What is the definition of 3D IC Package Substrates?
3D IC Package Substrate Manufacturer.The 3D IC Package Substrate Manufacturer is at the forefront of cutting-edge technology, crafting substrates that enable the integration of multiple layers of semiconductor devices. With precision engineering and innovative techniques, they fabricate substrates that serve as the foundation for advanced electronic systems. Their expertise lies in creating intricate designs that optimize electrical performance and thermal management, meeting the demands of high-performance computing and emerging applications. As pioneers in their field, they continually push the boundaries of possibility, driving the evolution of semiconductor packaging towards greater efficiency and functionality.
In the field of modern electronic packaging, 3D IC Package Substrates, as a key component, play a vital role. They are not only substitutes for traditional PCBs (Printed Circuit Boards), but also an advanced electronic packaging solution that provides a new way to optimize the performance, power consumption and volume of electronic equipment.
First, let us understand the concept of 3D IC Package Substrates. In short, 3D IC Package Substrates are substrates for vertically stacked integrated circuits (ICs). They provide physical support and electrical connections so that multiple ICs can be connected to each other in the vertical direction. Traditional electronic packaging solutions often install ICs on a flat PCB. The emergence of 3D IC Package Substrates breaks this limitation and allows ICs to be stacked in a vertical manner, thereby achieving higher integration and performance.
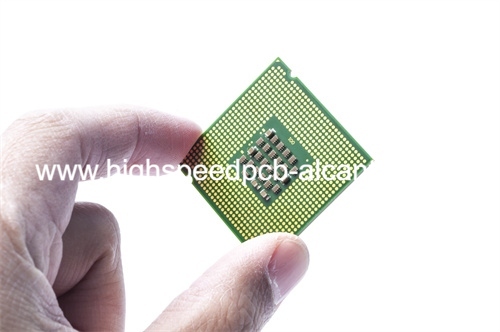
3D IC Package Substrate Manufacturer
So, how do 3D IC Package Substrates relate to vertical stacking of ICs? This involves the core concept of 3D integration. In traditional 2D packaging, ICs are usually mounted on a flat substrate and connected by horizontal interconnect lines. In 3D packaging, ICs are stacked vertically and connected through vertical interconnection channels, and these interconnection channels are supported and implemented by 3D IC Package Substrates. Through this vertical stacking method, 3D IC Package Substrates not only saves space, but also reduces the length of interconnect lines and reduces signal transmission delays, thereby improving performance and bandwidth.
Therefore, it can be said that 3D IC Package Substrates play a key role in modern electronic packaging. They not only provide physical support and electrical connections for the vertical stacking of ICs, but also provide new possibilities for performance optimization and functional realization of electronic devices. sex.
What are the different types of 3D IC Package Substrates?
In the field of 3D IC Package Substrates, organic substrates, ceramic substrates and silicon interposer substrates are the three main types, each type has its unique characteristics and advantages.
Organic substrate is a common type of 3D IC Package Substrates, usually made of organic materials such as FR-4 or polyimide. This type of substrate is highly flexible, low-cost, and suitable for a wide range of applications. Due to their flexibility, organic substrates can be adapted to different sizes and shapes, making them ideal for many electronic products.
Ceramic substrates are another common type of 3D IC Package Substrates, which are mainly made of ceramic materials such as aluminum oxide, aluminum nitride or zirconium oxide. Ceramic substrates have higher thermal conductivity and better mechanical strength than organic substrates and are therefore widely used in applications requiring high power and reliability. Ceramic substrates also offer excellent corrosion resistance and stability, making them suitable for harsh environmental conditions.
Silicon interposer substrate is an emerging type of 3D IC Package Substrates that uses silicon material as the substrate. The silicon interposer substrate realizes the stacking and interconnection of multi-layer ICs by making tiny holes (Through-Silicon Via, TSV) on the silicon substrate. Due to the excellent thermal conductivity and electrical properties of silicon, silicon interposer substrates have excellent thermal management capabilities and high-density integration advantages, and are suitable for high-performance computing and communications fields.
In general, each type of 3D IC Package Substrates has its unique advantages and applicable scenarios. Choosing the appropriate type depends on the requirements of the specific application, such as cost, performance, and reliability. By having an in-depth understanding of different types of 3D IC Package Substrates, we can better select and design solutions suitable for specific applications and promote the development and innovation of electronic packaging technology.
What are the advantages of 3D IC Package Substrates?
The advantages of 3D IC Package Substrates are reflected in many aspects. Compared with traditional PCBs, they bring significant performance improvements, space utilization optimization and thermal management improvements to electronic packaging.
First of all, 3D IC Package Substrates have outstanding advantages in performance. By enabling vertically stacked integrated circuits, these substrates are able to minimize interconnect lengths between components, thereby reducing signal delays and increasing system performance and bandwidth. This tight stacking structure can also promote the stability and reliability of signal transmission, providing more powerful support for high-speed communication and data processing of electronic devices.
Secondly, 3D IC Package Substrates can optimize space utilization. Traditional PCBs often face space constraints and are difficult to meet the demand for miniaturization and lightweight. The vertical integration design of 3D IC Package Substrates can effectively reduce the physical size of the system, allowing electronic devices to implement more functions in a smaller volume. This space optimization not only improves the portability and ease of use of the device, but also provides designers with greater creative space and promotes product innovation and differentiation.
In addition, 3D IC Package Substrates improve thermal management. As the performance of electronic devices continues to improve, heat generation and emissions have become important factors restricting their stable operation. Traditional PCBs are limited to horizontal layout, and their heat conduction and heat dissipation capabilities are limited, which can easily lead to concentration of hot spots and performance degradation. 3D IC Package Substrates adopts a more complex stacking structure and thermal conductivity design, which effectively disperses heat, improves heat dissipation efficiency, and ensures the stability and reliability of the system. This optimized thermal management not only extends the service life of electronic equipment, but also reduces maintenance costs and failure rates, bringing better experience and value to users.
Overall, 3D IC Package Substrates brings new development opportunities and solutions to the field of electronic packaging with its excellent performance, space optimization and thermal management capabilities. With the continuous advancement of technology and the continuous expansion of applications, they will continue to play an important role in various fields, driving the continuous evolution and innovation of electronic equipment.
Why choose 3D IC Package Substrates?
In the field of modern electronic packaging, the emergence of 3D IC Package Substrates has triggered new thinking about circuit design and integration. Compared with traditional flat PCB (Printed Circuit Board), choosing 3D IC Package Substrates brings many unique advantages, making it the first choice for engineers.
First, 3D IC Package Substrates have excellent performance advantages. By stacking multiple integrated circuits (ICs) vertically together, 3D IC Package Substrates can significantly shorten interconnect lengths, thereby reducing signal delays and increasing system operating speed and bandwidth. This vertical integration approach can also reduce the size of the circuit board, making the device more compact and lightweight.
Secondly, 3D IC Package Substrates have unique advantages in space utilization. Traditional flat PCBs are limited in wiring and assembly, while 3D IC Package Substrates can achieve vertical stacking, maximize space utilization, and provide room for more functions and components, thereby achieving higher integration and richer functions. .
In addition, 3D IC Package Substrates also have excellent thermal management capabilities. Because integrated circuits are more tightly packed vertically, heat is distributed more evenly throughout the device. In addition, manufacturers can integrate efficient heat dissipation structures into 3D IC Package Substrates to effectively conduct heat away from the device, thereby improving system stability and reliability.
Finally, choosing 3D IC Package Substrates can also achieve higher integration density. By vertically stacking ICs, the circuit board area is maximized, allowing more functions and components to be accommodated in a limited space. This high level of integration not only improves product performance, but also reduces the cost of the overall system and improves manufacturing efficiency.
In general, compared with traditional flat PCBs, choosing 3D IC Package Substrates can bring higher performance, more compact size, superior thermal management capabilities and higher integration density to electronic systems. These advantages make 3D IC Package Substrates an indispensable part of the modern electronic packaging field, opening up new design possibilities for engineers.
What is the manufacturing process of 3D IC Package Substrates?
The manufacturing process of 3D IC Package Substrates is a precise and complex process that involves multiple key steps, including the use of advanced technologies such as TSV (Through-Silicon Via) and flip bonding to achieve precise stacking and interconnection.
First, the first step in manufacturing 3D IC Package Substrates is to prepare the substrate. This involves selecting the appropriate substrate material, such as organic materials, ceramics or silicon, to process and process according to the specific application requirements. The key to substrate preparation is to ensure that the surface flatness and material properties meet the requirements to ensure the smooth progress of subsequent processes.
The next step is to form the TSV. TSV is a structure that penetrates vertically through the silicon wafer and is used to establish electrical connections between chips at different levels. This step is usually achieved by first forming holes on the surface of the silicon wafer, then filling them with conductive material and smoothing them. This process requires highly precise equipment and process control to ensure that the size and position of the TSV meet specified requirements.
This is followed by stacking and flip bonding of the chips. In this step, multiple chips are stacked vertically and interconnected using flip bonding technology. Flip bonding is a method of turning a chip upside down and bonding it to the surface of a substrate to make an electrical connection. This process requires highly precise alignment and temperature control to ensure bonding quality and reliability.
Finally, packaging and testing are required to complete the manufacturing of 3D IC Package Substrates. The packaging process involves assembling stacked chips into an outer package, encapsulating and sealing them to protect the chips from the environment. At the same time, rigorous testing and verification of chips is a key step to ensure their performance and reliability.
To sum up, the process of manufacturing 3D IC Package Substrates requires the comprehensive use of a variety of advanced technologies and precise process control to ensure that the quality and performance of the final product meet the requirements. Through careful design and strict execution of each step, the precise stacking and interconnection of 3D IC Package Substrates can be achieved, providing important support for the performance improvement and functional expansion of electronic systems.
What are the application areas of 3D IC Package Substrates?
As an advanced electronic packaging technology, 3D IC Package Substrates has shown great application potential in various fields. Their design concepts and performance advantages make them ideal for areas such as high-performance computing, artificial intelligence, 5G communications, and IoT devices.
First, let’s look at how 3D IC Package Substrates play a role in high-performance computing. In this field, large-scale data and complex computing tasks need to be processed, and traditional two-dimensional packaging is often difficult to meet performance requirements. The vertical integration design of 3D IC Package Substrates can stack multiple processing units together, greatly improving computing density and efficiency. Such a design can not only speed up the computing process, but also reduce power consumption, making high-performance computing systems more energy-saving and environmentally friendly.
Secondly, the field of artificial intelligence is also one of the important application scenarios of 3D IC Package Substrates. In artificial intelligence applications, a large amount of computing resources are usually required for model training and inference. By using 3D IC Package Substrates, multiple processing units, storage units and sensors can be integrated to achieve highly parallel computing and data processing, thus accelerating the deployment speed and response time of artificial intelligence applications.
In addition, with the popularization and application of 5G communication technology, there are higher requirements for the performance and power consumption of communication equipment. In this regard, 3D IC Package Substrates can play an important role. By vertically integrating key components such as radio frequency modules, digital signal processors and baseband processors, more compact and efficient 5G communications equipment can be achieved. This can not only improve communication speed and network capacity, but also reduce power consumption and system costs, and promote the development and application of 5G technology.
Finally, in the field of IoT devices, 3D IC Package Substrates can also play an important role. With the popularity of IoT devices, there are increasingly higher requirements for the size, power consumption and cost of the devices. The use of 3D IC Package Substrates can achieve compact design and high integration of devices, thereby meeting the needs of IoT devices for miniaturization, low power consumption and high performance. This can provide a more stable and reliable connection for IoT applications and promote the development and application of IoT technology.
To sum up, 3D IC Package Substrates have important application value in the fields of high-performance computing, artificial intelligence, 5G communications and Internet of Things devices. Their design concepts and performance advantages make them one of the key technologies that promote technological progress and innovation in various industries. With the continuous development of technology and the expansion of application scenarios, I believe that 3D IC Package Substrates will play an increasingly important role and bring more convenience and possibilities to our lives.
Where can I find 3D IC Package Substrates?
Finding reliable 3D IC Package Substrates manufacturers and suppliers is crucial to ensure you get the best solution for your project. Here are some methods and considerations for finding suppliers:
First, you can get to know the leading manufacturers and suppliers in the market through industry trade shows and conferences. These events often provide the opportunity to meet face-to-face with suppliers, where you can learn first-hand about their products and services and build relationships with them.
Second, a web search is another convenient way to find suppliers. Through search engines or professional supply chain platforms, you can find numerous supplier lists and evaluate their credibility and professionalism by reading customer reviews and company qualifications.
Additionally, you can seek advice from industry peers and professional organizations. They may recommend some trustworthy suppliers and share their experiences and advice.
For customized solutions for specific application needs, you can contact the supplier directly to detail your project requirements and technical specifications. Excellent suppliers will provide customized solutions based on your needs and provide professional advice and support to ensure smooth project implementation.
As our company, we are committed to providing high-quality 3D IC Package Substrates and providing customized solutions to our customers. We have rich experience and advanced production technology to meet the needs of various application fields. No matter the size of your project, we are dedicated to providing you with the best products and services.
All in all, it is crucial to choose reliable 3D IC Package Substrates manufacturers and suppliers. Through careful investigation and effective communication, you can find the partner that best suits your needs and achieve successful project implementation.
What is the quote for 3D IC Package Substrates?
When determining the quotation of 3D IC Package Substrates, multiple factors need to be considered, including material selection, manufacturing complexity, and order quantity. As the requirements of each project can be different, personalized quotes and consultation are crucial.
First, material selection is critical to the cost of 3D IC Package Substrates. Different materials have different costs and properties. For example, organic substrates generally cost less, but ceramic substrates conduct heat better and therefore are slightly more expensive. Silicon interposer substrates may require higher manufacturing costs but may be the best choice in certain applications.
Secondly, the manufacturing complexity will also affect the quotation of 3D IC Package Substrates. Some projects may require more complex manufacturing processes, such as using TSV technology or multi-layer stacking, which will increase costs. At the same time, if customized designs or special requirements are required, it may also lead to an increase in costs.
Finally, the order quantity is also one of the important factors affecting the quotation. Generally speaking, large-volume orders can enjoy lower unit prices because production scale can be achieved and costs can be reduced. Conversely, small batch orders may require paying a higher unit price to cover the relatively high production costs.
To get a personalized quote and consultation, you first need to contact a professional 3D IC Package Substrates manufacturer or supplier. They will evaluate your project requirements and provide quotations and recommendations accordingly. When consulting, you can provide as detailed project information as possible, including required materials, manufacturing requirements, expected order quantities, etc., so that they can give accurate quotations and plans.
In general, the quotation of 3D IC Package Substrates is a process customized according to project needs, and factors such as material, complexity, and quantity need to be comprehensively considered. Through communication and cooperation with professional suppliers, personalized quotes and solutions that best suit project needs can be obtained.
Frequently Asked Questions (FAQs)
What are the key design considerations when integrating 3D IC Package Substrates into electronic systems?
When integrating 3D IC Package Substrates, designers need to consider factors such as thermal management, signal integrity, power delivery, and mechanical stability. Ensuring proper heat dissipation, minimizing signal interference, optimizing power distribution, and maintaining structural integrity are critical aspects of the design process.
How do 3D IC Package Substrates contribute to energy efficiency and sustainability?
3D IC Package Substrates facilitate energy-efficient designs by enabling compact and optimized electronic systems. By reducing interconnect lengths and improving thermal management, these substrates enhance overall system efficiency and reliability. Additionally, their ability to accommodate multiple functions within a smaller footprint supports sustainability efforts by minimizing material usage and energy consumption.
What are the primary challenges associated with 3D integration, and how are they addressed?
Some of the main challenges of 3D integration include thermal management, fabrication complexity, interconnect reliability, and cost. Thermal issues arise due to the concentration of heat in compact designs, which requires innovative cooling solutions. Fabrication complexity increases with the need for precise alignment and interconnection of stacked components. Interconnect reliability is crucial for maintaining signal integrity and system performance. Cost considerations include upfront investment in advanced manufacturing processes and materials. These challenges are addressed through the development of specialized technologies, improved design methodologies, and economies of scale in production.
What are the reliability and longevity considerations for 3D IC Package Substrates?
Reliability and longevity are paramount in electronic systems utilizing 3D IC Package Substrates. Factors such as material selection, fabrication quality, thermal management, and environmental conditions impact the reliability of these substrates. Manufacturers employ rigorous testing procedures and quality control measures to ensure that 3D IC Package Substrates meet industry standards for reliability and longevity. Additionally, proper system-level design and maintenance practices contribute to the extended lifespan of electronic devices employing these substrates.
How do 3D IC Package Substrates compare to traditional PCBs in terms of cost and performance?
While 3D IC Package Substrates offer superior performance and compactness compared to traditional PCBs, they may entail higher initial costs due to specialized manufacturing processes and materials. However, the enhanced functionality, miniaturization capabilities, and improved thermal management provided by 3D IC Package Substrates often justify the investment, especially in applications requiring high performance and reliability.