What is ABF Package Substrate?
ABF Package Substrate Manufacturer.ABF Package Substrate Manufacturer specializes in crafting advanced substrate solutions for semiconductor packaging. With cutting-edge technology and meticulous craftsmanship, they engineer substrates to meet the exacting demands of modern electronics. Their expertise lies in producing high-density interconnects, enabling efficient signal transmission and superior thermal management. From concept to production, they ensure quality and precision, catering to diverse applications in consumer electronics, automotive, and beyond. Trusted by leading tech companies worldwide, they drive innovation in the field, shaping the future of semiconductor packaging with their state-of-the-art ABF substrates.
What exactly is ABF Package Substrate? This question leads us to the heart of modern electronic packaging technology. ABF (Ajinomoto Build-up Film) Package Substrate is a key high-density integrated circuit packaging material. It consists of multiple layers of films that are used to support and connect chips and other packaged components.
The ABF Package Substrate is a crucial component in modern electronic devices, serving to support and interconnect chips while facilitating their connection to the circuit board. Comprised primarily of a base material consisting of thin films, typically composed of specialized polyimide or polyamide materials, it ensures optimal performance and reliability.
Engineered to accommodate the requirements of high-density integrated circuits, the substrate features exceedingly fine lines and perforations, meeting the demands for miniaturization and enhanced functionality in contemporary electronics. Its manufacturing process is intricate, involving the layering, patterning, metallization, and other intricate procedures to ensure the quality and efficacy of the final product.
The significance of the ABF Package Substrate extends beyond its fundamental role as a packaging material; it serves as a technological enabler for the advancement of modern electronic devices. From smartphones to automotive electronic systems, from communication apparatus to medical equipment, this substrate is indispensable, furnishing a steadfast foundation and support for these high-performance, highly reliable electronic products.
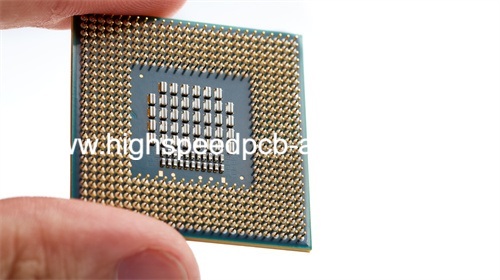
ABF Package Substrate Manufacturer
In essence, the ABF Package Substrate stands as an indispensable electronic packaging material, providing essential electrical and mechanical support for modern electronic devices by facilitating chip support and connection. Its high density and superior performance render it an integral element of the contemporary electronics industry, propelling ongoing innovation and product development.
What are the different types of ABF Package Substrate?
ABF (Ajinomoto Build-up Film) Package Substrate is a key high-density integrated circuit packaging material, and its different types are suitable for various application scenarios. Here are the two main types:
HDI boards, a prevalent type of ABF Package Substrate, are characterized by their high density of lines and insertion holes. These boards are well-suited for high-performance, compact electronic devices with stringent space constraints. HDI boards can accommodate more levels, allowing for increased functionality and connections within a limited board size.
Rigid-Flex boards, a notable variant of ABF Package Substrate, offer a blend of advantages from both rigid and flexible circuit boards. These specialized boards are engineered to allow specific regions to bend or flex while retaining rigidity in other sections. Such a distinctive construction renders Rigid-Flex boards particularly suitable for applications where space is at a premium, such as automotive electronics, aerospace systems, and medical devices. The design of Rigid-Flex boards minimizes the number of component connection points, thereby improving system reliability and enabling intricate three-dimensional designs.
In summary, various types of ABF Package Substrates, including HDI boards and Rigid-Flex boards, play vital roles in diverse application scenarios, offering essential support for the performance and reliability of electronic products. By selecting the appropriate type of ABF Package Substrate, designers can better fulfill the requirements of product design and drive the advancement of the electronics industry.
Why choose ABF Package Substrate?
In the modern electronics industry, there’s a growing preference for ABF Package Substrate as a crucial material over traditional options like FR-4 boards. This shift is primarily due to several key factors:
Enhanced Performance and Reliability: ABF Package Substrate outperforms FR-4 boards in terms of both performance and reliability. Thanks to its exceptional dielectric properties and signal transmission capabilities, ABF materials are extensively utilized in high-speed communication and automotive electronics. In environments requiring high-frequency and high-speed transmission, ABF Substrate effectively preserves signal integrity, minimizing signal attenuation and distortion. This, in turn, elevates system performance and reliability.
Superior Mechanical Properties: ABF Package Substrate doesn’t just excel in electrical performance but also boasts significant advantages in mechanical performance. This translates to improved durability and stability in electronic products. Whether enduring the vibrations typical in automotive electronics or the rigors of daily use in mobile devices, ABF Substrate maintains optimal performance, ensuring prolonged and stable operation of the product.
Due to the excellent processing performance of ABF Package Substrate, designers can more flexibly design complex circuit structures and achieve higher density wiring and more complex packaging forms. Compared with traditional FR-4 boards, ABF Substrate is easier to implement multi-layer, high-density wiring, helping to design more compact and lightweight electronic products. In addition, ABF Substrate makes it easier to perform drilling, circuit making and other processing steps, providing greater convenience and efficiency for the manufacturing process.
In summary, ABF Package Substrate has emerged as the preferred option for designing and producing a growing array of electronic products, owing to its superior performance, reliability, outstanding mechanical characteristics, and ease of processing, alongside enhanced flexibility and convenience. With the ongoing evolution of the electronics sector and technological advancements, I anticipate that ABF Substrate will assume an even greater significance in the future, offering sustained backing for the innovation and advancement of electronic products.
In what fields is ABF Package Substrate widely used?
ABF Package Substrate serves as a pivotal electronic packaging material across various industries, owing to its exceptional performance and reliability. It finds extensive application in communication, automotive electronics, and consumer electronics sectors.
ABF Package Substrate, serving as a high-density integrated circuit packaging material, effectively meets the requirements for miniaturization and superior performance in communication equipment. Its impressive signal transmission characteristics further enhance the stability and performance of communication systems.
The ABF Package Substrate plays a pivotal role in automotive electronics, particularly in vital components like in-car entertainment systems and automotive radars. With the progression of automotive technology towards intelligence and electrification, there’s an escalating demand for electronic products that offer improved performance and dependability. The resilient thermal and mechanical characteristics of ABF Package Substrate render it highly suitable for enduring severe conditions such as elevated temperatures, humidity, and vibrations in automotive settings. This ensures the steadfast and consistent functionality of electronic systems in demanding automotive scenarios.
ABF Package Substrate, with its high density, superior signal transmission performance, and thermal characteristics, meets the requirements for miniaturization, lightweight design, and high-speed communication in consumer electronic products. This, in turn, elevates the competitiveness and market share of such products.
In conclusion, ABF Package Substrate holds significant importance across communication, automotive electronics, consumer electronics, and other sectors. Its stellar performance and reliability serve as crucial pillars supporting electronic products across various domains, thereby propelling the advancement and growth of the entire electronics industry.
How to get ABF Package Substrate?
The ABF Package Substrate is a pivotal component within the modern electronics industry, playing an essential role in both product design and manufacturing workflows. As a respected supplier and manufacturer, our company is fully committed to delivering a diverse array of ABF Substrate solutions tailored precisely to our clients’ needs.
We offer a comprehensive range of ABF Substrate options, encompassing various types and configurations, spanning from HDI boards to Rigid-Flex boards and customized substrates. Our primary focus remains on furnishing top-tier products that aptly address the unique demands of our clientele.
Our proficiency lies in crafting bespoke ABF Substrate solutions meticulously aligned with the specific requirements of our customers. Whether it pertains to material selection, layer design, or distinct process specifications, we excel in providing personalized services to ensure optimal compatibility with their design and application parameters.
Central to our operations is an unwavering commitment to product excellence and dependability. We meticulously oversee every facet of the manufacturing journey, leveraging cutting-edge equipment and methodologies to uphold the stability and performance of ABF Substrate solutions. Rigorous quality assessments and certifications underscore our adherence to global standards and the quality expectations of our customers.
Beyond delivering superior products, we extend professional technical assistance and services. Our seasoned technical team stands ready to offer comprehensive consultancy, design enhancements, and post-sales support, aiding customers in tackling diverse technical hurdles encountered in ABF Package Substrate application.
We offer flexible delivery options, ensuring prompt product supply and distribution tailored to our clients’ needs and project timelines. Whether it involves fulfilling small-batch orders or large-scale customization requirements, we pride ourselves on timely delivery, facilitating the seamless advancement of customer projects.
Through our company’s supply services, customers can easily obtain high-quality, reliable ABF Package Substrate products, providing solid basic support for the design and manufacturing of their electronic products.
How is the quotation of ABF Package Substrate determined?
How is the quotation of ABF Package Substrate determined? This involves comprehensive consideration of a variety of factors, including material cost, design complexity, and production scale. Let’s find out in detail:
First of all, material cost is one of the important factors in determining the quotation of ABF Package Substrate. The production cost of ABF materials directly affects the overall manufacturing cost. ABF Package Substrate usually uses high-quality Ajinomoto Build-up Film (ABF) as the base material, and the cost of ABF materials is affected by raw material prices, supply and demand relationships, and manufacturing technology. Therefore, the price of ABF Substrate will vary as material costs fluctuate.
Secondly, design complexity will also have an impact on the quotation of ABF Package Substrate. Complex designs require more production steps and technical support, which will increase manufacturing costs. For example, if the design contains high-density circuits, micro-apertures or special hierarchies, it will increase the difficulty and cost of manufacturing. Therefore, the higher the design complexity, the quotation of ABF Substrate will increase accordingly.
Finally, production scale is also one of the important factors affecting the quotation of ABF Package Substrate. Generally speaking, large-scale production can bring cost economies of scale because as output increases, fixed costs can be spread over more products, thereby reducing the cost of each product. Therefore, for large quantity orders, suppliers usually offer more competitive prices. Conversely, small-scale production may result in higher unit costs.
To accurately determine the quotation for ABF Substrate, various factors such as material expenses, intricacy of design, and production volume come into play. For an exact estimate, it’s advisable to engage in detailed discussions with the supplier, furnishing specific design specifications and production requirements. This collaborative approach ensures that the supplier can devise a tailored quotation plan that aligns with your needs. Effective communication and cooperation facilitate the acquisition of ABF Package Substrate that meets your standards, enabling successful project execution.
What are the common problems with ABF Package Substrate?
Does ABF Package Substrate have any compatibility issues with certain components?
Compatibility issues may arise with certain components, particularly if they have specific requirements regarding thermal expansion or signal integrity. It’s essential to ensure compatibility through thorough testing and analysis during the design phase.
Are there any challenges related to manufacturing ABF Package Substrate?
Manufacturing ABF Package Substrate can present challenges such as ensuring uniform layer thickness, precise alignment of layers, and controlling factors like humidity and temperature during production. These challenges require careful monitoring and quality control measures to maintain consistency and reliability.
Are there compatibility issues with certain components when using ABF Package Substrate?
In some cases, compatibility issues may arise with specific components. It’s essential to verify compatibility during the design phase to avoid issues with connectivity or performance.
How does ABF Package Substrate handle thermal challenges, and are there potential overheating concerns?
While ABF Substrate typically exhibits good thermal performance, intensive applications or improper thermal management can lead to overheating. Designers should consider adequate heat dissipation solutions.
Are there restrictions on the design complexity when opting for ABF Package Substrate?
Generally, ABF Substrate provides flexibility in design. However, extremely complex designs may pose challenges during manufacturing, and designers should collaborate with manufacturers for optimal results.