What are Ball Grid Array (BGA) Package Substrates?
Ball Grid Array Package Substrate Manufacturer.A Ball Grid Array (BGA) Package Substrate Manufacturer specializes in creating the foundational layers used in BGA packages, which are crucial for mounting integrated circuits. They design and produce high-quality substrates that ensure reliable electrical connections and mechanical support. These substrates are vital for advanced electronic devices, providing the necessary pathways for signal transmission and heat dissipation. This manufacturer plays a key role in the electronics industry, contributing to the performance and miniaturization of modern gadgets and systems.
Ball Grid Array (BGA) Package Substrates play a vital role in the manufacturing of modern electronic devices. They are a basic component used to mount and connect integrated circuits (ICs), providing a unique way to improve the efficiency and performance of electronic packaging.
In traditional circuit board design, the chips on the circuit board are connected through pads and pins. However, as electronic products become increasingly smaller and more powerful, the traditional pin connection method has become insufficiently flexible and reliable. This introduces the concept of BGA Package Substrates.
The main feature of BGA Package Substrates is that they use a set of solder balls on the bottom of the package instead of traditional pins. These solder balls are arranged in a regular grid, hence the name “ball grid array”. With this layout, BGA Substrates is able to achieve more connection points in a relatively small space while providing higher electrical performance and thermal management capabilities.
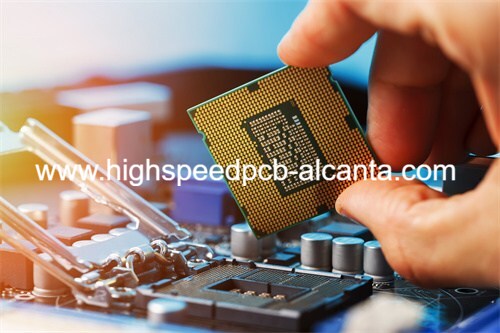
Ball Grid Array Package Substrate Manufacturer
Why are BGA Package Substrates so important? First, their design allows electronic devices to pack more functionality and performance into a smaller size. This is particularly important for devices such as smartphones, tablets, and laptops that rely on compact size and high performance. Secondly, BGA Substrates provide a more reliable connection, reducing mismatch and soldering issues on the circuit board, thereby improving product reliability and stability.
Overall, the emergence of Ball Grid Array (BGA) Package Substrates not only improves the performance and functionality of electronic devices, but also promotes progress and innovation in the electronics manufacturing industry. Through in-depth understanding and application of BGA Package Substrates, we can maintain a competitive advantage in an increasingly competitive market and meet consumer demand for smaller, stronger, and more reliable electronic products.
What types of BGA Package Substrates are there?
Ball Grid Array (BGA) Package Substrates, as an important part of modern electronic packaging, have many types, each type has its own unique characteristics and applicable scenarios. The following is an introduction to several common BGA Package Substrates types, their characteristics and application scenarios:
Organic substrate BGA Package Substrates are usually made of organic materials such as FR-4 and have the following characteristics:
Cost-effective: Lower costs due to the use of common organic materials.
Suitable for general applications: Suitable for electronic equipment with general performance requirements, such as household appliances and low-end communication equipment.
Ceramic substrate BGA Package Substrates are made of ceramic materials and have the following characteristics:
Excellent thermal conductivity: Ceramic materials have good thermal conductivity and help improve heat dissipation performance.
High reliability: Due to the stability and high temperature resistance of ceramic materials, it has high reliability.
Suitable for high-performance applications: Suitable for areas requiring high performance and high reliability, such as aerospace and medical equipment.
Metal core BGA Package Substrates use metal materials as substrates and have the following characteristics:
Excellent heat dissipation performance: Metal materials have good thermal conductivity and help to effectively dissipate heat.
High mechanical strength: The metal substrate has high mechanical strength and can withstand large mechanical stress.
Suitable for high-power applications: Suitable for high-power applications that require high thermal performance and mechanical strength, such as power modules and automotive electronics.
Flexible substrate BGA Package Substrates are made of flexible materials and have the following characteristics:
Flexible: The flexible substrate can bend and is suitable for application scenarios that require flexible design.
High space utilization: Due to the characteristics of the flexible substrate, it can better utilize space and is suitable for compact designs.
Suitable for curved surface design: Suitable for applications requiring curved surface design, such as portable devices and wearable devices.
Different types of BGA Package Substrates play important roles in different application scenarios. Engineers can choose the most suitable type according to specific needs to achieve the best performance and reliability.
What are the advantages of using BGA Package Substrates?
In modern electronic packaging, the use of Ball Grid Array (BGA) Package Substrates brings a series of significant advantages compared to traditional packaging methods. These advantages make BGA Package Substrates very popular.
First, BGA Package Substrates have obvious advantages in thermal management. Traditional packaging methods often cannot effectively handle the heat generated by integrated circuits, which can lead to device overheating and performance degradation. BGA Package Substrates adopts the design of spherical solder joints, which makes the heat conduction between the device and the base plate more efficient, effectively reducing the device temperature and ensuring the stability and reliability of the device.
Secondly, BGA Package Substrates excel in electrical performance. Compared with flat welding in traditional packaging methods, BGA solder balls provide a shorter and more stable electrical connection path, reduce signal transmission loss and electromagnetic interference, improve signal transmission rate and stability, and help improve Equipment performance.
In addition, the miniaturization feature of BGA Package Substrates is also one of its advantages. Because BGA solder balls can arrange more connection points in a smaller space, BGA Package Substrates can achieve higher I/O density, providing greater flexibility and freedom for device design. This is particularly important for today’s pursuit of thin, light and compact electronic devices.
In addition, BGA Package Substrates have higher reliability. The spherical design of BGA solder joints can absorb and relieve mechanical stress, reducing the risk of fatigue and breakage of solder joints, thus improving the life and stability of the device and reducing maintenance costs and risks.
Finally, the production cost of BGA Package Substrates is relatively low, which is one of the reasons why they are so popular. The automated production process of BGA welding is more efficient and cost-saving than traditional packaging methods. At the same time, BGA Package Substrates require relatively few materials and resources, which is beneficial to reducing overall production costs.
In summary, compared with traditional packaging methods, the use of BGA Package Substrates has multiple advantages such as thermal management advantages, electrical performance advantages, miniaturization advantages, higher reliability, and lower production costs. Therefore, it is highly favored in today’s electronic field. favor.
Why choose BGA Package Substrates?
In modern electronic design and packaging, BGA Package Substrates have become the first choice instead of traditional packaging methods. This is because BGA Package Substrates have many advantages over traditional packaging methods, making them more suitable in many application scenarios.
First, BGA Package Substrates have significant advantages in signal transmission and thermal management. Compared with traditional packaging methods, BGA Package Substrates have shorter signal paths, reducing signal delays and transmission losses, thereby improving signal integrity. In addition, BGA Package Substrates uses ball solder joint connectors, which have better thermal conductivity and can more effectively dissipate the heat generated by the device and keep the device within a good operating temperature range, thus improving the reliability and stability of the system.
Secondly, the high-density integrated design of BGA Package Substrates gives it more advantages in space utilization. Because BGA Package Substrates use ball solder joint connectors, more input/output connection points can be achieved in a smaller package size, thus achieving higher I/O density. This high-density integrated design gives BGA Package Substrates significant advantages in application scenarios that require miniaturization and high performance requirements, such as portable electronic devices, smartphones, and tablets.
In addition, the manufacturing process and assembly process of BGA Package Substrates are more simplified and automated. Because BGA Package Substrates uses ball solder joint connectors, its assembly process is simpler than traditional pin-type packages and can achieve a higher level of automation, thereby reducing production costs. This gives BGA Package Substrates more advantages in mass production and can meet the market’s demand for high quality and low cost.
In summary, BGA Package Substrates have clear advantages over traditional packaging methods, including better signal transmission and thermal management performance, higher integration density, and simpler manufacturing and assembly processes. Therefore, in many application scenarios, especially for electronic products that require high performance, compact design and cost-effectiveness, choosing BGA Package Substrates is a wise choice.
What is the manufacturing process of BGA Package Substrates?
The manufacturing process of BGA Package Substrates is a complex and precise process involving multiple key steps, each of which has an important impact on the quality and reliability of the final product. Here are the key steps in the manufacturing process of BGA Package Substrates and how to ensure the quality and reliability of the final product:
The first step in manufacturing BGA Package Substrates is design and planning. This includes determining the required materials, dimensions, laminate construction, and circuit layout. Designers must consider electronic product requirements and specifications to ensure that the final product can meet performance and reliability requirements.
Choosing the right substrate material is critical to manufacturing high-quality BGA Package Substrates. Common substrate materials include organic substrates (such as FR-4), ceramic substrates and metal substrates. Material selection depends on the application area, performance requirements and cost considerations.
The process of substrate manufacturing involves steps such as material pre-processing, lamination and compression. During this process, it is necessary to ensure that the material of each layer is evenly distributed and reaches the required thickness and precision. Every step in the manufacturing process must be tightly controlled to ensure substrate quality and consistency.
After substrate fabrication is complete, chip layout and connection become the next critical step. This involves mounting integrated circuits (ICs) on a substrate and using a soldering process to connect them to the circuit traces of the substrate. This step requires high-precision equipment and technology to ensure the correct alignment and reliable connection of the chips.
BGA Package Substrates are unique in that the bottom is covered with a series of solder balls for connection to the PCB. Solder ball processing involves adhering the solder balls to the underside of the chip, ensuring their even distribution and correct alignment. Quality control at this step is critical to ensure the quality of each solder ball and connection stability.
The last critical step is quality control and testing. At this stage, manufacturers will conduct strict quality inspection and functional testing of BGA Package Substrates to ensure that they meet design specifications and have stable performance. This may include visual inspection, solder joint strength testing, electrical testing, etc.
Through the above key steps, manufacturers can ensure that the quality and reliability of BGA Package Substrates reach expected levels. Strict manufacturing processes and quality control measures are key factors in ensuring the superior performance of BGA Package Substrates in a variety of applications.
What are the application scenarios of BGA Package Substrates?
BGA Package Substrates are widely used in multiple industries, and their roles and contributions vary. The following are some typical industry application scenarios:
In the consumer electronics industry, such as smartphones, tablets, game consoles and wearable devices, BGA Package Substrates play a key role. They are used to integrate various chips and devices into compact devices, enabling high-performance and high-density electronic layouts. In addition, BGA Substrates’ superior thermal management capabilities enable equipment to maintain stable performance over long periods of use, while reducing failure rates and improving product reliability.
In the automotive electronics industry, BGA Package Substrates are widely used in key components such as automotive control units, infotainment systems, and advanced driver assistance systems (ADAS). Due to the harshness of the automotive environment and high requirements for reliability, BGA Substrates’ stability and high-density connections make it the first choice. It can effectively resist vibration and temperature changes during vehicle operation, ensuring long-term reliable operation of electronic systems.
In the field of aerospace and defense, BGA Package Substrates are widely used in key applications such as avionics equipment, radar systems and satellite communication equipment. These applications place extremely high demands on highly reliable electronic components and strong anti-interference capabilities, and BGA Substrates meets these requirements with its excellent performance and stability. Its excellent thermal management performance and high-density connections make BGA Substrates play an irreplaceable role in the aerospace and defense industry.
To sum up, BGA Package Substrates play an important role in consumer electronics, automotive electronics, aerospace and defense and other industries. Its superior performance, reliability and high-density connections make it an indispensable key component in modern electronic equipment.
Where can I find BGA Package Substrates?
Finding a reliable supplier of BGA Package Substrates is critical, especially for companies with both standard and custom needs. As a professional supplier, we provide a wide range of BGA Package Substrates solutions to meet the needs of different customers.
First, you can search the Internet to find BGA Package Substrates suppliers. Through search engines, you can find the websites of multiple suppliers and learn about their products and services. Make sure to choose a supplier with a good reputation and extensive experience to ensure product quality and reliability.
Secondly, attending industry shows and exhibitions is another effective way to find BGA Package Substrates suppliers. At these exhibitions, you can communicate directly with various suppliers and learn about their product features and technical capabilities. Such face-to-face interactions help build trusting relationships and lay the foundation for future collaboration.
In addition, you can also look for BGA Package Substrates suppliers by referring to recommendations from peers in the industry. Talk to other companies to learn about their experience working with them and recommended suppliers. This word-of-mouth is often one of the surest ways to find reliable suppliers.
Finally, it is also a good option to consider working directly with our company. As a BGA Package Substrates supplier, we offer a variety of standard and custom solutions to meet your specific needs. We have advanced production equipment and rich industry experience to provide you with high-quality products and professional technical support.
Overall, finding a reliable BGA Package Substrates supplier requires some time and effort, but with the methods mentioned above, you can find the right supplier that meets your needs, thereby bringing long-term success to your project and business. success and development.
What is the quote for BGA Package Substrates?
BGA Package Substrates are a key component in modern electronic packaging. When selecting suppliers and evaluating costs, it is crucial to understand their price calculation and quotation methods. The following will introduce the key factors behind BGA Package Substrates’ quotations and the way suppliers provide quotations.
Price calculations for BGA Package Substrates usually consider the following key factors:
Substrate type and quality: Different types of substrates (such as organic substrates, ceramic substrates, metal substrates, etc.) and different quality levels will directly affect the price. For example, ceramic substrates are generally more expensive than organic substrates but have better thermal conductivity and reliability.
Number of layers and complexity: The number of layers and design complexity of BGA Package Substrates will affect production costs. Multi-layer structures and complex wiring may require more processes and higher manufacturing costs.
Size and pore size: The size and pore size of the substrates will also have an impact on the price. Larger sizes and smaller hole diameters generally mean more material and higher tooling costs.
Surface treatment and special requirements: Special surface treatments (such as gold plating, anti-corrosion coatings, etc.) and customized requirements (such as special shapes, edge connections, etc.) may increase costs.
Frequently Asked Questions (FAQs)
What are Ball Grid Array (BGA) Package Substrates and how do they differ from traditional PCBs?
Ball Grid Array (BGA) Package Substrates are specialized substrates used in electronic packaging to mount and interconnect integrated circuits (ICs). Unlike traditional PCBs, BGA substrates utilize an array of solder balls beneath the package, facilitating robust connections and improved thermal management.
What are the advantages of using BGA Package Substrates?
BGA Package Substrates offer several advantages, including enhanced thermal management, improved electrical performance, miniaturization capabilities, higher reliability, and cost-effectiveness. These attributes make them ideal for applications requiring compact designs and high-density interconnects.
Are BGA Package Substrates suitable for high-reliability applications such as aerospace and defense?
Yes, BGA Package Substrates are well-suited for high-reliability applications due to their robust solder connections and efficient heat dissipation capabilities. They are commonly used in avionics, radar systems, satellite communication devices, and other aerospace and defense applications.
How are BGA Package Substrates manufactured?
The manufacturing process of BGA Package Substrates involves several critical steps, including substrate preparation, layer buildup, solder ball attachment, and testing. Each stage is meticulously executed to ensure the quality and reliability of the final product.
Can BGA Package Substrates be customized to specific application requirements?
Yes, BGA Package Substrates can be customized to meet specific application requirements. Manufacturers offer options for substrate materials, sizes, configurations, and surface finishes to accommodate diverse needs.