production process to ensure that each Cavity PCB meets design requirements and industry standards. This highly engineered manufacturing process makes Cavity PCB ideal for the needs of complex electronic devices.
What are the applications of Cavity PCB?
Cavity PCB (grooved printed circuit board), as an innovative electronic packaging technology, shows a wide range of application prospects and has achieved remarkable success in many fields. Its unique design structure and flexibility make it the first choice in fields such as high-end communication equipment, medical instruments, and industrial control systems.
In the field of high-end communication equipment, the application of Cavity PCB highlights its excellent performance in meeting high-performance and miniaturization requirements. Since communication equipment usually requires highly integrated electronic components to support complex functions, the design structure of Cavity PCB allows the effective integration of multiple components in a limited space, providing higher circuit density and more reliable performance. In addition, the unique heat dissipation performance of Cavity PCB helps maintain the stable operation of communication equipment and ensures that it maintains good performance in high-temperature environments.
In the field of medical instruments, the wide application of Cavity PCB reflects its excellent performance in meeting the stringent requirements of medical equipment for high reliability and precision. Medical equipment often requires complex circuits to support various monitoring and diagnostic functions, and the design of Cavity PCB makes it possible to accommodate more functional components inside compact medical equipment. Its use inside space-constrained medical equipment helps improve device performance and meet the medical industry’s stringent standards for reliability and safety.
In the field of industrial control systems, the unique design advantages of Cavity PCB are reflected. Industrial control systems usually need to operate in extreme environments, which places extremely high requirements on the performance and stability of electronic components. The groove structure of Cavity PCB not only provides more flexible circuit layout options, but also allows dust-proof, waterproof and shock-resistant design to be integrated inside the circuit board, thereby enhancing the stability and durability of the industrial control system. At the same time, the high-performance heat dissipation characteristics of Cavity PCB help maintain the stability of electronic components under high load operation and provide excellent performance for industrial control systems.
Overall, the wide application of Cavity PCB not only reflects its unique value in high-end communications, medical and industrial control fields, but also demonstrates its excellent performance in environments with limited space and high-performance requirements. Its flexibility, customizability and reliability make Cavity PCB one of the key technologies that attract much attention in the field of electronic engineering today.
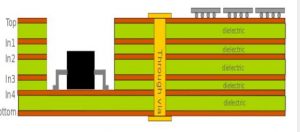
Cavity PCB
How to get Cavity PCB?
Securing high-quality Cavity PCBs is paramount for electronic engineers and product designers. Here are effective strategies for obtaining the necessary information when selecting the ideal Cavity PCB suppliers and manufacturers.
Firstly, it is advisable to directly reach out to our company, a reputable Cavity PCB supplier. We specialize in delivering excellent Cavity PCB solutions with a wealth of experience, committed to providing high-performance and reliable options tailored to diverse industries. Collaborating with us ensures access to a professional team, advanced manufacturing technology, and customized solutions to address your specific project requirements.
Alternatively, for those exploring additional supplier options, online platforms and e-marketplaces offer valuable resources. Several professional electronic component markets provide comprehensive supplier information, featuring numerous companies specializing in Cavity PCB production. These platforms furnish detailed insights such as company profiles, product specifications, and customer reviews, facilitating well-informed decision-making.
Moreover, industry exhibitions and technical seminars serve as excellent avenues to discover Cavity PCB suppliers. Active participation in these events enables direct face-to-face communication with manufacturers and suppliers, providing in-depth insights into their technical expertise, product quality, and service standards. This direct engagement helps establish a trustworthy relationship and lays a solid foundation for future collaboration.
Finally, you can use professional communities and forums to share your experiences with other electronics engineers and get recommendations and advice. Peer experience in online communities can provide you with real insights about different vendors, helping you make informed decisions.
Overall, choosing the appropriate Cavity PCB supplier and manufacturer requires some research and comparison. Working with a reliable supplier will provide strong support for your project, ensuring you receive high-quality, high-performance Cavity PCBs that meet your design and production needs.
What is the Cavity PCB quotation?
Obtaining a quote for Cavity PCB is one of the important tasks that both electronic engineers and manufacturers have to face during the design and production stages. This process involves multiple factors and considerations that determine final cost and manufacturing feasibility. Here are some tips and key information on how to get a quote for Cavity PCB.
First, it is crucial to understand the factors that go into Cavity PCB quotes. These factors can be divided into technical and commercial aspects:
The configuration of a Cavity PCB involves varying layers and layer counts, directly influencing production complexity and costs. The detailed specification of groove shapes and depths is crucial, significantly impacting the production process and required craftsmanship, necessitating precision in quoting.
Material choices, encompassing substrate and metallization materials, not only directly impact costs but also influence the performance and reliability of Cavity PCBs. Careful consideration of these materials is vital in the quoting process.
Surface treatment, a critical aspect for welding and assembly, adds another layer of complexity to the quote. The type of surface treatment selected becomes a key element in ensuring the success of the manufacturing process.
Moreover, the selection of manufacturers plays a pivotal role. Different manufacturers may adopt distinct pricing strategies and possess varying production capabilities, necessitating comprehensive evaluation when choosing a partner for Cavity PCB production.
Lead time: If there is a tighter lead time demand, the manufacturer may adjust prices to accommodate expedited production.
Design complexity: Complex designs may require more processes and inspection steps, thus affecting the quotation.
When getting a quote for Cavity PCB, it is also crucial to note the following:
Specify Detailed Design Requirements: Furnish comprehensive design documents that delve into specific details such as groove specifications, material requirements, and other pertinent information. This ensures manufacturers have a precise understanding of the project’s intricacies.
Evaluate Multiple Manufacturers: Reach out to several manufacturers, comparing their quotes, production capabilities, and service offerings. Through this comparative analysis, choose a partner that aligns best with your project requirements.
Negotiate Thoughtfully: Upon receiving quotations, engage in negotiation, particularly for sizable orders or long-term collaborations. Moderate negotiations can help achieve mutually beneficial agreements.
Emphasize Quality: While the allure of the lowest price is present, prioritize quotes that come with a quality guarantee. Ensuring that the chosen manufacturer maintains high standards is crucial for a successful project.
By adhering to these considerations, electronic engineers and manufacturers can efficiently obtain quotes for Cavity PCBs. This approach ensures not only the most cost-effective solutions but also the alignment of the chosen manufacturing partner with specific project needs.
Frequently Asked Questions (FAQs)
What are the main types of Cavity PCB?
Cavity PCBs come in various types, encompassing both single-layer and multi-layer structures. Each variant is meticulously optimized to cater to specific application domains, adeptly addressing the diverse requirements of various scenarios.
What are the advantages of Cavity PCB over other circuit boards?
Cavity PCB has many advantages over traditional circuit boards. Its grooved structure makes it stand out in terms of heat dissipation performance, design flexibility and performance superiority, making it the first choice for many innovative product designs.
In which application fields does Cavity PCB excel?
Cavity PCBs find extensive applications in high-end communication equipment, medical instruments, industrial control systems, and diverse fields. Their notable design flexibility and superior performance make them well-suited for environments characterized by constrained space and demanding performance requirements.
What is the manufacturing process of Cavity PCB?
The production of Cavity PCB involves several key steps, including the preparation of grooves, the assembly of multi-layer structures, metallization, and other crucial procedures. Precise execution and meticulous process control throughout the manufacturing process are essential to guarantee the optimal performance of the end product.
How to obtain Cavity PCB? Any recommended suppliers?
To obtain Cavity PCB, you can work with professional suppliers and manufacturers. These suppliers are typically able to provide high-quality Cavity PCBs, ensuring product reliability and performance.
How is the quote for Cavity PCB determined?
Securing a quote for a Cavity PCB involves considering several factors, such as design specifications, material preferences, and manufacturing intricacies. It’s crucial to obtain quotes from multiple suppliers to guarantee that you receive the most competitive pricing. This comparative approach ensures that you not only meet your design and quality requirements but also optimize costs through a thorough evaluation of available supplier options.
What are the performance characteristics of Cavity PCB?
Cavity PCB performance features include superior thermal performance, high customizability, flexible design options and adaptability to space constraints. These characteristics make Cavity PCB uniquely valuable in the design of complex electronic products.